Understanding PCB Colors
PCB colors are determined by the solder mask, which is a protective layer applied over the copper traces on the board. The solder mask serves several purposes:
- Insulates the copper traces from accidental short circuits
- Protects the copper from oxidation and corrosion
- Provides a surface for printing component labels and markings
- Enhances the aesthetic appeal of the PCB
The choice of PCB color can impact various aspects of the manufacturing process, functionality, and visual appearance of the final product.
The 7 Main PCB Colors
1. Green
Green is the most common and default color for PCBs. It is widely used due to its excellent contrast with copper traces and white silkscreen markings. Green PCBs offer several advantages:
- Good visual inspection capabilities
- Easier to spot defects and issues during manufacturing
- Widely available and cost-effective
- Suitable for a wide range of applications
2. Red
Red PCBs are often used in high-end audio equipment and consumer electronics. They provide a striking visual appearance and can enhance the perceived value of the product. However, red PCBs have some limitations:
- Reduced contrast with copper traces
- Potential for lower manufacturing yields due to difficulty in visual inspection
- Higher cost compared to green PCBs
3. Blue
Blue PCBs are gaining popularity in recent years, particularly in the gaming and high-performance computing sectors. They offer a unique aesthetic appeal and can help differentiate products from competitors. Blue PCBs have the following characteristics:
- Good contrast with copper traces and white silkscreen
- Visually appealing and modern look
- Potential for higher manufacturing costs
4. Black
Black PCBs are commonly used in high-end electronics, such as smartphones, smartwatches, and premium audio devices. They provide a sleek and sophisticated appearance, making them ideal for products where aesthetics are a key selling point. Black PCBs have the following properties:
- Excellent visual appearance
- High contrast with copper traces and white silkscreen
- Potential for higher manufacturing costs
- Requires careful handling to avoid visible scratches or fingerprints
5. White
White PCBs are relatively uncommon but can be used in specific applications where a clean and minimalistic look is desired. They are often found in LED lighting products and some medical devices. White PCBs have the following characteristics:
- Unique and clean appearance
- Good contrast with copper traces and black silkscreen
- Potential for higher manufacturing costs
- Requires careful handling to avoid visible dirt or stains
6. Yellow
Yellow PCBs are rarely used in commercial products but can be found in some industrial and military applications. They offer high visibility and can be useful in environments where clear identification is critical. Yellow PCBs have the following properties:
- High visibility and contrast
- Suitable for harsh environments
- Potential for higher manufacturing costs
- Limited availability compared to other colors
7. Purple
Purple PCBs are an uncommon choice but can be used to create a unique and eye-catching look in consumer electronics. They are sometimes used in gaming peripherals and high-end audio equipment. Purple PCBs have the following characteristics:
- Unique and visually striking appearance
- Good contrast with copper traces and white silkscreen
- Potential for higher manufacturing costs
- Limited availability compared to other colors
Factors to Consider When Selecting PCB Color
When choosing the best PCB color for your project, consider the following factors:
-
Application: Consider the end-use of your product and the environment it will be used in. Industrial and military applications may require specific colors for identification or visibility purposes.
-
Aesthetics: If your product’s appearance is a key selling point, choose a color that complements the overall design and enhances its visual appeal.
-
Manufacturing Cost: Some PCB colors may have higher manufacturing costs due to additional processing steps or material costs. Consider your budget and the impact of color choice on the overall project cost.
-
Availability: Not all PCB colors are readily available from all manufacturers. Check with your PCB supplier to ensure they can accommodate your color preference.
-
Contrast and Visibility: Ensure that the chosen color provides sufficient contrast with copper traces and silkscreen markings for easy visual inspection and troubleshooting.
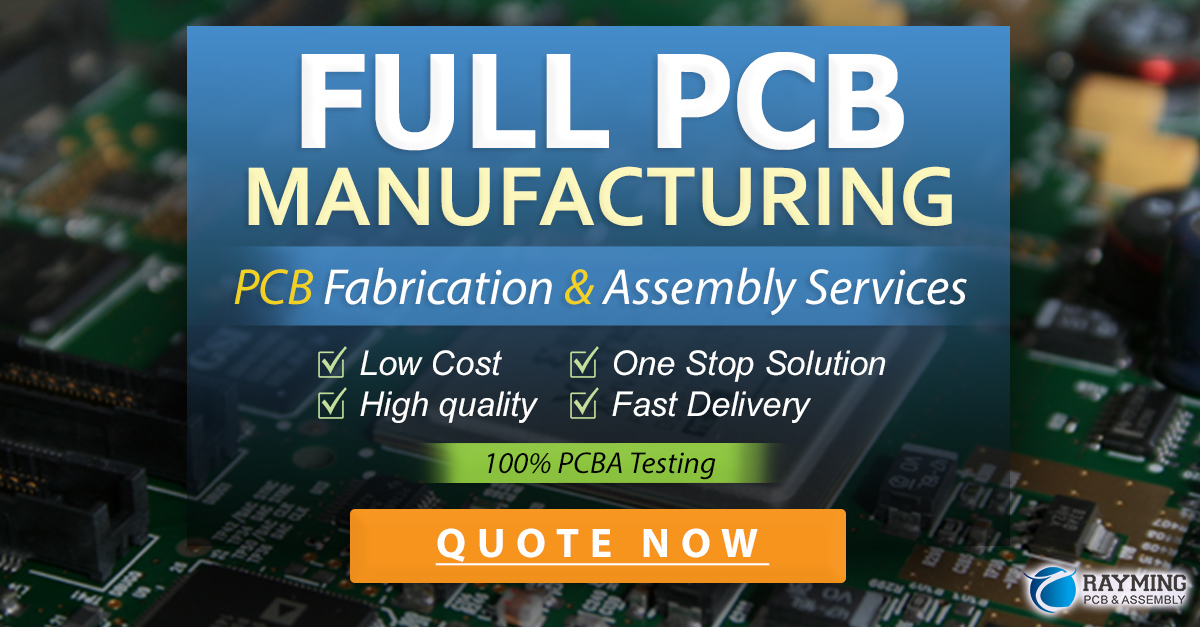
PCB Color Comparison Table
Color | Contrast with Copper | Visual Appeal | Manufacturing Cost | Availability |
---|---|---|---|---|
Green | Excellent | Standard | Low | High |
Red | Good | High | Medium | Medium |
Blue | Good | High | Medium | Medium |
Black | Excellent | Very High | High | Medium |
White | Good | Very High | High | Low |
Yellow | Excellent | Medium | High | Low |
Purple | Good | High | High | Low |
FAQ
-
Q: Does the PCB color affect its functionality?
A: No, the PCB color itself does not affect its functionality. The color is determined by the solder mask, which is a protective layer that does not impact the electrical properties of the board. -
Q: Can I mix different PCB colors in the same project?
A: Yes, you can use different PCB colors within the same project. However, keep in mind that this may increase manufacturing complexity and cost. -
Q: Are there any industry standards for PCB colors?
A: There are no strict industry standards for PCB colors. However, green is considered the default color and is widely used across various industries. -
Q: How does the PCB color affect the manufacturing process?
A: The PCB color can impact visual inspection capabilities during manufacturing. Some colors, such as red or black, may make it more difficult to spot defects or issues, potentially leading to lower yields. -
Q: Can I request a custom PCB color from my manufacturer?
A: Some PCB manufacturers may offer custom color options, but this will depend on their capabilities and may come with additional costs. It’s best to discuss your specific requirements with your chosen manufacturer.
Conclusion
Selecting the best PCB color for your project involves considering various factors, such as application, aesthetics, manufacturing cost, availability, and contrast. While green remains the most common and default choice, other colors like red, blue, black, white, yellow, and purple offer unique visual appeals and can be used to differentiate your product.
By understanding the properties and implications of each PCB color, you can make an informed decision that balances functionality, appearance, and cost. Always consult with your PCB manufacturer to ensure they can accommodate your color preference and to discuss any potential impact on the manufacturing process.
Leave a Reply