Introduction to Purple PCB
Purple PCBs, also known as purple solder mask PCBs, have gained popularity in recent years due to their unique appearance and aesthetic appeal. These printed circuit boards feature a distinctive purple color on the solder mask layer, which not only adds visual interest but also provides various benefits in terms of functionality and durability.
In this article, we will explore the world of purple PCBs, discussing their manufacturing process, advantages, applications, and more. Whether you are an electronics enthusiast, a designer, or simply curious about this fascinating technology, this comprehensive guide will provide you with valuable insights into purple color solder mask PCBs.
What is a Purple PCB?
A purple PCB is a printed circuit board that utilizes a purple-colored solder mask layer. The solder mask is a thin, protective coating applied to the copper traces and pads on the PCB surface. Its primary purpose is to prevent solder bridging and short circuits during the soldering process, as well as to protect the copper from oxidation and environmental factors.
Traditionally, green has been the most common color for solder masks due to its excellent contrast with copper traces and its ability to hide imperfections. However, advancements in PCB manufacturing technologies have enabled the production of solder masks in various colors, including purple, red, blue, black, and white.
Purple PCBs have gained attention not only for their eye-catching appearance but also for their practical benefits. The purple color offers good contrast against copper traces, making it easier for engineers and technicians to inspect and troubleshoot the board. Additionally, purple solder masks have been found to provide excellent resistance to UV light, making them suitable for outdoor applications.
Manufacturing Process of Purple PCBs
The manufacturing process of purple PCBs follows the same general steps as other printed circuit boards, with a few specific considerations for the purple solder mask. Here is an overview of the key stages involved in creating a purple PCB:
-
PCB Design: The first step is to design the PCB layout using specialized software. The design includes the placement of components, routing of copper traces, and the creation of solder mask and silkscreen layers.
-
PCB Fabrication: Once the design is finalized, the PCB fabrication process begins. This involves the following sub-steps:
- Substrate preparation: The base material, typically FR-4 (a glass-reinforced epoxy laminate), is cut to the desired size and shape.
- Copper lamination: Copper foil is laminated onto the substrate using heat and pressure.
- Drilling: Holes are drilled into the board for through-hole components and vias.
- Copper patterning: The unwanted copper is etched away, leaving behind the desired circuit pattern.
- Solder mask application: The purple solder mask is applied to the board using screen printing or photoimaging techniques. The solder mask is then cured using UV light or heat.
- Surface finish: A surface finish, such as HASL (Hot Air Solder Leveling) or ENIG (Electroless Nickel Immersion Gold), is applied to the exposed copper areas to prevent oxidation and enhance solderability.
-
Silkscreen printing: The silkscreen layer, which includes text and symbols, is printed onto the board for component identification and assembly guidance.
-
PCB Assembly: After the fabrication process, the PCB is ready for assembly. This involves soldering components onto the board, either through manual soldering or automated processes like SMT (Surface Mount Technology) and wave soldering.
-
Testing and Inspection: The assembled purple PCB undergoes rigorous testing and inspection to ensure its functionality, reliability, and adherence to quality standards. This may include visual inspections, automated optical inspections (AOI), and electrical tests.
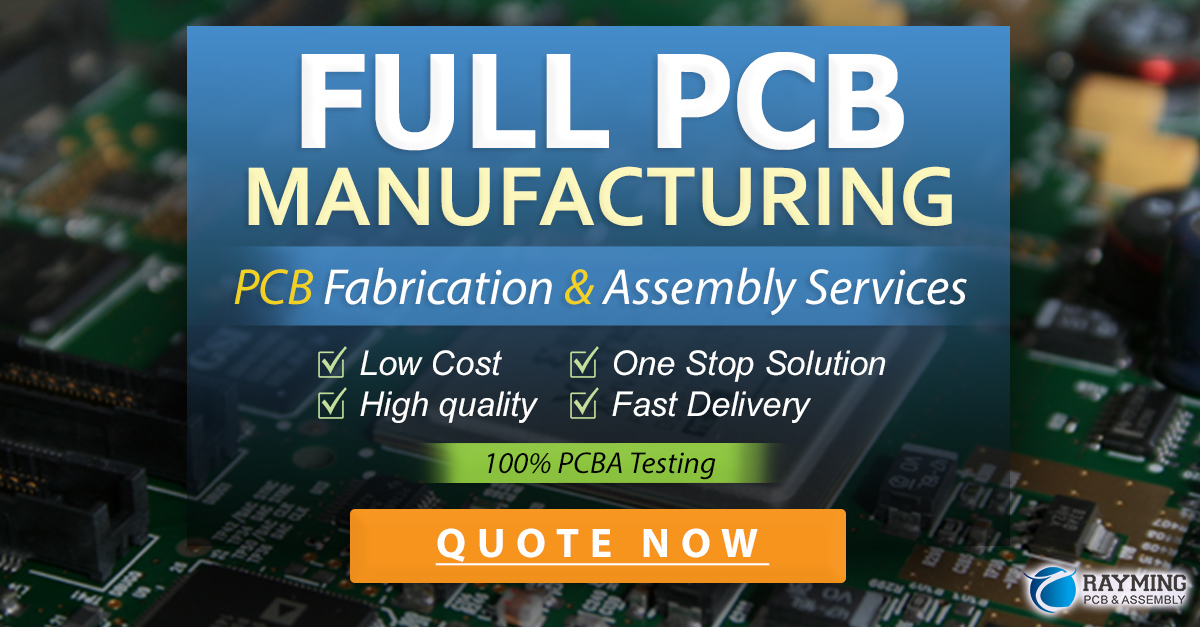
Advantages of Purple PCBs
Purple PCBs offer several advantages over traditional green solder mask PCBs. Let’s explore some of the key benefits:
-
Enhanced Visual Appeal: The unique purple color of these PCBs adds a distinctive and attractive appearance to electronic devices. This can be particularly advantageous for consumer electronics, where aesthetics play a significant role in product differentiation and customer appeal.
-
Improved Contrast and Visibility: Purple solder masks provide excellent contrast against copper traces, making it easier for engineers and technicians to inspect and troubleshoot the board. The enhanced visibility can help identify potential issues, such as solder bridges or damaged traces, more efficiently.
-
UV Resistance: Purple solder masks have been found to exhibit better resistance to UV light compared to other colors. This property makes purple PCBs suitable for outdoor applications or devices exposed to direct sunlight, as the solder mask is less likely to degrade or discolor over time.
-
Durability and Protection: The purple solder mask acts as a protective layer, shielding the copper traces and pads from oxidation, scratches, and other environmental factors. This added protection enhances the overall durability and longevity of the PCB.
-
Customization Options: Purple PCBs offer a unique opportunity for customization and branding. Manufacturers can incorporate logos, text, or patterns onto the purple solder mask layer, creating a distinctive and personalized look for their products.
-
Compatibility with Various Surface Finishes: Purple solder masks are compatible with a range of surface finishes, including HASL, ENIG, and OSP (Organic Solderability Preservative). This versatility allows manufacturers to choose the most suitable surface finish for their specific application and requirements.
Applications of Purple PCBs
Purple PCBs find applications across various industries and sectors, including:
-
Consumer Electronics: Purple PCBs are increasingly used in consumer electronic devices, such as smartphones, tablets, wearables, and gaming consoles. The attractive purple color adds a unique visual appeal to these products, making them stand out in a competitive market.
-
Automotive Electronics: The automotive industry utilizes purple PCBs in various electronic systems, such as infotainment displays, instrument clusters, and advanced driver assistance systems (ADAS). The enhanced contrast and UV resistance of purple solder masks make them suitable for the demanding automotive environment.
-
Medical Devices: Purple PCBs are employed in medical devices, including diagnostic equipment, monitoring systems, and wearable health trackers. The durability and protection offered by the purple solder mask ensure reliable performance in critical medical applications.
-
Industrial Automation: Purple PCBs are used in industrial automation systems, such as programmable logic controllers (PLCs), sensors, and human-machine interfaces (HMIs). The improved visibility and contrast of purple solder masks aid in the efficient troubleshooting and maintenance of these systems.
-
Aerospace and Defense: The aerospace and defense sectors utilize purple PCBs in various applications, including avionics, communication systems, and military equipment. The UV resistance and durability of purple solder masks make them suitable for the harsh environments encountered in these industries.
-
IoT Devices: With the proliferation of the Internet of Things (IoT), purple PCBs are increasingly used in IoT devices, such as smart home appliances, Wearable Technology, and industrial sensors. The visual appeal and customization options of purple PCBs can enhance the aesthetics of these connected devices.
Choosing the Right Purple PCB Manufacturer
When selecting a purple PCB manufacturer, several factors should be considered to ensure high-quality and reliable boards. Here are some key criteria to keep in mind:
-
Experience and Expertise: Look for a manufacturer with extensive experience in producing purple PCBs. They should have a proven track record of delivering high-quality boards and possess the necessary technical expertise to handle complex designs and specifications.
-
Manufacturing Capabilities: Ensure that the manufacturer has the necessary equipment and facilities to produce purple PCBs efficiently and consistently. They should employ state-of-the-art manufacturing technologies and adhere to strict quality control processes.
-
Material Selection: Choose a manufacturer that uses high-quality materials for the purple solder mask and other PCB Components. The solder mask should be durable, UV-resistant, and compatible with the intended surface finish.
-
Certifications and Standards: Verify that the manufacturer holds relevant certifications and complies with industry standards, such as ISO 9001, IPC, and UL. These certifications demonstrate their commitment to quality and reliability.
-
Customer Support: Select a manufacturer that provides excellent customer support throughout the entire PCB manufacturing process. They should be responsive to inquiries, offer technical assistance, and provide timely updates on the project status.
-
Lead Time and Pricing: Consider the manufacturer’s lead time and pricing structure. While cost is an important factor, it should not compromise the quality and reliability of the purple PCBs. Strike a balance between competitive pricing and ensuring that the manufacturer can deliver the boards within the required timeframe.
Frequently Asked Questions (FAQ)
-
Q: Are purple PCBs more expensive than traditional green PCBs?
A: Purple PCBs may be slightly more expensive than green PCBs due to the specialized solder mask material and the additional processing steps involved. However, the cost difference is usually marginal and varies depending on the manufacturer and the specific requirements of the project. -
Q: Can purple PCBs be used for high-frequency applications?
A: Yes, purple PCBs can be used for high-frequency applications. The choice of solder mask color does not directly impact the electrical performance of the PCB. However, it is essential to ensure that the purple solder mask material is compatible with the desired dielectric properties and meets the specific requirements of the high-frequency application. -
Q: Are purple PCBs suitable for lead-free soldering processes?
A: Yes, purple PCBs are compatible with lead-free soldering processes. The purple solder mask material is designed to withstand the higher temperatures associated with lead-free soldering, ensuring the integrity and reliability of the solder joints. -
Q: Can purple PCBs be manufactured with different surface finishes?
A: Yes, purple PCBs can be manufactured with various surface finishes, such as HASL, ENIG, and OSP. The choice of surface finish depends on the specific requirements of the application, including solderability, durability, and cost considerations. -
Q: How do I specify the purple color when ordering PCBs?
A: When ordering purple PCBs, you can specify the desired color using industry-standard color codes or by providing a Pantone color reference. Most PCB manufacturers have a range of standard purple solder mask options available, but custom colors can also be accommodated upon request. It is advisable to discuss the specific color requirements with the manufacturer to ensure a perfect match.
Conclusion
Purple color solder mask PCBs have emerged as a popular choice for electronics manufacturers and designers, offering a unique combination of aesthetic appeal, functionality, and durability. With their distinctive purple color, enhanced contrast, and UV resistance, purple PCBs find applications across various industries, from consumer electronics to automotive, medical, and industrial sectors.
When considering purple PCBs for your next project, it is crucial to partner with a reputable and experienced PCB manufacturer. Look for a manufacturer that employs advanced manufacturing technologies, uses high-quality materials, and adheres to strict quality control processes. By selecting the right manufacturer and leveraging the benefits of purple PCBs, you can create visually stunning and reliable electronic products that stand out in the market.
As the electronics industry continues to evolve, purple PCBs are poised to play an increasingly important role in shaping the future of printed circuit board technology. With their unique properties and growing popularity, purple PCBs offer exciting opportunities for innovation, customization, and differentiation in the ever-competitive world of electronics manufacturing.
Characteristic | Purple PCB | Traditional Green PCB |
---|---|---|
Visual Appeal | Unique and attractive purple color | Standard green color |
Contrast and Visibility | Enhanced contrast against copper traces | Good contrast, but not as prominent as purple |
UV Resistance | Excellent resistance to UV light | Adequate UV resistance, but may degrade over time |
Durability and Protection | Protective layer against oxidation and scratches | Similar protection, but purple may offer additional benefits |
Customization Options | Allows for logos, text, and patterns on the solder mask | Limited customization options |
Cost | Slightly higher due to specialized materials and processing | Generally less expensive |
In conclusion, purple color solder mask PCBs offer a compelling combination of aesthetics, performance, and reliability. As the demand for visually appealing and high-quality electronic products continues to grow, purple PCBs are well-positioned to meet the evolving needs of manufacturers and consumers alike. By embracing this innovative technology and partnering with skilLED PCB manufacturers, companies can unlock new possibilities in electronic design and differentiate themselves in an increasingly competitive market.
Leave a Reply