1. Choose the Right Solder Paste
Selecting the appropriate solder paste is essential for achieving a strong and reliable solder joint when working with flex PCBs and SMD components. The solder paste should have the following properties:
1.1 Viscosity
The viscosity of the solder paste should be suitable for the application method and the size of the SMD components. A solder paste with the right viscosity will ensure proper coverage and adhesion to the pads on the flex PCB.
Viscosity Range | Application Method |
---|---|
800,000-1,000,000 cP | Stencil Printing |
400,000-600,000 cP | Dispense |
150,000-250,000 cP | Syringe |
1.2 Alloy Composition
The alloy composition of the solder paste should be compatible with the surface finish of the flex PCB and the SMD components. The most common alloy compositions for Flex PCB Soldering are:
- Sn63/Pb37 (Tin-Lead)
- Sn96.5/Ag3.0/Cu0.5 (Lead-Free)
- Sn42/Bi57.6/Ag0.4 (Low-Temperature Lead-Free)
1.3 Flux Activity
The flux activity of the solder paste should be appropriate for the type of flex PCB and SMD components being used. The flux helps to remove oxides from the surfaces being soldered and promotes wetting of the solder.
Flux Activity | Type | Application |
---|---|---|
Low | ROL0 | Clean surfaces, low oxidation |
Moderate | ROL1 | Slightly oxidized surfaces |
High | ROH1 | Heavily oxidized surfaces |
2. Control the Soldering Temperature
Controlling the soldering temperature is crucial when working with flex PCBs, as they are more sensitive to heat compared to rigid PCBs. Excessive heat can cause damage to the flex PCB, resulting in delamination, warping, or other defects.
2.1 Reflow Soldering Temperature Profile
When using reflow soldering for flex PCBs, it is important to follow the recommended temperature profile provided by the solder paste manufacturer. A typical reflow soldering temperature profile consists of four stages:
- Preheat: Gradually raise the temperature to activate the flux and evaporate solvents.
- Soak: Maintain a stable temperature to allow the components and PCB to reach thermal equilibrium.
- Reflow: Raise the temperature above the melting point of the solder alloy to form the solder joints.
- Cooling: Gradually cool down the PCB to room temperature to allow the solder joints to solidify.
2.2 Hand Soldering Temperature
If hand soldering is required for certain components or repairs, it is essential to use a temperature-controlled soldering iron with a fine tip. The recommended soldering temperature for flex PCBs is between 315°C and 370°C (600°F to 700°F), depending on the solder alloy and the size of the components.
3. Use Proper Soldering Techniques
Proper soldering techniques are essential for achieving reliable and consistent solder joints when working with flex PCBs and SMD components.
3.1 Stencil Printing
Stencil printing is the most common method for applying solder paste to flex PCBs. The stencil should be designed with the appropriate aperture size and shape for each SMD component. The thickness of the stencil should be selected based on the size of the components and the desired solder volume.
Component Size | Stencil Thickness |
---|---|
0201 | 0.1 mm (4 mil) |
0402 | 0.1-0.15 mm (4-6 mil) |
0603 | 0.15-0.2 mm (6-8 mil) |
0805 and larger | 0.2-0.25 mm (8-10 mil) |
3.2 Component Placement
Accurate component placement is crucial for ensuring proper solder joint formation and preventing short circuits or other defects. When placing SMD components on flex PCBs, consider the following:
- Use a pick-and-place machine or fine-tipped tweezers for precise placement.
- Align the components with the solder paste deposits on the pads.
- Ensure that the components are seated flat on the PCB surface.
3.3 Reflow Soldering
During the reflow soldering process, it is important to monitor the temperature profile and ensure that it adheres to the recommended guidelines. Key points to consider include:
- Proper preheating to activate the flux and evaporate solvents.
- Adequate soak time to allow the components and PCB to reach thermal equilibrium.
- Peak temperature and duration sufficient to form reliable solder joints.
- Gradual cooling to prevent thermal shock and allow the solder joints to solidify.
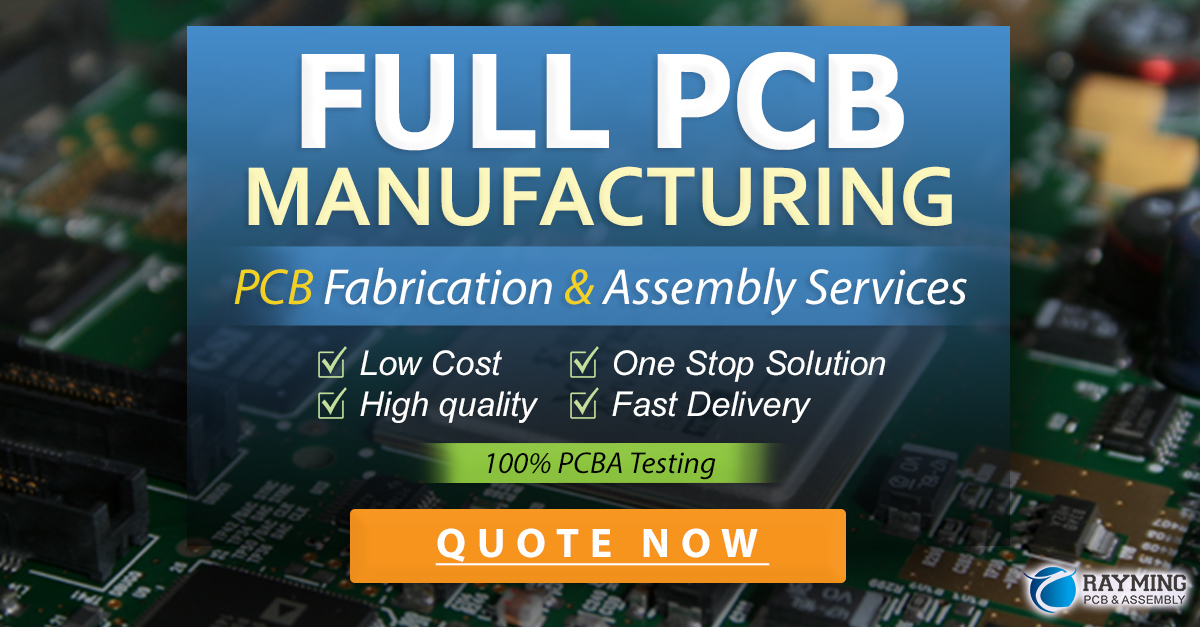
4. Inspect and Clean the Solder Joints
After the soldering process, it is essential to inspect and clean the solder joints to ensure their quality and reliability.
4.1 Visual Inspection
Perform a visual inspection of the solder joints using a magnifying lens or microscope. Look for the following characteristics of a good solder joint:
- Smooth and shiny surface
- Concave meniscus shape
- Proper wetting of the pad and component termination
- No visible defects (e.g., voids, cracks, or bridges)
4.2 X-Ray Inspection
For components with hidden solder joints, such as ball grid arrays (BGAs) or quad flat no-lead (QFN) packages, X-ray inspection may be necessary to verify the quality of the solder joints.
4.3 Cleaning
After inspection, clean the flux residue from the flex PCB using an appropriate cleaning method and solution. The cleaning method should be compatible with the type of flux used and the materials of the flex PCB and components.
Flux Type | Cleaning Method |
---|---|
Water-soluble | DI water |
Rosin | Isopropyl alcohol (IPA) |
No-clean | No cleaning required |
5. Handle and Store Flex PCBs Properly
Proper handling and storage of flex PCBs are essential to maintain their integrity and prevent damage.
5.1 Handling
When handling flex PCBs, follow these guidelines:
- Wear clean, lint-free gloves to prevent contamination and skin oils from affecting the soldering process.
- Avoid excessive bending or twisting of the flex PCB, as this can cause damage to the copper traces or the substrate.
- Use support fixtures or carriers when necessary to prevent damage during handling or transportation.
5.2 Storage
To ensure the longevity and reliability of flex PCBs, store them properly:
- Keep flex PCBs in a clean, dry, and temperature-controlled environment.
- Use anti-static bags or containers to protect the PCBs from electrostatic discharge (ESD) damage.
- Avoid storing flex PCBs in areas with high humidity or excessive temperature fluctuations.
Frequently Asked Questions (FAQ)
1. What is the difference between flex PCBs and rigid PCBs in terms of soldering?
Flex PCBs require more attention to temperature control and handling compared to rigid PCBs. The flexible nature of the substrate makes it more susceptible to damage from excessive heat or mechanical stress during the soldering process.
2. Can I use the same soldering techniques for flex PCBs as I do for rigid PCBs?
While many of the soldering techniques are similar, there are some key differences to consider when working with flex PCBs. These include using lower soldering temperatures, selecting compatible solder paste and flux, and proper handling to prevent damage to the flexible substrate.
3. How do I select the right solder paste for my flex PCB application?
When selecting a solder paste for flex PCB soldering, consider factors such as the viscosity, alloy composition, and flux activity. The solder paste should be compatible with the surface finish of the flex PCB and the SMD components, and it should have the appropriate properties for the application method (e.g., stencil printing, dispensing, or syringe application).
4. What are some common defects to look for when inspecting solder joints on flex PCBs?
Common defects to look for during solder joint inspection include voids, cracks, bridges, poor wetting, and incomplete fillets. Visual inspection with a magnifying lens or microscope can help identify these defects, while X-ray inspection may be necessary for hidden solder joints.
5. How can I prevent damage to my flex PCBs during handling and storage?
To prevent damage to flex PCBs during handling and storage, follow best practices such as wearing clean gloves, avoiding excessive bending or twisting, using support fixtures when necessary, and storing the PCBs in a clean, dry, and temperature-controlled environment. Use anti-static bags or containers to protect the PCBs from electrostatic discharge damage.
By paying attention to these five key aspects of flex PCB soldering SMD components, you can ensure a successful and reliable soldering process, resulting in high-quality electronic devices that meet your performance and durability requirements.
Leave a Reply