Introduction to PCB Hole Tolerances
When designing and manufacturing printed circuit boards (PCBs), it is crucial to understand and account for the various manufacturing tolerances that can affect the final product. One of the most critical tolerances to consider is the finished hole size tolerance, which refers to the acceptable variation in the diameter of drilled holes on a PCB. These holes are essential for accommodating components, vias, and mounting points, and any deviation from the desired size can lead to assembly issues and compromised functionality.
In this article, we will delve into the world of PCB hole tolerances, exploring the factors that influence them, the industry standards that govern them, and the best practices for designing and manufacturing PCBs with optimal hole sizes.
Why PCB Hole Tolerances Matter
PCB hole tolerances play a vital role in ensuring the proper fit and function of components, as well as the overall reliability of the assembled board. Here are some key reasons why hole tolerances are so important:
-
Component Compatibility: Many electronic components, such as through-hole resistors, capacitors, and connectors, rely on precisely sized holes for accurate placement and secure attachment to the PCB. If the holes are too small, components may not fit properly, leading to assembly difficulties and potential damage. Conversely, if the holes are too large, components may not be held securely in place, resulting in poor electrical connections and mechanical instability.
-
Via Integrity: Vias, which are small holes that connect different layers of a multi-layer PCB, must be drilled to the correct size to ensure proper electrical conductivity and signal integrity. Inaccurate via hole sizes can lead to issues such as increased resistance, signal reflections, and even open circuits.
-
Manufacturability: PCB manufacturers have specific capabilities and limitations when it comes to drilling holes. Designing holes with tolerances that are too tight or beyond the capabilities of the chosen fabrication process can result in higher costs, longer lead times, and reduced yields.
-
Reliability: Properly sized holes contribute to the overall reliability of the assembled PCB. Poorly fitted components or vias can lead to mechanical stress, vibration-induced failures, and intermittent electrical connections, all of which can compromise the long-term performance and durability of the device.
Factors Affecting PCB Hole Tolerances
Several factors can influence the finished hole size on a PCB, and understanding these factors is essential for designing boards with appropriate tolerances. Some of the key factors include:
PCB Material
The type of material used for the PCB substrate can have a significant impact on hole tolerances. Common PCB materials include:
- FR-4: A glass-reinforced epoxy laminate, FR-4 is the most widely used PCB material. It offers good mechanical and electrical properties, as well as reasonable drilling characteristics.
- High-Frequency Materials: PCBs designed for high-frequency applications, such as RF and microwave circuits, often use specialized materials like Rogers, Teflon, or ceramic-based laminates. These materials may have different drilling properties compared to FR-4, which can affect hole tolerances.
- Metal Core: Metal Core PCBs, which feature a metal substrate for enhanced thermal dissipation, can be more challenging to drill accurately due to the harder material and potential for burr formation.
Hole Diameter
The nominal hole diameter is a crucial factor in determining the achievable tolerance. Generally, smaller holes are more difficult to drill with tight tolerances compared to larger holes. This is due to the increased wear and deflection of smaller drill bits, as well as the higher spindle speeds required for smaller diameters.
PCB Thickness
The thickness of the PCB Stack-up can also influence hole tolerances. Thicker boards require longer drill times and are more susceptible to drill wander and breakage, which can lead to larger hole size variations. Additionally, the aspect ratio, which is the ratio of the hole depth to its diameter, becomes more challenging to maintain as the board thickness increases.
Drilling Process
The specific drilling process employed by the PCB manufacturer can have a significant impact on hole tolerances. Some common drilling methods include:
- Mechanical Drilling: This is the most common method for creating holes in PCBs, using high-speed steel or carbide drill bits. Mechanical drilling is suitable for a wide range of hole sizes and can achieve relatively tight tolerances when properly optimized.
- Laser Drilling: Laser drilling uses a focused laser beam to vaporize the PCB material, creating precise, small-diameter holes. This method is often used for high-density designs or microvias, but it can be more expensive than mechanical drilling.
- Punching: For larger holes or slots, punching may be used as an alternative to drilling. Punching involves using a die to cut through the PCB material, and it can offer faster cycle times and improved hole quality compared to drilling.
Plating and Finishing
After the holes are drilled, they typically undergo a plating process to create conductive surfaces for electrical connections. The plating process can also affect the finished hole size, as the plating thickness will reduce the hole diameter. Common plating materials include copper, nickel, and gold, each with its own plating thickness and characteristics.
Industry Standards for PCB Hole Tolerances
To ensure consistency and reliability across the PCB manufacturing industry, several standards organizations have established guidelines for hole tolerances. Two of the most widely recognized standards are:
IPC-6012
IPC, the Association Connecting Electronics Industries, publishes the IPC-6012 standard, which defines the qualifications and performance specifications for rigid printed boards. This standard includes hole size tolerances for various classes of PCBs, based on the intended end-use and reliability requirements.
IPC-6012 defines three classes of PCBs:
- Class 1: General Electronic Products
- Class 2: Dedicated Service Electronic Products
- Class 3: High Reliability Electronic Products
Each class has its own set of hole size tolerances, with Class 3 having the tightest requirements. For example, a Class 2 PCB with a nominal hole size of 0.5 mm may have a tolerance of ±0.075 mm, while a Class 3 PCB with the same nominal hole size would have a tolerance of ±0.05 mm.
IEC 60189-2
The International Electrotechnical Commission (IEC) publishes the IEC 60189-2 standard, which provides guidelines for the design, manufacture, and testing of printed circuit boards. This standard includes hole size tolerances similar to those found in IPC-6012, with some minor differences in the specific values and classifications.
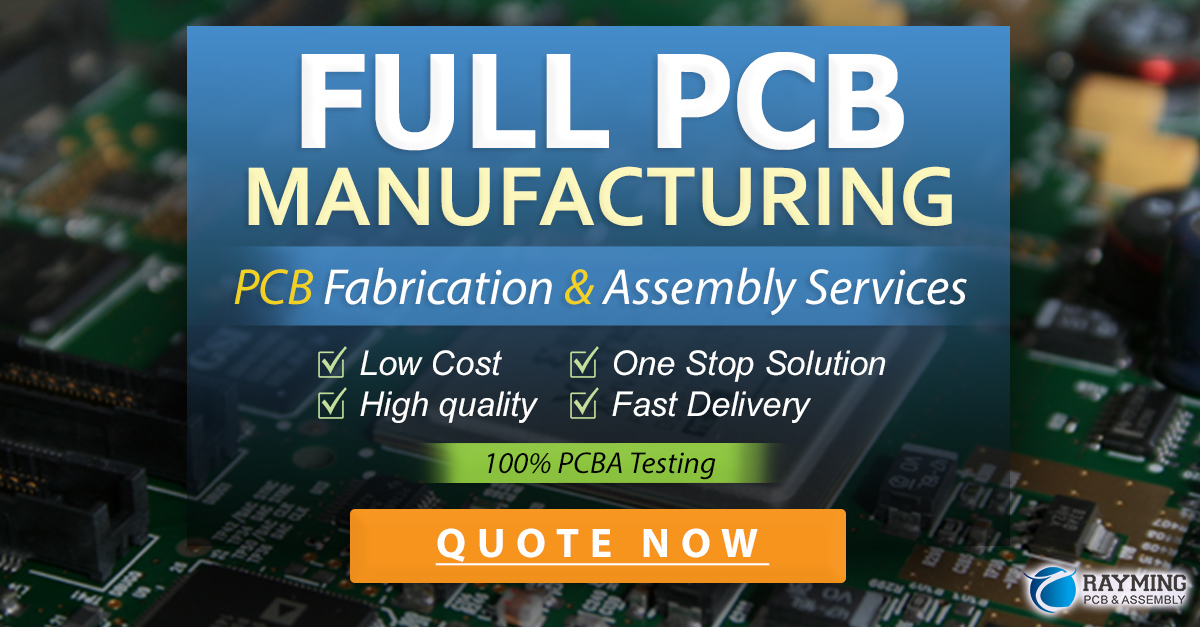
Designing PCBs with Hole Tolerances in Mind
To ensure successful PCB fabrication and assembly, designers must consider hole tolerances throughout the design process. Here are some best practices for designing PCBs with appropriate hole tolerances:
-
Choose the Right Nominal Hole Size: When selecting component packages and designing footprints, consider the nominal hole sizes that are readily available and compatible with your chosen manufacturing process. Avoid specifying hole sizes that are too small or too close to the tolerance limits, as this can increase the risk of manufacturing issues and assembly defects.
-
Communicate with Your Manufacturer: Engage with your PCB manufacturer early in the design process to discuss their capabilities, limitations, and recommended hole tolerances. They can provide valuable insights and guidance based on their specific equipment and processes, helping you design a board that is optimized for manufacturability.
-
Use Standardized Hole Sizes: Whenever possible, use standardized hole sizes that are common in the industry and compatible with a wide range of components and manufacturing processes. This can help reduce the risk of tolerance-related issues and ensure better availability of drills and tooling.
-
Allow for Plating Thickness: When specifying hole sizes, remember to account for the plating thickness that will be applied during the manufacturing process. The plating will reduce the finished hole diameter, so designers must compensate by specifying slightly larger drill sizes to achieve the desired finished hole size.
-
Consider the PCB Stack-Up: The thickness and composition of the PCB stack-up can affect hole tolerances, particularly for high aspect ratio holes. Work with your manufacturer to optimize the stack-up design for the specific hole sizes and tolerances required, considering factors such as drill wander, material properties, and plating requirements.
-
Implement Design for Manufacturing (DFM) Checks: Use DFM software tools to analyze your PCB design and identify potential hole tolerance issues before sending the design to manufacturing. These tools can flag holes that are too small, too close to the edge of the board, or violate other manufacturing constraints, allowing you to make necessary adjustments and avoid costly redesigns or production delays.
Best Practices for Manufacturing PCBs with Tight Hole Tolerances
For PCB manufacturers, achieving tight hole tolerances requires a combination of advanced equipment, optimized processes, and skilled operators. Some best practices for manufacturing PCBs with tight hole tolerances include:
-
Invest in High-Quality Drilling Equipment: Use modern, high-precision drilling machines that are capable of maintaining tight tolerances and minimizing drill wander. Regular maintenance and calibration of the equipment are essential for ensuring consistent hole quality.
-
Optimize Drilling Parameters: Carefully select and optimize drilling parameters, such as spindle speed, feed rate, and peck cycles, based on the specific PCB material, thickness, and hole size. Proper optimization can help reduce drill wear, minimize breakage, and improve hole quality.
-
Use High-Quality Drill Bits: Choose high-quality drill bits that are suitable for the specific PCB material and hole size range. Carbide drills are often preferred for their durability and ability to maintain sharp cutting edges, while diamond-coated drills can offer even better performance for challenging materials or high-volume production.
-
Implement Rigorous Quality Control: Establish a robust quality control system that includes regular hole size measurements, visual inspections, and cross-sectioning to verify hole quality and plating integrity. Use statistical process control (SPC) techniques to monitor and optimize the drilling process over time.
-
Collaborate with Customers: Work closely with your customers to understand their specific hole tolerance requirements and design constraints. Provide feedback and guidance on best practices for designing PCBs with achievable hole tolerances, and communicate any potential manufacturing challenges or limitations early in the process.
FAQ
- What is the difference between drill size and finished hole size?
-
The drill size refers to the diameter of the drill bit used to create the hole in the PCB, while the finished hole size is the final diameter of the hole after plating. The finished hole size will be smaller than the drill size due to the plating thickness.
-
How do I specify hole tolerances on my PCB design?
-
Hole tolerances are typically specified as a plus/minus deviation from the nominal hole size. For example, a 0.5 mm hole with a tolerance of ±0.05 mm would be specified as “0.5 ±0.05 mm.” Consult with your PCB manufacturer for their specific requirements and recommendations for specifying hole tolerances.
-
What is the smallest hole size that can be drilled in a PCB?
-
The smallest achievable hole size depends on various factors, such as the PCB material, thickness, aspect ratio, and the capabilities of the specific manufacturing process. In general, most PCB manufacturers can reliably drill holes down to 0.2 mm in diameter, with some specialized processes capable of even smaller sizes.
-
How do I ensure that my PCB design is compatible with the manufacturer’s hole tolerances?
-
To ensure compatibility, communicate with your PCB manufacturer early in the design process to discuss their capabilities and recommended hole tolerances. Use standardized hole sizes whenever possible, and consider the factors that can affect hole tolerances, such as PCB material, thickness, and plating requirements. Implement DFM checks to identify and address any potential hole tolerance issues before sending the design to manufacturing.
-
What are the consequences of not adhering to hole tolerances in PCB manufacturing?
- Failing to adhere to hole tolerances can lead to various manufacturing and assembly issues, such as component misalignment, poor solderability, and compromised electrical connections. In extreme cases, hole tolerance violations can result in non-functional or unreliable PCBs, leading to costly rework, delays, or even product failures in the field. Adhering to appropriate hole tolerances is crucial for ensuring the quality, reliability, and manufacturability of PCBs.
Conclusion
PCB hole tolerances play a critical role in ensuring the proper functionality, reliability, and manufacturability of printed circuit boards. By understanding the factors that influence hole tolerances, designing with industry standards and best practices in mind, and collaborating closely with PCB manufacturers, designers can create PCBs that are optimized for their specific applications and manufacturing processes.
As PCB technology continues to evolve, with ever-increasing complexity and miniaturization, the importance of hole tolerances will only grow. By staying informed about the latest developments in PCB materials, manufacturing processes, and design tools, engineers and manufacturers can work together to push the boundaries of what is possible in PCB fabrication while maintaining the highest levels of quality and reliability.
Leave a Reply