What is PCB Trace Impedance and Why Does it Matter?
PCB trace impedance refers to the opposition that a printed circuit board trace presents to alternating current (AC). It is an important parameter to consider when designing high-speed digital circuits or sensitive analog circuits. Matching the impedance of PCB Traces to the source and load impedances is critical for several reasons:
- It minimizes signal reflections and distortions that can degrade signal integrity
- It reduces electromagnetic interference (EMI) and crosstalk between traces
- It ensures maximum power transfer from source to load
- It helps to control the characteristic impedance of transmission lines on the PCB
Therefore, accurately calculating and controlling the impedance of PCB traces is essential for optimizing circuit performance, reliability, and electromagnetic compatibility (EMC).
Factors That Affect PCB Trace Impedance
Several factors influence the impedance of a PCB trace:
- Trace width and thickness
- Dielectric constant and thickness of the PCB substrate material
- Height of the trace above the reference plane(s)
- Proximity to other traces and copper features
The characteristic impedance of a PCB trace is determined by its geometry and the properties of the surrounding dielectric material, as described by the following equation:
Z0 = (87 / √ϵr) × ln(5.98 × h / (0.8 × w + t))
Where:
– Z0 is the characteristic impedance in ohms (Ω)
– ϵr is the relative permittivity (dielectric constant) of the substrate material
– h is the height of the trace above the reference plane in mils (1 mil = 0.001 inch)
– w is the width of the trace in mils
– t is the thickness of the trace in mils
This equation assumes a microstrip trace geometry, where the signal trace is above a single reference plane, usually ground. For stripline traces embedded between two reference planes, the equation is slightly different.
Substrate Materials and Their Dielectric Constants
The dielectric constant (Dk) of the PCB substrate material significantly impacts the trace impedance. Some common PCB substrate materials and their typical dielectric constants are:
Material | Dielectric Constant (Dk) |
---|---|
FR-4 | 4.0 – 4.5 |
Rogers RO4003C | 3.38 ± 0.05 |
Rogers RO4350B | 3.48 ± 0.05 |
Isola IS410 | 3.97 ± 0.05 |
PTFE (Teflon) | 2.1 |
Polyimide | 3.4 |
Materials with lower dielectric constants, like PTFE, will result in higher trace impedances for a given geometry compared to materials with higher Dk values, such as FR-4.
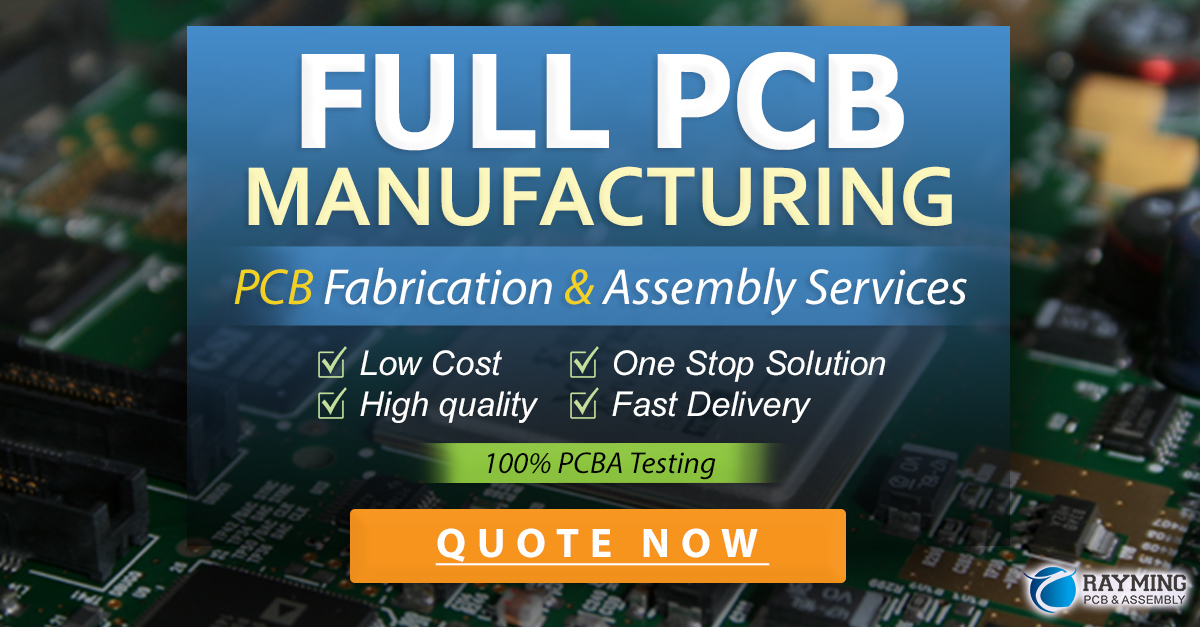
Calculating Microstrip Trace Impedance
To calculate the impedance of a microstrip trace, follow these steps:
-
Determine the desired characteristic impedance (Z0) based on your circuit requirements, typically 50Ω or 75Ω.
-
Choose a suitable PCB substrate material and note its dielectric constant (ϵr).
-
Decide on the thickness of the substrate (h) based on your PCB Stackup design.
-
Select a reasonable trace thickness (t) based on your PCB manufacturing capabilities and current carrying requirements, typically 1.4 mils (0.5 oz copper) or 2.8 mils (1 oz copper).
-
Calculate the required trace width (w) using the microstrip impedance equation or an online calculator. One such calculator is the Saturn PCB Design Toolkit.
For example, to achieve a 50Ω impedance on a 6-mil thick FR-4 substrate (ϵr = 4.4) with a 1.4-mil thick trace:
w = (5.98 × h / e^(Z0 × √ϵr / 87)) – (0.8 × t)
= (5.98 × 6 / e^(50 × √4.4 / 87)) – (0.8 × 1.4)
≈ 9.7 mils
Calculating Stripline Trace Impedance
Stripline traces are embedded between two reference planes, usually ground planes. The impedance equation for stripline traces is:
Z0 = (60 / √ϵr) × ln((1.9 × (2 × h + t)) / (0.8 × w + t))
Where the variables have the same meanings as in the microstrip equation, but h represents the height of the trace above the lower reference plane.
To calculate stripline trace impedance:
-
Follow steps 1-4 from the microstrip calculation process.
-
Determine the height (h) of the trace above the lower reference plane based on your PCB stackup.
-
Calculate the required trace width (w) using the stripline impedance equation or an online calculator.
For example, to achieve a 50Ω impedance on an 8-mil thick FR-4 substrate (ϵr = 4.4) with a 1.4-mil thick trace centered between two ground planes:
h = (8 – 1.4) / 2 = 3.3 mils
w = ((1.9 × (2 × h + t)) / e^(Z0 × √ϵr / 60)) – (0.8 × t)
= ((1.9 × (2 × 3.3 + 1.4)) / e^(50 × √4.4 / 60)) – (0.8 × 1.4)
≈ 5.4 mils
Impedance Control Considerations
To ensure that your PCB traces meet the target impedance, consider the following:
- Work closely with your PCB fabricator to understand their capabilities and tolerances for trace width, thickness, and dielectric thickness control.
- Specify controlled impedance requirements clearly in your PCB design files and fabrication drawings.
- Allow for additional spacing between impedance-controlled traces and other copper features to minimize impedance variations.
- Use PCB design tools with built-in Impedance Calculators and 2D or 3D field solvers for more accurate simulations.
- Perform impedance testing on fabricated PCBs to verify that traces meet the specified impedance targets.
Frequently Asked Questions (FAQ)
-
Q: What is the most common impedance for PCB traces in digital circuits?
A: The most common impedance for PCB traces in digital circuits is 50Ω, as it matches the typical output impedance of drivers and Input Impedance of receivers in many digital devices. -
Q: Can I use the same trace width for all impedance-controlled traces on my PCB?
A: Not necessarily. The required trace width to achieve a target impedance depends on the substrate thickness and dielectric constant, which may vary in different layers of your PCB stackup. Always calculate trace widths based on the specific layer and substrate properties. -
Q: How does trace roughness affect impedance?
A: Trace roughness can increase the effective dielectric constant and decrease the characteristic impedance of a trace. This effect becomes more pronounced at higher frequencies. To account for this, some PCB manufacturers may adjust the trace width slightly to compensate for the roughness effects. -
Q: What is the impact of Solder Mask on trace impedance?
A: Solder mask has a higher dielectric constant than air, so it can decrease the characteristic impedance of a trace when applied over it. The impact is generally small for thin solder mask layers but should be considered for very high-speed or high-precision designs. Some impedance calculators include an option to factor in solder mask effects. -
Q: How do I handle impedance matching for differential pairs?
A: Differential pairs require both odd-mode and even-mode impedance control. The odd-mode impedance is determined by the spacing between the traces, while the even-mode impedance depends on the trace width and distance to the reference plane(s). Special calculators and design rules are used to determine the optimal trace width and spacing for differential pairs to achieve the desired differential impedance, common-mode impedance, and coupling between the traces.
In summary, calculating and controlling PCB trace impedance is a critical aspect of high-speed digital and sensitive analog PCB design. By understanding the factors that affect trace impedance, using appropriate equations and calculators, and working closely with your PCB fabricator, you can ensure that your PCB traces meet the target impedance requirements for optimal signal integrity and EMC performance.
Leave a Reply