The printed circuit board (PCB) industry has seen incredible innovations in recent years. One of the most exciting is the development of rigid-flex PCBs. These boards offer flexibility and durability far beyond traditional rigid boards. For projects with space constraints or complex interconnect requirements, rigid-flex is often the best choice. The downside is long lead times of 4-8 weeks for fabrication. However, some PCB manufacturers now offer fast turn rigid flex PCBs with lead times of just 4-7 days.
What Are Rigid Flex PCBs?
Rigid-flex PCBs provide the best of both worlds – the support of rigid boards and the flexibility of flex circuits. They contain both rigid sections and flexible polyimide sections allowing the board to bend and fold. Rigid sections provide stability and component mounting surfaces, while flex interconnects enable dynamic fit and 3D configuration capabilities.
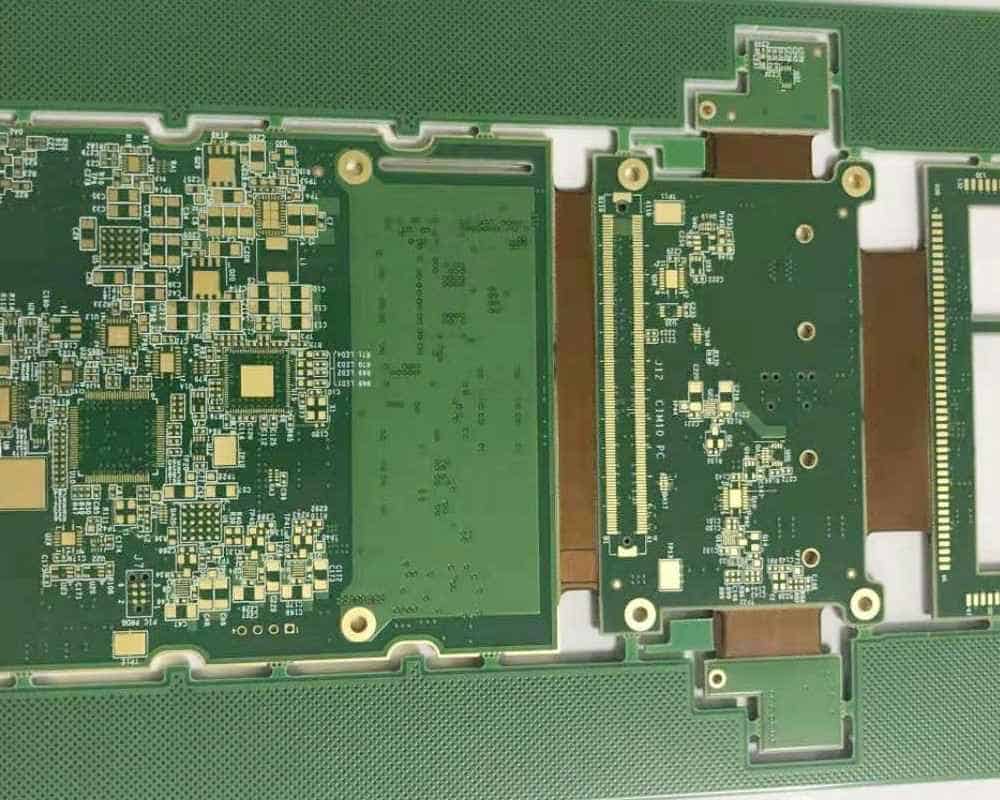
Rigid flex boards have many advantages over traditional PCBs:
- Flexible – can bend, fold and twist to fit constrained spaces
- Dynamic – can accommodate movement and articulation
- Reliable – excellent shock and vibration resistance
- Lightweight – thinner and lighter than rigid boards
- Efficient – optimal for complex routing and dense interconnections
- Packaged Efficiently – condensed and space saving
With these capabilities, rigid-flex PCBs are ideal for products like:
- Wearable devices
- Internet of Things (IoT) products
- Robotics and UAVs
- Medical instruments
- Automotive electronics
- Aerospace avionics
However, rigid flex PCB fabrication typically has long lead times. This is due to the complex laminating process which bonds the rigid and flex layers together. But now PCB manufacturers offer fast turn rigid flex to accelerate time to market.
Fast Turn Rigid Flex PCB Capabilities
In the past, rigid flex PCBs typically required 4-8 week lead times. This made prototyping iterations slow and new product launches take much longer. However, advanced manufacturers have developed fast turn rigid flex capabilities that slash lead times to 4-7 days.
With fast turnaround, engineers can quickly test prototypes and bring innovative products to market faster. Shorter lead times mean you can fail faster, learn quicker, and iterate more times before product release.
Fast turn rigid flex PCB capabilities include:
Rapid Design Verification
- 24 hour design review and prototyping feedback
- Quickly confirm design intent before full fabrication
Advanced Supply Chain
- Local sourcing of base materials
- Eliminates wait times for offshore materials
Optimized Fabrication
- Parallel processing and flex-optimized lines
- Automated inspection and testing
Consolidated Shipping
- Coordinated transportation and logistics
- Consolidates multiple deliveries into one shipment
This combination of capabilities allows PCB manufacturers to reduce lead times from weeks to days.
When to Use Fast Turn vs. Standard Lead Times
With vastly reduced lead times for rigid flex PCBs, when should you utilize fast turn services? Here are some guidelines on when to use fast turn or standard times:
Fast Turn 4-7 Days
- Prototyping – validate concepts quickly
- Design revisions – make rapid adjustments
- New product development – speed up launch timeline
Standard Lead Times 4-8 Weeks
- Mass production – lower costs in volume
- Existing/mature designs – maximize yield
- Non-urgent projects – control spending
In the early stages of development, fast turnaround is highly beneficial. The ability to quickly test prototypes and make revisions accelerates learning. This results in higher quality finished products developed faster.
Once a design is stable for production, standard lead times provide cost savings. The focus shifts to optimizing fabrication yield rather than speed.
Rigid Flex PCB Design Considerations
To maximize quality and manufacturability, keep these design guidelines in mind when developing rigid flex PCBs:
- Match Coefficients of Thermal Expansion (CTE) – Use compatible rigid and flex materials to prevent warping and separation during temperature changes. FR-4 and polyimide film usually work well together.
- Distribute Stiffeners – Add rigid support regions throughout flex areas to prevent flexing beyond material capabilities. Stiffeners prevent damage and failures.
- Avoid Acute Bends – Design bends with radii greater than 2X material thickness to prevent cracking and failures.
- Minimize Flex Layers – Use single or double layer flex regions when possible. High layer count flex is difficult to manufacture reliably.
- Optimize Component Placement – Position components in rigid sections and away from curvatures to avoid stressing solder joints.
- Account for Dynamic Clearances – Ensure adequate clearances between traces and pads in both static and dynamic positions. Flexing changes spacing.
Following design for manufacturing guidelines upfront will ensure your rigid flex PCBs can be fabricated successfully with quality and reliability.
Comparing Fast Turn Rigid Flex PCB Manufacturers
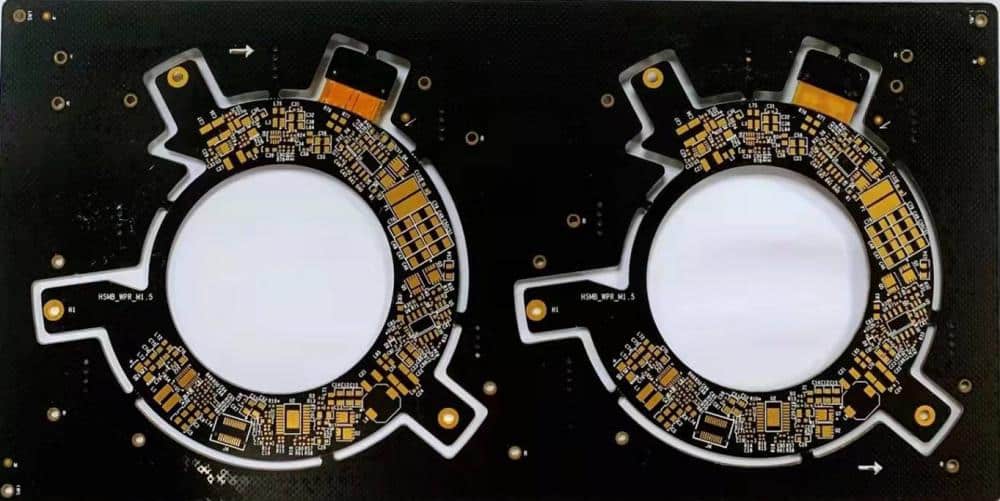
If fast turnaround is critical for your project, how do you select the right rigid flex PCB manufacturer? Here are key factors to consider in your evaluation:
Experience
- Years in business and number of customers served
- Case studies and examples of past performance
- Types of products fabricated (rigid flex expertise)
Quality
- IPC certifications held
- Inspection practices and capabilities
- Historical yields and defect rates
Reliability
- Circuit board and flex material quality
- Qualification and testing capabilities
- Field failure rate history
Customer Service
- Responsiveness and communication
- Design review process and feedback
- Customer support reputation
Value
- Pricing and minimum order quantities
- Standard free services (design review, etc.)
- Shipping costs and logistics services
By thoroughly evaluating manufacturers on these criteria, you can select a trusted partner for your fast turn rigid flex PCB production.
FQA About Fast Turn Rigid Flex PCBs
Here are answers to some frequently asked questions about fast turn rigid flex PCB capabilities:
What are the typical lead times for rigid flex PCBs?
Traditional lead times are 4-8 weeks. However, advanced manufacturers offer fast turn services with 4-7 day lead times.
What’s the primary benefit of fast turnaround?
Faster iteration and reduced time to market. You can test prototypes faster and launch products sooner.
What types of designs are best suited for fast turn?
New product introductions still in prototyping stage. Also good for mature products needing design tweaks and revisions.
Is quality reduced with fast turn services?
No – reputable manufacturers use same quality processes but expedite materials and utilize optimized production lines.
How can fast turn services reduce lead times so drastically?
By sourcing materials locally, parallel processing, inspection automation, and logistics coordination. It’s an end-to-end acceleration.
Does fast turn have higher costs than standard services?
Sometimes, but savings from faster development and market introduction often outweigh the premium.
Ready for Faster Rigid Flex PCB Prototypes?
Rigid flex PCBs enable innovative designs not possible with rigid boards. And fast turn capabilities drastically accelerate development timelines. With a trusted partner, your team can shave weeks off project schedules and launch products ahead of the competition.
Ready to discuss your rigid flex PCB needs? Contact us today to explore how fast turn services can benefit your next project!
Leave a Reply