Solder Mask vs Paste: Understanding the Key Differences
When it comes to printed circuit board (PCB) manufacturing, two important materials often come into play: solder mask and solder paste. While they may sound similar, they serve distinct purposes and have unique characteristics. In this article, we will delve into the differences between solder mask and solder paste, exploring their roles in the PCB Assembly process and how they contribute to the overall functionality and reliability of electronic devices.
What is Solder Mask?
Solder mask, also known as solder resist or solder stop, is a thin layer of polymer material applied to the surface of a PCB. Its primary purpose is to protect the copper traces and pads from oxidation, corrosion, and accidental short-circuiting during the soldering process. Solder mask also provides insulation between the conductive parts of the PCB, preventing unwanted electrical connections.
Characteristics of Solder Mask
- Typically green in color, but can also be found in other colors such as red, blue, black, or white
- Applied as a liquid or dry film and then cured using UV light or heat
- Covers the entire PCB surface, except for the areas where components will be soldered (pads and vias)
- Helps to improve the PCB’s appearance and readability by providing a contrasting background for silkscreen markings
What is Solder Paste?
Solder paste is a material used in the surface mount technology (SMT) assembly process to attach electronic components to the PCB. It is a homogeneous mixture of tiny solder particles suspended in a flux medium. The solder particles are typically made of a tin-lead alloy or lead-free alternatives like tin-silver-copper (SAC).
Characteristics of Solder Paste
- Gray, paste-like consistency
- Applied to the PCB pads using a stencil or syringe
- Contains flux to clean and protect the metal surfaces during soldering
- Melts when exposed to heat, forming a strong electrical and mechanical bond between the component leads and PCB pads
The Role of Solder Mask in PCB Manufacturing
Solder mask plays a crucial role in the PCB manufacturing process, offering several benefits that contribute to the overall quality and reliability of the final product.
Protection Against Short Circuits
One of the primary functions of solder mask is to prevent short circuits between adjacent copper traces or pads. By covering the PCB surface, leaving only the necessary areas exposed for soldering, solder mask minimizes the risk of accidental bridging or short-circuiting during the assembly process.
Insulation and Resistance
Solder mask acts as an insulating layer, providing electrical resistance between the conductive parts of the PCB. This insulation helps to maintain the integrity of the electrical signals and prevents leakage currents that could lead to performance issues or device failure.
Improved Durability
The solder mask layer protects the copper traces and pads from oxidation, corrosion, and physical damage. By shielding these critical components from the environment, solder mask enhances the durability and longevity of the PCB, ensuring reliable operation over an extended period.
Enhanced Aesthetics and Readability
Solder mask not only serves functional purposes but also contributes to the visual appeal of the PCB. The contrasting background provided by the solder mask makes it easier to read silkscreen markings, such as component designators and polarity indicators. This improved readability aids in the assembly process and facilitates troubleshooting and repairs.
The Role of Solder Paste in PCB Assembly
Solder paste is an essential material in the SMT Assembly process, enabling the secure attachment of surface mount components to the PCB.
Forming Electrical and Mechanical Connections
The primary purpose of solder paste is to create a strong electrical and mechanical bond between the component leads and the PCB pads. When exposed to heat during the reflow soldering process, the solder particles in the paste melt and form a reliable connection, ensuring proper functionality of the assembLED PCB.
Flux Activity
The flux medium in solder paste serves several important functions:
– Cleaning: Flux removes oxides and contaminants from the metal surfaces, promoting better wetting and bonding of the solder.
– Protection: Flux shields the metal surfaces from oxidation during the soldering process, ensuring a high-quality solder joint.
– Heat transfer: Flux helps to distribute heat evenly across the solder joint, facilitating the formation of a strong and reliable connection.
Stencil Printing
Solder paste is typically applied to the PCB pads using a stencil printing process. A stainless steel stencil with apertures corresponding to the PCB pad layout is placed over the board, and solder paste is deposited onto the stencil. A squeegee blade is then used to spread the paste across the stencil, forcing it through the apertures and onto the pads. This process ensures precise and consistent solder paste deposition, which is critical for achieving high-quality solder joints.
Reflow Soldering
After the solder paste is applied and the components are placed on the PCB, the assembly undergoes a reflow soldering process. The PCB is exposed to a controlled temperature profile in a reflow oven, which causes the solder particles in the paste to melt and form a strong bond between the component leads and PCB pads. The flux in the solder paste helps to clean and protect the metal surfaces during this process, ensuring optimal solder joint formation.
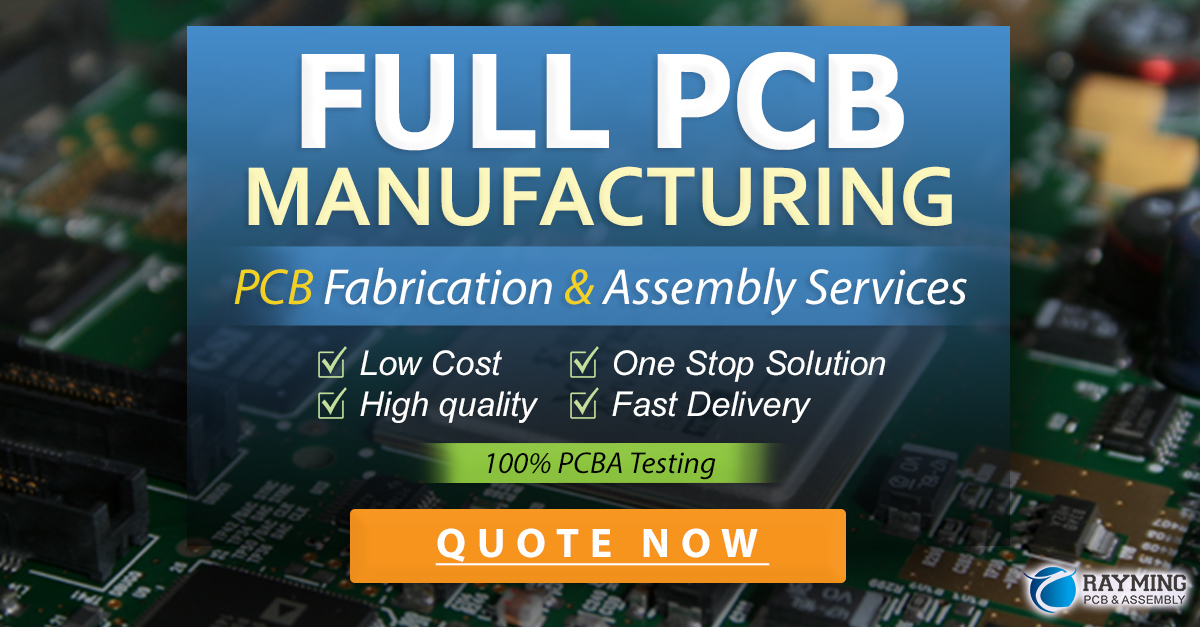
Comparing Solder Mask and Solder Paste
While solder mask and solder paste serve different purposes in the PCB manufacturing and assembly processes, they share some common goals in ensuring the quality, reliability, and functionality of the final product.
Feature | Solder Mask | Solder Paste |
---|---|---|
Purpose | Protects PCB surface, prevents short circuits | Forms electrical and mechanical connections |
Application | Covers entire PCB, except pads and vias | Applied to PCB pads using stencil or syringe |
Material | Polymer (liquid or dry film) | Solder particles suspended in flux medium |
Appearance | Typically green, other colors available | Gray, paste-like consistency |
Process | Applied and cured during PCB manufacturing | Used during SMT assembly, melts during reflow soldering |
Both solder mask and solder paste contribute to the production of high-quality PCBs by:
– Protecting the PCB and its components from damage
– Ensuring proper electrical insulation and connectivity
– Enhancing the reliability and longevity of the assembled device
However, they are used at different stages of the PCB manufacturing and assembly process and serve distinct purposes in achieving these goals.
Frequently Asked Questions (FAQ)
1. Can solder mask be applied after soldering?
No, solder mask is applied during the PCB manufacturing process, before any components are soldered to the board. Once the components are soldered, it is not possible to apply solder mask without damaging the components or the solder joints.
2. Is solder paste necessary for through-hole components?
Solder paste is primarily used for surface mount components in the SMT assembly process. Through-hole components are typically hand-soldered or wave-soldered using a solder wire or molten solder bath, respectively. However, in some cases, solder paste can be used for through-hole components in a process called pin-in-paste (PIP) soldering.
3. What happens if solder paste is not applied correctly?
If solder paste is not applied correctly, it can lead to various assembly issues, such as:
– Insufficient Solder volume, resulting in weak or open connections
– Excessive solder volume, causing bridging or short circuits
– Misaligned components due to uneven solder paste deposition
– Poor solder joint formation, affecting the reliability and functionality of the assembled PCB
4. Can solder mask color affect the PCB’s performance?
The color of the solder mask does not directly impact the PCB’s electrical performance. However, some Solder Mask Colors may have different thermal absorption properties, which could affect the PCB’s heat dissipation characteristics. In general, the choice of solder mask color is more often based on aesthetic preferences or design requirements, such as improving contrast for better readability of silkscreen markings.
5. How does the choice of solder paste alloy affect the soldering process?
The choice of solder paste alloy can impact various aspects of the soldering process, including:
– Melting temperature: Different alloys have different melting points, which affect the reflow temperature profile and the thermal stress on components.
– Wetting and spreading characteristics: Some alloys may have better wetting and spreading properties, resulting in more reliable solder joints.
– Mechanical strength: The composition of the alloy can influence the mechanical strength of the solder joint, affecting the overall reliability of the assembled PCB.
– Environmental considerations: Lead-free alloys, such as SAC, are becoming increasingly popular due to environmental regulations and health concerns associated with lead-based solders.
Conclusion
Solder mask and solder paste are two essential materials in the world of PCB manufacturing and assembly. While they may seem similar at first glance, they serve distinct purposes and are used at different stages of the production process.
Solder mask is a protective layer applied to the PCB surface during manufacturing, providing insulation, preventing short circuits, and enhancing the durability and appearance of the board. On the other hand, solder paste is a material used during the SMT assembly process to form electrical and mechanical connections between surface mount components and the PCB pads.
Understanding the differences between solder mask and solder paste, as well as their respective roles in the PCB production process, is crucial for designers, manufacturers, and assembly professionals. By selecting the appropriate materials and processes, they can ensure the production of high-quality, reliable, and functionally sound PCBs that meet the ever-growing demands of modern electronic devices.
Leave a Reply