What are High-Conductivity PCBs?
High-conductivity PCBs, also known as thermal management PCBs, are specially designed circuit boards that prioritize heat dissipation. Unlike traditional PCBs, which primarily focus on electrical conductivity, high-conductivity PCBs incorporate materials and features that enhance Thermal Conductivity. By efficiently transferring heat away from power devices, these PCBs help maintain optimal operating temperatures and improve overall system performance.
Key Features of High-Conductivity PCBs
- Thermal Conductivity: High-conductivity PCBs utilize materials with excellent thermal conductivity properties, such as copper, aluminum, or specialized thermal substrates.
- Thermal Vias: These PCBs often incorporate thermal vias, which are strategically placed vias filled with thermally conductive materials to facilitate heat transfer through the board.
- Heat Spreading Layers: Additional layers, such as thick copper planes or dedicated heat spreading layers, are incorporated to evenly distribute heat across the PCB.
- Thermal Interface Materials (TIMs): TIMs, such as thermal pads or thermal adhesives, are used to improve thermal contact between the power device and the PCB, enhancing heat transfer efficiency.
Type 1: Metal Core PCBs (MCPCBs)
Metal Core PCBs (MCPCBs) are a popular choice for high thermal conductivity applications. These PCBs feature a metal substrate, typically aluminum or copper, which acts as a heat spreader. The metal substrate is sandwiched between the top and bottom layers of the PCB, providing a direct path for heat dissipation.
Advantages of MCPCBs
- Excellent Thermal Conductivity: The metal substrate in MCPCBs offers superior thermal conductivity compared to traditional FR-4 PCBs, enabling efficient heat dissipation.
- Lightweight and Compact: MCPCBs are thinner and lighter than other high-conductivity PCB options, making them suitable for space-constrained applications.
- Cost-Effective: MCPCBs are relatively cost-effective compared to other high-conductivity PCB solutions, making them an attractive option for many power device applications.
Applications of MCPCBs
MCPCBs are commonly used in power-intensive applications such as:
- LED lighting systems
- Power supplies
- Motor drives
- Automotive electronics
Type 2: Insulated Metal Substrate (IMS) PCBs
Insulated Metal Substrate (IMS) PCBs are another popular choice for high thermal conductivity applications. IMS PCBs consist of a metal substrate, typically aluminum, covered with a thin layer of dielectric material. The dielectric layer provides electrical insulation while allowing efficient heat transfer from the power device to the metal substrate.
Advantages of IMS PCBs
- High Thermal Conductivity: IMS PCBs offer excellent thermal conductivity due to the metal substrate, enabling efficient heat dissipation from power devices.
- Electrical Isolation: The dielectric layer in IMS PCBs provides electrical isolation between the power device and the metal substrate, preventing short circuits and ensuring safe operation.
- Mechanical Strength: The metal substrate in IMS PCBs provides mechanical strength and rigidity, making them suitable for harsh environments and applications with vibration or mechanical stress.
Applications of IMS PCBs
IMS PCBs are commonly used in applications such as:
- High-power LED lighting
- Automotive electronics
- Power converters
- Industrial controls
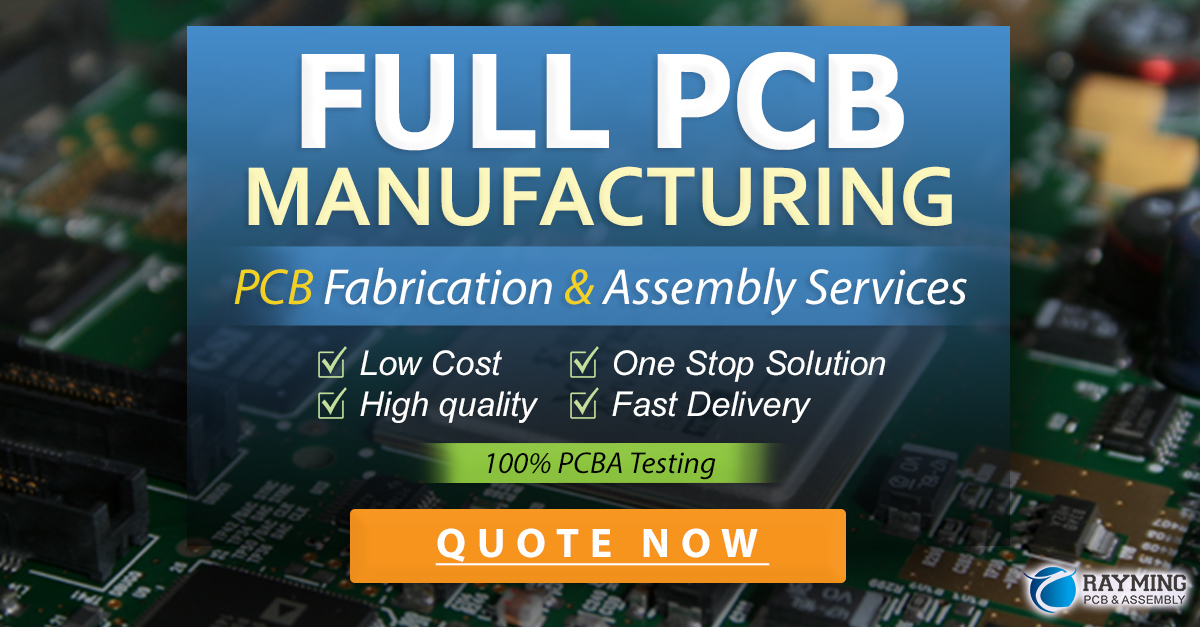
Type 3: Direct Bonded Copper (DBC) PCBs
Direct Bonded Copper (DBC) PCBs are a specialized type of high thermal conductivity PCB that offers exceptional thermal performance. DBC PCBs consist of a ceramic substrate, typically aluminum oxide (Al2O3) or aluminum nitride (AlN), with a layer of copper bonded directly to both sides of the substrate. The direct bonding process creates a strong, thermally conductive interface between the copper and the ceramic substrate.
Advantages of DBC PCBs
- Superior Thermal Conductivity: DBC PCBs offer the highest thermal conductivity among the three types of high-conductivity PCBs discussed in this article. The ceramic substrate and direct bonding process enable exceptional heat dissipation capabilities.
- Excellent Electrical Insulation: The ceramic substrate in DBC PCBs provides excellent electrical insulation, allowing for high voltage operation and preventing electrical breakdown.
- High Reliability: DBC PCBs are known for their high reliability and durability, even in challenging environmental conditions such as high temperatures and thermal cycling.
Applications of DBC PCBs
DBC PCBs are commonly used in high-power and high-temperature applications such as:
- Power electronics modules
- Electric vehicle inverters
- Solar inverters
- High-power LED lighting
Comparison Table
PCB Type | Thermal Conductivity | Electrical Insulation | Mechanical Strength | Cost |
---|---|---|---|---|
MCPCB | High | Low | Moderate | Low |
IMS PCB | High | Moderate | High | Moderate |
DBC PCB | Very High | High | High | High |
Frequently Asked Questions (FAQ)
- Q: How do high-conductivity PCBs differ from traditional PCBs?
A: High-conductivity PCBs incorporate materials and features that prioritize thermal conductivity, such as metal substrates, thermal vias, and heat spreading layers. Traditional PCBs primarily focus on electrical conductivity and may not have specialized thermal management capabilities. - Q: Can high-conductivity PCBs be used in all electronic applications?
A: While high-conductivity PCBs are highly beneficial for power device applications that generate significant heat, they may not be necessary for low-power or low-heat applications. The choice of PCB type depends on the specific thermal management requirements of the application. - Q: What factors should be considered when selecting a high-conductivity PCB?
A: When selecting a high-conductivity PCB, consider factors such as the thermal conductivity requirements, electrical insulation needs, mechanical strength, and cost. The specific application and its operating conditions will dictate the most suitable type of high-conductivity PCB. - Q: Can high-conductivity PCBs be customized for specific applications?
A: Yes, high-conductivity PCBs can be customized to meet the specific requirements of an application. Factors such as the PCB layout, layer stack-up, thermal via placement, and material selection can be tailored to optimize thermal performance and meet other design constraints. - Q: Are there any challenges associated with manufacturing high-conductivity PCBs?
A: Manufacturing high-conductivity PCBs can be more complex compared to traditional PCBs. Specializedmaterials, bonding processes, and precise control of layer thicknesses are required to ensure optimal thermal performance. Working with experienced PCB manufacturers who have expertise in high-conductivity PCBs is essential for successful production.
Conclusion
High thermal conductivity PCBs play a crucial role in effectively dissipating heat from power devices, ensuring optimal performance and reliability. The three types of high-conductivity PCBs discussed in this article – Metal Core PCBs (MCPCBs), Insulated Metal Substrate (IMS) PCBs, and Direct Bonded Copper (DBC) PCBs – offer distinct advantages and are suitable for different applications based on their thermal conductivity, electrical insulation, mechanical strength, and cost considerations.
When designing power device applications, it is essential to carefully evaluate the thermal management requirements and select the appropriate type of high-conductivity PCB. Factors such as the operating environment, power density, and reliability expectations should be taken into account. Collaborating with experienced PCB manufacturers and thermal management experts can help ensure the successful implementation of high-conductivity PCBs in power device applications.
As the demand for efficient and reliable power electronics continues to grow across various industries, the importance of high thermal conductivity PCBs cannot be overstated. By leveraging the benefits of MCPCBs, IMS PCBs, and DBC PCBs, designers can effectively manage heat dissipation, enhance system performance, and ensure the long-term reliability of power devices. As technology advances, it is likely that new materials and manufacturing techniques will further improve the thermal management capabilities of high-conductivity PCBs, enabling even more advanced and efficient power device applications in the future.
Leave a Reply