Introduction to Edge Connector Bevelling
Edge connector bevelling is a crucial process in the manufacturing of printed circuit boards (PCBs) and other electronic components. It involves the precise shaping and smoothing of the edges of PCB Connectors to ensure proper fit, reliable connections, and improved durability. This article will explore the importance of edge connector bevelling, its applications, techniques, and the benefits it offers in the electronics industry.
Understanding PCB Connectors
Before delving into the specifics of edge connector bevelling, it is essential to understand the role of PCB connectors. PCB connectors are components that allow the connection and communication between different parts of a circuit board or between multiple PCBs. They come in various types, such as:
- Card edge connectors
- Board-to-board connectors
- Wire-to-board connectors
- Surface mount connectors
Each type of connector serves a specific purpose and requires precise manufacturing to ensure optimal performance.
The Need for Edge Connector Bevelling
Ensuring Proper Fit
One of the primary reasons for edge connector bevelling is to ensure a proper fit between the connector and its mating component. When the edges of a connector are left unbevelled, they may not align correctly with the corresponding slot or socket. This misalignment can lead to poor connections, intermittent failures, or even damage to the components.
By bevelling the edges of the connector, manufacturers create a smooth and precise surface that allows for easy insertion and a secure fit. The bevelled edges guide the connector into place, reducing the risk of misalignment and ensuring a reliable connection.
Improving Contact Reliability
In addition to ensuring proper fit, edge connector bevelling also enhances contact reliability. When a connector is inserted into its mating component, the contacts on both sides must make a firm and consistent connection. Any irregularities or roughness on the edges of the connector can interfere with this contact, leading to poor signal integrity or intermittent connections.
Bevelling the edges of the connector helps to create a smooth and uniform surface that promotes optimal contact between the connector and its mating component. This improved contact reliability translates to better signal transmission, reduced noise, and overall enhanced performance of the electronic device.
Enhancing Durability
Edge connector bevelling also plays a crucial role in enhancing the durability of PCB connectors. When a connector is subjected to repeated insertions and removals, the edges can become worn or damaged over time. This wear and tear can lead to poor connections, reduced reliability, and ultimately, failure of the electronic device.
By bevelling the edges of the connector, manufacturers create a more resilient and durable component. The smooth, rounded edges are less likely to catch or snag during insertion and removal, reducing the risk of damage. Additionally, the bevelled edges distribute the insertion and removal forces more evenly, minimizing stress on the connector and prolonging its lifespan.
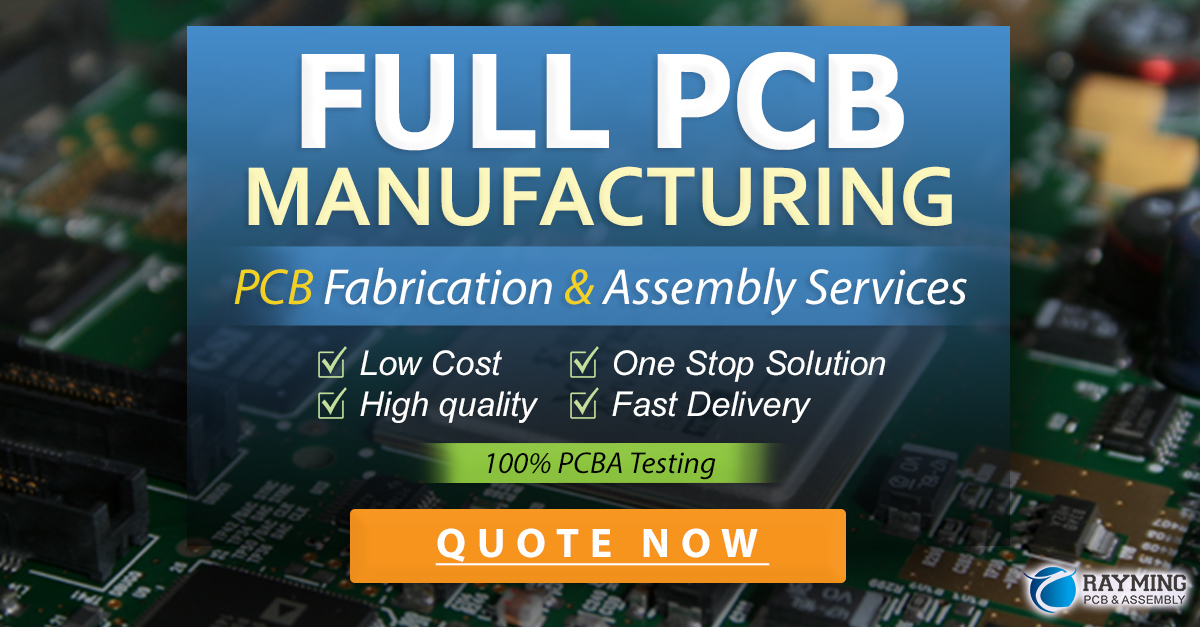
Edge Connector Bevelling Techniques
There are several techniques used for edge connector bevelling, each with its own advantages and considerations. Some common techniques include:
Mechanical Bevelling
Mechanical bevelling involves the use of specialized tools, such as routers or grinders, to physically remove material from the edges of the connector. This technique is often used for larger connectors or those with complex shapes. Mechanical bevelling offers precision and flexibility, allowing for custom bevel angles and profiles.
However, mechanical bevelling also has some drawbacks. It can be time-consuming and labor-intensive, especially for high-volume production. Additionally, the process generates dust and debris, which must be carefully managed to prevent contamination of the PCB or other components.
Chemical Bevelling
Chemical bevelling, also known as etching, uses chemical solutions to remove material from the edges of the connector. This technique involves immersing the connector in a carefully controlled chemical bath that selectively dissolves the unwanted material, leaving a smooth and bevelled edge.
Chemical bevelling offers several advantages over mechanical methods. It is faster and more efficient, making it suitable for high-volume production. It also produces less dust and debris, reducing the risk of contamination. However, chemical bevelling requires careful control of the etching process to ensure consistent results and avoid over-etching, which can weaken the connector.
Laser Bevelling
Laser bevelling is a high-precision technique that uses focused laser beams to remove material from the edges of the connector. This method offers unparalleled accuracy and consistency, allowing for very fine bevel angles and intricate profiles.
Laser bevelling is particularly useful for small, delicate connectors or those with tight tolerances. It is a non-contact process, meaning there is no physical tool wear or deformation of the connector during bevelling. Additionally, laser bevelling generates minimal dust and debris, making it a clean and efficient option.
However, laser bevelling equipment can be expensive, and the process may be slower compared to other techniques, especially for larger connectors or high-volume production.
Factors Affecting Edge Connector Bevelling
Several factors must be considered when implementing edge connector bevelling to ensure optimal results. These include:
Material Properties
The material properties of the connector, such as its hardness, ductility, and thermal conductivity, play a significant role in the bevelling process. Different materials may require different bevelling techniques or parameters to achieve the desired results. For example, harder materials may be more challenging to bevel mechanically, while softer materials may be more susceptible to over-etching during chemical bevelling.
Bevel Angle and Profile
The bevel angle and profile are critical factors in edge connector bevelling. The bevel angle refers to the slope of the bevelled edge, while the profile describes the shape of the bevel, such as a simple chamfer or a more complex contour.
The choice of bevel angle and profile depends on the specific application and the mating component. A steeper bevel angle may provide better guidance and alignment, while a shallower angle may offer improved contact reliability. Similarly, a simple chamfer may suffice for some applications, while others may require a more intricate profile to ensure optimal performance.
Tolerance and Precision
Tolerance and precision are essential considerations in edge connector bevelling. The bevelled edges must meet tight dimensional requirements to ensure proper fit and reliable connections. Any deviations from the specified tolerances can lead to misalignment, poor contact, or even failure of the electronic device.
Achieving the required tolerance and precision depends on the chosen bevelling technique, the skill of the operator, and the quality control measures in place. Manufacturers must carefully monitor and control the bevelling process to ensure consistent and accurate results.
Benefits of Edge Connector Bevelling
Implementing edge connector bevelling offers several benefits for the electronics industry, including:
-
Improved reliability: Bevelled edges ensure proper fit and reliable connections, reducing the risk of failures and enhancing the overall reliability of electronic devices.
-
Better signal integrity: Smooth, bevelled edges promote optimal contact between connectors and their mating components, minimizing noise and improving signal transmission.
-
Increased durability: Bevelled edges are less susceptible to wear and tear, prolonging the lifespan of connectors and reducing the need for replacements.
-
Easier assembly: Bevelled edges guide connectors into place, simplifying the assembly process and reducing the risk of misalignment or damage.
-
Cost savings: By improving reliability and durability, edge connector bevelling helps to reduce maintenance and repair costs associated with electronic devices.
Applications of Edge Connector Bevelling
Edge connector bevelling finds applications in various sectors of the electronics industry, including:
-
Consumer electronics: Smartphones, tablets, laptops, and other consumer devices rely on bevelled connectors for reliable connections and optimal performance.
-
Automotive electronics: The harsh environment and vibrations in vehicles necessitate the use of robust, bevelled connectors to ensure reliable operation of electronic systems.
-
Industrial equipment: Industrial machines and control systems employ bevelled connectors to withstand the demanding conditions and maintain reliable connections.
-
Medical devices: Edge connector bevelling is crucial in medical electronics to ensure accurate data transmission and reliable operation of life-saving equipment.
-
Aerospace and defense: High-reliability connectors with bevelled edges are essential in aerospace and defense applications, where failure is not an option.
Frequently Asked Questions (FAQ)
-
What is the purpose of edge connector bevelling?
Edge connector bevelling serves to ensure proper fit, reliable connections, and improved durability of PCB connectors by creating smooth, precise edges that guide the connector into place and promote optimal contact with the mating component. -
What are the different techniques used for edge connector bevelling?
The three main techniques used for edge connector bevelling are mechanical bevelling (using tools like routers or grinders), chemical bevelling (using etching solutions), and laser bevelling (using focused laser beams). -
How does edge connector bevelling improve signal integrity?
Bevelled edges create a smooth, uniform surface that promotes optimal contact between the connector and its mating component, minimizing noise and ensuring better signal transmission. -
What factors should be considered when implementing edge connector bevelling?
When implementing edge connector bevelling, factors such as material properties, bevel angle and profile, tolerance and precision, and the specific application requirements must be considered to ensure optimal results. -
In which industries is edge connector bevelling commonly used?
Edge connector bevelling is widely used in various sectors of the electronics industry, including consumer electronics, automotive electronics, industrial equipment, medical devices, and aerospace and defense applications.
Conclusion
Edge connector bevelling is a vital process in the manufacturing of PCBs and electronic components, ensuring proper fit, reliable connections, and enhanced durability. By creating smooth, precise edges on connectors, bevelling techniques like mechanical, chemical, and laser bevelling help to improve signal integrity, simplify assembly, and reduce maintenance costs.
As the electronics industry continues to evolve and demand ever-increasing performance and reliability, the importance of edge connector bevelling will only grow. Manufacturers must stay up-to-date with the latest bevelling technologies and best practices to meet the stringent requirements of modern electronic devices and ensure the highest quality products for their customers.
Leave a Reply