Introduction to PCB sensor placement
When designing a printed circuit board (PCB) that incorporates external sensors, proper placement of these components is crucial for optimal performance, reliability, and manufacturability. This comprehensive guide will delve into the various aspects of PCB sensor placement, including best practices, considerations for different Sensor Types, and common pitfalls to avoid.
Understanding the Importance of Proper PCB Sensor Placement
Proper placement of external sensors on a PCB is essential for several reasons:
-
Signal integrity: Optimal sensor placement ensures that the sensor can accurately measure the desired parameter without interference from other components or environmental factors.
-
Reliability: Well-placed sensors are less likely to be affected by vibrations, heat, or other stressors that could cause premature failure.
-
Manufacturability: Carefully positioned sensors simplify the assembly process and reduce the likelihood of errors during soldering or other manufacturing steps.
-
Space optimization: Efficient sensor placement helps minimize the overall size of the PCB, which is particularly important in space-constrained applications.
Factors to Consider When Placing Sensors on a PCB
When determining the best location for an external sensor on a PCB, consider the following factors:
Sensor Type and Function
Different types of sensors have unique requirements for placement on a PCB. Some common sensor types and their placement considerations include:
Sensor Type | Placement Considerations |
---|---|
Temperature | Place away from heat-generating components and ensure adequate airflow. |
Humidity | Avoid placing near components that generate heat or moisture. |
Pressure | Position in an area where the sensor can be easily connected to the pressure source. |
Accelerometer | Orient the sensor according to the desired axis of measurement and minimize vibrations. |
Gyroscope | Place away from sources of electromagnetic interference (EMI) and ensure proper orientation. |
Signal Path and Interference
To maintain signal integrity, it is important to:
- Keep sensor signal traces as short as possible to minimize noise and interference.
- Route sensor signal traces away from high-frequency or high-current traces to avoid crosstalk.
- Use ground planes or shielding to reduce EMI and improve signal quality.
Environmental Factors
Consider the environment in which the PCB will operate and place sensors accordingly:
- For sensors exposed to harsh conditions (e.g., extreme temperatures, moisture, or vibrations), use protective enclosures or potting compounds.
- Position sensors away from sources of heat, moisture, or vibrations that could affect their performance.
Accessibility and Maintenance
Place sensors in locations that are easily accessible for calibration, replacement, or maintenance:
- Avoid placing sensors in hard-to-reach areas of the PCB.
- Consider using sockets or connectors for sensors that may require frequent replacement.
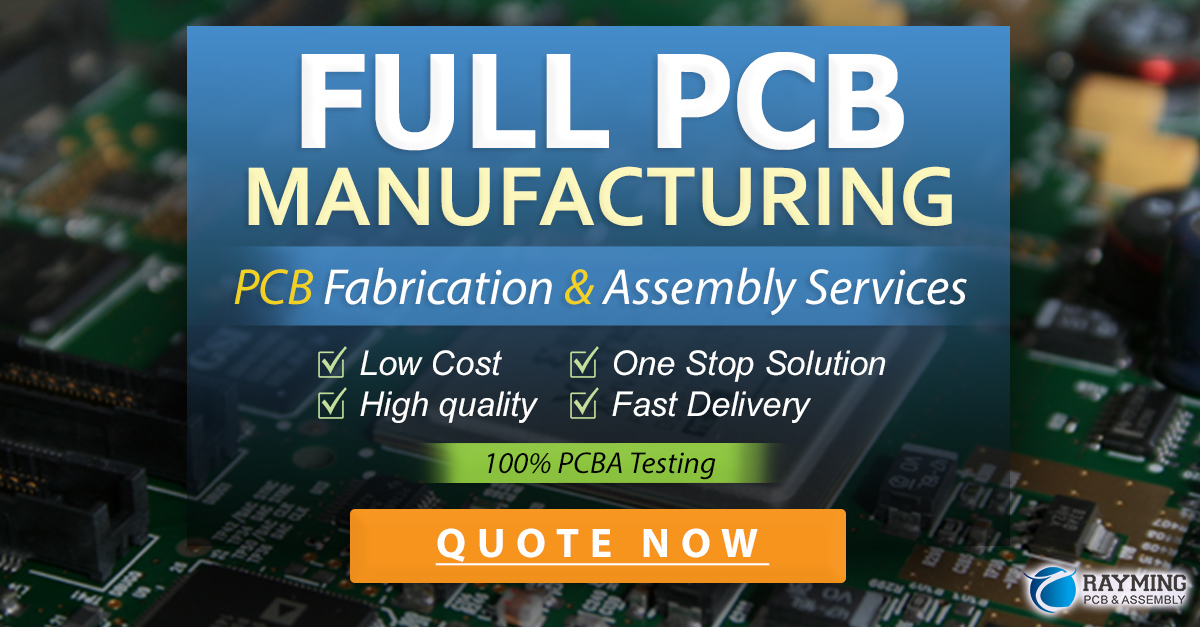
Best Practices for PCB Sensor Placement
Follow these best practices to ensure optimal sensor placement on your PCB:
- Consult the sensor manufacturer’s datasheet and application notes for specific placement recommendations.
- Use simulation tools to analyze sensor placement and optimize signal integrity.
- Collaborate with experienced PCB designers and engineers to review your placement strategy.
- Conduct thorough testing and validation of sensor performance in the intended operating environment.
Common Pitfalls to Avoid in PCB Sensor Placement
Be aware of these common pitfalls when placing sensors on a PCB:
- Placing sensors too close to high-frequency or high-current components, leading to interference.
- Failing to consider the sensor’s orientation and its impact on measurement accuracy.
- Neglecting to account for environmental factors that could affect sensor performance.
- Placing sensors in locations that are difficult to access for maintenance or replacement.
Case Studies: Successful PCB Sensor Placement Strategies
Case Study 1: Industrial Control System
In an industrial control system, multiple sensors were used to monitor temperature, pressure, and vibration. The PCB designers followed these strategies for successful sensor placement:
- Temperature sensors were placed away from heat-generating components and in areas with good airflow.
- Pressure sensors were positioned close to the pressure sources and connected using short, direct tubing.
- Vibration Sensors (accelerometers) were oriented according to the desired measurement axis and mounted on a rigid part of the PCB.
The result was a reliable and efficient control system that accurately monitored the required parameters.
Case Study 2: Wearable Medical Device
A wearable medical device required the integration of various sensors to monitor a patient’s vital signs. The PCB designers implemented these placement strategies:
- Pulse oximetry sensors were placed in a location that ensured good contact with the patient’s skin.
- Temperature sensors were positioned away from heat-generating components and in an area that accurately reflected the patient’s body temperature.
- Accelerometers for motion tracking were oriented according to the desired measurement axes and placed in a location that minimized interference from other components.
The well-placed sensors enabled accurate and reliable monitoring of the patient’s vital signs, contributing to the overall effectiveness of the medical device.
Frequently Asked Questions (FAQ)
-
Q: How do I determine the best location for a sensor on my PCB?
A: Consider factors such as the sensor’s function, signal path, environmental conditions, and accessibility. Consult the sensor manufacturer’s datasheet and application notes for specific placement recommendations, and collaborate with experienced PCB designers to review your placement strategy. -
Q: What can I do to minimize interference between sensors and other components on the PCB?
A: To minimize interference, keep sensor signal traces as short as possible, route them away from high-frequency or high-current traces, and use ground planes or shielding to reduce EMI. Additionally, place sensors away from components that generate heat, moisture, or vibrations. -
Q: How can I ensure my sensors are easily accessible for maintenance or replacement?
A: Place sensors in locations that are easily accessible on the PCB, avoiding hard-to-reach areas. Consider using sockets or connectors for sensors that may require frequent replacement, and ensure that the PCB design allows for easy access to these components. -
Q: What should I do if I’m unsure about the best placement for a particular sensor?
A: If you’re unsure about sensor placement, consult the sensor manufacturer’s datasheet and application notes for guidance. You can also seek advice from experienced PCB designers or engineers who have worked with similar sensors in the past. Additionally, simulation tools can help analyze sensor placement and optimize signal integrity. -
Q: How can I test and validate my sensor placement strategy?
A: Conduct thorough testing and validation of sensor performance in the intended operating environment. This may involve creating prototypes, performing bench tests, and conducting field trials. Analyze the data collected from these tests to ensure that the sensors are functioning as expected and providing accurate and reliable measurements. If issues are identified, iterate on the placement strategy and retest until satisfactory results are achieved.
Conclusion
Proper placement of external sensors on a PCB is essential for ensuring optimal performance, reliability, and manufacturability. By considering factors such as sensor type, signal integrity, environmental conditions, and accessibility, designers can create PCBs that effectively integrate sensors and meet the requirements of their specific applications.
By following best practices, avoiding common pitfalls, and learning from successful case studies, PCB designers can develop robust sensor placement strategies that contribute to the overall success of their projects. As technology continues to advance and the demand for sensor-integrated PCBs grows, a solid understanding of sensor placement principles will become increasingly valuable for engineers and designers alike.
Leave a Reply