Understanding PCB Inductance
In the world of printed circuit board (PCB) design, inductance is a crucial factor that can significantly impact the performance of your electronic circuits. PCB inductance refers to the ability of a PCB trace to store energy in a magnetic field when an electric current flows through it. This stored energy can lead to unwanted effects such as signal integrity issues, electromagnetic interference (EMI), and Power Supply noise.
To ensure optimal performance and minimize these unwanted effects, it is essential to understand how to calculate the inductance of a PCB trace accurately. In this comprehensive guide, we will delve into the fundamentals of PCB inductance, explore various methods for calculating trace inductance, and provide practical examples to help you master this critical aspect of PCB design.
What is PCB Inductance?
Before we dive into the calculation methods, let’s define what PCB inductance is. Inductance is a measure of a conductor’s ability to store energy in a magnetic field when an electric current flows through it. In the context of PCBs, the traces on the board act as conductors, and their geometry, along with the surrounding environment, determines their inductance.
The inductance of a PCB trace is influenced by several factors, including:
- Trace length
- Trace width
- Trace thickness
- Dielectric constant of the PCB material
- Proximity to other traces and components
Understanding these factors is crucial for accurately calculating the inductance of a PCB trace and optimizing your designs accordingly.
Why is PCB Inductance Important?
PCB inductance plays a vital role in the performance and reliability of electronic circuits. Here are some key reasons why understanding and managing PCB inductance is essential:
-
Signal Integrity: High inductance in PCB Traces can lead to signal integrity issues, such as ringing, overshoot, and undershoot. These issues can cause false triggering, data errors, and other undesirable effects, compromising the reliability of your electronic systems.
-
Electromagnetic Interference (EMI): PCB traces with high inductance can act as antennas, radiating electromagnetic energy and causing interference with nearby electronic devices. This can lead to compliance issues and degrade the overall performance of your system.
-
Power Supply Noise: Inductance in power supply traces can contribute to power supply noise, such as voltage spikes and drops. This noise can propagate throughout the PCB, affecting the stability and reliability of the entire system.
-
High-Speed Design: As electronic systems operate at increasingly higher frequencies, the impact of PCB inductance becomes more pronounced. Accurately calculating and managing trace inductance is crucial for ensuring the proper functioning of high-speed circuits.
By understanding and effectively managing PCB inductance, you can improve signal integrity, reduce EMI, minimize power supply noise, and optimize the performance of your high-speed designs.
Methods for Calculating PCB Trace Inductance
There are several methods available for calculating the inductance of a PCB trace. Each method has its own advantages and limitations, and the choice of method depends on the specific design requirements and the level of accuracy needed. Let’s explore some of the most common methods:
1. Microstrip Inductance Formula
The microstrip inductance formula is a widely used method for calculating the inductance of a PCB trace. It assumes that the trace is a microstrip, which means it is a conducting strip separated from a ground plane by a dielectric material. The formula takes into account the trace dimensions and the dielectric constant of the PCB material.
The microstrip inductance formula is given by:
L = 0.002 × l × [ln(2l / (w + t)) + 0.5 + 0.2235 × (w + t) / l] nH
Where:
– L is the inductance in nanohenries (nH)
– l is the trace length in centimeters (cm)
– w is the trace width in centimeters (cm)
– t is the trace thickness in centimeters (cm)
To use this formula effectively, follow these steps:
- Determine the dimensions of your PCB trace (length, width, and thickness) in centimeters.
- Plug the values into the microstrip inductance formula.
- Calculate the inductance in nanohenries (nH).
Here’s an example calculation:
Let’s say we have a PCB trace with the following dimensions:
– Trace length (l) = 5 cm
– Trace width (w) = 0.1 cm
– Trace thickness (t) = 0.0035 cm
Plugging these values into the microstrip inductance formula:
L = 0.002 × 5 × [ln(2 × 5 / (0.1 + 0.0035)) + 0.5 + 0.2235 × (0.1 + 0.0035) / 5] nH
L = 0.01 × [ln(10 / 0.1035) + 0.5 + 0.2235 × 0.1035 / 5] nH
L = 0.01 × [4.5719 + 0.5 + 0.0046] nH
L = 0.01 × 5.0765 nH
L = 0.0508 nH
So, the inductance of the given PCB trace is approximately 0.0508 nH.
The microstrip inductance formula provides a quick and straightforward way to estimate the inductance of a PCB trace. However, it assumes an ideal microstrip structure and does not account for factors such as trace bends, vias, or the proximity to other traces and components.
2. Grover’s Inductance Equations
Grover’s inductance equations, named after Frederick W. Grover, provide a more comprehensive approach to calculating PCB trace inductance. These equations consider various trace geometries and configurations, making them suitable for a wider range of PCB designs.
Grover’s equations cover several common trace configurations, including:
- Straight wire
- Rectangular loop
- Circular loop
- Spiral inductor
For each configuration, there is a specific equation that takes into account the trace dimensions and geometry. Let’s look at an example using the straight wire equation.
The straight wire inductance equation is given by:
L = 0.002 × l × [ln(2l / r) - 0.75] μH
Where:
– L is the inductance in microhenries (μH)
– l is the wire length in centimeters (cm)
– r is the wire radius in centimeters (cm)
To use this equation, follow these steps:
- Determine the length and radius of your PCB trace in centimeters.
- Plug the values into the straight wire inductance equation.
- Calculate the inductance in microhenries (μH).
Here’s an example calculation:
Let’s say we have a straight PCB trace with the following dimensions:
– Trace length (l) = 10 cm
– Trace width (w) = 0.2 cm (assuming a circular cross-section, the radius r = w / 2 = 0.1 cm)
Plugging these values into the straight wire inductance equation:
L = 0.002 × 10 × [ln(2 × 10 / 0.1) - 0.75] μH
L = 0.02 × [ln(200) - 0.75] μH
L = 0.02 × [5.2983 - 0.75] μH
L = 0.02 × 4.5483 μH
L = 0.0910 μH
So, the inductance of the given straight PCB trace is approximately 0.0910 μH.
Grover’s inductance equations provide more accurate results compared to the microstrip inductance formula, as they consider various trace geometries. However, they still rely on simplifying assumptions and may not account for all the complexities of real-world PCB designs.
3. Electromagnetic Simulation
For the most accurate calculation of PCB trace inductance, electromagnetic (EM) simulation is the preferred method. EM simulation tools, such as Ansys HFSS, CST Studio Suite, or Keysight ADS, use numerical techniques like the finite element method (FEM) or the method of moments (MoM) to solve Maxwell’s equations and accurately model the electromagnetic behavior of PCB traces.
EM simulation offers several advantages over analytical formulas:
- It can handle complex trace geometries, including bends, vias, and non-uniform Cross-Sections.
- It accurately models the effects of dielectric materials and substrate properties.
- It can account for the proximity effects of nearby traces and components.
- It provides visualization of the electromagnetic fields and current distributions.
To perform EM simulation for PCB trace inductance calculation, follow these general steps:
- Create a 3D model of your PCB, including the trace geometry, dielectric layers, and relevant components.
- Define the material properties, such as conductivity and dielectric constant, for each part of the model.
- Set up the simulation parameters, including the frequency range, boundary conditions, and port excitations.
- Run the simulation and wait for the solver to compute the electromagnetic fields and currents.
- Post-process the results to extract the inductance value and visualize the field distributions.
Here’s an example of how EM simulation can be used to calculate PCB trace inductance:
Let’s consider a simple PCB with a single microstrip trace. We’ll use Ansys HFSS for this example.
-
Create a 3D model of the PCB in HFSS, including the substrate, ground plane, and microstrip trace. Define the trace dimensions, such as length, width, and thickness.
-
Assign the appropriate material properties to the substrate (e.g., FR-4) and the conductor (e.g., copper).
-
Set up the simulation parameters:
- Frequency range: 1 GHz to 10 GHz
- Boundary conditions: Radiation boundary on the outer faces of the model
-
Port excitation: Lumped port at one end of the microstrip trace
-
Run the simulation and wait for HFSS to solve the electromagnetic problem.
-
Post-process the results:
- View the 3D electromagnetic field distributions to understand the behavior of the trace
- Extract the S-parameters (scattering parameters) from the simulation results
- Convert the S-parameters to Z-parameters (impedance parameters)
- Calculate the inductance from the imaginary part of the Z-parameter at the desired frequency
EM simulation provides the most accurate results for PCB trace inductance calculation, taking into account the complex geometry, material properties, and electromagnetic interactions. However, it requires specialized software tools and can be computationally intensive, especially for large and intricate PCB designs.
Practical Considerations and Design Guidelines
When designing PCBs and managing trace inductance, there are several practical considerations and guidelines to keep in mind. These tips will help you optimize your designs and minimize the impact of inductance on your electronic circuits.
1. Minimize Trace Length
One of the most effective ways to reduce PCB trace inductance is to minimize the trace length. Shorter traces have lower inductance, as the stored magnetic energy is proportional to the length of the conductor. When routing your PCB, aim to keep the traces as short as possible, especially for high-speed signals and power supply traces.
2. Use Wide Traces
Another way to reduce trace inductance is to use wider traces. Increasing the trace width decreases the inductance per unit length, as it allows for a larger cross-sectional area for current flow. However, keep in mind that wider traces also have higher capacitance, so there is a trade-off between inductance and capacitance. Find the right balance based on your specific design requirements.
3. Avoid Sharp Bends
Sharp bends in PCB traces can lead to localized increases in inductance. When current flows through a bend, it experiences a sudden change in direction, which can result in a concentration of magnetic fields and higher inductance. To minimize this effect, use smooth, gradual bends instead of sharp 90-degree turns. If sharp bends are unavoidable, consider using mitered corners to reduce the inductance.
4. Use Ground Planes
Incorporating ground planes in your PCB design can help reduce trace inductance. A ground plane is a large area of copper that serves as a low-impedance return path for currents. By providing a nearby ground reference, the ground plane reduces the loop area and, consequently, the inductance of the traces. Make sure to use a solid ground plane and keep it as close to the signal traces as possible.
5. Consider Differential Signaling
For high-speed digital signals, consider using differential signaling instead of single-ended signaling. Differential signaling uses two complementary signals that are 180 degrees out of phase. The magnetic fields generated by the two signals tend to cancel each other out, reducing the overall inductance and electromagnetic interference. Differential traces should be routed close together and have equal lengths to maintain signal integrity.
6. Use Multilayer PCBs
In complex designs with many traces and components, using Multilayer PCBs can help manage trace inductance. By distributing the traces across multiple layers and using power and ground planes, you can reduce the loop area and minimize the inductance. Multilayer PCBs also allow for better control over trace impedance and can help minimize crosstalk between signals.
7. Perform EM Simulation
As mentioned earlier, electromagnetic simulation is the most accurate method for calculating PCB trace inductance. Whenever possible, perform EM simulations to validate your designs and identify potential inductance issues. Simulation tools can help you optimize trace routing, adjust trace widths and spacing, and evaluate the impact of different PCB materials and stackups.
By following these practical considerations and design guidelines, you can effectively manage PCB trace inductance and ensure the optimal performance of your electronic circuits.
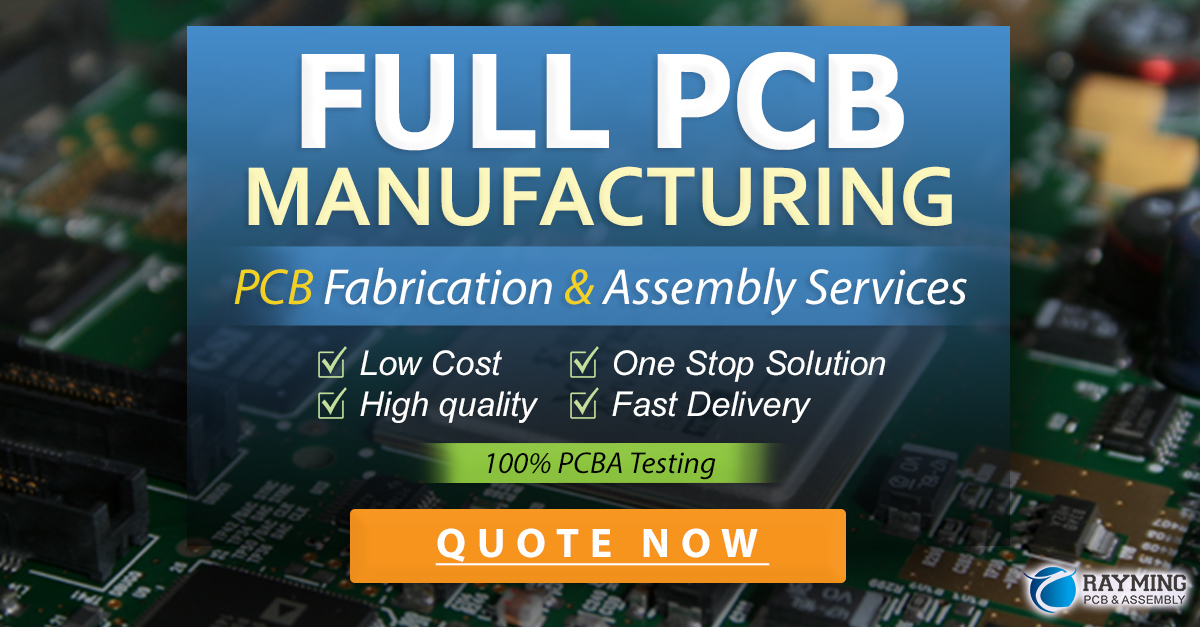
Frequently Asked Questions (FAQ)
- What is the difference between self-inductance and mutual inductance?
Self-inductance is the inductance of a single conductor, which represents the ability of the conductor to store energy in its own magnetic field when a current flows through it. Mutual inductance, on the other hand, is the inductance between two conductors, which represents the ability of one conductor to induce a voltage in another conductor due to the magnetic field generated by the current flowing in the first conductor.
- How does the dielectric constant of the PCB material affect trace inductance?
The dielectric constant of the PCB material influences the electromagnetic fields surrounding the traces. A higher dielectric constant results in a more concentrated electric field around the traces, which can lead to higher capacitance and lower characteristic impedance. However, the dielectric constant has a relatively minor effect on trace inductance compared to factors like trace geometry and ground plane proximity.
- Can I use online calculators or software tools to calculate PCB trace inductance?
Yes, there are various online calculators and software tools available that can help you calculate PCB trace inductance. These tools often implement analytical formulas like the microstrip inductance formula or Grover’s equations. Some popular options include the Saturn PCB Toolkit, PCB Toolkit, and EEWeb PCB Trace Inductance Calculator. However, keep in mind that these tools may have limitations and may not account for all the complexities of real-world PCB designs.
- What is the impact of PCB trace inductance on signal integrity?
PCB trace inductance can have a significant impact on signal integrity, especially in high-speed digital circuits. High inductance can lead to signal distortion, ringing, overshoot, and undershoot. These effects can cause false triggering, data errors, and timing issues, compromising the reliability and performance of the electronic system. Managing trace inductance is crucial for ensuring good signal integrity and maintaining the desired signal waveforms.
- How can I measure the inductance of a PCB trace experimentally?
To measure the inductance of a PCB trace experimentally, you can use an impedance analyzer or a network analyzer. These instruments can measure the S-parameters (scattering parameters) of the trace over a range of frequencies. From the S-parameters, you can extract the Z-parameters (impedance parameters) and calculate the inductance by looking at the imaginary part of the Z-parameter at the desired frequency. Alternatively, you can use a specialized inductance meter that directly measures the inductance of the trace using techniques like the four-point probe method.
Conclusion
Calculating the inductance of PCB traces is a critical aspect of PCB design, as it directly impacts the performance, signal integrity, and electromagnetic compatibility of electronic circuits. In this comprehensive guide, we explored the fundamentals of PCB inductance, discussed various methods for calculating trace inductance, and provided practical considerations and design guidelines.
We covered analytical methods like the microstrip inductance formula and Grover’s equations, which offer quick estimates of trace inductance based on trace geometry and dimensions. We also discussed the importance of electromagnetic simulation for accurate inductance calculation, taking into account the complex interactions between traces, dielectric materials, and nearby components.
To optimize your PCB designs and manage trace inductance effectively, remember to:
- Minimize trace lengths
- Use wide traces
- Avoid sharp bends
- Incorporate ground planes
- Consider differential signaling
- Utilize multilayer PCBs
- Perform EM simulations
By understanding and applying these concepts and techniques, you can design PCBs with well-controlled inductance, ensuring optimal performance, signal integrity, and electromagnetic compatibility.
As you embark on your PCB design journey, keep exploring and learning about the
Leave a Reply