What is PCB Edge Clearance?
PCB edge clearance refers to the minimum distance that must be maintained between the edge of a printed circuit board (PCB) and any copper traces, components, or other conductive elements. This clearance is crucial for ensuring the structural integrity and functionality of the PCB, as well as compliance with industry standards and manufacturing requirements.
Why is PCB Edge Clearance Important?
Maintaining proper PCB edge clearance is essential for several reasons:
-
Manufacturing Reliability: Adequate edge clearance helps prevent damage to the PCB during the manufacturing process, especially during depaneling or singulation.
-
Mechanical Strength: Sufficient distance between the edge and conductive elements reduces the risk of cracks or fractures due to mechanical stress.
-
Electrical Insulation: Proper edge clearance helps maintain electrical insulation and prevents short circuits or signal interference.
-
Compliance with Standards: Many industry standards, such as IPC-2221, specify minimum edge clearance requirements to ensure quality and reliability.
Factors Affecting PCB Edge Clearance
Several factors influence the determination of appropriate PCB edge clearance:
PCB Thickness
The thickness of the PCB is a critical factor in determining edge clearance. Thicker boards generally require larger edge clearances to accommodate the increased mechanical stress during handling and assembly.
PCB Thickness | Minimum Edge Clearance |
---|---|
0.8 mm | 0.5 mm |
1.6 mm | 1.0 mm |
2.4 mm | 1.5 mm |
Copper Weight
The weight or thickness of the copper traces on the PCB also affects edge clearance requirements. Heavier copper weights may necessitate larger clearances to prevent delamination or cracking.
Copper Weight | Minimum Edge Clearance |
---|---|
0.5 oz | 0.5 mm |
1.0 oz | 0.8 mm |
2.0 oz | 1.2 mm |
PCB Material
The choice of PCB material can influence edge clearance requirements. Some materials, such as high-frequency laminates or flexible substrates, may have specific clearance guidelines to ensure optimal performance and reliability.
Manufacturing Process
The manufacturing process used to fabricate the PCB can also impact edge clearance. For example, PCBs that undergo scoring or V-groove singulation may require larger clearances compared to those that are routed or milled.
Best Practices for PCB Edge Clearance
To ensure optimal PCB design and manufacturing, consider the following best practices:
Adhere to Industry Standards
Follow the guidelines provided by industry standards such as IPC-2221 or IPC-6012 when determining edge clearance requirements. These standards offer specific recommendations based on PCB thickness, copper weight, and other factors.
Communicate with Manufacturers
Engage in open communication with your PCB manufacturer to discuss their specific edge clearance requirements and capabilities. Some manufacturers may have stricter guidelines or additional recommendations based on their equipment and processes.
Consider PCB Panelization
When designing a PCB, consider the panelization layout and how it will affect edge clearance. Ensure that the panel design allows for sufficient clearance between individual boards and the panel edges.
Perform Design Rule Checks (DRC)
Utilize PCB design software that includes Design Rule Check (DRC) functionality to automatically verify edge clearance and other design guidelines. This helps identify and resolve any clearance violations before proceeding to manufacturing.
Account for Tolerances
Incorporate appropriate tolerances when defining edge clearance to accommodate potential variations in manufacturing processes or material properties. This may involve adding a safety margin to the minimum clearance values specified in standards or by manufacturers.
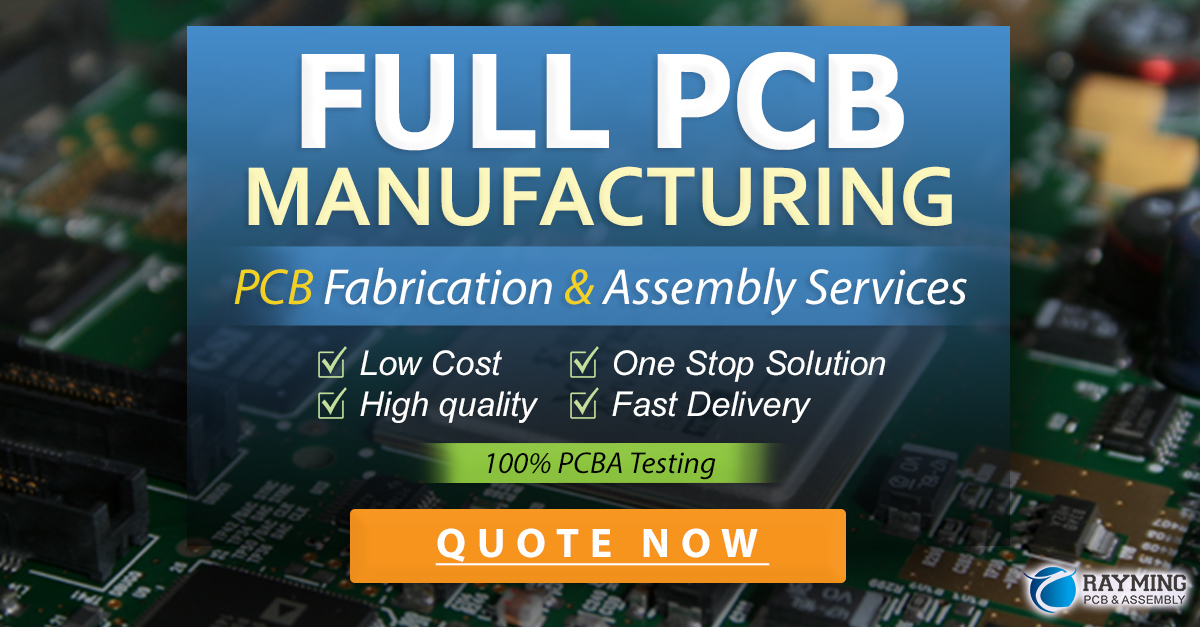
Frequently Asked Questions (FAQ)
- What happens if PCB edge clearance is insufficient?
Insufficient PCB edge clearance can lead to various issues, such as: - Damage to the PCB during manufacturing or handling
- Increased risk of cracks or fractures due to mechanical stress
- Potential short circuits or signal interference
-
Non-compliance with industry standards
-
How do I determine the appropriate edge clearance for my PCB?
To determine the appropriate edge clearance for your PCB, consider the following factors: - PCB thickness
- Copper weight
- PCB material
-
Manufacturing process
Consult industry standards, such as IPC-2221 or IPC-6012, and communicate with your PCB manufacturer for specific guidelines and recommendations. -
Can I use the same edge clearance for all PCB designs?
No, edge clearance requirements may vary depending on the specific characteristics of each PCB design, such as thickness, copper weight, material, and manufacturing process. It is essential to evaluate edge clearance on a case-by-case basis and consult relevant standards and manufacturer guidelines. -
What are the consequences of non-compliance with industry standards for edge clearance?
Non-compliance with industry standards for edge clearance can result in several consequences, including: - Reduced PCB reliability and performance
- Increased risk of manufacturing defects or failures
- Potential rejection by customers or regulatory bodies
-
Liability issues in case of product failures or safety concerns
-
How can I verify edge clearance compliance in my PCB design?
To verify edge clearance compliance in your PCB design, follow these steps: - Use PCB design software with Design Rule Check (DRC) functionality to automatically check clearance values
- Visually inspect the PCB layout to identify any potential clearance violations
- Communicate with your PCB manufacturer and provide them with the design files for their review and feedback
- Conduct thorough testing and inspection of manufactured PCBs to ensure compliance with clearance requirements
Conclusion
PCB edge clearance is a critical aspect of PCB design that ensures the structural integrity, functionality, and reliability of the final product. By understanding the factors affecting edge clearance, adhering to industry standards, and following best practices, designers can create PCBs that meet manufacturing requirements and perform optimally in their intended applications.
Effective communication with PCB manufacturers, utilization of design tools, and thorough testing and inspection are essential for achieving edge clearance compliance and avoiding potential issues during manufacturing or in the field. By prioritizing edge clearance considerations throughout the design process, PCB designers can contribute to the development of high-quality, reliable electronic products.
Leave a Reply