Introduction to DC Motor Controllers
A DC motor controller is a device that regulates the speed, torque, and direction of a DC motor. It plays a crucial role in various applications, from industrial machinery to robotics and automotive systems. Understanding the basics of DC Motor Controllers is essential for anyone working with or designing systems that involve DC motors.
In this article, we will explore seven key aspects of DC motor controllers that you should know to make informed decisions and optimize your motor control systems.
1. Types of DC Motor Controllers
There are several types of DC motor controllers available, each with its own characteristics and advantages. Let’s take a look at the most common types:
Pulse Width Modulation (PWM) Controllers
PWM controllers are the most widely used type of DC motor controller. They regulate the motor’s speed and torque by varying the width of the voltage pulses supplied to the motor. The longer the pulse width, the higher the average voltage applied to the motor, resulting in increased speed and torque.
Advantages of PWM controllers:
– Efficient power utilization
– Precise speed control
– Simple implementation
PID Controllers
PID (Proportional-Integral-Derivative) controllers use a feedback loop to continuously monitor and adjust the motor’s performance based on the desired setpoint. They calculate the error between the desired and actual motor output and apply corrective actions to minimize the error.
Advantages of PID controllers:
– Accurate and stable control
– Ability to handle disturbances and load changes
– Customizable tuning parameters
Brushless DC (BLDC) Controllers
BLDC controllers are specifically designed for brushless DC motors. These motors have permanent magnets on the rotor and electromagnets on the stator. BLDC controllers use electronic commutation to control the switching sequence of the stator windings, enabling precise control over the motor’s rotation.
Advantages of BLDC controllers:
– High efficiency and reliability
– Compact size and low maintenance
– Suitable for high-speed applications
2. Motor Specifications and Controller Selection
When selecting a DC motor controller, it’s essential to consider the specifications of the motor you are using. The controller must be compatible with the motor’s voltage and current ratings to ensure safe and efficient operation.
Voltage Rating
The controller’s voltage rating should match the motor’s rated voltage. Using a controller with a lower voltage rating than the motor can result in insufficient power delivery and reduced performance. On the other hand, using a controller with a higher voltage rating can damage the motor.
Current Rating
The controller’s current rating should be equal to or higher than the motor’s maximum current draw. If the controller’s current rating is too low, it may not be able to supply enough current to the motor during peak loads, leading to poor performance or controller damage.
Power Rating
The power rating of the controller should be sufficient to handle the motor’s power requirements. The power rating is calculated by multiplying the voltage and current ratings. Ensure that the controller’s power rating exceeds the motor’s maximum power consumption.
Here’s a table summarizing the key specifications to consider when selecting a DC motor controller:
Specification | Description |
---|---|
Voltage Rating | Should match the motor’s rated voltage |
Current Rating | Should be equal to or higher than the motor’s maximum current draw |
Power Rating | Should exceed the motor’s maximum power consumption |
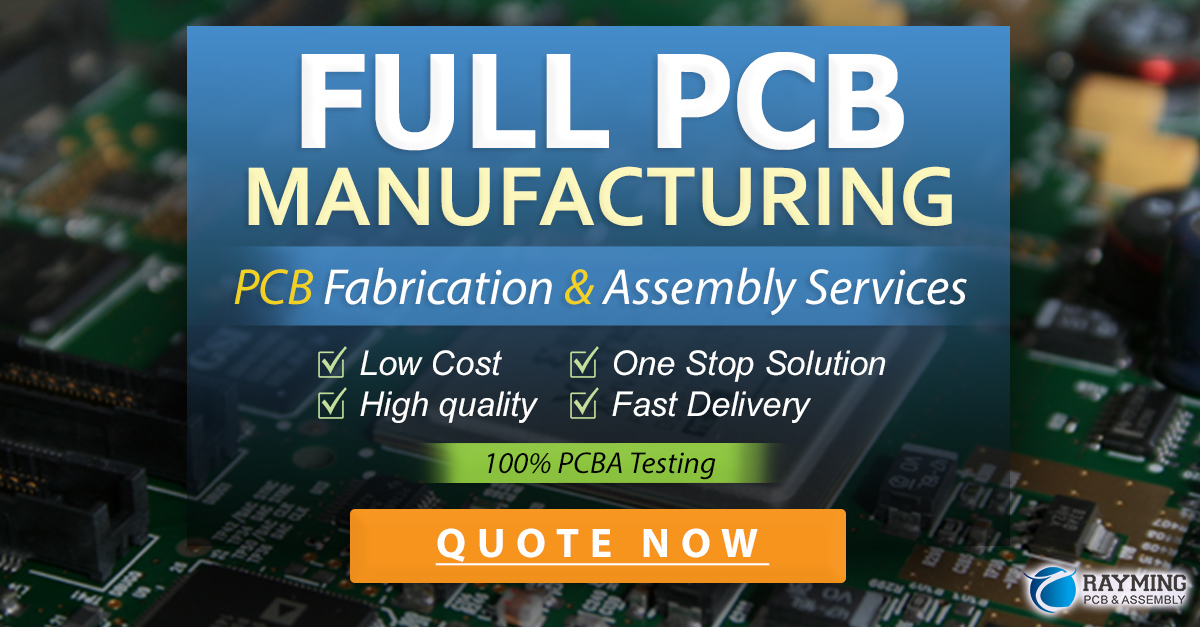
3. Speed Control Methods
DC motor controllers offer various speed control methods to regulate the motor’s speed according to the application requirements. Let’s explore the most common speed control methods:
Open-Loop Speed Control
Open-loop speed control is the simplest method, where the controller adjusts the voltage or current supplied to the motor without any feedback from the motor itself. The speed is controlled by varying the duty cycle of the PWM signal or the voltage level.
Advantages of open-loop speed control:
– Simple implementation
– Low cost
– Suitable for applications with low speed regulation requirements
Closed-Loop Speed Control
Closed-loop speed control involves using feedback from the motor, such as an encoder or tachometer, to measure the actual motor speed. The controller compares the measured speed with the desired speed and adjusts the voltage or current accordingly to minimize the error.
Advantages of closed-loop speed control:
– Precise speed regulation
– Ability to maintain constant speed under varying load conditions
– Suitable for applications with high speed accuracy requirements
Sensorless Speed Control
Sensorless speed control methods estimate the motor speed without using physical sensors. These methods rely on monitoring the back-EMF (electromotive force) generated by the motor or using observer-based techniques to estimate the speed.
Advantages of sensorless speed control:
– Reduced system complexity and cost
– Eliminates the need for additional sensors
– Suitable for applications where sensor installation is challenging
4. Protection Features
DC motor controllers often include various protection features to safeguard the motor and the controller itself from potential damage. Let’s discuss some common protection features:
Overcurrent Protection
Overcurrent protection prevents excessive current from flowing through the motor and controller. If the current exceeds a predetermined threshold, the controller will either limit the current or shut down the system to prevent damage.
Overvoltage Protection
Overvoltage protection safeguards the controller and motor from voltage spikes or surges that exceed the rated voltage. The controller will typically clamp the voltage or disconnect the power supply to protect the components.
Thermal Protection
Thermal protection monitors the temperature of the controller and motor. If the temperature exceeds a safe operating range, the controller will reduce the current or shut down the system to prevent overheating and damage.
Short-Circuit Protection
Short-circuit protection detects and prevents damage caused by short-circuits in the motor or wiring. The controller will rapidly cut off the power supply to protect the system from excessive current flow.
Here’s a table summarizing the common protection features in DC motor controllers:
Protection Feature | Description |
---|---|
Overcurrent Protection | Prevents excessive current flow |
Overvoltage Protection | Safeguards against voltage spikes or surges |
Thermal Protection | Monitors temperature and prevents overheating |
Short-Circuit Protection | Detects and prevents damage from short-circuits |
5. Regenerative Braking
Regenerative braking is a feature found in some DC motor controllers that allows the motor to act as a generator during deceleration or braking. When the motor is slowed down or stopped, the kinetic energy is converted back into electrical energy, which can be returned to the power source or dissipated as heat.
Advantages of regenerative braking:
– Improved energy efficiency
– Reduced heat generation during braking
– Extended battery life in battery-powered systems
However, implementing regenerative braking requires additional components, such as capacitors or batteries, to store the recovered energy. The controller must also be designed to handle the reverse flow of current during the braking process.
6. Communication Interfaces
DC motor controllers often include communication interfaces that allow them to interact with other devices, such as microcontrollers, PLCs, or higher-level control systems. These interfaces enable data exchange, parameter configuration, and real-time monitoring of the motor’s performance.
Common communication interfaces used in DC motor controllers:
Serial Communication (RS-232, RS-485)
Serial communication interfaces, such as RS-232 or RS-485, provide a simple and reliable way to transmit data between the controller and other devices. RS-232 is suitable for short-distance, point-to-point communication, while RS-485 supports longer distances and multi-drop configurations.
CAN (Controller Area Network)
CAN is a robust communication protocol widely used in automotive and industrial applications. It allows multiple devices to communicate on a shared bus, providing high noise immunity and error detection capabilities.
Ethernet
Ethernet interfaces enable the controller to connect to a local area network (LAN) or the internet. This allows remote monitoring, control, and integration with other networked devices using standard protocols like TCP/IP.
Wireless (Bluetooth, Wi-Fi)
Wireless interfaces, such as Bluetooth or Wi-Fi, offer the convenience of wireless connectivity between the controller and other devices. This eliminates the need for physical wiring and enables remote control and monitoring from mobile devices or computers.
7. Application-Specific Considerations
When selecting and implementing a DC motor controller, it’s important to consider the specific requirements of your application. Different applications may have unique demands in terms of performance, environment, and safety.
Industrial Applications
In industrial settings, DC motor controllers must be robust, reliable, and capable of handling harsh environments. They may need to comply with specific safety standards and have features like ingress protection (IP) ratings to withstand dust, moisture, or other contaminants.
Automotive Applications
DC motor controllers used in automotive applications must meet stringent requirements for reliability, temperature range, and vibration resistance. They should also comply with automotive industry standards and have features like undervoltage protection to handle voltage fluctuations in the vehicle’s electrical system.
Robotics and Automation
In robotics and automation applications, DC motor controllers need to provide precise and responsive control to ensure accurate movement and positioning. They may require advanced features like position control, trajectory planning, and the ability to interface with sensors and other automation components.
Frequently Asked Questions (FAQ)
-
What is the difference between a DC motor driver and a DC motor controller?
A DC motor driver is a simpler device that primarily provides the necessary current and voltage to drive the motor. A DC motor controller, on the other hand, includes additional features like speed control, feedback, and protection mechanisms. -
Can a DC motor controller be used with any DC motor?
No, a DC motor controller must be selected based on the specifications of the motor, such as voltage rating, current rating, and power requirements. Using a controller that is not compatible with the motor can result in poor performance or damage to the motor and controller. -
How do I tune a PID controller for my DC motor?
Tuning a PID controller involves adjusting the proportional, integral, and derivative gains to achieve the desired motor response. The tuning process typically involves trial and error, starting with a basic understanding of each gain’s effect on the system. It’s recommended to start with low gains and gradually increase them until the desired performance is achieved. -
What is the role of PWM in DC Motor Speed Control?
Pulse Width Modulation (PWM) is a technique used to control the speed of a DC motor by varying the width of the voltage pulses supplied to the motor. By adjusting the duty cycle of the PWM signal, the average voltage applied to the motor can be varied, thus controlling its speed. -
How do I select the appropriate current rating for my DC motor controller?
The current rating of the DC motor controller should be equal to or higher than the motor’s maximum current draw. To determine the required current rating, refer to the motor’s specifications or measure the current consumption under maximum load conditions. It’s recommended to choose a controller with a current rating that provides some headroom to account for transient currents or future system upgrades.
Conclusion
DC motor controllers play a vital role in regulating the speed, torque, and direction of DC motors in various applications. Understanding the different types of controllers, motor specifications, speed control methods, protection features, and communication interfaces is crucial for selecting the appropriate controller for your specific requirements.
By considering factors such as voltage and current ratings, power requirements, and application-specific needs, you can ensure optimal performance, efficiency, and reliability of your DC motor control system.
Remember to refer to the manufacturer’s documentation and seek expert guidance when necessary to make informed decisions and achieve the best results in your DC motor control applications.
Leave a Reply