Understanding BOM and CPL
What is a Bill of Materials (BOM)?
A Bill of Materials (BOM) is a comprehensive list of all the components, parts, and materials required to manufacture a product. It serves as a blueprint for the production process, detailing the quantities, specifications, and relationships between each item. BOMs are essential for maintaining consistency, planning inventory, and estimating costs.
Types of BOMs
There are several types of BOMs, each serving a specific purpose:
-
Engineering BOM (EBOM): This type of BOM focuses on the product design and includes all the components and parts necessary to create the product from an engineering perspective.
-
Manufacturing BOM (MBOM): The MBOM is derived from the EBOM and is tailored to the manufacturing process. It considers the specific components, quantities, and assembly steps required for production.
-
Sales BOM (SBOM): The SBOM is a simplified version of the BOM used by the sales team to communicate the product structure and options to customers.
-
Service BOM: This BOM lists all the components and parts needed for product maintenance and repair.
BOM Type | Purpose |
---|---|
Engineering BOM (EBOM) | Product design and engineering |
Manufacturing BOM (MBOM) | Production process and assembly |
Sales BOM (SBOM) | Customer communication and product options |
Service BOM | Maintenance and repair |
What is a Component Parts List (CPL)?
A Component Parts List (CPL) is a document that provides detailed information about each component or part listed in the BOM. It includes specifications such as part numbers, descriptions, suppliers, and lead times. The CPL is crucial for procurement, inventory management, and ensuring the right components are available when needed.
CPL Data Fields
A typical CPL includes the following data fields:
- Part Number
- Description
- Supplier Information
- Lead Time
- Unit of Measure
- Cost
- Quantity Required
Data Field | Description |
---|---|
Part Number | Unique identifier for each component |
Description | Detailed information about the component |
Supplier Information | Details about the supplier, including name and contact information |
Lead Time | The time required to procure the component |
Unit of Measure | The unit in which the component is measured (e.g., pieces, meters) |
Cost | The price of the component |
Quantity Required | The number of components needed for production |
BOM and CPL Management
Best Practices for Creating BOMs
Creating accurate and comprehensive BOMs is crucial for streamlining the production process. Here are some best practices to follow:
-
Use a Hierarchical Structure: Organize the BOM in a hierarchical manner, starting with the finished product at the top and breaking it down into subassemblies and individual components.
-
Include Revision Control: Implement a revision control system to track changes made to the BOM over time. This helps maintain accuracy and ensures everyone is working with the latest version.
-
Collaborate with Cross-Functional Teams: Involve teams from engineering, manufacturing, procurement, and quality control in the BOM creation process to ensure all necessary information is captured.
-
Maintain Consistency: Use consistent naming conventions, part numbers, and descriptions throughout the BOM to avoid confusion and errors.
Efficient CPL Management Techniques
Managing CPL data effectively is essential for optimizing inventory levels and ensuring smooth procurement processes. Consider the following techniques:
-
Centralize CPL Data: Maintain a centralized database for CPL information, accessible to all relevant teams. This ensures everyone has access to the most up-to-date data.
-
Regularly Update Supplier Information: Keep supplier information current, including lead times, pricing, and contact details. This helps in making informed procurement decisions and prevents delays.
-
Implement Automation: Utilize software solutions or PLM (Product Lifecycle Management) systems to automate CPL data management, reducing manual efforts and minimizing errors.
-
Conduct Regular Audits: Perform periodic audits of CPL data to identify and rectify any discrepancies or outdated information.
Integrating BOM and CPL Data
Benefits of BOM-CPL Integration
Integrating BOM and CPL data offers several benefits:
-
Enhanced Visibility: Integration provides a holistic view of the product structure and component details, enabling better decision-making.
-
Improved Efficiency: Seamless data flow between BOM and CPL reduces manual data entry and minimizes errors.
-
Faster Time-to-Market: Integration streamlines the production process, allowing for quicker product development and launch.
-
Cost Optimization: By having accurate BOM and CPL data, organizations can optimize inventory levels, reduce waste, and negotiate better prices with suppliers.
Integration Strategies
Here are some strategies for integrating BOM and CPL data:
-
Utilize PLM Systems: Implement a PLM system that enables the creation, management, and integration of BOM and CPL data in a single platform.
-
Establish Data Standards: Define clear data standards and formats for BOM and CPL information to ensure consistency and ease of integration.
-
Implement Electronic Data Interchange (EDI): Use EDI to exchange BOM and CPL data electronically with suppliers, reducing manual effort and improving accuracy.
-
Leverage APIs: Utilize APIs (Application Programming Interfaces) to integrate BOM and CPL data with other enterprise systems, such as ERP (Enterprise Resource Planning) or MRP (Material Requirements Planning).
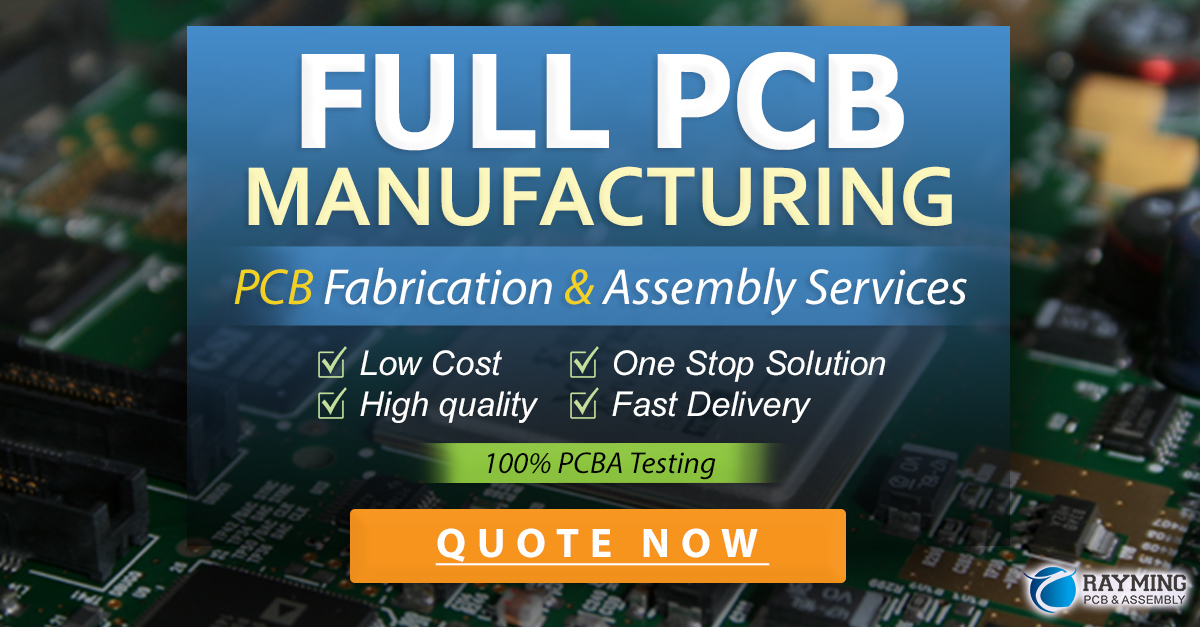
Common Challenges and Solutions
Dealing with BOM and CPL Discrepancies
Discrepancies between BOM and CPL data can lead to production delays and inventory issues. To address this challenge:
-
Establish Clear Communication Channels: Ensure effective communication between engineering, manufacturing, and procurement teams to identify and resolve discrepancies promptly.
-
Implement Change Management Processes: Establish formal change management processes to track and approve changes to BOM and CPL data.
-
Conduct Regular Reconciliations: Perform periodic reconciliations between BOM and CPL data to identify and rectify any inconsistencies.
Managing BOM and CPL Data for Complex Products
Managing BOM and CPL data for complex products with numerous components can be challenging. Consider the following solutions:
-
Modularize the Product Structure: Break down complex products into smaller, manageaBLE Modules, each with its own BOM and CPL.
-
Utilize Variant Management: Implement variant management techniques to handle product variations and customize BOMs and CPLs accordingly.
-
Employ Advanced Software Tools: Utilize specialized software solutions designed to handle complex BOM and CPL structures, such as PLM systems with advanced configuration management capabilities.
Frequently Asked Questions (FAQ)
-
What is the difference between BOM and CPL?
A BOM (Bill of Materials) is a list of all the components and materials required to manufacture a product, while a CPL (Component Parts List) provides detailed information about each component listed in the BOM. -
Why is it important to maintain accurate BOM and CPL data?
Accurate BOM and CPL data is crucial for ensuring smooth production processes, effective inventory management, cost optimization, and timely product delivery. -
How often should I update my BOM and CPL data?
BOM and CPL data should be updated whenever there are changes to the product design, components, suppliers, or specifications. It is recommended to review and update the data regularly to maintain accuracy. -
Can I use the same BOM for different product variations?
While the core components may remain the same, it is advisable to create separate BOMs for different product variations to accurately capture the specific components and quantities required for each variant. -
What are the consequences of poor BOM and CPL management?
Poor BOM and CPL management can lead to production delays, inventory shortages or excesses, increased costs, quality issues, and customer dissatisfaction.
Conclusion
BOM and CPL data are the backbone of effective manufacturing and product development processes. By understanding their significance, implementing best practices, and leveraging integration strategies, organizations can streamline operations, optimize costs, and improve overall efficiency. Remember to maintain accurate and up-to-date BOM and CPL data, foster collaboration among teams, and continuously assess and refine your processes. With these tips and tricks in mind, you can harness the full potential of BOM and CPL data to drive success in your manufacturing endeavors.
Leave a Reply