What is Flex PCB and Why is it Used?
Flexible printed circuit boards, also known as flex PCBs or flex circuits, are a type of printed circuit board that uses flexible materials as the base instead of the traditional rigid materials like FR4. Flex PCBs are made by laminating thin, flexible polymer films like polyimide with copper traces and other components. This allows the PCB to bend, fold, and twist without damaging the circuits.
The main advantages of using flex PCBs include:
-
Flexibility: Flex PCBs can be bent and folded to fit into tight spaces or conform to the shape of a device. This allows for more compact and space-efficient designs.
-
Durability: Despite being flexible, flex PCBs are highly durable and resistant to shocks, vibrations, and extreme temperatures. The materials used are also lightweight yet strong.
-
Reliability: The flexible nature of flex PCBs reduces the risk of connection failures from stresses like repeated flexing. High quality materials provide stable performance.
-
Design Freedom: Flex PCBs open up new possibilities for creative product designs that would be difficult or impossible with rigid boards. 3D configurations are possible.
-
Weight & Space Savings: Using a flex PCB can reduce the size and weight of a device by eliminating bulky wires and connectors between rigid PCBs.
Due to these benefits, flex PCBs have become essential in many industries and applications where traditional rigid PCBs fall short. The following sections will explore some of the top applications of flex PCB technology.
Consumer Electronics
Smartphones
One of the largest markets for flex PCBs is smartphones and mobile devices. As consumers demand thinner, lighter, and more feature-packed phones, manufacturers are turning to flex PCBs to meet these challenges.
In a modern smartphone, flex PCBs serve several purposes:
- Connecting the main logic board to other components like cameras, buttons, speakers, and I/O ports
- Routing signals around tightly packed batteries and electronics
- Enabling folding or slide-out screen designs
- Reducing overall thickness and weight compared to rigid PCB + wire setups
For example, the iPhone X used a large flex PCB to wrap around the dual battery cells and connect the motherboard on top to the Lightning port on bottom. Some models use flex as the main board itself.
Wearables
Wearable Technology like smartwatches, fitness trackers, AR/VR headsets and smart clothing rely heavily on flex PCBs to function. The small sizes and curved surfaces of these devices necessitates the use of flexible circuits.
In a typical smartwatch, a flex PCB will snake through the narrow cavity between the display and back cover, connecting multiple rigid PCBs holding the processor, sensors, battery and more. Pressure, moisture and shock resistance are key.
For smart clothing, flex PCBs can be woven directly into the fabric to connect sensors and electronics without impacting comfort and mobility. Flex allows designs to stretch and conform to the body.
Laptops
Although laptops use mostly rigid PCBs for the main boards, flex PCBs still play an important role. They are commonly used for:
- Connecting the main board to the display (eDP cable)
- Touchpad interfaces
- Keyboard membranes and backlighting
- Routing signals to speakers, camera, lid switches, etc.
- Enabling 2-in-1 hinge designs that fold 360°
As laptops continue slimming down and adding features, the applications for flex will likely expand. Reliability is paramount as these cables must withstand repeated opening and closing.
Automotive Electronics
Infotainment & Dashboards
Modern vehicle cockpits are increasingly packed with electronic displays, controls and interfaces surrounding the driver. Flex PCBs are essential for connecting everything behind the scenes.
Infotainment systems use flex to link the central display to various boards handling functions like audio, navigation, climate and vehicle data. Flex allows the large screen to be mounted flush while boards are hidden elsewhere.
Digital instrument clusters also use flex PCBs to create curved and reconfigurable displays that blend with the dashboard design. Replacing physical gauges with flex-mounted LCDs saves weight.
ADAS Sensors
Advanced Driver Assistance Systems (ADAS) like collision warning, lane keeping and auto-parking rely on numerous sensors mounted around the vehicle periphery. Flex PCBs provide both the mounting surfaces and interconnects for these compact radar, camera and ultrasonic units.
Compared to Wire Harnesses, flex PCBs can simplify installation, reduce weight, and improve reliability in the harsh operating conditions. As sensor counts increase, flex will help manage the wiring complexity.
EV Battery Packs
Electric vehicles require sophisticated battery management systems (BMS) to monitor and control the large array of individual cells. Flex PCBs are used to connect the BMS boards to each cell for sensing voltage and temperature.
The long, thin aspect ratio of flex is perfect for snaking between tightly packed cells without wasting space. They can also flex to handle thermal expansion and road vibration. Specialized materials provide heat and moisture resistance.
As EVs proliferate, the demand for battery flex PCBs will rise. The push for higher density and longer range will require even more advanced flex designs.
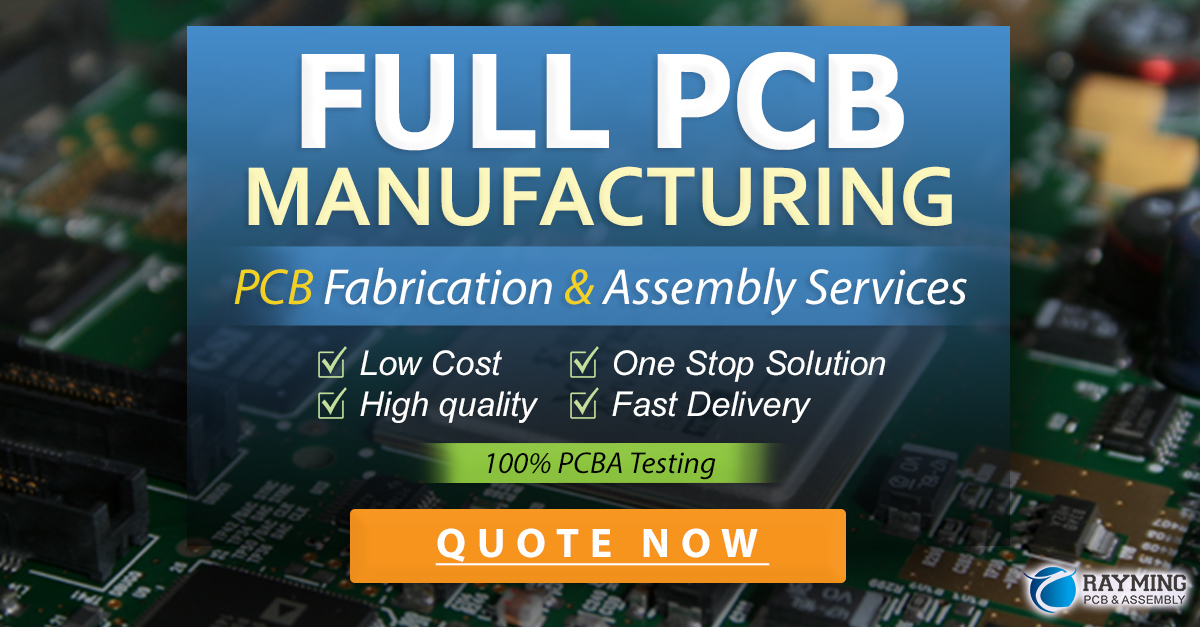
Medical Devices
Diagnostic Equipment
Many medical imaging and diagnostic devices utilize flex PCBs for their compact and dense electronics. Some examples include:
-
Ultrasound probes: Flex PCBs connect the transducer array head to the main beamforming electronics, allowing for small, ergonomic designs. High frequency performance is critical.
-
Endoscopes: Miniature cameras and sensors mounted on flex PCBs enable minimally invasive imaging inside the body. Extreme flexibility and durability are required.
-
Wearable monitors: Flex allows medical wearables like ECG, EEG and blood pressure sensors to conform to the patient’s body for comfort and reliable readings over extended periods.
The biocompatibility, chemical resistance and sterilizable nature of flex PCB materials are key advantages in medical settings. Regulations often require using specialized grades.
Implantables
One of the most demanding applications for flex PCBs is in implantable medical devices like pacemakers, neurostimulators and drug delivery systems. The flex circuit must survive for years inside the harsh environment of the human body.
Implantable flex PCBs are used for:
- Connecting multiple rigid PCBs in a 3D configuration to fit the compact titanium enclosure
- Providing a flexible interface to leads that connect to heart, brain or other organs
- Enabling folding designs that expand once implanted
- Supporting biocompatible sensors in contact with tissue or fluids
These flex designs push the limits of materials, reliability and assembly processes. Specialized polyimide films, soldermasks, adhesives and components are required. There is no room for failure.
As implantable technology advances, flex PCBs will be instrumental in meeting the shrinking size and increasing complexity. Applications like neural interfaces and bioresorbable scaffolds are on the horizon.
Industrial & Aerospace
Sensors & Controls
Flex PCBs are a common choice for industrial sensor assemblies due to their durability and resistance to harsh conditions. They can operate in extreme temperatures, high pressure, and corrosive environments that would damage rigid PCBs.
Some applications include:
-
Process control equipment: Flex-based sensors for monitoring fluid flow, gas concentration, vibration, and more. Thin profiles allow embedding in pipes and machinery.
-
Automotive sensors: Flex PCBs are used in engine control units, tire pressure monitors, oil quality sensors, and other under-hood electronics exposed to heat and chemicals.
-
Aerospace instruments: Avionics and satellites use flex PCBs for weight savings and ability to fit in tight, irregular cavities. High altitude/vacuum performance is essential.
The combination of flex circuits and rigid PCBs (rigid-flex) is often used to create compact 3D sensor assemblies. Rigid boards provide mechanical mounting points while flex does interconnect.
Robotics
Robotics applications are increasingly using flex PCBs to simplify wiring and improve reliability. Some uses include:
-
Robot arms: Flex can be used to route power and signals through the joints and links of a robot arm, eliminating moving cables that can fatigue and tangle. This improves precision and uptime.
-
Grippers: Sensors and actuators for robotic grippers can be mounted on flex PCBs that conform to fingertip contours. This saves space and enables direct surface mounting.
-
Humanoid bots: Flex allows replicating the muscle-like connections and motions in advanced humanoid designs. It can span gaps and accommodate unorthodox geometry.
The light weight, thin profile and dynamic flexibility of flex are all assets in robotic systems. As designs become more lifelike and dexterous, flex PCBs will be key.
Frequently Asked Questions
Q: How long do flex PCBs last compared to rigid?
A: Flex PCBs are actually more durable than rigid PCBs in many cases. While rigid boards are prone to cracking from shock and vibration, flex PCBs can dissipate those forces through bending. The polyimide materials in flex are also highly resistant to heat, cold, moisture and chemicals. With proper design, a flex PCB can easily last 10+ years, even with repeated flexing.
Q: Are flex PCBs more expensive?
A: In general, flex PCBs do cost more than equivalent rigid PCBs on a per-unit basis. The materials, processes and precision required are higher. However, a well-designed flex solution can still be cost effective when considering the total system cost. Flex often enables size, weight and component reductions that offset the premium. The improved reliability also lowers lifetime costs. It depends on the application.
Q: Can you solder components to flex PCBs?
A: Yes, flex PCBs can be assembled with most of the same soldering processes as rigid boards, including reflow, wave and hand soldering. The key is properly supporting the flex circuit to prevent damage from handling and heat. Backing layers, frames and specialized pallets are used. Some components may require additional strain relief like underfill or staking. Following supplier guidelines and industry standards is crucial for success.
Q: How do you connect a flex PCB to a rigid PCB?
A: The three most common methods are:
-
Connectors: The flex PCB has a contact finger pattern that mates with a ZIF or LIF style connector on the rigid board. This allows easy insertion/removal.
-
Direct Soldering: The flex is typically designed with a “rigid” section that can be directly soldered to pads on the rigid PCB. Stiffeners are used to support the joint.
-
Rigid-Flex: A Rigid-Flex Design has rigid PCB sections built into the same assembly as the flex. The rigid areas can be SMT assembled and then directly connected.
The best method depends on the specific design constraints and connection requirements.
Q: What industries use flex PCBs the most?
A: Currently, the top industries by flex PCB Market share are:
- Consumer electronics, particularly smartphones, wearables and laptops
- Automotive, for infotainment, sensors and battery management
- Medical, in both diagnostic equipment and implantable devices
- Aerospace/Defense, for avionics and Military Electronics
- Industrial equipment, for sensors, controls and robotics
However, flex PCBs are being designed into an ever expanding range of products. If a device needs dense packaging, flexible connectivity or durability, flex PCBs are likely part of the solution. The materials and processes continue to evolve to meet new challenges.
Leave a Reply