Introduction to COB LED Manufacturing
COB (Chip-on-Board) LED manufacturing is a cutting-edge technology that has revolutionized the lighting industry. This innovative approach to LED packaging involves mounting multiple LED chips directly onto a substrate or circuit board, creating a single, compact light source. COB LED manufacturing offers numerous advantages over traditional LED packaging methods, including improved efficiency, better heat dissipation, and enhanced color consistency.
In this ultimate guide, we will delve into the world of COB LED manufacturing, exploring its key aspects, benefits, and applications. Whether you are a lighting professional, a manufacturer, or simply interested in learning more about this advanced technology, this comprehensive guide will provide you with valuable insights and information.
Understanding COB LED Technology
What is COB LED?
COB LED, or Chip-on-Board LED, is a packaging technology where multiple LED chips are mounted directly onto a substrate or circuit board, forming a single light source. Unlike traditional LED packaging methods, such as SMD (Surface Mounted Device) or DIP (Dual In-line Package), COB LED packaging eliminates the need for individual LED packaging and allows for a higher density of LED chips on a single board.
Key Features of COB LED
- High LED Chip Density: COB LED technology enables a high density of LED chips to be mounted on a single substrate, resulting in a compact and powerful light source.
- Improved Thermal Management: The direct mounting of LED chips onto the substrate allows for better heat dissipation, which is crucial for maintaining the longevity and performance of the LEDs.
- Enhanced Color Consistency: COB LED packaging ensures that all LED chips are closely packed together, resulting in a more uniform and consistent color output.
- Simplified Driver Circuitry: With COB LED technology, the driver circuitry can be simplified, as all LED chips are connected in series on a single board.
- Versatile Beam Angles: COB LEDs can be designed with various beam angles, from narrow spot lights to wide flood lights, making them suitable for a wide range of applications.
Advantages of COB LED over Traditional LED Packaging
Aspect | COB LED | Traditional LED Packaging |
---|---|---|
LED Density | High density of LED chips on a single substrate | Limited density due to individual LED packaging |
Heat Dissipation | Direct mounting on substrate improves thermal management | Individual packaging hinders effective heat dissipation |
Color Consistency | Closely packed LED chips ensure uniform color output | Variations in color due to separate packaging of LED chips |
Driver Circuitry | Simplified driver circuitry as LEDs are connected in series | Complex driver circuitry for individual LED control |
Beam Angle | Versatile beam angles, from narrow spot to wide flood | Limited beam angle options due to individual LED packaging |
COB LED Manufacturing Process
Step 1: Substrate Preparation
The COB LED manufacturing process begins with the preparation of the substrate or circuit board. The substrate material is typically made of aluminum or ceramic, chosen for its excellent Thermal Conductivity and mechanical stability. The substrate is cleaned and treated to ensure proper adhesion of the LED chips.
Step 2: LED Chip Placement
Next, the LED chips are placed onto the substrate using a high-precision Pick-and-Place machine. The machine accurately positions the LED chips on the designated locations on the substrate, ensuring proper alignment and spacing. The number and arrangement of LED chips depend on the desired output and application of the COB LED.
Step 3: Wire Bonding
Once the LED chips are placed on the substrate, they are connected using a process called wire bonding. Thin gold or aluminum wires are used to create electrical connections between the LED chips and the substrate. Wire bonding ensures that the LED chips are properly connected in series, allowing for uniform current distribution and optimal performance.
Step 4: Encapsulation
After wire bonding, the COB LED undergoes an encapsulation process to protect the LED chips and wire bonds from environmental factors such as moisture, dust, and mechanical stress. A silicone or epoxy resin is applied over the LED chips and wire bonds, creating a protective layer that also enhances light extraction and color consistency.
Step 5: Phosphor Coating (Optional)
For white COB LEDs, an additional step of phosphor coating is required. A phosphor material, typically made of yttrium aluminum garnet (YAG), is applied over the encapsulated LED chips. The phosphor converts the blue light emitted by the LED chips into white light, allowing for the creation of high-quality white COB LEDs.
Step 6: Singulation and Packaging
Once the COB LED is encapsulated and coated with phosphor (if required), it undergoes a singulation process where the substrate is cut into individual COB LED modules. The modules are then packaged according to the specific requirements of the application, such as adding a heat sink, lens, or reflector.
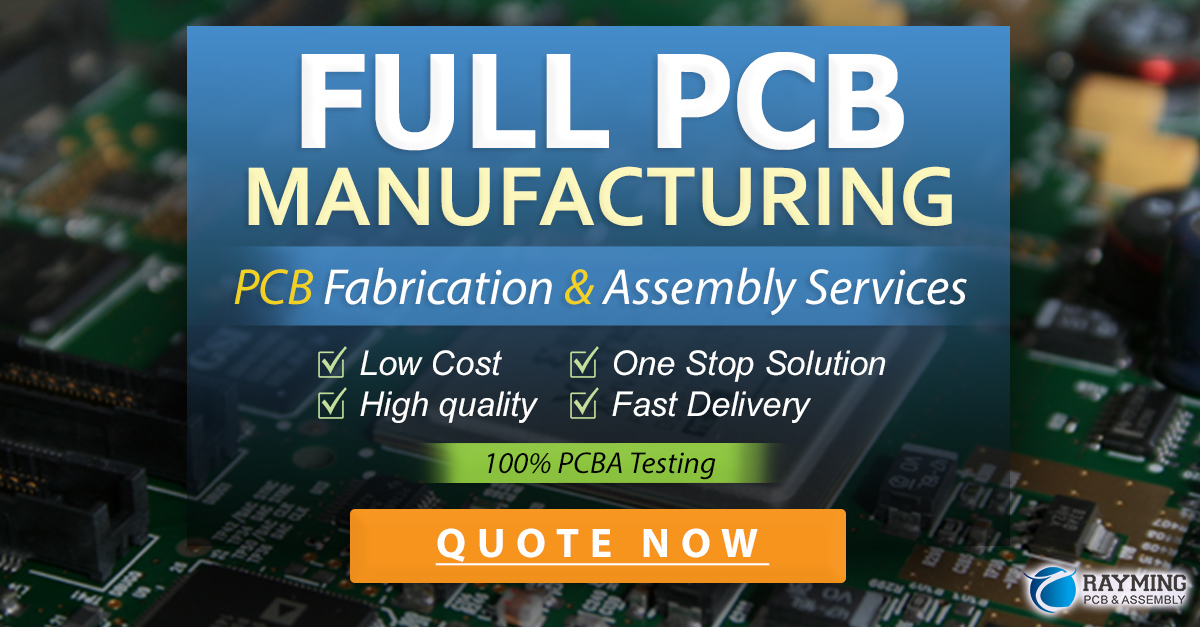
Applications of COB LED
COB LED technology finds applications in various domains, thanks to its high efficiency, compact size, and superior color consistency. Some of the key applications of COB LED include:
- General Lighting: COB LEDs are widely used in general lighting applications, such as indoor and outdoor lighting, downlights, spotlights, and track lights.
- Automotive Lighting: COB LEDs are increasingly used in automotive lighting applications, including headlights, taillights, and interior lighting, due to their high brightness and compact size.
- Horticulture Lighting: COB LEDs are ideal for horticulture lighting applications, as they can be customized to provide the specific wavelengths of light required for optimal plant growth.
- Stage and Entertainment Lighting: COB LEDs are used in stage and entertainment lighting, offering high brightness, color consistency, and beam control for creating dynamic lighting effects.
- Medical Lighting: COB LEDs are used in medical lighting applications, such as surgical lights and examination lights, providing bright, focused, and shadow-free illumination.
Benefits of One-Stop COB LED Manufacturing
One-stop COB LED manufacturing offers numerous benefits for businesses and customers alike. By consolidating the entire manufacturing process under one roof, one-stop manufacturing ensures:
- Streamlined Production: One-stop manufacturing eliminates the need for coordinating with multiple suppliers and manufacturers, streamlining the production process and reducing lead times.
- Quality Control: With all manufacturing steps performed in-house, one-stop manufacturing allows for stringent quality control measures, ensuring consistent and high-quality COB LED products.
- Customization Opportunities: One-stop manufacturing enables greater flexibility in customizing COB LED products according to specific customer requirements, such as size, color temperature, and beam angle.
- Cost Efficiency: By eliminating the need for multiple suppliers and reducing transportation costs, one-stop manufacturing can lead to cost savings that can be passed on to the customers.
- Faster Time-to-Market: One-stop manufacturing accelerates the product development and production process, enabling faster time-to-market for new COB LED products.
Frequently Asked Questions (FAQ)
-
What is the difference between COB LED and SMD LED?
COB LED and SMD LED are two different packaging technologies for LEDs. COB LED involves mounting multiple LED chips directly onto a substrate, forming a single light source, while SMD LED packages individual LED chips separately. COB LED offers higher LED density, better heat dissipation, and improved color consistency compared to SMD LED. -
Can COB LEDs be dimmed?
Yes, COB LEDs can be dimmed using appropriate dimming drivers and control systems. However, it is essential to ensure that the dimming driver is compatible with the specific COB LED product and that the dimming range is suitable for the intended application. -
How long do COB LEDs last?
COB LEDs have a long lifespan, typically lasting up to 50,000 hours or more, depending on the specific product and operating conditions. Factors such as temperature, current, and voltage can impact the lifespan of COB LEDs. -
Are COB LEDs more energy-efficient than traditional lighting sources?
Yes, COB LEDs are significantly more energy-efficient than traditional lighting sources, such as incandescent bulbs and fluorescent lamps. COB LEDs can convert a higher percentage of electrical energy into light, resulting in lower power consumption and reduced energy costs. -
How do I choose the right COB LED for my application?
When selecting a COB LED for your application, consider factors such as the required luminous flux, color temperature, color rendering index (CRI), beam angle, and thermal management requirements. It is also essential to ensure that the COB LED is compatible with the intended driver and control system. Consulting with a COB LED manufacturer or lighting professional can help you make an informed decision based on your specific needs.
Conclusion
COB LED manufacturing has transformed the lighting industry, offering a compact, efficient, and high-performance solution for a wide range of applications. With its superior thermal management, color consistency, and design flexibility, COB LED technology has become the preferred choice for lighting professionals and manufacturers worldwide.
By opting for one-stop COB LED manufacturing, businesses can benefit from streamlined production, enhanced quality control, customization opportunities, cost efficiency, and faster time-to-market. As the lighting industry continues to evolve, COB LED technology is poised to play a crucial role in shaping the future of illumination.
Whether you are a lighting designer, manufacturer, or end-user, understanding the intricacies of COB LED manufacturing is essential for making informed decisions and harnessing the full potential of this advanced technology. By following this ultimate guide, you can navigate the world of COB LED manufacturing with confidence and unlock new possibilities for your lighting applications.
Leave a Reply