Introduction to BGA Soldering
Ball Grid Array (BGA) soldering is a critical process in Surface Mount Technology (SMT) assembly that involves attaching a BGA component to a Printed Circuit Board (PCB). BGA components have a grid of solder balls underneath them, which are used to make electrical connections with the PCB. The soldering process requires precision and accuracy to ensure a reliable and robust connection between the BGA component and the PCB.
Importance of BGA Soldering in SMT Assembly
BGA soldering is essential in SMT assembly because it enables the use of high-density components with a large number of interconnects. BGA packages offer several advantages over other SMT packages, such as:
- Reduced package size
- Improved electrical performance
- Better thermal management
- Higher interconnect density
However, BGA soldering is also more challenging than other SMT soldering processes due to the hidden solder joints and the need for precise alignment and temperature control.
9 Ways to Get BGA Soldering on PCB in SMT Assembly
1. Use the Right Solder Paste
The first step in achieving reliable BGA soldering is to use the right solder paste. The solder paste should have the following properties:
- Appropriate melting temperature
- Good wetting ability
- Low voiding
- Adequate tack strength
The solder paste should also be compatible with the BGA component and the PCB material. Lead-free solder pastes are commonly used in BGA soldering due to environmental regulations.
2. Ensure Proper Alignment
Proper alignment between the BGA component and the PCB is critical for achieving a reliable solder joint. Misalignment can lead to open or short circuits, which can cause the device to malfunction. To ensure proper alignment, follow these steps:
- Use a stencil with the correct aperture size and shape for the BGA pads.
- Align the stencil with the PCB using fiducial marks or optical alignment systems.
- Place the BGA component on the PCB using a pick-and-place machine with high accuracy.
- Verify the alignment using an automated optical inspection (AOI) system.
3. Control the Reflow Profile
The reflow profile is a critical factor in BGA soldering. It determines the temperature and time profile of the soldering process. A proper reflow profile should have the following characteristics:
- Gradual ramp-up to avoid thermal shock
- Adequate soak time to activate the flux and remove volatiles
- Peak temperature high enough to melt the solder but not too high to cause damage
- Gradual cool-down to avoid thermal stress
The reflow profile should be optimized for the specific BGA component and PCB material. It is also important to monitor the reflow process using thermocouples or profiling systems to ensure consistency.
4. Use Nitrogen Reflow
Nitrogen reflow is a technique that involves using nitrogen gas to displace oxygen during the reflow process. This helps to reduce oxidation and improve the wetting of the solder. Nitrogen reflow can also reduce voids in the solder joints, which can improve reliability.
To implement nitrogen reflow, the reflow oven should be equipped with a nitrogen injection system. The nitrogen flow rate and purity should be controlled to achieve the desired oxygen level in the oven.
5. Implement Solder Preforms
Solder preforms are pre-shaped pieces of solder that are placed between the BGA component and the PCB. They help to control the amount of solder and ensure consistent solder joint height. Solder preforms can also reduce voids and improve the mechanical strength of the solder joint.
To use solder preforms, follow these steps:
- Select the appropriate preform size and shape for the BGA component.
- Place the preform on the PCB using a pick-and-place machine or manual placement.
- Align the BGA component with the preform and place it on top.
- Reflow the assembly using the optimized profile.
6. Use Underfill Material
Underfill material is an epoxy-based compound that is applied between the BGA component and the PCB after soldering. It helps to distribute the stress and strain caused by thermal expansion mismatches between the component and the PCB. Underfill can also improve the mechanical strength and reliability of the solder joint.
To apply underfill, follow these steps:
- Clean the PCB and BGA component to remove flux residues and contaminants.
- Dispense the underfill material along the edge of the BGA component using a dispenser.
- Allow the underfill to flow under the component by capillary action.
- Cure the underfill using heat or UV light.
7. Implement X-Ray Inspection
X-ray inspection is a non-destructive testing method that allows the visualization of hidden solder joints under the BGA component. It can detect defects such as voids, cracks, and bridges that are not visible by optical inspection.
To implement X-ray inspection, follow these steps:
- Select an X-ray system with sufficient resolution and magnification for the BGA component.
- Set up the inspection parameters, such as voltage, current, and exposure time.
- Place the PCB Assembly in the X-ray chamber and align it with the detector.
- Acquire the X-ray image and analyze it for defects.
8. Use Rework and Repair Techniques
Despite best efforts, BGA soldering defects can still occur. In such cases, rework and repair techniques can be used to fix the problem. Some common rework and repair techniques include:
- Hot air rework: Using a focused hot air nozzle to melt the solder and remove the BGA component.
- Solder paste dispensing: Applying fresh solder paste to the PCB pads before replacing the BGA component.
- Solder ball replacement: Removing damaged solder balls and replacing them with new ones.
Rework and repair should be performed by skilled technicians using specialized tools and equipment.
9. Implement Process Control and Monitoring
To ensure consistent and reliable BGA soldering, it is important to implement process control and monitoring. This involves:
- Defining and documenting the process parameters and steps.
- Monitoring the process variables, such as temperature, time, and humidity.
- Performing regular maintenance and calibration of the equipment.
- Conducting statistical process control (SPC) to identify and correct process deviations.
Process control and monitoring help to reduce variability and improve the quality of the BGA solder joints.
Conclusion
BGA soldering is a critical process in SMT assembly that requires precision and accuracy. By following the 9 ways outlined in this article, you can achieve reliable and robust BGA solder joints. These include using the right solder paste, ensuring proper alignment, controlling the reflow profile, using nitrogen reflow, implementing solder preforms, using underfill material, implementing X-ray inspection, using rework and repair techniques, and implementing process control and monitoring.
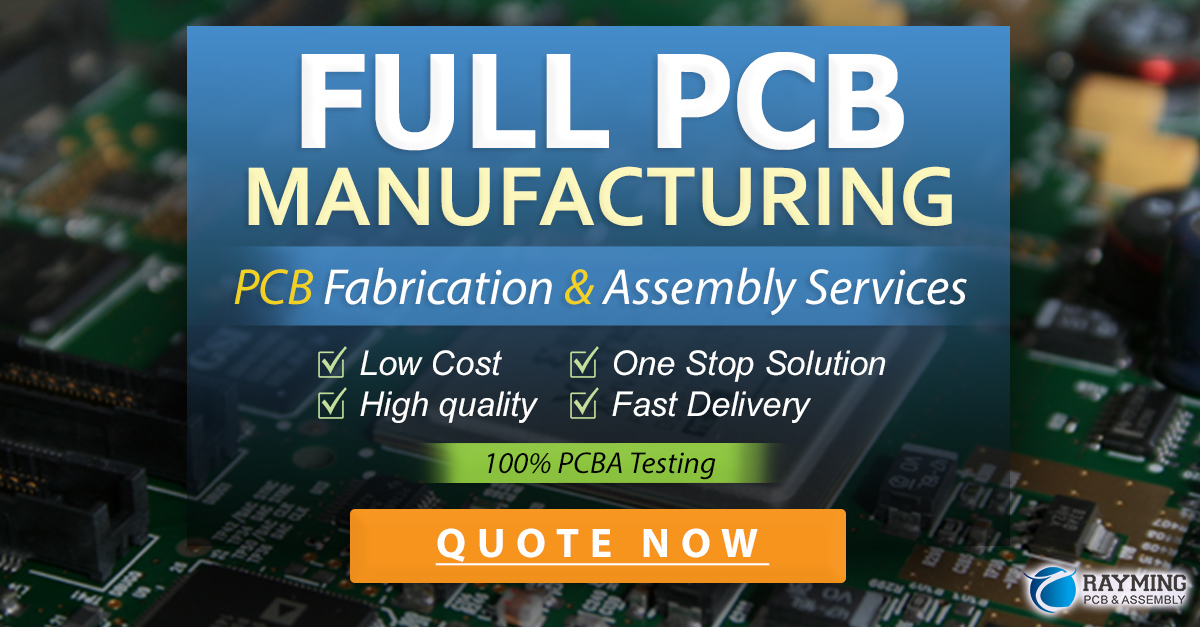
Frequently Asked Questions (FAQ)
1. What is BGA soldering?
BGA soldering is a process of attaching a BGA component to a PCB using solder balls. It involves applying solder paste to the PCB pads, placing the BGA component on top, and reflowing the assembly to melt the solder and form the solder joints.
2. Why is BGA soldering challenging?
BGA soldering is challenging because the solder joints are hidden under the component and cannot be visually inspected. It also requires precise alignment and temperature control to ensure reliable and consistent solder joints.
3. What are the advantages of using solder preforms in BGA soldering?
Solder preforms help to control the amount of solder and ensure consistent solder joint height. They can also reduce voids and improve the mechanical strength of the solder joint.
4. What is underfill material and why is it used in BGA soldering?
Underfill material is an epoxy-based compound that is applied between the BGA component and the PCB after soldering. It helps to distribute the stress and strain caused by thermal expansion mismatches between the component and the PCB, improving the mechanical strength and reliability of the solder joint.
5. How can process control and monitoring improve BGA soldering quality?
Process control and monitoring help to reduce variability and improve the quality of the BGA solder joints. This involves defining and documenting the process parameters and steps, monitoring the process variables, performing regular maintenance and calibration of the equipment, and conducting statistical process control (SPC) to identify and correct process deviations.
Technique | Advantage | Disadvantage |
---|---|---|
Solder Paste | Enables precise solder deposition | Requires stencil and printing process |
Nitrogen Reflow | Reduces oxidation and improves wetting | Requires nitrogen injection system |
Solder Preforms | Controls solder amount and joint height | Adds an extra step in the assembly process |
Underfill Material | Improves mechanical strength and reliability | Requires additional dispense and cure process |
X-Ray Inspection | Detects hidden defects under the component | Requires specialized equipment and skilled operators |
Leave a Reply