Understanding High-Speed Signals
What are High-Speed Signals?
High-speed signals are electrical signals that have a high frequency and fast rise and fall times. These signals are typically used in applications that require fast data transmission, such as high-speed digital interfaces, high-bandwidth analog circuits, and high-frequency RF (Radio Frequency) systems. The characteristics of high-speed signals make them more susceptible to various issues, such as signal integrity problems, electromagnetic interference (EMI), and power integrity concerns.
Challenges in High-Speed PCB Design
Designing high-speed PCBs presents several challenges that must be addressed to ensure the proper functioning of the circuit. Some of the key challenges include:
-
Signal Integrity: High-speed signals are prone to distortion, reflection, and crosstalk, which can degrade the quality of the signal and lead to data errors.
-
Electromagnetic Compatibility (EMC): High-speed circuits can generate significant amounts of EMI, which can interfere with other electronic devices and cause compliance issues with regulatory standards.
-
Power Integrity: High-speed circuits often have demanding power requirements, and maintaining a clean and stable power supply is crucial for proper operation.
-
Thermal Management: High-speed circuits can generate substantial amounts of heat, which must be effectively dissipated to prevent performance degradation and reliability issues.
Signal Integrity in High-Speed PCB Design
What is Signal Integrity?
Signal integrity refers to the ability of a signal to maintain its original characteristics as it propagates through a PCB. In high-speed PCB design, signal integrity is a critical concern because high-frequency signals are more susceptible to distortion, reflection, and crosstalk. These issues can lead to data errors, reduced performance, and even complete system failure.
Techniques for Improving Signal Integrity
To ensure good signal integrity in high-speed PCB design, several techniques can be employed:
-
Controlled Impedance: Designing traces with controlled impedance helps to minimize reflections and ensure proper signal termination.
-
Differential Signaling: Using differential pairs for high-speed signals helps to reduce EMI and improve noise immunity.
-
Trace Routing: Careful trace routing, including the use of smooth curves, avoidance of sharp bends, and proper spacing between traces, can minimize crosstalk and signal distortion.
-
Termination: Proper termination techniques, such as series termination and parallel termination, help to minimize reflections and ensure clean signal transitions.
Example: Controlled Impedance
Controlled impedance is a crucial aspect of high-speed PCB design. To achieve controlled impedance, the dimensions of the PCB traces must be carefully calculated based on the desired characteristic impedance and the properties of the PCB materials. The table below shows an example of the required trace width and spacing for a 50Ω controlled impedance microstrip trace on a typical FR-4 PCB:
PCB Material | Dielectric Constant (εr) | Trace Width (mm) | Trace Thickness (mm) | Substrate Thickness (mm) |
---|---|---|---|---|
FR-4 | 4.3 | 0.38 | 0.035 | 0.2 |
By adhering to these dimensions, the PCB designer can ensure that the traces have the desired characteristic impedance, which helps to maintain signal integrity and minimize reflections.
Electromagnetic Compatibility (EMC) in High-Speed PCB Design
What is EMC?
Electromagnetic compatibility (EMC) refers to the ability of an electronic device to operate properly in its electromagnetic environment without causing or being susceptible to electromagnetic interference (EMI). In high-speed PCB design, EMC is a critical consideration because high-frequency signals can generate significant amounts of EMI, which can interfere with other electronic devices and cause compliance issues with regulatory standards.
Techniques for Improving EMC
To ensure good EMC in high-speed PCB design, several techniques can be employed:
-
Grounding and Shielding: Proper grounding and shielding techniques, such as the use of ground planes, shielded enclosures, and gaskets, can help to reduce EMI and improve EMC.
-
Decoupling and Filtering: Decoupling capacitors and filtering components can help to suppress high-frequency noise and prevent EMI from propagating through the power supply and signal lines.
-
Trace Routing: Careful trace routing, including the use of differential pairs, balanced transmission lines, and proper spacing between traces, can help to minimize EMI and improve EMC.
-
Component Placement: Strategic component placement, such as keeping high-speed components away from the edges of the PCB and separating analog and digital circuits, can help to reduce EMI and improve EMC.
Example: Decoupling Capacitors
Decoupling capacitors are essential components in high-speed PCB design for maintaining power integrity and reducing EMI. The table below shows an example of the recommended decoupling capacitor values and placement for a typical high-speed digital circuit:
Capacitor Value | Placement |
---|---|
100 nF | Close to each power pin of high-speed ICs |
1 µF | Distributed throughout the PCB, near power supplies |
10 µF | Near the main power entry point of the PCB |
By using a combination of decoupling capacitors with different values and placing them strategically throughout the PCB, designers can effectively suppress high-frequency noise and maintain power integrity, which helps to improve EMC and overall system performance.
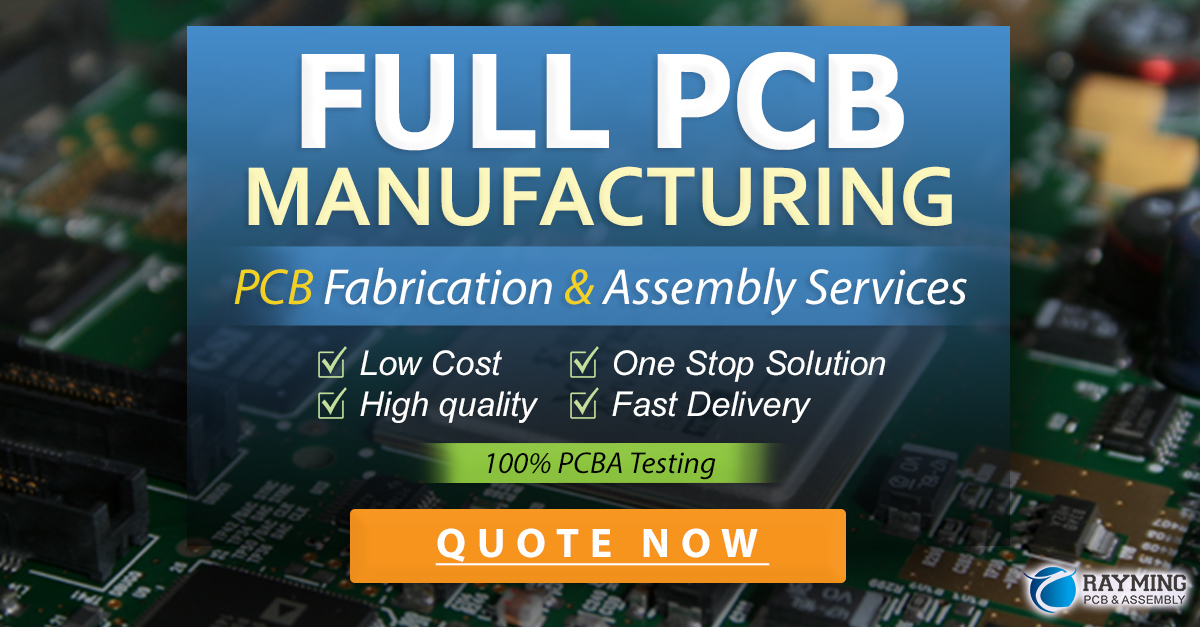
Power Integrity in High-Speed PCB Design
What is Power Integrity?
Power integrity refers to the ability of a PCB to provide a clean, stable, and adequate power supply to all the components on the board. In high-speed PCB design, power integrity is a critical concern because high-speed circuits often have demanding power requirements, and any fluctuations or noise in the power supply can lead to signal integrity issues, reduced performance, and even complete system failure.
Techniques for Improving Power Integrity
To ensure good power integrity in high-speed PCB design, several techniques can be employed:
-
Power Plane Partitioning: Dividing the power plane into separate regions for different power supplies and high-speed components can help to isolate noise and prevent interference between different parts of the circuit.
-
Decoupling and Bypassing: Using decoupling capacitors and bypass capacitors can help to suppress high-frequency noise and maintain a stable power supply for high-speed components.
-
Voltage Regulation: Using Voltage Regulators and power management ICs can help to provide a clean and stable power supply, even in the presence of fluctuations in the input voltage or load current.
-
Power Plane Stitching: Using vias to stitch together the power planes on different layers of the PCB can help to reduce impedance and improve current flow, which can help to maintain power integrity.
Example: Power Plane Partitioning
Power plane partitioning is a technique used to isolate different power supplies and high-speed components on a PCB to prevent noise and interference. The table below shows an example of how a power plane can be partitioned for a typical high-speed digital circuit:
Power Plane Region | Voltage | Components |
---|---|---|
Digital Core | 1.2 V | High-speed digital ICs, such as FPGAs and CPUs |
Digital I/O | 3.3 V | Digital I/O buffers and interface components |
Analog | 5 V | Analog components, such as ADCs and DACs |
By partitioning the power plane into separate regions for each power supply and group of components, designers can effectively isolate noise and prevent interference between different parts of the circuit, which helps to maintain power integrity and improve overall system performance.
Thermal Management in High-Speed PCB Design
Why is Thermal Management Important?
Thermal management is a critical aspect of high-speed PCB design because high-speed circuits can generate substantial amounts of heat, which can lead to performance degradation, reliability issues, and even complete system failure. As components become more compact and power-dense, the challenge of effectively dissipating heat becomes increasingly important.
Techniques for Improving Thermal Management
To ensure effective thermal management in high-speed PCB design, several techniques can be employed:
-
Component Placement: Strategic component placement, such as keeping high-power components away from heat-sensitive components and providing adequate spacing for airflow, can help to improve heat dissipation and prevent thermal issues.
-
Thermal Vias: Using thermal vias to conduct heat from high-power components to the PCB’s ground plane or dedicated thermal layers can help to improve heat dissipation and reduce component temperatures.
-
Heatsinks and Cooling Solutions: Using heatsinks, fans, and other cooling solutions can help to dissipate heat more effectively and maintain acceptable component temperatures.
-
Thermal Simulation: Conducting thermal simulations during the design phase can help to identify potential thermal issues and optimize the PCB Layout for improved heat dissipation.
Example: Thermal Vias
Thermal vias are a common technique used to improve heat dissipation in high-speed PCB design. The table below shows an example of the recommended thermal via specifications for a typical high-power component:
Parameter | Value |
---|---|
Via Diameter | 0.3 mm |
Via Plating | 1 oz. Cu |
Via Pitch | 1.2 mm |
Number of Vias | 16 |
By placing an array of thermal vias beneath a high-power component, designers can effectively conduct heat away from the component and into the PCB’s ground plane or dedicated thermal layers, which helps to improve heat dissipation and maintain acceptable component temperatures.
Best Practices for High-Speed PCB Design
To ensure successful high-speed PCB design, it is essential to follow best practices and guidelines that address the various challenges and considerations involved. Some of the key best practices include:
-
System-Level Design: Conducting a thorough system-level analysis and simulation to identify potential issues and optimize the overall design for high-speed performance.
-
Component Selection: Choosing components that are well-suited for high-speed applications, such as low-jitter oscillators, high-bandwidth op-amps, and high-speed digital ICs.
-
PCB Stack-Up Design: Designing a PCB stack-up that provides adequate power and ground planes, minimizes crosstalk and EMI, and supports controlled impedance traces.
-
Trace Routing and Placement: Following best practices for trace routing and placement, such as using smooth curves, avoiding sharp bends, and providing adequate spacing between traces to minimize crosstalk and signal distortion.
-
Simulation and Verification: Conducting comprehensive simulations and verification tests to ensure that the high-speed PCB design meets all performance, signal integrity, and EMC requirements.
Conclusion
High-speed PCB design is a complex and challenging field that requires a deep understanding of signal integrity, electromagnetic compatibility, power integrity, and thermal management. By following best practices and employing advanced techniques, such as controlled impedance, differential signaling, decoupling and filtering, and thermal management, designers can create high-performance PCBs that meet the demanding requirements of modern electronic systems. As technology continues to advance, the importance of high-speed PCB design will only continue to grow, making it an essential skill for electronics engineers and PCB designers alike.
Frequently Asked Questions (FAQ)
1. What is the difference between a high-speed PCB and a standard PCB?
A high-speed PCB is specifically designed to handle high-frequency signals and fast data transmission rates, while a standard PCB is designed for lower-frequency applications. High-speed PCBs require special considerations for signal integrity, EMC, power integrity, and thermal management, which are not as critical in standard PCB design.
2. What are the most common signal integrity issues in high-speed PCB design?
The most common signal integrity issues in high-speed PCB design include signal distortion, reflection, crosstalk, and jitter. These issues can be caused by factors such as improper trace routing, inadequate termination, and poor power integrity, and can lead to data errors, reduced performance, and even complete system failure.
3. How can I reduce EMI in my high-speed PCB design?
To reduce EMI in high-speed PCB design, you can employ techniques such as proper grounding and shielding, decoupling and filtering, careful trace routing, and strategic component placement. Using differential signaling, balanced transmission lines, and shielded enclosures can also help to minimize EMI and improve EMC.
4. What is the importance of power integrity in high-speed PCB design?
Power integrity is critical in high-speed PCB design because high-speed circuits often have demanding power requirements, and any fluctuations or noise in the power supply can lead to signal integrity issues, reduced performance, and even complete system failure. Maintaining a clean, stable, and adequate power supply is essential for ensuring the proper operation of high-speed components.
5. How can I ensure effective thermal management in my high-speed PCB design?
To ensure effective thermal management in high-speed PCB design, you can employ techniques such as strategic component placement, the use of thermal vias, heatsinks, and cooling solutions, and conducting thermal simulations during the design phase. By optimizing the PCB layout for heat dissipation and using appropriate cooling solutions, you can maintain acceptable component temperatures and prevent thermal issues that can degrade performance and reliability.
Leave a Reply