Introduction to Solder Paste Preparation
Solder paste is a critical component in the surface mount technology (SMT) assembly process. It is a mixture of tiny solder particles suspended in a flux medium, which is applied to printed circuit boards (PCBs) using a stencil printing process. The quality and consistency of the solder paste directly impact the reliability and performance of the assembled electronic devices. Therefore, proper solder paste data preparation is essential to ensure optimal printing results and minimize defects.
In this article, we will delve into the various aspects of solder paste data preparation, including the importance of paste material selection, stencil design considerations, printing parameters, and quality control measures. By understanding and implementing best practices in solder paste data preparation, manufacturers can achieve high-quality solder joints, improve production efficiency, and reduce costly rework and repairs.
The Role of Solder Paste in SMT Assembly
Solder paste plays a crucial role in the SMT assembly process. It serves multiple purposes:
-
Mechanical Attachment: The solder paste temporarily holds the surface mount components in place on the PCB during the assembly process.
-
Electrical Connection: During the reflow soldering process, the solder particles in the paste melt and form a permanent electrical and mechanical connection between the component leads and the PCB pads.
-
Flux Activity: The flux medium in the solder paste helps to remove oxides and contaminants from the metal surfaces, promoting better wetting and a strong solder joint.
-
Thermal Transfer: The solder paste acts as a thermal interface material, facilitating heat transfer from the component to the PCB during the reflow process.
Solder Paste Composition and Properties
Solder paste is a homogeneous mixture of solder alloy particles and flux medium. The composition and properties of the solder paste significantly influence its performance and the quality of the solder joints.
Solder Alloy Particles
The solder alloy particles in the paste determine the melting temperature, wetting behavior, and mechanical properties of the solder joints. The most common solder alloys used in SMT assembly are:
-
Tin-Lead (SnPb): Traditional solder alloys containing a mixture of tin and lead, such as Sn63Pb37 (63% tin, 37% lead) and Sn62Pb36Ag2 (62% tin, 36% lead, 2% silver). These alloys have a melting point of around 183°C and provide good wetting and reliability.
-
Lead-Free: Due to environmental and health concerns, lead-free solder alloys have gained prominence. Common lead-free alloys include SAC305 (96.5% tin, 3% silver, 0.5% copper), SAC405 (95.5% tin, 4% silver, 0.5% copper), and SnAgCu (tin-silver-copper) with varying compositions. Lead-free alloys typically have higher melting points (217-227°C) and require tighter process control compared to SnPb alloys.
The solder particle size and shape also influence the printing and reflow characteristics. Smaller particle sizes (Type 3 or Type 4) are commonly used for fine-pitch components and high-density PCB layouts, while larger particles (Type 5 or Type 6) are suitable for larger components and standard pitches.
Flux Medium
The flux medium in the solder paste serves several functions:
-
Oxide Removal: The flux chemically removes oxides and contaminants from the metal surfaces, ensuring good wetting and a strong solder joint.
-
Suspension: The flux suspends the solder particles evenly throughout the paste, preventing settling and separation.
-
Rheology Control: The flux controls the flow properties (viscosity and thixotropy) of the solder paste, enabling proper printing and preventing slumping or bridging.
-
Activation: The flux activates the solder particles during the reflow process, promoting good wetting and joint formation.
Flux formulations are classified based on their activity level and residue characteristics:
-
No-Clean: No-clean fluxes leave minimal residue after reflow and do not require post-soldering cleaning. They are widely used in SMT assembly due to their convenience and compatibility with various PCB Finishes.
-
Water-Soluble: Water-soluble fluxes have higher activity levels and leave residues that must be cleaned with water or an aqueous solution after soldering. They are suitable for applications that require a high degree of cleanliness.
-
Rosin-Based: Rosin-based fluxes contain natural or synthetic resins that provide good wetting and protection against oxidation. They can be either no-clean or cleanable, depending on the residue level and post-soldering requirements.
Stencil Design Considerations
Stencil design is a critical aspect of solder paste data preparation. The stencil determines the amount and distribution of solder paste deposited onto the PCB pads. Proper stencil design ensures consistent paste volume, minimizes defects, and accommodates various component types and sizes.
Stencil Thickness
The stencil thickness is a key parameter that affects the solder paste volume and printing quality. The optimal stencil thickness depends on several factors, including the component pitch, pad size, and solder paste type.
-
Standard Thickness: For most SMT applications, a stencil thickness of 0.1 mm (4 mil) to 0.15 mm (6 mil) is commonly used. This thickness range provides a good balance between paste volume and printability.
-
Fine-Pitch Components: For fine-pitch components (0.5 mm pitch or less), a thinner stencil (0.08 mm to 0.1 mm) may be required to achieve proper paste volume and prevent bridging or slumping.
-
Large Components: For larger components or connectors, a thicker stencil (0.15 mm to 0.2 mm) may be necessary to deposit sufficient paste volume and ensure good joint formation.
Aperture Design
The aperture design refers to the openings in the stencil that define the size, shape, and location of the solder paste deposits. Proper aperture design is crucial for achieving consistent paste volume and preventing defects.
-
Aperture Size: The aperture size should be optimized based on the pad size and desired paste volume. As a general guideline, the aperture size should be 10-20% smaller than the pad size to account for paste spread during printing.
-
Aperture Shape: The aperture shape can be circular, square, rectangular, or custom-designed depending on the pad geometry and component requirements. Circular apertures are commonly used for round pads, while square or rectangular apertures are suitable for rectangular pads.
-
Aperture Orientation: The aperture orientation should match the orientation of the pads on the PCB. Misaligned apertures can lead to insufficient paste coverage or bridging between adjacent pads.
-
Aperture Pitch: The aperture pitch should be consistent with the component pitch to ensure proper alignment and paste deposition. Fine-pitch components may require special consideration to prevent paste bridging.
Stencil Material and Finish
The stencil material and finish influence the printing quality, durability, and cleaning characteristics of the stencil.
-
Stainless Steel: Stainless steel is the most common material used for solder paste stencils. It provides good durability, stability, and printability. Stainless steel stencils can be laser-cut or electroformed, depending on the aperture size and detail requirements.
-
Nickel-Plated: Nickel-plated stencils have a smooth surface finish that improves paste release and prevents solder paste adhesion. Nickel plating also enhances the stencil’s corrosion resistance and extends its lifespan.
-
Nano-Coated: Nano-coated stencils have a hydrophobic coating that further enhances paste release and prevents paste sticking. Nano-coating can improve printing consistency and reduce the need for frequent stencil cleaning.
Stencil Cleaning and Maintenance
Regular stencil cleaning and maintenance are essential to ensure consistent printing quality and prevent defects. Solder paste residues, debris, and contamination can accumulate on the stencil surface and apertures, affecting paste release and volume.
-
Understencil Wiping: Understencil wiping involves using a solvent-impregnated paper or fabric to clean the bottom side of the stencil after each print cycle. This process removes excess solder paste and prevents paste buildup on the aperture walls.
-
Periodic Cleaning: Periodic cleaning of the stencil, typically every few hours or shifts, involves removing the stencil from the printer and thoroughly cleaning both sides with a solvent or aqueous solution. This process removes any stubborn residues and ensures the stencil remains in optimal condition.
-
Stencil Storage: Proper storage of the stencil, such as keeping it in a protective cover or container when not in use, helps to prevent damage, warping, and contamination.
Printing Parameters and Process Control
Solder paste printing is a critical step in the SMT assembly process, and proper control of printing parameters is essential for achieving consistent and high-quality results. Key printing parameters and process control measures include:
Print Speed and Pressure
-
Print Speed: The print speed refers to the speed at which the squeegee blade moves across the stencil during the printing process. Optimal print speed depends on the solder paste type, stencil design, and PCB layout. Typical print speeds range from 20 to 200 mm/s, with slower speeds used for fine-pitch components and higher viscosity pastes.
-
Print Pressure: Print pressure is the force applied by the squeegee blade onto the stencil during printing. Adequate print pressure ensures proper solder paste transfer and fills the stencil apertures completely. However, excessive pressure can cause paste slumping or stencil damage. Print pressure is typically adjusted based on the solder paste viscosity, stencil thickness, and aperture size.
Squeegee Blade
The squeegee blade is responsible for pushing the solder paste across the stencil and filling the apertures. Squeegee blade characteristics and settings influence the printing quality.
-
Blade Material: Squeegee blades are commonly made of metal (stainless steel) or polyurethane. Metal blades provide better durability and are suitable for high-volume production, while polyurethane blades offer better conformity and are preferred for fine-pitch applications.
-
Blade Angle: The blade angle, typically set between 45° and 60°, affects the shearing action and paste deposit consistency. A lower blade angle provides better aperture filling, while a higher angle improves paste release and minimizes slumping.
-
Blade Pressure: The blade pressure should be adjusted to ensure proper paste filling and release without causing stencil deformation or damage. Optimal blade pressure depends on the paste viscosity, stencil thickness, and blade material.
Print Alignment and Registration
Accurate alignment and registration of the stencil to the PCB are critical for ensuring precise solder paste deposition on the pads.
-
Vision Alignment: Most modern solder paste printers incorporate vision systems that use fiducial marks or reference points on the PCB and stencil for alignment. The vision system automatically adjusts the stencil position to achieve proper registration.
-
Manual Alignment: In some cases, manual alignment may be necessary, especially for prototypes or low-volume production. Skilled operators use alignment marks and visual inspection to ensure proper stencil-to-PCB Registration.
-
Print Offset: Print offset refers to the distance between the stencil and PCB during printing. A small offset (0.1 mm to 0.2 mm) is typically maintained to prevent stencil damage and ensure consistent paste release. The offset is controlled by the printer’s z-axis movement and should be regularly calibrated.
Print Repeatability and Consistency
Maintaining print repeatability and consistency is crucial for achieving high-quality solder paste deposits across multiple PCBs.
-
Print Pitch: The print pitch, or the distance between successive prints, should be consistent to ensure uniform paste deposition. Inconsistent pitch can lead to variations in paste volume and affect component placement accuracy.
-
Print Cycle Time: The print cycle time, which includes the time for printing, stencil cleaning, and PCB indexing, should be optimized to maximize throughput without compromising quality. Adequate time should be allocated for paste recovery between prints to maintain consistent rheology.
-
Environmental Control: Solder paste is sensitive to temperature and humidity variations. Maintaining a controlled environment (typically 22-28°C and 35-65% RH) helps to ensure consistent paste behavior and minimize defects.
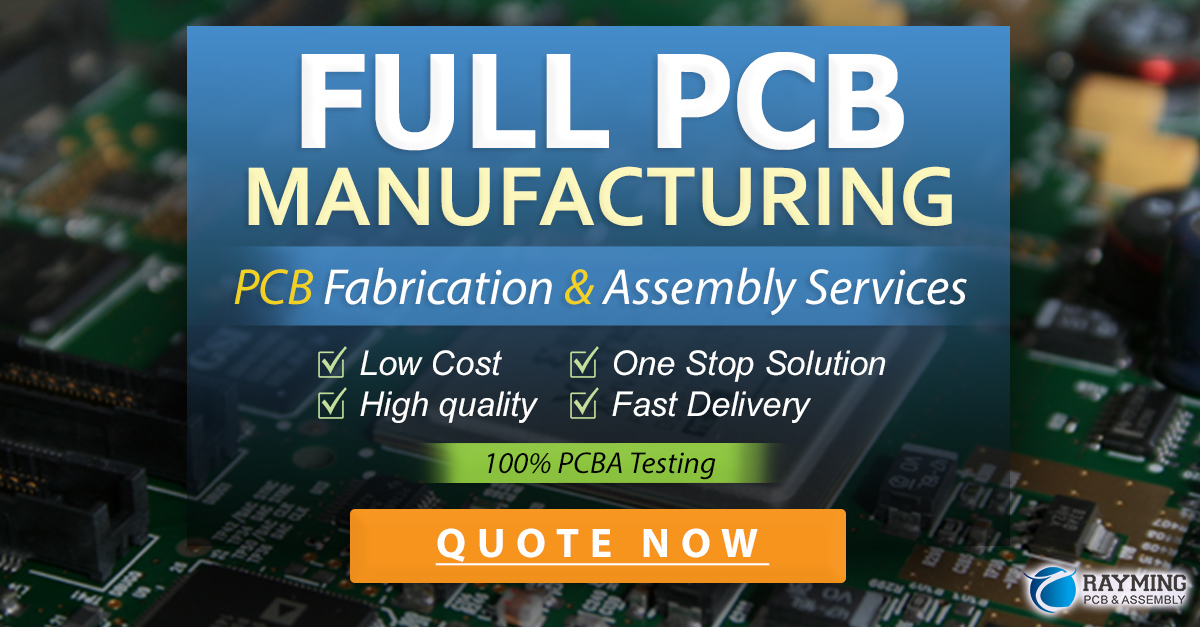
Quality Control and Inspection
Implementing robust quality control and inspection measures is essential for identifying and addressing solder paste printing issues promptly. Regular monitoring and analysis of the printing process help to maintain high-quality output and minimize rework and scrap.
Solder Paste Inspection (SPI)
Solder Paste Inspection (SPI) is an automated inspection technique that uses 2D or 3D vision systems to assess the quality of solder paste deposits after printing.
-
2D SPI: 2D SPI systems capture top-down images of the solder paste deposits and analyze them for volume, area, and shape. They can detect gross defects such as missing or excessive paste, bridging, and misalignment.
-
3D SPI: 3D SPI systems use laser triangulation or structured light to create a three-dimensional profile of the solder paste deposits. They provide more detailed information on paste volume, height, and shape, enabling the detection of subtle defects and volume variations.
SPI systems compare the measured solder paste parameters against predefined acceptance criteria and generate pass/fail results and statistical data for process control and traceability.
Visual Inspection
Visual inspection by trained operators complements automated SPI and helps to identify defects that may be missed by the inspection systems.
-
Post-Print Inspection: Operators visually inspect the printed PCBs for any obvious defects, such as missing or smeared paste, stencil damage, or contamination. They may use magnification tools or microscopes for detailed examination.
-
First-Article Inspection: First-article inspection involves a thorough visual examination of the first PCB printed after a changeover or setup. This inspection verifies the stencil alignment, aperture cleanliness, and overall print quality before proceeding with the production run.
Statistical Process Control (SPC)
Statistical Process Control (SPC) involves collecting and analyzing process data to monitor the stability and capability of the solder paste printing process.
-
Process Capability: Process capability indices, such as Cp and Cpk, are used to assess the ability of the printing process to meet the specified requirements consistently. These indices consider the process variation and the specification limits for key parameters like paste volume and height.
-
Control Charts: Control charts, such as X-bar and R charts, are used to monitor the process over time and detect any trends, shifts, or anomalies. These charts plot the measured parameters against predetermined control limits and provide a visual indication of process stability.
-
Pareto Analysis: Pareto analysis is used to prioritize the most frequent or critical printing defects based on their occurrence and impact. This analysis helps to focus improvement efforts on the key issues affecting the process quality.
Continuous Improvement
Continuous improvement is essential for optimizing the solder paste printing process and addressing any recurring issues or inefficiencies.
-
Root Cause Analysis: When printing defects or process deviations are identified, a systematic root cause analysis should be conducted to identify the underlying factors contributing to the issues. Tools like fishbone diagrams and 5-why analysis can be used to drill down to the root causes.
-
Corrective and Preventive Actions (CAPA): Based on the root cause analysis, appropriate corrective actions should be implemented to address the immediate issues and prevent their recurrence. Preventive actions should also be taken to proactively identify and mitigate potential risks and failure modes.
-
Process Optimization: Regular process optimization efforts, such as design of experiments (DOE) and parameter fine-tuning, help to improve the printing performance, reduce variability, and enhance overall process capability. Collaboration between process engineers, quality teams, and operators is crucial for driving continuous improvement.
Frequently Asked Questions (FAQ)
- What is the optimal solder paste viscosity for printing?
The optimal solder paste viscosity depends on various factors, such as the stencil aperture size, printing speed, and component pitch. Generally, a viscosity range of 800,000 to 1,200,000 centipoise (cP) is suitable for most SMT applications. Higher viscosity pastes are better for fine-pitch components and smaller apertures, while lower viscosity pastes are easier to print and release from the stencil. It’s essential to consult the paste manufacturer’s recommendations and conduct print trials to determine the best viscosity for your specific process.
- How often should I clean my solder paste stencil?
The frequency of stencil cleaning depends on the solder paste type, printing volume, and environmental conditions. As a general guideline, understencil wiping should be performed after every print cycle to remove excess paste and prevent buildup. Periodic thorough cleaning, typically every few hours or at the end of a shift, is recommended to remove any stubborn residues and maintain stencil cleanliness. However, the actual cleaning frequency may vary based on the specific process requirements and the level of contamination observed during production.
- What are the most common solder paste printing defects?
Some of the
Leave a Reply