Electronic component manufacturing is the process of fabricating the various individual parts and devices that will be assembled into finished electronic systems. The electronics industry relies on a vast global supply chain of component manufacturing spanning semiconductors, passives, connectors, electromechanical parts, and more. Understanding the manufacturing processes for these components provides insight into how raw materials are transformed into the building blocks of electronic circuits and systems.
This article provides an overview of the technologies and techniques used to manufacture the diverse range of electronic components and their packaging. We will examine fabrication methods for key component families including integrated circuits, passive elements, discrete semiconductors, connectors, and electromechanical parts. The discussion covers both large scale commercial production as well as low volume and prototype approaches.
Integrated Circuit (IC) Manufacturing
Integrated circuits like processors, memory chips, and analog ICs are at the heart of all electronic systems. Their manufacturing relies on semiconductor fabrication facilities, or “fabs”, that use sophisticated techniques to build microscopic transistor circuits on silicon wafers.
Wafer Fabrication
Building ICs on wafers involves complex sequential processes to construct multi-layered semiconductor devices via materials deposition, photolithography patterning, etching, doping, and polishing. Hundreds of steps are required to yield finished wafers containing identical ICs arrays.
IC Packaging
After fabrication, wafer IC dies are tested and cut from the wafer before assembly into packages that connect the die to a circuit board. Popular package types include:
- Plastic dual in-line packages (DIP)
- Small outline integrated circuits (SOIC)
- Quad flat packs (QFP)
- Ball grid arrays (BGA)
- Chip scale packages (CSP)
Packaging attaches wire bonds or flip chip bumps to IC pads and encapsulates the die in a protective housing with pins or leads for board mounting.
IC Assembly
Component placement, wire bonding, and molding steps assemble packaged ICs ready for shipment to electronics manufacturers. Automated assembly lines perform precision high-rate placement and soldering.
IC fabs require multi-billion dollar investments. Cutting-edge process nodes below 10nm push the limits of physics and are owned by just a handful of companies. However, older nodes above 130nm can be accessed through small to medium size silicon foundries.
Passive Component Manufacturing
Passive components like resistors, capacitors, and inductors serve fundamental roles in every electronic circuit. Manufacturing processes for the main passives categories include:
Resistors
Fixed resistor types:
- Carbon Film – Made by depositing resistive carbon compound on ceramic rod.
- Metal Film – Nichrome or tantalum wire wound around ceramic core.
- Metal Oxide – Oxide deposited on ceramic substrates using screening printing or sputtering.
Variable trimmer potentiometers use cermet thick film printing or wire winding. All types encapsulated in epoxy cases and lead terminated.
Capacitors
Popular capacitors and their manufacturing:
- Multilayer Ceramic – Alternating layers of metal and dielectric printed and stacked to form a monolithic block.
- Tantalum – Sintered tantalum powder surrounds tantalum wire in molten salt bath.
- Aluminum Electrolytic – Aluminum foil and electrolyte rolled into a cylinder shape.
- Film – Thin plastic film like polyester sandwiched between metal foil plates.
Leads attached via soldering or conductive epoxy.
Inductors
Inductor types:
- Wire wound – Coiled insulated copper wire around ferrite or air core.
- Thick film – Printed inductor fired onto a ceramic substrate.
- Multilayer – Alternating conductive and dielectric layers pressed and cofired.
Most are encapsulated in epoxy or coated. Small high-frequency chip inductors left unpackaged.
Robotic assembly of passive components onto reels and tapes facilitates automated pick-and-place.
Discrete Semiconductor Manufacturing
Discrete diodes, transistors, and thyristors serve as common active components. Key steps:
Wafer Fabrication
Similar to ICs, discrete semiconductors are built on wafers through doping, layering, diffusion, and photolithography. Lower complexity than ICs.
Die Attachment
Dies cut from wafer are epoxy attached to metal lead frames in upside-down configuration to facilitate heat transfer through the leads.
Wire Bonding
Thin gold or aluminum wires connect die pads to leads electrically via ultrasonic or thermosonic processes.
Encapsulation
Molding or dipping seals the die and wires in epoxy resin blocks for environmental and mechanical protection.
Lead Trimming
Excess leads are trimmed away leaving just the terminal leads. Lead frame is etched away.
Automated assembly and modular packages like TO-92 and SOT-23 help enable cost-effective production.
Connector Manufacturing
Connectors provide detachable electrical links between components or systems through impedance-matched physical interface. Major families and their manufacturing include:
Board Level Connectors
- Pin and Socket – Stamped pins inserted into molded housings.
- Edge Card – Formed metal contacts crimped onto plastic or ceramic.
- D-Sub – Stamped pins set into metal shielding.
Wire-to-Board
- Terminal Blocks – Screw terminals inserted into plastic or ceramic blocks.
- Headers – Machined, stamped, or formed leads set in housings.
Cable Assemblies
- Circular – Multipin connectors contain soldered/crimped wires.
- Ribbon – Parallel wire cables with insulation displacement termination.
Automated machining and molding form parts while robotic assembly solders connections.
Electromechanical Parts Manufacturing
Switches, relays, sensors, and other mechanical components with electrical inputs/outputs comprise another category:
Switches
- Snap action – Formed metal contact domes on pc board or housing.
- Tactile switches – Formed contacts under molded button surface.
- Toggle and rocker switches – Molded or machined plastic bodies with internally fabricated mechanical contacts.
Relays
- Electromechanical – Coiled fine wire around iron core actuates mechanical contacts. Automated coil winding.
- Solid state – Discrete semiconductor components on printed circuit substrates.
Other Electromechanical
- Connectors use insert molding, stamping, machining
- Sensors use semiconductor fab processes combined with micromachining techniques.
- PCBs use automated multilayer printed circuit fabrication.
Hybrid processes manufacture electromechanical parts, combining both mechanical forming and electrical circuit fabrication.
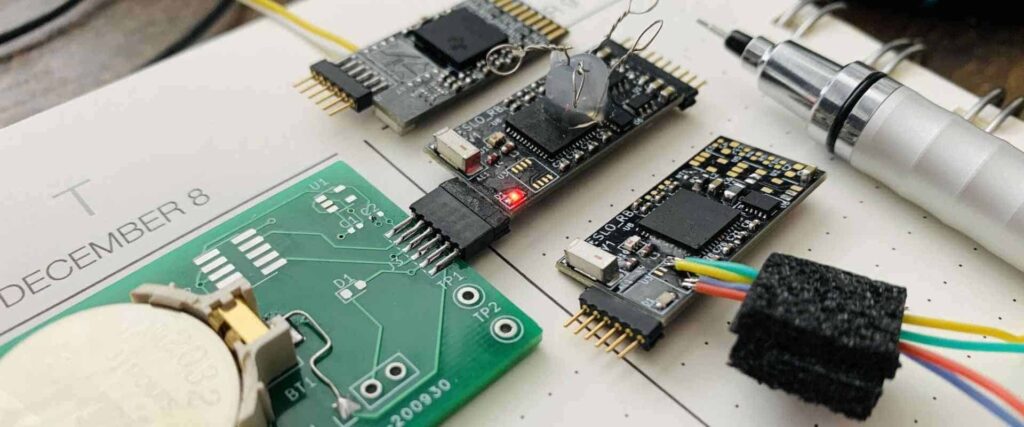
Component Packaging and Interconnects
Packaging and interconnect processes integrate components into assemblies:
Lead Wires and Terminals
- Connector leads stamped or machined
- Insulated wire cut, stripped, and tinning
- Heat shrink tubing cut for insulation
- Solder lugs and terminals stamped
Board Assembly
- SMT assembly uses pick-and-place and reflow ovens
- PTH assembly uses wave or hand soldering
- Conformal coating done via spraying or dipping
Enclosure Fabrication
- Plastic enclosures molded via injection or machining
- Sheet metal enclosures formed by stamping and bending
- Cast enclosures from metal alloys
Automation allows mass manufacturing while flexibility enables small batch fabrication.
Materials for Electronics Manufacturing
Electronic components utilize a diverse array of materials spanning metals, plastics, ceramics, semiconductors and more:
Metals
- Gold – Bonding wires
- Copper – Traces, pins, leads
- Tin – Solder, plating
- Aluminum – Heat sinks, capacitors
- Nickel, tungsten, cobalt – Alloys, resistors
Plastics and Polymers
- Epoxy – Encapsulants, insulation
- PVC – Wire insulation
- Polycarbonate – Connector bodies
- Polyester, polystyrene – Capacitors
- PTFE – High temperature wire
Ceramics and Glass
- Alumina – Substrates, packaging
- Silica – Insulators, passives
- Beryllia – Thermal management
- Ferrite – Inductors, transformers
- Quartz – Resonators, filters
Semiconductors
- Silicon – ICs, discrete semiconductors, sensors
- Gallium arsenide – High speed ICs
- Germanium – Transistors
- Doped silicon – Diodes
Composites
- FR4 – Circuit boards
- Carbon composite – Structural and thermal
- Ceramic matrix – High temperature boards
Combining elemental materials into composites attains specific electrical, mechanical, and thermal properties for applications.
Low Volume and Prototype Manufacturing
While high volume commercial production uses dedicated factories, R&D and prototypes employ flexible smaller scale manufacturing. These leverage:
Manual Assembly
- Hand soldering
- Wire bonding and crimping
- Precision assembly fixtures
CNC Machining
- Milling of boards, enclosures, parts
- Drilling, routing, grinding, engraving
3D Printing
- SLA, SLS, FDM plastics printing
- DMLS metal printing
- Printed electronics deposition
Rapid Tooling
- 3D printed molds for injection molding
- Laser/machined mold masters
- Castable tooling resins
Flexible Electronics
- Inkjet and aerosol printing
- Photolithography film exposures
- Laser direct structuring
Short runs, custom designs, and fast turnaround characterize prototyping production based on these technologies.
Quality Management
Maintaining quality levels during electronics manufacturing involves:
- Statistical process control tracking
- Test and inspection regimes
- Controlled procedures and training
- Supply chain qualification
- Traceability systems
- Configuration control
- Corrective action processes
Quality must be designed in and actively managed given the unforgiving tolerances of electronics.
Conclusion
Modern electronic systems stand on a foundation of sophisticated component manufacturing processes. From semiconductor fabrication to polymer molding, each technique adds unique value in transforming raw materials into functional circuits. The diversity of manufacturing approaches highlights the breadth of the electronics industry supply chain.
Ongoing technology advances continue to drive manufacturing improvements including automation, smart manufacturing, nanotechnology, and sustainability. By understanding the transformations involved in their creation, engineers gain deeper insight into the design and integration of electronic components at the core of every system.
Frequently Asked Questions
What are some key differences between commercial and military/aerospace electronic component manufacturing?
Some key differences:
- Added documentation – Full traceability and control plans required in aerospace/military.
- Extended qualification – Components qualified over wider temperature and operating ranges.
- Enhanced testing – 100% test coverage including x-ray, long term burn-in.
- Tighter tolerances – Tighter defect limits to ppm vs. percent levels.
- Specialized materials – Use of hardened components to withstand vibration, radiation, etc.
- ITAR compliance – Special controls for restricted technology.
- Longer lifecycles – Decades vs. commercial lifecycles in years.
Aerospace and military requirements result in much more rigorous materials, validation, and quality control relative to commercial grade electronics.
What are some newer technologies emerging in electronics manufacturing?
Some newer and emerging technologies include:
- Additive manufacturing like 3D printing of circuits and components
- Advanced robotics for assembly automation
- Smart vision systems for inspection and control
- Nanomaterials for next-generation electronics
- High density interconnect PCBs
- Flexible hybrid electronics (FHE)
- Artificial intelligence for manufacturing optimization
- Sustainable materials and processes
Many innovations aim to increase precision and customization while reducing cycle times and costs.
How might component manufacturing need to adapt for very high volume consumer electronics?
Adaptations for ultra high volume like mobile phones:
- Highly automated assembly lines synchronized for maximum throughput
- Minimal non-value added steps
- Just-in-time supply chains for fast material delivery
- Standardized components and modular architecture
- Test and inspection integrated seamlessly inline
- Ultra clean room environments
- Fast changeovers between product variants
- Small footprint equipment with contained material flows
Every part of the process needs to be streamlined and waste eliminated to achieve millions of units manufactured.
What role does quality control play in electronic component manufacturing?
Quality control plays crucial roles across:
- Statistical process monitoring and control
- Inspecting incoming parts and materials
- Executing test procedures at each build stage
- Performing environmental stress screening
- Validating manufacturing tools and processes
- Managing reliability and performance data
- Driving corrective/preventive actions as needed
- Controlling handling and ESD protocols
There is zero tolerance in electronics for undetected defects escaping to customers. Quality is the bedrock for reliable products.
How might component sourcing and procurement need to adapt as technologies evolve?
Adapting component sourcing and procurement approaches as technologies evolve involves:
- Continually qualifying new suppliers, technologies, materials
- Expanding distribution networks as needs grow
- Implementing data standards for searchability/compatibility
- Developing strategic partnerships beyond just cost focus
- Forecasting future component availability challenges
- Investing in custom/bespoke solutions where needed
- Considering geopolitical challenges and localization
- Leveraging online platforms and procurement automation
Sourcing strategies must proactively adapt supply bases to meet evolving technical demands as electronics advance.
Conclusion
In summary, modern electronic systems rely extensively on sophisticated component manufacturing techniques spanning miniaturized semiconductors through precision electro-mechanical assemblies. An understanding of the transformations involved in crafting raw materials into functional circuits provides insight into the art of electronics design. Ongoing advances aim to make manufacturing ever faster, smaller, cheaper, and more precise as component technologies scale up in complexity. But always central will be the methodical fabrication processes that turn base materials into the vital components underpinning electronics innovation.
Leave a Reply