What is a PCB Trace?
A printed circuit board (PCB) trace is a thin strip of copper or other conductive material that forms the interconnections between components on a PCB. Traces carry electrical signals and power between the various components soldered to the PCB. They are essentially the “wires” of the circuit board.
PCB traces are etched from copper sheets laminated onto a non-conductive substrate. The substrate is typically made of FR4, a glass-reinforced epoxy laminate. During PCB fabrication, unwanted copper is chemically removed to leave behind only the desired trace pattern connecting the components.
Key Characteristics of PCB Traces
Several important parameters define the properties and performance of PCB traces:
Trace Width
Trace width refers to the physical width of a PCB trace. It is a critical parameter that impacts:
- Current carrying capacity
- Resistance
- Impedance
- Electromagnetic interference (EMI)
Wider traces can safely carry more current, have lower resistance and inductance, but take up more space. Narrower traces allow for denser routing but have lower current limits.
Typical trace widths range from 3-10 mils (0.075-0.254 mm) for signal traces up to 100-500 mils (2.5-12.7 mm) for high-current power traces. The exact width is calculated based on the required current, allowable temperature rise, copper thickness, and acceptable voltage drop.
Trace Thickness
Trace thickness, also known as copper weight or copper thickness, is the thickness of the copper layer that makes up the traces. It is typically specified in ounces per square foot (oz/ft²). Common standard thicknesses are:
- 0.5 oz/ft² (17.5 μm)
- 1 oz/ft² (35 μm)
- 2 oz/ft² (70 μm)
Thicker copper allows higher current carrying capacity and lower resistance but is more expensive. It is commonly used for power traces or high-current applications.
Trace Spacing
Trace spacing is the distance between adjacent traces. It determines the PCB’s voltage breakdown resistance and impacts crosstalk.
Minimum trace spacing depends on the PCB’s expected operating voltage. For typical low-voltage circuits, trace spacings range from 3-10 mils (0.075-0.254 mm). Higher voltages require proportionally larger spacings to prevent arcing.
Closely spaced traces are more susceptible to electromagnetic coupling and crosstalk. Sensitive signals like high-speed digital lines, clocks, and analog signals benefit from wider spacings to adjacent traces.
Trace Geometry
Trace geometry refers to the routing shape and angles of the traces. Ideally, traces should be kept as short and direct as possible. Avoid unnecessarily long or meandering routes to minimize resistance and inductance.
Sharp 90° corners in traces can cause acid traps during PCB Etching, leading to over-etching and thinning of the traces. Therefore, it’s best to use rounded corners and angles called mitered bends. A 45° routing angle is a good compromise between sharp 90° and fully curved 180° bends.
Designing PCB Traces
Proper PCB trace design is crucial for ensuring signal integrity, power integrity, and electromagnetic compatibility (EMC) of the circuit. Here are some key considerations and best practices:
Impedance Control
Impedance is the AC resistance of a trace that takes into account its inductance and capacitance. It is an important parameter for high-speed signals like digital buses, RF lines, and high-speed interfaces.
To maintain signal integrity, the trace impedance must match the impedance of the source and load. This is called impedance matching. Mismatched impedances cause signal reflections, leading to ringing, overshoot, and signal distortion.
Common controlled impedances used are:
Impedance | Application |
---|---|
50 Ω | RF, coaxial lines, USB |
75 Ω | Video, Ethernet |
90 Ω | SCSI |
100 Ω | Differential pairs, Ethernet |
120 Ω | Differential pairs |
To achieve the target impedance, the trace width, thickness, spacing to ground planes, and dielectric properties of the PCB substrate must be carefully designed. PCB design tools have built-in calculators to assist with controlled impedance trace design.
Length Matching
For digital signals that operate in parallel, like data and address buses, the trace lengths must be closely matched. Length mismatch between traces causes signals to arrive at different times, leading to timing errors and reduced noise margin.
Typical length matching requirements are:
Signal Speed | Length Matching Tolerance |
---|---|
< 50 MHz | 500 mil (12.7 mm) |
50 – 100 MHz | 100 mil (2.5 mm) |
100 – 250 MHz | 20 mil (0.5 mm) |
> 250 MHz | 5 mil (0.127 mm) |
To match trace lengths, serpentine routing or trombone structures can be used to add length to shorter traces. Alternatively, the shorter traces can be routed in a zig-zag or sawtooth pattern.
Differential Pairs
Differential signaling uses two traces routed in parallel to carry a signal. The two traces are driven with equal and opposite signals. Differential pairs offer good noise immunity and low EMI as the fields from the two traces cancel each other.
Common differential pair traces are:
- USB
- Ethernet
- PCIe
- HDMI
- LVDS
For differential traces, it is crucial to maintain uniform trace width and spacing along the entire length. This ensures equal impedance and velocity for the two traces. Ideally, the spacing between the positive and negative traces should be at least 3x the trace width for good field cancellation.
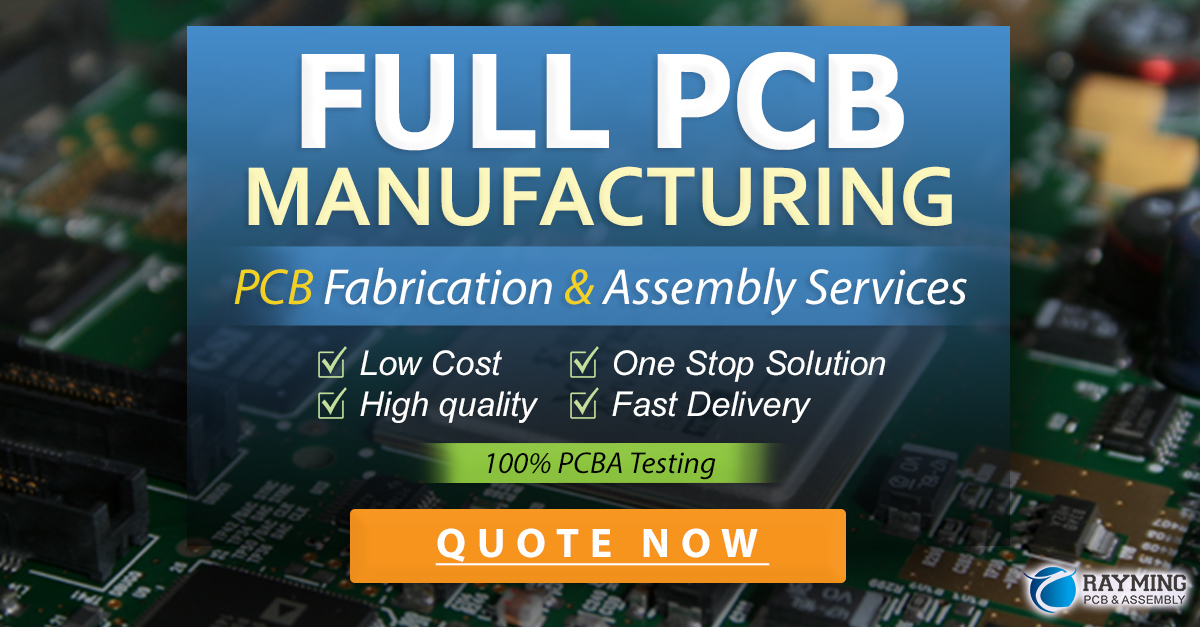
Routing PCB Traces
General Routing Guidelines
- Route traces on appropriate layers for their signal type – analog, digital, power
- Avoid crossing splits/cuts in ground and power planes
- Avoid routing traces under components or connectors
- Keep trace lengths as short as possible
- Use 45° corners instead of 90° bends
- Provide ground Return Paths adjacent to signal traces
- Avoid routing traces over non-functional pads
Power Routing
- Use wide traces or power planes for low impedance
- Use separate analog and digital power traces/planes to prevent cross-contamination
- Connect Decoupling capacitors close to ICs with short, wide traces
- Use star routing topology for power distribution
Signal Routing
- Group related signals together
- Separate sensitive analog signals from noisy digital traces
- Use ground guard traces between sensitive signals
- Route clock traces on inner layers close to ground planes
- Keep high-speed traces away from board edges
- Avoid routing traces under crystals or oscillators
- Use ground stitching vias to provide consistent return paths
PCB Layers and Stack-Up
A PCB Stack-Up refers to the arrangement of copper and dielectric layers in a multi-layer PCB. The stack-up determines the number of routing layers, the impedances of the traces, and the overall thickness of the PCB.
Common PCB layer stack-ups are:
Layers | Stack-up |
---|---|
2 | Signal – Ground |
4 | Signal – Ground – Power – Signal |
6 | Signal – Ground – Signal – Signal – Power – Signal |
In general, it is good practice to have dedicated ground and power planes, and to symmetrically arrange the layers to prevent warpage. High-speed designs may use special stack-ups with extra ground planes for improved signal integrity.
FAQ
What is the difference between a trace and a via?
A trace is a flat conductive pathway on the surface of a PCB layer, while a via is a vertical hole that is plated with metal to connect traces on different layers together.
How do you calculate the current carrying capacity of a trace?
The current carrying capacity of a trace depends on its cross-sectional area (width x thickness), the allowable temperature rise, and the ambient temperature. It can be calculated using the IPC-2152 standard or online trace current capacity calculators.
What is a necked-down trace?
A necked-down trace is a trace that has a reduced width for a short segment, usually near a component pad or via. Necking down is done to allow for more routing space but can create a hot spot due to the higher current density in the narrower section.
What is the difference between microstrip and stripline traces?
Microstrip traces are routed on the outer layers of a PCB, with one side exposed to air. Stripline traces are routed on inner layers, with ground planes above and below. Striplines have better controlled impedance and lower crosstalk compared to microstrips.
What is a blind via and a buried via?
A blind via connects an outer layer to an inner layer, but does not go through the entire PCB. A buried via connects two inner layers without touching the outer layers. Blind and buried vias are used to save space on the outer layers but are more expensive to manufacture compared to standard through-hole vias.
Leave a Reply