Introduction to Rogers PCB and its Performance Benefits
Rogers PCB, named after the Rogers Corporation, is a specialized type of printed circuit board known for its exceptional performance characteristics. Unlike traditional FR-4 PCBs, Rogers PCBs utilize advanced dielectric materials that offer superior electrical properties, making them ideal for high-frequency and high-speed applications. These materials, such as Rogers RO4000, RO3000, and RT/duroid series, exhibit low dielectric constant (Dk), low dissipation factor (Df), and stable performance over a wide range of frequencies and temperatures.
The unique properties of Rogers PCBs enable them to deliver excellent signal integrity, low loss, and reduced electromagnetic interference (EMI), which are critical factors in designing performance-driven electronic systems. Industries such as telecommunications, aerospace, defense, and automotive rely on Rogers PCBs to achieve optimal performance in demanding environments.
In this article, we will explore eight technical tips to help you design performance-driven Rogers PCBs, ensuring that your electronic designs meet the highest standards of reliability, speed, and efficiency.
Tip 1: Choose the Right Rogers Material for Your Application
Understanding the Properties of Rogers Materials
Rogers Corporation offers a wide range of dielectric materials, each with unique properties tailored to specific applications. When designing a Rogers PCB, it is crucial to select the appropriate material based on your project requirements. Consider factors such as the operating frequency, dielectric constant, dissipation factor, thermal conductivity, and mechanical properties.
Some popular Rogers materials include:
Material | Dielectric Constant (Dk) | Dissipation Factor (Df) | Applications |
---|---|---|---|
RO4003C | 3.38 @ 10 GHz | 0.0027 @ 10 GHz | High-frequency, low-loss applications |
RO3003 | 3.00 @ 10 GHz | 0.0010 @ 10 GHz | High-frequency, low-loss, low-Dk applications |
RT/duroid 5870 | 2.33 @ 10 GHz | 0.0012 @ 10 GHz | Microwave and millimeter-wave applications |
Matching the Material to Your Design Requirements
When selecting a Rogers material, consider the following guidelines:
- High-frequency applications (>1 GHz) benefit from low-Dk materials like RO3003 or RT/duroid 5870, which minimize signal delays and reduce conductor losses.
- Low-loss applications require materials with low dissipation factors, such as RO4003C or RO3003, to minimize signal attenuation and maintain signal integrity.
- Thermally demanding applications may require materials with higher thermal conductivity, such as RO4350B or RO4360G2, to efficiently dissipate heat and maintain stable performance.
By choosing the right Rogers material for your specific application, you can optimize the performance of your PCB and ensure reliable operation in demanding environments.
Tip 2: Optimize Trace Geometry for Impedance Control
Understanding Characteristic Impedance
Maintaining proper characteristic impedance is essential for minimizing signal reflections and ensuring optimal signal integrity in high-speed designs. The characteristic impedance of a trace is determined by its geometry (width and thickness) and the dielectric properties of the surrounding material.
In Rogers PCBs, the dielectric constant (Dk) of the material plays a crucial role in determining the characteristic impedance. Lower Dk values result in wider traces for a given impedance, which can be advantageous for manufacturing and signal integrity.
Calculating Trace Dimensions
To achieve the desired characteristic impedance, use impedance calculators or simulation tools to determine the appropriate trace width and thickness. These tools take into account the dielectric properties of the Rogers material, the copper thickness, and the desired impedance value.
For example, to achieve a 50Ω characteristic impedance on a Rogers RO4003C material with a dielectric constant of 3.38 and a thickness of 0.008″ (0.20 mm), the trace width would be approximately 0.024″ (0.61 mm) for a 1 oz (35 μm) copper thickness.
Maintaining Consistent Impedance
To maintain consistent impedance throughout your PCB design, follow these guidelines:
- Keep trace widths and thicknesses uniform for each impedance-controlled signal layer.
- Avoid abrupt changes in trace geometry, such as sharp bends or discontinuities, which can cause impedance mismatches and signal reflections.
- Use ground planes and proper grounding techniques to provide a stable reference for impedance-controlled traces.
- Consider the effects of via transitions on impedance and minimize their impact by using appropriate via sizes and anti-pad dimensions.
By optimizing trace geometry and maintaining consistent impedance, you can minimize signal integrity issues and ensure reliable high-speed performance in your Rogers PCB design.
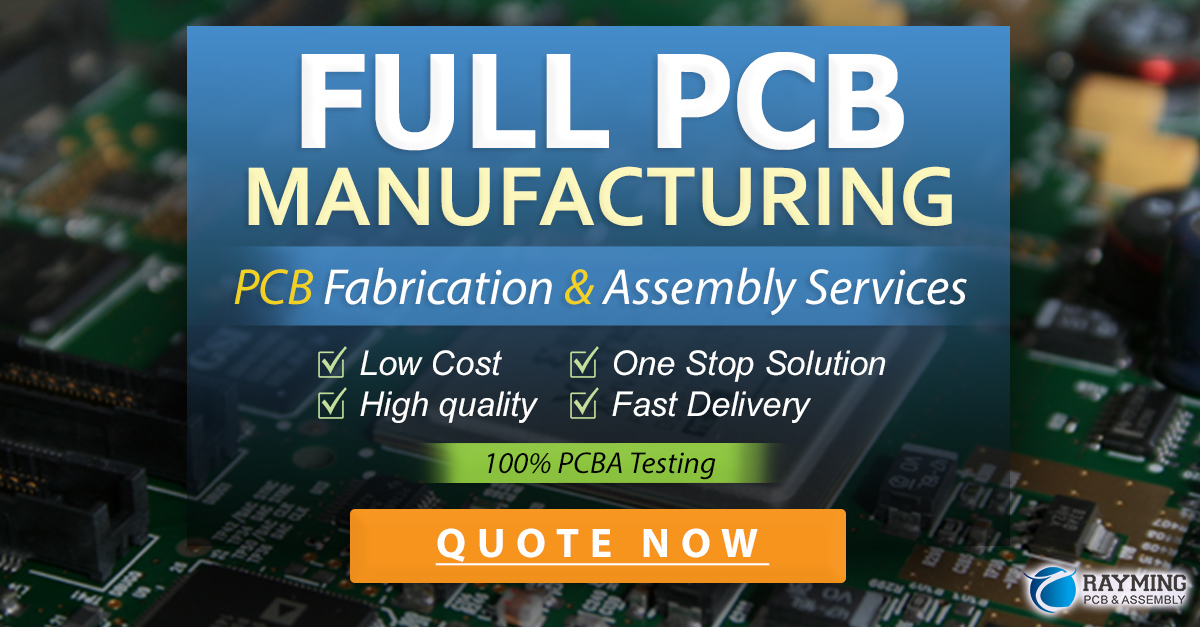
Tip 3: Minimize Losses with Proper Copper Surface Treatment
Understanding Copper Losses
In high-frequency applications, copper losses can significantly impact signal integrity and overall system performance. Copper losses occur due to the skin effect, where high-frequency currents tend to flow on the surface of the conductor rather than uniformly throughout its cross-section. This phenomenon increases the effective resistance of the conductor, leading to higher losses and signal attenuation.
Choosing the Right Copper Surface Treatment
To minimize copper losses in Rogers PCBs, consider using advanced copper surface treatments that enhance conductivity and reduce surface roughness. Some popular surface treatments include:
- Electroless Nickel Immersion Gold (ENIG): ENIG provides a smooth, solderable surface with excellent corrosion resistance. The nickel layer acts as a barrier, while the gold layer protects against oxidation.
- Immersion Silver (IAg): IAg offers a cost-effective alternative to ENIG, providing good solderability and conductivity. However, it may be more susceptible to oxidation over time.
- Rolled Annealed (RA) Copper: RA copper undergoes a rolling and annealing process that results in a smooth, low-profile surface finish. This treatment minimizes skin effect losses and improves high-frequency performance.
Optimizing Copper Thickness
In addition to surface treatments, the thickness of the copper layer can also impact losses. Thicker copper layers provide lower resistance and can help reduce losses, especially in high-current applications. However, thicker copper may also increase manufacturing costs and affect impedance control.
Consider the trade-offs between loss reduction and other design factors when selecting the appropriate copper thickness for your Rogers PCB.
Tip 4: Implement Proper Grounding and Shielding Techniques
The Importance of Proper Grounding
Proper grounding is essential for maintaining signal integrity, reducing electromagnetic interference (EMI), and ensuring the overall stability of your Rogers PCB design. A well-designed grounding system provides a low-impedance return path for high-frequency currents and minimizes ground bounce and voltage fluctuations.
To implement effective grounding techniques:
- Use dedicated ground planes for each signal layer to provide a stable reference and minimize ground loop areas.
- Strategically place ground vias near signal vias to provide a low-impedance return path and minimize inductance.
- Use ground pours or gridded ground patterns to create a low-impedance ground structure and improve shielding effectiveness.
- Implement split ground planes or isolated ground regions for sensitive analog and digital sections to minimize noise coupling.
Shielding Techniques for EMI Reduction
In addition to proper grounding, shielding techniques can help reduce EMI and improve the electromagnetic compatibility (EMC) of your Rogers PCB design. Some effective shielding techniques include:
- Using conductive enclosures or shield cans to isolate sensitive components or sections of the PCB.
- Implementing guard traces or co-planar waveguides to provide additional shielding for critical signals.
- Applying conductive coatings or conductive gaskets to improve shielding effectiveness at enclosure seams and openings.
- Utilizing shielded connectors and cables to minimize EMI coupling and radiated emissions.
By implementing proper grounding and shielding techniques, you can significantly improve the signal integrity and EMC performance of your Rogers PCB design.
Tip 5: Optimize Via Design for Signal Integrity
The Impact of Vias on Signal Integrity
Vias are essential for interconnecting different layers in a multi-layer Rogers PCB, but they can also introduce discontinuities and affect signal integrity. The transition through a via can cause impedance mismatches, reflections, and increased insertion loss, especially at high frequencies.
To minimize the impact of vias on signal integrity:
- Use appropriate via sizes and anti-pad dimensions to maintain consistent impedance and minimize capacitive discontinuities.
- Implement via shielding techniques, such as ground vias or coaxial vias, to provide a continuous return path and reduce coupling between adjacent vias.
- Minimize the number of vias in high-speed signal paths to reduce the overall discontinuity and insertion loss.
- Consider the use of blind or buried vias to reduce the length of the via transition and improve signal integrity.
Via Stitching for Improved Power Integrity
In addition to signal integrity considerations, vias also play a crucial role in power distribution and power integrity. Via stitching is a technique that involves placing multiple vias in close proximity to create a low-impedance path for power distribution and reduce voltage drop.
To implement effective via stitching:
- Place power and ground vias in a regular pattern, such as a grid or checkerboard arrangement, to minimize the distance between vias and reduce inductance.
- Use multiple smaller vias instead of a single large via to improve current handling capacity and reduce the risk of thermal issues.
- Optimize the via pitch and spacing based on the power requirements and the target impedance of the power distribution network.
By optimizing via design for both signal and power integrity, you can ensure reliable performance and minimize the impact of vias on your Rogers PCB design.
Tip 6: Consider Thermal Management Strategies
The Importance of Thermal Management
Effective thermal management is crucial for maintaining the performance and reliability of your Rogers PCB design. High-frequency and high-power applications generate significant amounts of heat that must be dissipated to prevent component degradation and ensure long-term reliability.
Rogers materials, such as RO4000 and RO3000 series, offer good thermal conductivity compared to traditional FR-4 materials, which helps in heat dissipation. However, additional thermal management strategies may be necessary to ensure optimal performance.
Thermal Management Techniques
To effectively manage heat in your Rogers PCB design, consider the following techniques:
- Use thermal vias or thermal pads to provide a low-resistance path for heat transfer from components to the PCB substrate or heat sinks.
- Implement copper pours or solid copper planes on outer layers to spread heat and improve thermal conductivity.
- Utilize heat sinks or thermal interface materials (TIMs) to enhance heat dissipation from high-power components.
- Consider the use of thermal management materials, such as thermally conductive adhesives or thermal gap pads, to improve heat transfer between components and the PCB.
- Optimize component placement and layout to minimize thermal coupling and ensure adequate airflow for convective cooling.
Thermal Simulation and Analysis
To validate your thermal management strategies and ensure optimal performance, consider conducting thermal simulations and analyses during the design phase. Thermal simulation tools can help you predict temperature distributions, identify hot spots, and optimize your design for efficient heat dissipation.
By incorporating appropriate thermal management techniques and conducting thorough thermal analyses, you can ensure that your Rogers PCB design operates within safe temperature limits and maintains reliable performance over its intended lifetime.
Tip 7: Implement Robust Power Distribution Networks
The Importance of Power Distribution Networks (PDNs)
A robust power distribution network (PDN) is essential for ensuring clean, stable, and reliable power delivery to all components in your Rogers PCB design. A well-designed PDN minimizes voltage fluctuations, reduces noise coupling, and maintains power integrity across the entire frequency spectrum.
In high-frequency and high-speed designs, the PDN must be carefully designed to provide low impedance and sufficient current handling capacity to meet the power requirements of the system.
Designing Effective PDNs
To design an effective PDN for your Rogers PCB, consider the following guidelines:
- Use appropriate power and ground plane arrangements, such as split planes or multiplane structures, to provide a low-impedance power distribution path and minimize voltage fluctuations.
- Implement decoupling capacitors strategically near power pins of active components to provide local energy storage and reduce high-frequency noise.
- Use a combination of bulk, ceramic, and low-ESL (equivalent series inductance) capacitors to cover a wide frequency range and ensure effective decoupling.
- Optimize the placement and routing of power traces to minimize inductance and ensure uniform current distribution.
- Consider the use of power integrity simulation tools to analyze the impedance profile of your PDN and identify potential resonances or instabilities.
Power Plane Capacitance and Impedance Control
In Rogers PCBs, the dielectric properties of the substrate material can significantly impact the power plane capacitance and impedance characteristics of the PDN. The high dielectric constant and low dissipation factor of Rogers materials can provide additional capacitance between power and ground planes, which can be beneficial for decoupling and noise reduction.
However, it is important to consider the impact of power plane capacitance on impedance control and signal integrity. The increased capacitance may require adjustments to the PCB stackup and trace geometry to maintain the desired characteristic impedance.
By implementing a robust PDN design and considering the specific properties of Rogers materials, you can ensure reliable power delivery and maintain optimal performance in your high-frequency and high-speed applications.
Tip 8: Validate Your Design with Simulation and Testing
The Importance of Simulation and Testing
Validating your Rogers PCB design through simulation and testing is crucial for identifying and addressing potential issues before fabrication and assembly. Simulation tools can help you analyze signal integrity, power integrity, thermal performance, and electromagnetic compatibility (EMC) of your design, allowing you to make necessary adjustments and optimizations.
Testing your fabricated Rogers PCB Prototype is equally important to verify its performance against design specifications and ensure its reliability in real-world operating conditions.
Signal Integrity Simulation
Signal integrity (SI) simulation tools, such as Hyperlynx or Keysight ADS, can help you analyze the behavior of high-speed signals in your Rogers PCB design. These tools can simulate signal propagation, reflection, crosstalk, and other SI effects, allowing you to optimize trace routing, termination strategies, and impedance control.
By conducting SI simulations, you can identify potential issues, such as excessive overshoot, undershoot, or ringing, and make necessary adjustments to your design before fabrication.
Power Integrity Simulation
Power integrity (PI) simulation tools, such as Ansys SIwave or Cadence Sigrity, can help you analyze the impedance profile and voltage fluctuations of your power distribution network (PDN). These tools can simulate the behavior of your PDN across a wide frequency range, helping you identify resonances, voltage drops, and other PI issues.
By conducting PI simulations, you can optimize your PDN design, ensure adequate decoupling, and minimize power-related noise and instability in your Rogers PCB.
Electromagnetic Compatibility (EMC) Simulation
EMC simulation tools, such as Ansys HFSS or CST Studio Suite, can help you analyze the electromagnetic behavior of your Rogers PCB design. These tools can simulate electromagnetic fields, radiation patterns, and coupling effects, allowing you to identify potential EMI sources and optimize your design for EMC compliance.
By conducting EMC simulations, you can ensure that your Rogers PCB meets the required EMC standards and minimizes interference with other electronic systems.
Testing and Measurement
Once your Rogers PCB prototype is fabricated, it is essential to conduct thorough testing and measurements to validate its performance. Some key tests include:
- Time-domain reflectometry (TDR) measurements to verify impedance control and identify discontinuities.
- Vector network analyzer (VNA) measurements to characterize S-parameters, insertion loss, and return loss.
- Spectrum analyzer measurements to assess EMI and identify potential sources of interference.
- Thermal imaging or temperature measurements to verify thermal performance and identify hot spots.
By conducting comprehensive testing and measurements, you can validate your Rogers PCB design, identify any issues, and make necessary adjustments to ensure optimal performance and reliability.
Conclusion
Designing performance-driven Rogers PCBs requires careful consideration of various technical aspects, from material selection and trace geometry optimization to grounding, shielding, and thermal management. By following the eight technical tips outlined in this article, you can effectively design and validate your Rogers PCB to achieve optimal signal integrity, power integrity, and electromagnetic compatibility.
Remember to choose the right Rogers material for your application, optimize trace geometry for impedance control, minimize losses with proper copper surface treatment, implement effective grounding and shielding techniques, optimize via design, consider thermal management strategies, implement robust power distribution networks, and validate your design through simulation and testing.
By adhering to these technical guidelines and best practices, you can unlock the full potential of Rogers materials and create high-performance PCBs that meet the demanding requirements of today’s advanced electronic systems.
FAQ
- Q: What are the key advantages of using Rogers materials for high-frequency PCB design?
A: Rogers materials offer several advantages for high-frequency PCB design, including low dielectric constant (Dk), low dissipation factor (Df), stable performance over a wide temperature range, and good thermal conductivity. These properties enable
Leave a Reply