Introduction
A capacitor is a passive electronic component that stores electrical energy in an electric field. Capacitors are widely used in electronic circuits for blocking direct current while allowing alternating current to pass, smoothing power supply voltages, timing circuits, tuning radios, filtering signals, and many other purposes.
Printed circuit board (PCB) capacitors are a type of capacitor that is soldered directly onto the printed circuit board rather than using traditional leaded components. PCB capacitors provide several advantages over leaded capacitors:
Size and Weight
PCB capacitors are much smaller and lighter since they don’t require leads or packaging. This allows for denser PCB layouts and reduced overall weight.
Performance
The shorter connections to a PCB capacitor can provide better high frequency performance compared to leaded versions. Parasitic inductance and resistance introduced by leads is greatly reduced.
Reliability
With no leads to break off or crack solder joints, PCB capacitors are more rugged and reliable. The connections are an integral part of the device.
Automated Assembly
PCB capacitors can be automatically placed and soldered by pick-and-place machines, reducing manufacturing costs and errors.
This article provides an in-depth look at PCB capacitor construction, characteristics, types, applications, and tradeoffs compared to leaded capacitors.
How Do PCB Capacitors Work?
A capacitor consists of two conductive plates or electrodes separated by a dielectric insulator. When voltage is applied, opposite electric charges build up on each plate +Q and -Q. The capacitance (ability to store charge) depends on the area of the plates A, distance between them d, and properties of the dielectric material K:Copy code
C = (K*A)/d
PCB capacitors have a layered construction with alternating metal electrodes and dielectric films stacked together. The electrodes provide the conductive plates and dielectric provides the insulator. Common dielectrics used include ceramic, plastic film, mica, and tantalum oxide.
Here is a cross-section diagram of a multilayer ceramic chip capacitor showing the alternating electrodes connected to terminations on top and bottom:
The terminations allow the capacitor to be soldered to pads on a PCB. The more layers, the greater the capacitance for a given footprint. High capacitance values can be achieved in a small surface mount package.
When voltage is applied to the terminations, charge Q builds up on the electrodes proportional to capacitance:Copy code
Q = C * V
The capacitor stores this charge and blocks direct current (DC) from flowing while passing alternating current (AC). PCB capacitors exhibit the same basic capacitive behavior as leaded versions but in a smaller surface mount form factor.
Types of PCB Capacitors
Many different capacitor dielectrics have been adapted into PCB surface mount packages. Here are some of the most common varieties:
Multilayer Ceramic Capacitors (MLCCs)
MLCCs are the most widely used PCB capacitor type. They are constructed of alternating layers of metal electrode and ceramic dielectric. The ceramic dielectric provides high permittivity allowing high capacitance values. The small size, low cost, and high reliability have made them ideal for all types of PCBs.
MLCCs are available in a huge range of capacitance values from 1 pF to 1 uF and voltage ratings up to 3000V. The most common dielectric formulations are Class 1 ceramics like X7R which offer stability over temperature. High K multilayer ceramic capacitors provide ultra small case sizes for a given capacitance.
Plastic Film Capacitors
These capacitors use thin plastic film like polypropylene as the dielectric. They are constructed by winding alternating layers of metal foil electrode and plastic film into a cylindrical shaped winding. The winding is encased in epoxy resin and has axial or radial terminations.
Plastic film capacitors offer very high insulation resistance and stable capacitance over frequency and temperature. Types like polypropylene film are commonly used for high voltage AC power applications. Radial leaded versions are through-hole mounted while SMT film caps have planar terminations.
Mica Capacitors
Mica is a naturally occurring silicate mineral with excellent dielectric properties. Sheets of mica are layered between metal foil electrodes and assembled into a stack. The stack is enclosed in an epoxy case with leads or surface mount terminations.
Mica capacitors have high stability and low losses at high frequencies like radio VHF/UHF bands. Their power factor and dielectric absorption is very low. These properties make mica a good choice for precision RF and timing circuits.
Tantalum Capacitors
Tantalum capacitors use a sintered porous tantalum anode covered in a thin tantalum pentoxide dielectric layer to achieve high capacitance. The dielectric layer is very thin providing high capacitance but also makes them vulnerable to damage from voltage spikes. Tantalum capacitors offer high capacitance values in small case sizes.
There are two types of tantalum PCB capacitors:
- Solid tantalum – The sintered porous tantalum slug anode is dipped in manganese dioxide electrolyte and encased in a molded epoxy body with terminations.
- Tantalum polymer – The anode uses conductive polymer instead of liquid electrolyte. This allows simpler construction and elimination of the fragile manganese dioxide layer.
Tantalum polymer capacitors have replaced most solid tantalum types due to their better reliability and reduction of potential fire hazard if damaged.
Aluminum capacitors
Aluminum capacitors construct the anode from very high surface area etched aluminum foil that is anodized to form an insulating aluminum oxide layer. The anode and cathode foils are then wound with electrolyte into a cylindrical capacitor. They provide high capacitance in a small size at low cost.
Aluminum electrolytic capacitors are available in through-hole and SMT versions. They have higher leakage than other types and must be polarity oriented when mounting on a PCB due to the electrolyte system. Miniaturized SMT aluminum caps are being developed to replace bulky radial and axial electrolytics.
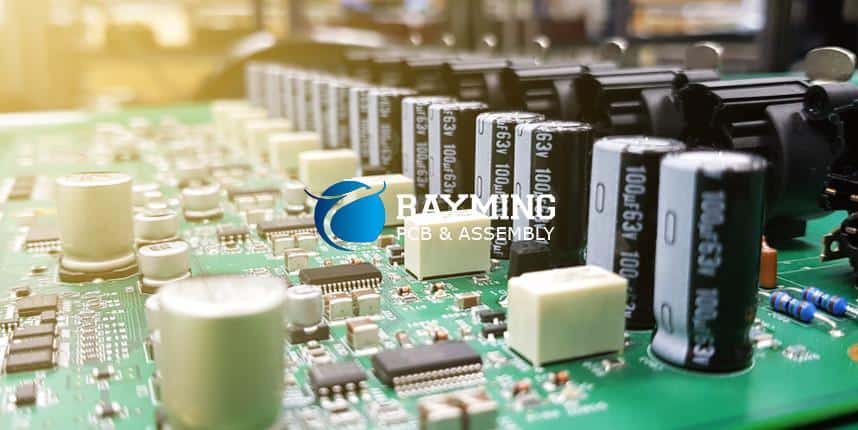
PCB Capacitor Characteristics
Key electrical characteristics to consider for PCB capacitors:
- Capacitance – Capacitance value in Farads. Available from less than 1 pF to over 1 mF. Tolerance can range from +/-1% to +/-20% or more.
- Voltage Rating – Maximum working voltage the capacitor can withstand without damage. Rating is typically in volts DC but may be AC for film and mica types.
- Temperature Coefficient – Changes in capacitance value over temperature. Expressed in parts per million per degree C (ppm/°C). Lower is better for precision applications.
- Leakage Current – Small amount of stray current that leaks through the dielectric. Lower is better, tantalum and film capacitors have very low leakage while electrolytics higher.
- Equivalent Series Resistance (ESR) – Resistive losses due to conductors and capacitor structure. Lower ESR equals better high frequency performance. Important for power supply decoupling.
- Dielectric Absorption (Dissipation Factor) – Inefficiency due to energy retained by the dielectric when the capacitor discharges. Lower values improve capacitor performance for precision applications. Mica and film capacitors have very low absorption.
Below is a comparison table of the capacitance stability, voltage ratings, and costs for common PCB capacitor dielectrics:
Type | Temperature Stability | Voltage Rating | Cost |
---|---|---|---|
Ceramic X7R | Good | Medium | Low |
Ceramic Y5V | Poor | Low | Very low |
Tantalum Polymer | Good | Low | Moderate |
Aluminum Electrolytic | Medium | Medium | Very low |
Plastic Film | Excellent | High | Moderate |
Mica | Excellent | High | High |
PCB Capacitor Packages
Surface mount PCB capacitors are available in a variety of standard package styles. The case size determines the capacitance value that can be achieved. Commonly used package types:
0201 and 0402 Chip Packages
The smallest SMT capacitor packages with length and width dimensions of just 0.02″ x 0.01″ (0201) and 0.04″ x 0.02″ (0402). Used for values typically below 100 nF where small size is critical. Difficult for automated assembly and prone to cracking from stress.
0603 and 0805 Chip Packages
The 0603 (0.06″ x 0.03″) and 0805 (0.08″ x 0.05″) case sizes are the most common chip packages used for values up to 10 uF. Standard pick-and-place equipment handles these sizes well. Provides a good balance of space efficiency and assembly yield.
1206 and 1210 Larger Chips
For capacitance in the 10s of uF range, the larger 1206 (0.126″ x 0.063″) and 1210 (0.126″ x 0.1″) rectangular chip packages are used. The increased area allows more dielectric layers and higher capacitance.
Radial Leaded Packages
Radial leaded capacitors have leads spaced evenly around the circumference in a radial direction. Common for higher voltage film and aluminum electrolytic capacitors. Requires through-hole assembly or can be manually soldered.
Axial Leaded Packages
Axial capacitors have two leads extending from one end of the cylindrical body axially. Allows for compact stacking of multiple capacitors vertically on the circuit board. Requires through-hole assembly and tends to take up more PCB area than other packages.
SMT Aluminum Electrolytic Cans
Aluminum electrolytic capacitors packaged in truncated cone shaped anodized aluminum cans with surface mount terminations are available. Reduces the PCB footprint compared to radial versions. Lower voltage ratings around 25V – 50V.
MELF / SOD Packages
MELF (metal electrode leadless face) and SOD (small outline diode) are molded cylindrical epoxy packages with planar terminations on the ends. Often used for high voltage MLCCs.
PCB Capacitor Applications
PCB capacitors serve many purposes in electronic circuits including:
Decoupling and Bypass
Decoupling capacitors provide charge storage reservoirs close to ICs on the PCB. They smooth power supply variations and noise at high frequencies that could otherwise cause digital logic errors or analog distortion. A typical application is 100 nF ceramic capacitors placed at each power pin of an IC.
AC Coupling and DC Blocking
Capacitors couple AC signals between circuits while blocking DC voltages. This allows DC biasing of various circuit stages independently. Large value electrolytic capacitors are used for audio coupling applications.
Timing and Oscillators
The charge/discharge timing of RC networks provides a simple way to create time delays or generate oscillations. Timing capacitors must have high stability over temperature and frequency variation. Mica, polypropylene, polystyrene film are common choices.
Snubbers
Snubber capacitors suppress voltage spikes across inductive components like transformers and motors when switching on or off. Film or ceramic capacitors are placed in parallel to absorb this energy.
Tuned Circuits
Capacitors and inductors are combined to form tuned RF filter circuits in radios, television, and networking equipment. Variability of ceramic capacitors requires tight tolerance film or mica types for RF tuning capacitors.
Power Factor Correction
Large banks of low ESR aluminum electrolytic capacitors smooth ripple voltage from the rectified AC input to improve power factor and efficiency. This allows proper operation of the power supply.
Energy Storage and Discharge
Flash camera strobes, defibrillators, laser systems and pulsed power equipment rely on specialized high energy density capacitors for rapid burst power output. Supercapacitors provide large capacitance for energy harvesting applications.
PCB Capacitors vs. Leaded Capacitors
PCB capacitors eliminate the leads of traditional capacitors, but there are still some applications where leaded capacitors excel:
High Voltage Operation
Leaded power film capacitors and mica compression trimmer capacitors are available for very high AC and pulse voltage operation well beyond the rating of SMT caps.
Circuit Tuning and Adjustments
Variable air or vacuum trimmer capacitors allow adjustable tuning of resonant tank circuits. Multi-sectional variable capacitors provide continuous range adjustment.
Through-Hole Mounting
Through-hole axial and radial leaded electrolytic capacitors continue to be used on low cost consumer electronics with standard printed circuit boards.
Very High Capacitance Values
Specialized supercapacitor modules providing 100s to 1000s of farads are constructed from larger cells that require mounting hardware and wiring.
Rugged Environments
Larger potted or metal encased power film and mica capacitors withstand shock, vibration, moisture, and temperature extremes better than SMT versions.
Cost Savings
Some larger case size leaded capacitors remain more economical than smaller PCB capacitors for very high voltage, temperature range, or wattage ratings.
Summary
PCB capacitors offer space, performance, and reliability improvements over their leaded predecessors. The evolution of surface mount packaging has allowed high capacitance multilayer ceramics, plastic film, mica, and tantalum capacitors to be integrated directly onto printed circuit boards rather than use traditional axial and radial leaded components. While leaded capacitors still have a place for specialized high voltage, power, and tunable applications, PCB capacitors dominate modern electronic circuit designs with their small size, automation-friendly packages, and stable electrical characteristics. Continuing advances in materials and manufacturing techniques will lead to further integration and miniaturization of PCB capacitor technology.
Frequently Asked Questions
What are the different types of PCB capacitors?
The most common types of PCB capacitors are:
- Multilayer ceramic capacitors (MLCCs) – Made from alternating layers of ceramic dielectric and metal electrode. Most widely used due to small size and low cost.
- Plastic film capacitors – Uses thin plastic dielectric like polypropylene film. Known for high stability and reliability.
- Mica capacitors – Constructed from sheets of mica for low losses at high frequencies.
- Tantalum capacitors – Offer high capacitance values but limited voltage range and polarity sensitive.
- Aluminum electrolytic capacitors – Provide high capacitance in compact SMT versions but have higher leakage than other types.
How does capacitance value affect selection?
Higher capacitance allows more charge to be stored for a given voltage. Key factors:
- For bypass/decoupling small values like 0.1 uF are used to filter high frequencies.
- Coupling and DC blocking depends on the impedance needed. May use 1 uF to 1000s uF range.
- Timing circuits depend on the RC time constant needed and are often in the nF range.
- Tuned circuits require tight tolerance so capacitance does not shift frequency.
What is the difference between dielectric absorption and ESR?
Dielectric absorption is an inefficiency of the capacitor where a small amount of charge gets soaked into the dielectric when discharged. This can affect accuracy in timing and sample-hold circuits.
ESR is the equivalent series resistance of the capacitor. This causes power losses due to current flow through the capacitor electrodes and terminations. Higher ESR degrades high frequency filtering performance.
How are PCB capacitors labeled?
PCB capacitors use a coded label to denote capacitance value and tolerance. The first two digits are the significant value and the third digit the multiplier. Code like “473” represents “47 x 10^3” pF = 47,000 pF or 47 nF. A letter tolerance like “K” = +/- 10% may follow.
Why is voltage rating important for capacitor selection?
The voltage rating must exceed the working voltage seen by the capacitor to prevent dielectric breakdown and failure. Higher voltage ratings allow for margin and transient spikes. Ceramic caps have lower ratings up to a few hundred volts while film caps are available in many hundreds to thousands of volts.
Leave a Reply