How AXI Works
X-ray Imaging Principles
AXI systems work by generating X-rays and directing them through the PCBA being inspected. As X-rays pass through the board, they are attenuated differently depending on the density and thickness of the materials they encounter. Denser materials like metals absorb more X-rays compared to less dense materials like plastics and air gaps. The X-rays that pass through the PCBA are then captured by a detector, creating a grayscale image where darker areas represent denser materials and lighter areas represent less dense ones.
AXI System Components
A typical AXI system consists of several key components:
- X-ray source: Generates the X-rays used for imaging. Common types include sealed tube and open tube sources.
- Manipulator: Moves and positions the PCBA within the X-ray beam to capture images from different angles.
- Detector: Captures the X-rays that pass through the PCBA and converts them into a digital image. Flat panel detectors are most commonly used.
- Image processing software: Analyzes the captured X-ray images to identify defects and anomalies based on predefined criteria.
- User interface: Allows operators to control the system, view inspection results, and manage data.
Inspection Techniques
AXI systems employ various imaging techniques to inspect different aspects of PCBAs:
- 2D X-ray: Provides a top-down view of the PCBA, useful for detecting component presence, absence, and placement issues.
- Oblique view: Captures angled images of the PCBA to inspect solder joints and other features that may be obscured in a 2D view.
- 3D X-ray: Uses computed tomography (CT) to generate a 3D reconstructed image of the PCBA, allowing for detailed inspection of internal structures.
- Laminography: A technique that focuses the X-ray beam on a specific layer within the PCBA, useful for inspecting multilayer boards.
Benefits of AXI
Improved Defect Detection
One of the primary benefits of AXI is its ability to detect a wide range of defects that are difficult or impossible to identify with other inspection methods. These include:
- Solder joint defects (voids, insufficient solder, bridges)
- Component placement issues (misalignment, tombstoning)
- Missing or incorrect components
- PCB Fabrication defects (broken traces, delamination)
By detecting these defects early in the manufacturing process, AXI helps prevent costly rework and reduce overall product failure rates.
Increased Inspection Speed
AXI systems can inspect PCBAs much faster than manual inspection methods. Modern AXI machines can scan a typical PCBA in just a few seconds, enabling high-volume production lines to maintain throughput while ensuring consistent quality control. This speed advantage becomes even more significant as PCBA complexity increases and manual inspection times lengthen.
Objective and Repeatable Results
AXI provides objective and repeatable inspection results by using predefined inspection criteria and automated analysis algorithms. This eliminates the subjectivity and variability associated with human inspectors, ensuring consistent quality standards across production runs. AXI also generates detailed inspection reports that can be used for traceability and process improvement purposes.
Inspection of Hidden Features
AXI’s ability to “see through” PCBAs allows it to inspect features that are hidden from view, such as:
- Solder joints under BGAs and other high-density packages
- Plated through-holes and vias
- Internal layers of multilayer boards
This capability is crucial for modern electronics manufacturing, where increasing component density and board complexity make visual inspection of these features impractical.
Applications of AXI
AXI is used across a wide range of electronics manufacturing applications, including:
- Consumer electronics
- Automotive electronics
- Aerospace and defense systems
- Medical devices
- Industrial control systems
- Telecommunications equipment
The specific inspection requirements and challenges vary depending on the application, but AXI’s versatility and adaptability make it a valuable tool for ensuring quality control in diverse manufacturing environments.
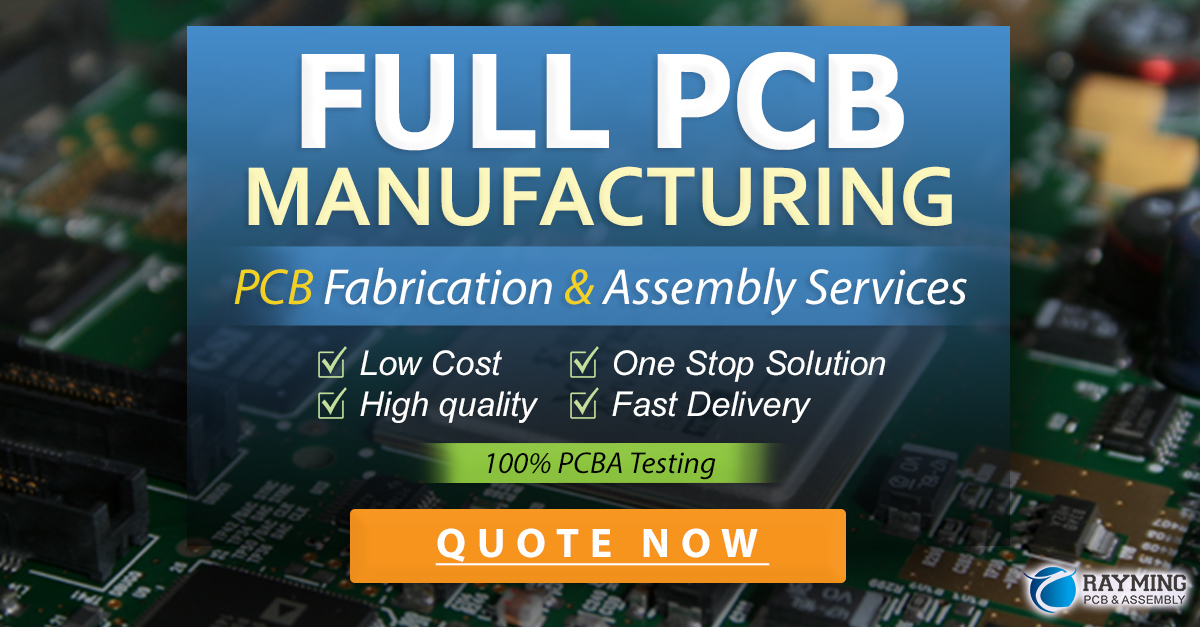
Implementing AXI
Selecting an AXI System
When selecting an AXI system for a specific application, several factors should be considered:
- Inspection requirements: The system should be capable of detecting the types of defects and features relevant to the application, with appropriate resolution and accuracy.
- Throughput: The system should have sufficient inspection speed to meet production volume requirements without creating bottlenecks.
- PCBA characteristics: The system should be compatible with the size, complexity, and material composition of the PCBAs being inspected.
- Integration: The system should be able to integrate with existing manufacturing processes and data management systems.
- Cost: The total cost of ownership, including upfront equipment costs, maintenance, and operator training, should be considered.
Inspection Program Development
Developing an effective AXI inspection program involves several key steps:
- CAD data import: The PCBA’s CAD data is imported into the AXI system to create a reference model for inspection.
- Inspection recipe creation: An inspection recipe is created, specifying the features to be inspected, acceptance criteria, and imaging parameters.
- Customization and optimization: The inspection recipe is fine-tuned to minimize false calls and ensure reliable defect detection for the specific PCBA.
- Verification and validation: The inspection program is tested on a representative sample of PCBAs to verify its performance and validate the results.
Integration with Manufacturing Processes
To maximize the benefits of AXI, it should be integrated into the overall manufacturing process as a key quality control step. This typically involves:
- Placing the AXI system at the appropriate point in the production line (e.g., after solder reflow)
- Establishing data connectivity between the AXI system and other manufacturing systems (e.g., MES, SPC)
- Defining workflows for handling defective PCBAs identified by AXI (e.g., repair, rework, scrap)
- Training operators on AXI system use and results interpretation
Future Trends in AXI
As electronics manufacturing continues to evolve, AXI technology is advancing to keep pace with new challenges and requirements. Some key trends shaping the future of AXI include:
Increased Adoption of 3D AXI
3D AXI using CT is becoming more widely adopted for inspecting complex PCBAs with high component density and multi-layer structures. As 3D AXI systems become faster and more cost-effective, they are expected to play a larger role in quality control for advanced electronics manufacturing.
Integration with AI and Machine Learning
AXI systems are increasingly incorporating artificial intelligence (AI) and machine learning (ML) techniques to enhance defect detection and classification capabilities. AI/ML algorithms can automatically learn and adapt to new defect patterns, reducing the need for manual algorithm tuning and enabling faster New Product Introduction.
Inline AXI
Inline AXI systems that can inspect PCBAs directly on the production line without requiring off-line batch processing are becoming more common. These systems enable real-time quality control feedback and faster identification of process issues, reducing scrap and rework costs.
Big Data Analytics
AXI systems generate vast amounts of data on PCBA quality and process performance. Advances in big data analytics tools are enabling manufacturers to better leverage this data for process optimization, traceability, and predictive maintenance.
FAQ
What are the limitations of AXI?
While AXI is a powerful inspection tool, it does have some limitations:
– X-ray imaging may not be suitable for inspecting certain materials (e.g., very thick or dense PCBAs)
– AXI cannot detect all types of defects (e.g., functional or electrical issues)
– AXI systems can be expensive to purchase and maintain compared to other inspection methods
Is AXI safe for operators?
Yes, modern AXI systems are designed with operator safety in mind. The X-ray sources are typically enclosed and shielded to prevent exposure, and safety interlocks prevent operation when the enclosure is open. However, proper training and safety procedures should still be followed when working with AXI equipment.
Can AXI be used for inspecting non-electronic products?
While AXI is primarily used for electronics inspection, the underlying X-ray imaging technology can be applied to inspect other types of products, such as mechanical assemblies, welded structures, and composite materials. However, the specific inspection requirements and challenges will differ from electronics applications.
How does AXI compare to other inspection methods?
AXI offers several advantages over other inspection methods:
– Compared to manual visual inspection, AXI is faster, more objective, and can detect hidden defects
– Compared to automated optical inspection (AOI), AXI can inspect features that are obscured from view, such as solder joints under components
– Compared to electrical testing, AXI can detect physical defects that may not immediately cause electrical failures
However, AXI is typically more expensive than these other methods and may not be necessary for all applications. A comprehensive quality control strategy often involves using multiple inspection methods in combination.
What training is required for AXI operators?
AXI operators should be trained on the specific equipment they will be using, as well as general principles of X-ray imaging and PCBA inspection. Key topics include:
– System operation and maintenance
– Safety procedures
– Inspection program development and optimization
– Results interpretation and defect classification
– Data management and reporting
The exact training requirements will depend on the specific AXI system and application, but a combination of classroom instruction and hands-on experience is typically recommended.
Conclusion
Automated X-ray Inspection is a powerful and versatile tool for ensuring quality control in electronics manufacturing. By providing fast, objective, and reliable inspection of hidden features, AXI helps manufacturers detect and prevent defects that can lead to costly failures and repairs. As PCBA complexity continues to increase and quality requirements become more stringent, AXI will play an increasingly critical role in ensuring the reliability and performance of electronic products across a wide range of industries.
However, implementing AXI effectively requires careful consideration of inspection requirements, system capabilities, and integration with existing manufacturing processes. As AXI technology continues to advance, with increased adoption of 3D imaging, AI/ML, inline inspection, and big data analytics, manufacturers will have even more powerful tools at their disposal for optimizing quality control and driving continuous improvement.
By staying at the forefront of AXI technology and best practices, electronics manufacturers can position themselves to meet the evolving challenges of the industry and deliver high-quality, reliable products to their customers.
Some key data related to AXI:
Defect Type | Typical AXI Detection Rate |
---|---|
Solder joint voids | 90-95% |
Insufficient solder | 85-90% |
Solder bridges | 95-98% |
Component placement errors | 90-95% |
Missing components | 98-100% |
PCBA Complexity | Typical AXI Inspection Time |
---|---|
Simple (< 100 components) | 5-10 seconds |
Moderate (100-500 components) | 10-30 seconds |
Complex (> 500 components) | 30-60 seconds |
Industry | Typical AXI Adoption Rate |
---|---|
Consumer electronics | 75-85% |
Automotive | 85-95% |
Aerospace/Defense | 90-100% |
Medical devices | 80-90% |
Industrial controls | 70-80% |
These data points highlight the effectiveness of AXI for detecting common defect types, the inspection speed advantages for complex PCBAs, and the high adoption rates across critical industries where quality and reliability are paramount. As AXI continues to evolve and improve, these benefits will only become more pronounced, cementing its position as an indispensable tool for electronics manufacturing quality control.
Leave a Reply