1. Solder Bridging
Solder bridging occurs when excess solder creates an unintended connection between two or more solder pads or traces on a PCB. This can lead to short circuits and malfunctions in the electronic device.
Causes of Solder Bridging
- Incorrect Solder Paste application
- Improper solder reflow process
- Poor component placement
- Inadequate PCB design
Solutions for Solder Bridging
- Optimizing solder paste application:
- Use stencils with appropriate aperture sizes
- Ensure proper solder paste viscosity and consistency
-
Regularly maintain and clean solder paste application equipment
-
Improving solder reflow process:
- Adjust reflow oven temperature profile
- Ensure proper PCB preheat and cooling rates
-
Maintain appropriate conveyor speed
-
Enhancing component placement accuracy:
- Use pick-and-place machines with high precision
- Implement vision systems for component alignment
-
Regularly calibrate and maintain placement equipment
-
Optimizing PCB design:
- Increase spacing between solder pads and traces
- Use solder mask to prevent bridging
- Implement design for manufacturing (DFM) guidelines
2. Dry Solder Joints
Dry solder joints, also known as cold solder joints, occur when the solder fails to properly bond with the component leads or PCB pads. This results in a weak and unreliable connection that can cause intermittent failures or complete loss of electrical continuity.
Causes of Dry Solder Joints
- Insufficient solder application
- Improper solder reflow temperature
- Contaminated or oxidized component leads or PCB pads
- Inadequate flux activity
Solutions for Dry Solder Joints
- Ensuring sufficient solder application:
- Optimize solder paste printing process
- Use appropriate solder wire diameter for manual soldering
-
Regularly inspect and maintain solder application equipment
-
Maintaining proper solder reflow temperature:
- Set reflow oven temperature according to solder paste specifications
- Monitor and control the temperature profile during reflow
-
Regularly calibrate and maintain reflow ovens
-
Cleaning and preventing contamination:
- Thoroughly clean component leads and PCB pads before soldering
- Use appropriate cleaning agents and methods
-
Store components and PCBs in a clean, dry environment
-
Selecting appropriate flux:
- Choose flux with adequate activity for the specific application
- Ensure compatibility between flux and solder paste or wire
- Regularly inspect and replace flux as needed
3. Tombstoning
Tombstoning, also known as drawbridging, is a phenomenon where small surface-mount components, such as chip resistors or capacitors, stand up on one end during the solder reflow process. This can lead to an open circuit or intermittent connection.
Causes of Tombstoning
- Uneven heating of component pads
- Misalignment of component placement
- Incorrect solder paste volume or composition
- Inadequate PCB pad design
Solutions for Tombstoning
- Optimizing component pad design:
- Ensure equal thermal mass on both component pads
- Use symmetrical pad shapes and sizes
-
Implement proper pad spacing and orientation
-
Improving component placement accuracy:
- Use pick-and-place machines with high precision
- Implement vision systems for component alignment
-
Regularly calibrate and maintain placement equipment
-
Adjusting solder paste application:
- Use appropriate solder paste volume and composition
- Ensure even solder paste distribution on pads
-
Optimize stencil design and printing process
-
Controlling reflow temperature profile:
- Ensure even heating of the PCB during reflow
- Adjust reflow oven settings to minimize temperature gradients
- Regularly monitor and maintain reflow ovens
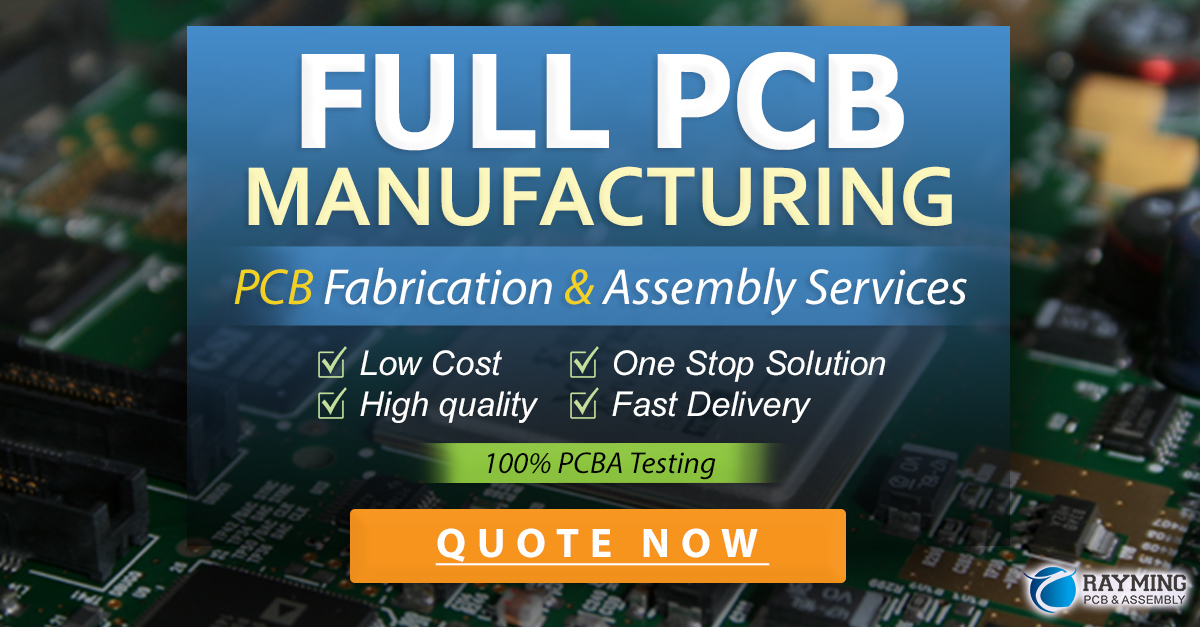
4. Copper Trace Damage
Copper trace damage can occur during PCB fabrication, assembly, or handling processes. Damaged traces can lead to open circuits, increased resistance, or complete failure of the affected circuit.
Causes of Copper Trace Damage
- Mechanical stress or impact
- Improper handling or storage
- Exposure to harsh chemicals or environments
- Manufacturing defects
Solutions for Copper Trace Damage
- Implementing proper handling and storage procedures:
- Use ESD-safe packaging and handling materials
- Store PCBs in a clean, dry, and temperature-controlled environment
-
Train personnel on correct handling techniques
-
Enhancing PCB design for durability:
- Use appropriate trace widths and spacing
- Implement strain relief features for connectors and components
-
Apply conformal coating or other protective measures
-
Optimizing manufacturing processes:
- Regularly inspect and maintain fabrication equipment
- Implement quality control measures and testing procedures
-
Use appropriate etching and plating techniques
-
Selecting suitable materials and finishes:
- Choose high-quality Copper Foils and substrates
- Apply appropriate surface finishes for protection
- Consider using reinforced or Flexible PCB materials when necessary
5. Solder Mask Issues
Solder mask is a protective coating applied to the PCB surface to prevent solder bridging and provide insulation between conductors. Issues with solder mask can lead to short circuits, reduced insulation resistance, or difficulty in soldering components.
Causes of Solder Mask Issues
- Improper solder mask application or curing
- Contamination or damage during handling
- Incompatible solder mask material
- Incorrect solder mask aperture size or registration
Solutions for Solder Mask Issues
- Optimizing solder mask application process:
- Use appropriate solder mask material and thickness
- Ensure proper curing temperature and time
-
Regularly inspect and maintain solder mask application equipment
-
Improving handling and storage procedures:
- Use clean, lint-free gloves when handling PCBs
- Store PCBs in a clean, dry, and temperature-controlled environment
-
Avoid exposure to harsh chemicals or UV light
-
Selecting compatible solder mask materials:
- Choose solder mask with good adhesion and chemical resistance
- Ensure compatibility with the PCB substrate and surface finish
-
Consider using liquid photoimageable solder mask for high precision
-
Verifying solder mask aperture size and registration:
- Use appropriate aperture sizes for component pads and vias
- Ensure proper alignment and registration of solder mask to copper features
- Implement automated optical inspection (AOI) for quality control
6. Plated Through-Hole (PTH) Defects
Plated through-holes (PTHs) are used to create electrical connections between different layers of a PCB. Defects in PTHs can cause open circuits, intermittent connections, or reliability issues.
Causes of PTH Defects
- Inadequate plating thickness or coverage
- Voids or inclusions in the plating
- Drill wander or misalignment
- Contamination or residues in the holes
Solutions for PTH Defects
- Optimizing the plating process:
- Use appropriate plating chemistry and parameters
- Ensure proper hole cleaning and activation before plating
-
Regularly monitor and maintain plating baths and equipment
-
Improving drilling accuracy:
- Use high-quality drill bits and machines
- Implement drill stack-up and registration techniques
-
Regularly inspect and replace worn or damaged drill bits
-
Enhancing hole cleaning and preparation:
- Use effective hole cleaning methods, such as plasma or chemical etching
- Ensure complete removal of drilling residues and contaminants
-
Apply appropriate pre-treatment processes before plating
-
Implementing quality control measures:
- Perform cross-sectional analysis and microscopic inspection of PTHs
- Use automated inspection systems for hole quality assessment
- Establish and monitor process control parameters and limits
7. Bow and Twist
Bow and twist are dimensional distortions that can occur in PCBs due to uneven stress distribution or material properties. These distortions can cause assembly issues, poor component fit, or reduced reliability.
Causes of Bow and Twist
- Unbalanced copper distribution across layers
- Improper lamination process or parameters
- Mismatch in material properties or thermal expansion
- Inadequate PCB design or stack-up
Solutions for Bow and Twist
- Balancing copper distribution:
- Implement copper thieving or balancing techniques
- Distribute copper evenly across PCB Layers
-
Use symmetrical stack-up and design when possible
-
Optimizing lamination process:
- Use appropriate lamination pressure, temperature, and time
- Ensure proper conditioning and staging of PCB layers before lamination
-
Regularly maintain and calibrate lamination equipment
-
Selecting compatible materials:
- Choose PCB materials with similar thermal expansion coefficients
- Use high-quality and consistent materials from reliable suppliers
-
Consider using specialized materials for demanding applications
-
Enhancing PCB design and stack-up:
- Minimize large, unsupported copper areas
- Use symmetrical stack-up and balanced copper distribution
- Implement stress-relief features, such as slots or cutouts, when necessary
8. Electrostatic Discharge (ESD) Damage
Electrostatic discharge (ESD) can cause damage to sensitive electronic components on PCBs, leading to latent defects, reduced performance, or complete failure.
Causes of ESD Damage
- Improper handling or storage of PCBs and components
- Insufficient ESD protection measures in the manufacturing environment
- Lack of proper grounding and dissipative materials
- Triboelectric charging during handling or transport
Solutions for ESD Damage
- Implementing ESD protection measures:
- Use ESD-safe workstations, tools, and equipment
- Provide ESD training to personnel handling PCBs and components
-
Regularly test and maintain ESD protection equipment
-
Ensuring proper grounding and dissipation:
- Use grounded, dissipative mats and flooring in the work area
- Wear ESD-safe clothing, gloves, and wrist straps
-
Implement ionization systems to neutralize static charges
-
Optimizing PCB design for ESD protection:
- Include ESD protection devices, such as transient voltage suppressors (TVS) or varistors
- Use guard rings or shielding techniques for sensitive circuits
-
Consider conformal coating or other protective measures
-
Enhancing packaging and transport procedures:
- Use ESD-safe packaging materials, such as static shielding bags or containers
- Label ESD-sensitive items and handle them appropriately
- Minimize manual handling and transfer of PCBs and components
9. Delamination and Blistering
Delamination and blistering occur when the layers of a PCB separate or form localized swelling due to various factors. These defects can compromise the structural integrity and electrical performance of the PCB.
Causes of Delamination and Blistering
- Improper lamination process or parameters
- Moisture absorption or outgassing during assembly or operation
- Thermal stress or cycling
- Incompatible or low-quality materials
Solutions for Delamination and Blistering
- Optimizing lamination process:
- Use appropriate lamination pressure, temperature, and time
- Ensure proper conditioning and drying of PCB layers before lamination
-
Regularly maintain and calibrate lamination equipment
-
Minimizing moisture absorption:
- Use moisture-resistant or low-absorption PCB materials
- Bake PCBs before assembly to remove absorbed moisture
-
Implement controlled storage and handling conditions
-
Managing thermal stress:
- Use PCB materials with similar thermal expansion coefficients
- Implement stress-relief features, such as underfill or conformal coating
-
Optimize assembly and operating temperature profiles
-
Selecting high-quality materials:
- Choose PCB materials from reliable suppliers with consistent quality
- Verify material compatibility and performance through testing and qualification
- Consider using specialized materials for demanding environments or applications
Frequently Asked Questions (FAQ)
- What are the most common causes of PCB failure?
Some of the most common causes of PCB failure include: - Manufacturing defects, such as solder bridging or dry joints
- Environmental factors, such as moisture, temperature, or vibration
- Improper handling or storage, leading to ESD damage or contamination
-
Design issues, such as inadequate trace sizing or component placement
-
How can I prevent solder bridging on my PCBs?
To prevent solder bridging, you can: - Optimize solder paste application using appropriate stencils and parameters
- Improve component placement accuracy with pick-and-place machines and vision systems
- Adjust reflow oven temperature profiles and conveyor speed
-
Implement Design for Manufacturing (DFM) guidelines in your PCB layout
-
What is the best way to store and handle PCBs to avoid damage?
To properly store and handle PCBs: - Use ESD-safe packaging materials and handling procedures
- Store PCBs in a clean, dry, and temperature-controlled environment
- Avoid exposure to moisture, dust, or chemical contaminants
-
Train personnel on correct handling techniques and ESD precautions
-
How can I identify and troubleshoot dry solder joints?
To identify and troubleshoot dry solder joints: - Visually inspect solder joints for dull, grainy, or incomplete appearance
- Use a multimeter or continuity tester to check for intermittent or open connections
- Reflow or rework the affected solder joints using appropriate techniques and tools
-
Analyze the root cause of the dry joint, such as insufficient solder, contamination, or improper reflow
-
What are some best practices for designing reliable and manufacturable PCBs?
Some best practices for designing reliable and manufacturable PCBs include: - Following Design for Manufacturing (DFM) and Design for Assembly (DFA) guidelines
- Using appropriate trace widths, spacing, and via sizes for the intended application
- Implementing ESD protection measures and selecting compatible materials
- Optimizing component placement and orientation for ease of assembly and reliability
- Performing thorough design reviews, simulations, and prototyping before mass production
By understanding the common problems associated with PCBs and implementing the appropriate solutions and best practices, you can enhance the reliability, performance, and longevity of your electronic devices. Regular inspection, maintenance, and adherence to industry standards and guidelines can further minimize the risk of PCB failures and ensure the success of your projects.
Problem | Causes | Solutions |
---|---|---|
Solder Bridging | – Incorrect solder paste application – Improper solder reflow process – Poor component placement – Inadequate PCB design |
– Optimize solder paste application – Improve solder reflow process – Enhance component placement accuracy – Optimize PCB design |
Dry Solder Joints | – Insufficient solder application – Improper solder reflow temperature – Contaminated or oxidized component leads or PCB pads – Inadequate flux activity |
– Ensure sufficient solder application – Maintain proper solder reflow temperature – Clean and prevent contamination – Select appropriate flux |
Tombstoning | – Uneven heating of component pads – Misalignment of component placement – Incorrect solder paste volume or composition – Inadequate PCB pad design |
– Optimize component pad design – Improve component placement accuracy – Adjust solder paste application – Control reflow temperature profile |
Copper Trace Damage | – Mechanical stress or impact – Improper handling or storage – Exposure to harsh chemicals or environments – Manufacturing defects |
– Implement proper handling and storage procedures – Enhance PCB design for durability – Optimize manufacturing processes – Select suitable materials and finishes |
Solder Mask Issues | – Improper solder mask application or curing – Contamination or damage during handling – Incompatible solder mask material – Incorrect solder mask aperture size or registration |
– Optimize solder mask application process – Improve handling and storage procedures – Select compatible solder mask materials – Verify solder mask aperture size and registration |
PTH Defects | – Inadequate plating thickness or coverage – Voids or inclusions in the plating – |
Leave a Reply