Introduction to cEDM
cEDM, or Collaborative Electronic Design and Manufacturing, is a groundbreaking approach that combines the power of collaborative design with the efficiency of modern manufacturing techniques. This innovative methodology is transforming the way electronics are designed and produced, enabling companies to bring their products to market faster, more cost-effectively, and with higher quality than ever before.
What is cEDM?
At its core, cEDM is a holistic approach to electronics design and manufacturing that emphasizes collaboration, automation, and data-driven decision-making. By leveraging the latest advancements in software, hardware, and manufacturing technologies, cEDM streamlines the entire product development lifecycle, from concept to production.
Key Components of cEDM
- Collaborative Design
- Automated Manufacturing
- Data-Driven Optimization
- Continuous Improvement
The Benefits of cEDM
Increased Efficiency
One of the primary benefits of cEDM is its ability to dramatically increase efficiency throughout the product development process. By automating repetitive tasks, reducing manual errors, and enabling real-time collaboration, cEDM allows teams to work smarter, not harder.
Faster Time-to-Market
In today’s fast-paced, highly competitive market, speed is everything. cEDM helps companies bring their products to market faster by streamlining the design and manufacturing processes, eliminating bottlenecks, and enabling parallel development.
Cost Reduction
cEDM also offers significant cost savings by reducing waste, minimizing rework, and optimizing resource utilization. By leveraging data-driven insights and continuous improvement methodologies, companies can identify and eliminate inefficiencies, resulting in lower production costs and higher profit margins.
Improved Quality
Finally, cEDM helps ensure that products meet or exceed customer expectations by embedding quality control and testing throughout the development process. By catching and correcting issues early on, companies can avoid costly recalls and reputation damage down the line.
Implementing cEDM
Collaborative Design Tools
To fully leverage the benefits of cEDM, companies must invest in the right collaborative design tools. These tools should enable real-time collaboration, version control, and seamless integration with manufacturing systems.
Tool | Description |
---|---|
CAD Software | Computer-aided design software for creating 3D models and 2D drawings |
PLM Systems | Product lifecycle management systems for managing product data and workflows |
Simulation Tools | Tools for simulating and testing product performance and manufacturability |
Automated Manufacturing Systems
Automated manufacturing systems are another critical component of cEDM. These systems leverage advanced technologies such as robotics, 3D printing, and machine learning to streamline production and reduce human error.
System | Description |
---|---|
Robotics | Automated systems for tasks such as assembly, testing, and inspection |
3D Printing | Additive manufacturing technology for rapid prototyping and small-batch production |
Machine Learning | Algorithms for optimizing production processes and predicting maintenance needs |
Data-Driven Optimization
To fully realize the benefits of cEDM, companies must also embrace data-driven optimization. This involves collecting and analyzing data from all stages of the product development lifecycle to identify opportunities for improvement.
Data Source | Description |
---|---|
Sensor Data | Data collected from sensors embedded in products and production equipment |
Quality Control Data | Data collected during testing and inspection processes |
Customer Feedback | Data collected from customer reviews, surveys, and support requests |
Continuous Improvement
Finally, cEDM requires a commitment to continuous improvement. This means regularly reviewing and refining processes, incorporating feedback from stakeholders, and staying up-to-date with the latest industry trends and best practices.
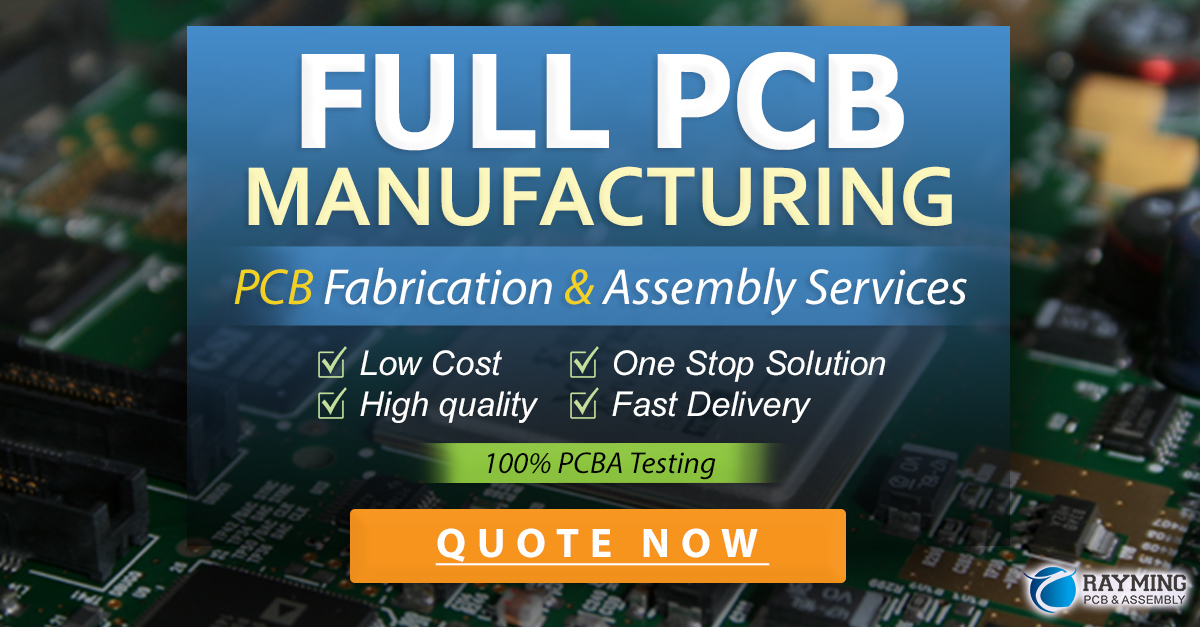
cEDM Use Cases
Automotive Electronics
The automotive industry is one of the most prominent adopters of cEDM, using it to design and manufacture everything from infotainment systems to advanced driver assistance systems (ADAS).
Medical Devices
cEDM is also making significant inroads in the medical device industry, where it is being used to develop everything from wearable health monitors to surgical robots.
Consumer Electronics
From smartphones to smart home devices, cEDM is transforming the way consumer electronics are designed and manufactured, enabling companies to bring innovative new products to market faster and more cost-effectively.
Challenges and Limitations
Upfront Investment
One of the main challenges of implementing cEDM is the upfront investment required. Companies must invest in new software, hardware, and training to fully leverage the benefits of this approach.
Skill Gap
Another challenge is the skill gap that exists in many organizations. cEDM requires a new set of skills and expertise, which can be difficult to find and develop.
Resistance to Change
Finally, there may be resistance to change within organizations, particularly among those who are used to traditional design and manufacturing methods.
Future of cEDM
Industry 4.0
cEDM is a key enabler of Industry 4.0, the fourth industrial revolution characterized by the convergence of physical and digital technologies. As Industry 4.0 continues to gain momentum, cEDM will become increasingly important for companies looking to stay competitive.
Artificial Intelligence
Artificial intelligence (AI) is another technology that is poised to have a significant impact on cEDM in the coming years. By leveraging AI algorithms, companies will be able to further optimize their design and manufacturing processes, leading to even greater efficiency and cost savings.
Sustainability
Finally, cEDM will play a critical role in promoting sustainability in the electronics industry. By enabling more efficient use of resources, reducing waste, and promoting circular economy principles, cEDM will help companies meet their environmental and social responsibility goals.
Frequently Asked Questions
What is the difference between cEDM and traditional electronics design and manufacturing?
cEDM is a more collaborative, automated, and data-driven approach than traditional methods, enabling faster time-to-market, lower costs, and higher quality.
How much does it cost to implement cEDM?
The cost of implementing cEDM varies depending on the size and complexity of the organization, but it typically requires a significant upfront investment in software, hardware, and training.
What skills are required for cEDM?
cEDM requires a combination of technical skills (e.g., CAD design, programming, data analysis) and soft skills (e.g., collaboration, communication, problem-solving).
How long does it take to implement cEDM?
The implementation timeline for cEDM varies depending on the organization’s readiness and resources, but it typically takes several months to a year to fully transition to this approach.
What industries are using cEDM?
cEDM is being used in a wide range of industries, including automotive, medical devices, consumer electronics, aerospace, and defense.
Conclusion
cEDM represents a paradigm shift in the way electronics are designed and manufactured. By leveraging the latest advancements in software, hardware, and manufacturing technologies, cEDM enables companies to bring their products to market faster, more cost-effectively, and with higher quality than ever before. As Industry 4.0 continues to gain momentum and new technologies such as AI emerge, cEDM will become increasingly critical for companies looking to stay competitive in the fast-paced, ever-evolving electronics industry. By embracing cEDM and committing to continuous improvement, companies can unlock new levels of efficiency, innovation, and sustainability, positioning themselves for success in the years to come.
Leave a Reply