1. Bridging
Bridging is a common PCB Soldering defect that occurs when solder inadvertently connects two or more adjacent pins or pads, creating an unintended short circuit. This can happen due to excessive solder, improper soldering technique, or poor PCB Design.
Tips to prevent bridging:
- Use the appropriate amount of solder
- Maintain proper soldering iron temperature
- Ensure adequate spacing between pins or pads during PCB design
- Use a solder mask to prevent solder from spreading to adjacent areas
2. Cold Joint
A cold joint occurs when the solder fails to melt completely, resulting in a poor connection between the component and the PCB. This can be caused by insufficient heat, improper fluxing, or a dirty soldering iron tip.
Tips to prevent cold joints:
- Ensure the soldering iron is at the correct temperature
- Clean the soldering iron tip regularly
- Use the appropriate flux
- Preheat the PCB and components before soldering
3. Tombstoning
Tombstoning, also known as the “Manhattan effect,” occurs when a surface-mount component stands up on one end during the soldering process. This is usually caused by uneven heating or an imbalance in the solder paste volume on the pads.
Tips to prevent tombstoning:
- Ensure even distribution of solder paste on the pads
- Maintain proper alignment of components during placement
- Use a temperature profile that allows for even heating of the component and PCB
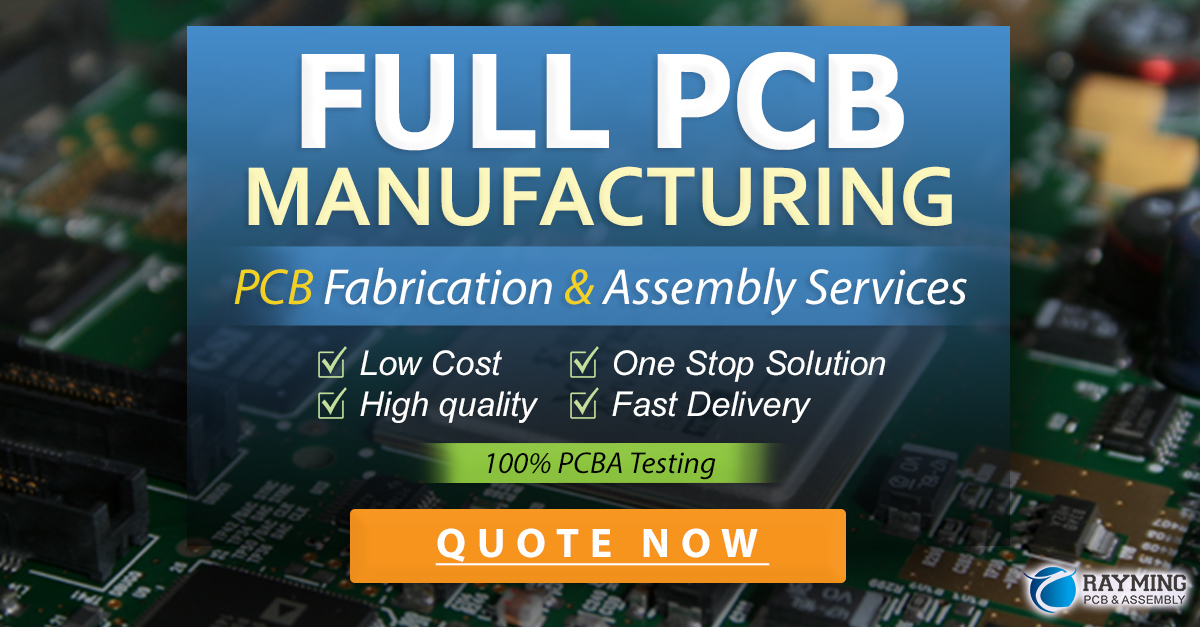
4. Solder Balls
Solder balls are small, spherical balls of solder that can form on the PCB during the soldering process. They can cause short circuits and lead to reliability issues. Solder balls can be caused by excessive solder, improper solder paste application, or incorrect reflow temperature profile.
Tips to prevent solder balls:
- Use the appropriate amount of solder paste
- Ensure proper stencil design and alignment during solder paste application
- Optimize the reflow temperature profile
- Use a nitrogen atmosphere during reflow soldering to reduce oxidation
5. Insufficient Solder
Insufficient solder occurs when there is not enough solder to create a proper connection between the component and the PCB. This can lead to weak joints and poor electrical conductivity. Insufficient solder can be caused by inadequate solder paste application, incorrect stencil design, or improper soldering technique.
Tips to prevent insufficient solder:
- Ensure proper stencil design and alignment during solder paste application
- Use the appropriate amount of solder paste
- Maintain proper soldering iron temperature and technique
- Inspect solder joints visually and with x-ray for critical components
6. Lifted Pads
Lifted pads occur when the copper pad on the PCB separates from the board during the soldering process. This can be caused by poor PCB design, excessive heat during soldering, or improper handling of the PCB.
Tips to prevent lifted pads:
- Ensure proper PCB design with adequate copper anchoring
- Maintain appropriate soldering iron temperature
- Handle PCBs with care, avoiding excessive bending or flexing
- Use a temperature-controlled soldering iron to avoid overheating
7. Solder Flags
Solder flags, also known as solder spikes or horns, are sharp, pointed protrusions of solder that can occur on the PCB. They can cause short circuits and lead to reliability issues. Solder flags can be caused by improper solder paste application, incorrect reflow temperature profile, or poor PCB design.
Tips to prevent solder flags:
- Ensure proper stencil design and alignment during solder paste application
- Optimize the reflow temperature profile
- Use a nitrogen atmosphere during reflow soldering to reduce oxidation
- Ensure adequate pad size and shape in PCB design
8. Starved Solder Joint
A starved solder joint occurs when there is insufficient solder between the component lead and the PCB pad, resulting in a weak connection. This can be caused by inadequate solder paste application, incorrect soldering iron temperature, or poor wetting of the component lead or PCB pad.
Tips to prevent starved solder joints:
- Ensure proper solder paste application
- Maintain appropriate soldering iron temperature
- Clean component leads and PCB pads before soldering
- Use an appropriate flux to improve solder wetting
9. Dewetting
Dewetting occurs when the molten solder fails to adhere to the surface of the component lead or PCB pad, resulting in a poor connection. This can be caused by contamination, oxidation, or incorrect soldering temperature.
Tips to prevent dewetting:
- Clean component leads and PCB pads before soldering
- Use an appropriate flux to remove oxides and improve solder wetting
- Maintain proper soldering iron temperature
- Ensure the soldering environment is clean and free from contaminants
10. Blowholes
Blowholes are small, crater-like voids that can form in the solder joint during the soldering process. They can weaken the solder joint and lead to reliability issues. Blowholes can be caused by trapped gases, contamination, or incorrect reflow temperature profile.
Tips to prevent blowholes:
- Ensure proper cleaning of component leads and PCB pads
- Optimize the reflow temperature profile to allow for proper outgassing
- Use a nitrogen atmosphere during reflow soldering to reduce oxidation
- Ensure the solder paste is free from contamination
11. Solder Beading
Solder beading occurs when small, round balls of solder form on the surface of the solder joint. While not always a defect, excessive solder beading can indicate poor wetting or incorrect solder paste volume.
Tips to prevent excessive solder beading:
- Ensure proper solder paste volume and placement
- Maintain appropriate soldering iron temperature
- Use an appropriate flux to improve solder wetting
- Ensure component leads and PCB pads are clean and free from oxidation
12. Flux Residue
Flux residue is a common occurrence after soldering, but excessive or corrosive flux residue can lead to reliability issues and even cause short circuits.
Tips to manage flux residue:
- Use a no-clean flux whenever possible
- If using a water-soluble or rosin-based flux, ensure proper cleaning after soldering
- Monitor the amount of flux used during soldering
- Ensure the soldering environment is clean and free from contaminants
13. Whiskers
Solder whiskers are thin, hair-like protrusions that can grow from the surface of the solder joint over time. They can cause short circuits and lead to reliability issues. Whiskers are more common in lead-free solders and can be influenced by factors such as stress, temperature, and humidity.
Tips to prevent whiskers:
- Use lead-based solders when possible and allowed by regulations
- Ensure proper storage and handling of PCBs to minimize stress
- Use conformal coatings to protect solder joints from environmental factors
- Monitor solder joints regularly for whisker growth, especially in critical applications
FAQs
1. What is the most common PCB soldering defect?
Bridging is one of the most common PCB Soldering Defects, as it can easily occur when there is excessive solder or poor soldering technique.
2. Can PCB soldering defects be repaired?
Many PCB soldering defects can be repaired using techniques such as solder wick, solder sucker, or hot air rework. However, some defects, such as lifted pads or extensive damage, may require more advanced repair methods or even PCB replacement.
3. How can I improve my PCB soldering skills?
Practice is key to improving PCB soldering skills. Start with simple projects and work your way up to more complex ones. Attend workshops, read tutorials, and watch videos to learn proper techniques. Investing in quality soldering tools and maintaining a clean, organized workspace can also help.
4. What are the consequences of PCB soldering defects?
PCB soldering defects can lead to a range of issues, including poor performance, reliability problems, and even complete failure of the electronic device. In critical applications, such as medical or aerospace equipment, soldering defects can have serious safety implications.
5. How can I ensure consistent PCB soldering quality?
Implementing a robust quality control process is essential for ensuring consistent PCB soldering quality. This can include visual inspections, x-ray analysis, and electrical testing. Establishing and adhering to standard operating procedures, providing regular training for operators, and using automated Soldering Equipment when possible can also help maintain high-quality soldering results.
Defect Type | Causes | Prevention Tips |
---|---|---|
Bridging | Excessive solder, improper technique, poor PCB design | Use appropriate solder amount, maintain proper iron temperature, ensure adequate pad spacing |
Cold Joint | Insufficient heat, improper fluxing, dirty iron tip | Ensure correct iron temperature, clean tip regularly, use appropriate flux, preheat PCB and components |
Tombstoning | Uneven heating, imbalanced solder paste | Ensure even solder paste distribution, maintain component alignment, use proper temperature profile |
[Table 1: Common PCB Soldering Defects, Causes, and Prevention Tips]
In conclusion, understanding the various types of PCB soldering defects and their causes is crucial for ensuring the quality and reliability of electronic devices. By implementing the tips and best practices outlined in this article, you can minimize the occurrence of these defects and improve your PCB soldering results. Regular training, quality control, and continuous improvement processes are also essential for maintaining high standards in PCB soldering.
Leave a Reply