Introduction to PCB Soldering
PCB soldering is a critical process in the manufacturing of electronic devices. It involves joining electronic components to a printed circuit board (PCB) using molten solder. Proper PCB soldering ensures the reliability and functionality of the electronic device. However, there are several issues that can arise during the PCB soldering process, which can lead to defects and failures in the final product. In this article, we will discuss 10 issues that we need to pay attention to in PCB soldering.
1. Solder Bridging
Solder bridging is a common issue in PCB soldering where the solder inadvertently connects two or more pins or pads that should not be connected. This can happen when too much solder is applied or when the soldering iron is not properly controlled. Solder bridging can cause short circuits and other electrical issues in the final product.
To prevent solder bridging, it is important to use the right amount of solder and to control the soldering iron carefully. Using a soldering iron with a fine tip can also help to minimize the risk of solder bridging.
2. Cold Solder Joints
Cold solder joints occur when the solder does not properly melt and flow around the joint. This can happen when the soldering iron is not hot enough or when the solder is not applied properly. Cold solder joints can cause intermittent electrical connections and can lead to failures in the final product.
To prevent cold solder joints, it is important to use a soldering iron that is hot enough to melt the solder properly. The soldering iron should be held at a 45-degree angle to the joint and the solder should be applied to the joint, not the soldering iron tip.
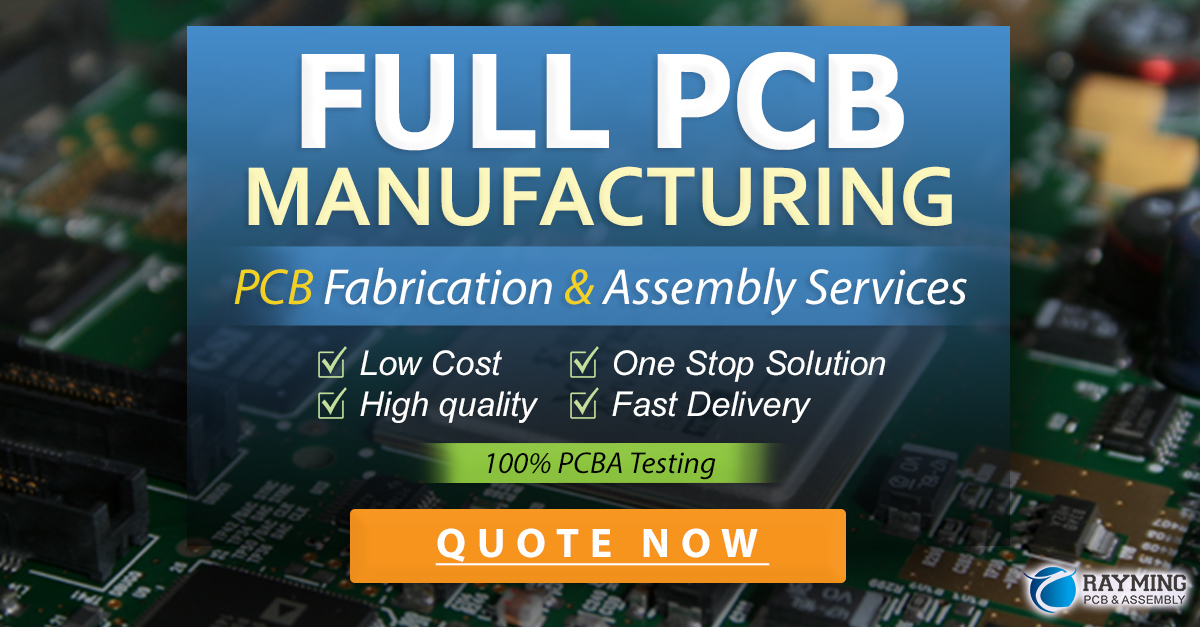
3. Insufficient Solder
Insufficient solder can occur when not enough solder is applied to the joint. This can happen when the soldering iron is not hot enough or when the solder is not applied for long enough. Insufficient solder can cause weak joints that can break or fail over time.
To prevent insufficient solder, it is important to use enough solder to create a strong joint. The solder should be applied until it flows around the entire joint and creates a concave fillet.
4. Excessive Solder
Excessive solder can occur when too much solder is applied to the joint. This can happen when the soldering iron is held on the joint for too long or when too much solder is used. Excessive solder can cause short circuits and other electrical issues in the final product.
To prevent excessive solder, it is important to use the right amount of solder and to control the soldering iron carefully. The solder should be applied until it flows around the entire joint and creates a concave fillet, but not so much that it creates a bulging or convex joint.
5. Lifted Pads
Lifted pads occur when the copper pad on the PCB separates from the board during the soldering process. This can happen when the soldering iron is held on the pad for too long or when too much force is applied to the component during soldering. Lifted pads can cause open circuits and other electrical issues in the final product.
To prevent lifted pads, it is important to use a soldering iron with a temperature that is appropriate for the PCB material and to apply the right amount of pressure when soldering components. Using a PCB with a thicker copper layer can also help to prevent lifted pads.
6. Tombstoning
Tombstoning is a common issue in surface mount technology (SMT) soldering where one end of a component lifts up from the PCB, creating a tombstone-like appearance. This can happen when there is an imbalance in the solder volume on the two pads of the component or when the component is not properly aligned with the pads.
To prevent tombstoning, it is important to ensure that the solder paste is applied evenly to both pads of the component and that the component is properly aligned with the pads. Using a stencil or solder paste dispenser can help to ensure even solder paste application.
7. Solder Balls
Solder balls are small spheres of solder that can form on the PCB during the soldering process. They can cause short circuits and other electrical issues in the final product. Solder balls can form when there is too much solder on the PCB or when the solder is not properly heated.
To prevent solder balls, it is important to use the right amount of solder and to ensure that the solder is properly heated. Using a soldering iron with a temperature that is appropriate for the solder type can help to prevent solder balls.
8. Flux Residue
Flux is a chemical that is used in the soldering process to help the solder flow and adhere to the joints. However, if the flux is not properly cleaned off the PCB after soldering, it can leave a residue that can cause corrosion and other issues in the final product.
To prevent flux residue, it is important to use a flux that is appropriate for the soldering process and to clean the PCB thoroughly after soldering. Using a solvent or cleaning agent that is compatible with the flux can help to remove any residue.
9. Component Misalignment
Component misalignment occurs when a component is not properly aligned with the pads on the PCB. This can cause poor electrical connections and other issues in the final product. Component misalignment can happen when the component is not properly placed on the PCB or when the solder paste is not applied evenly.
To prevent component misalignment, it is important to use a pick-and-place machine or other automated assembly equipment to ensure that components are properly placed on the PCB. Using a stencil or solder paste dispenser can also help to ensure even solder paste application.
10. Thermal Damage
Thermal damage can occur when the PCB or components are exposed to excessive heat during the soldering process. This can cause the PCB material to delaminate or the components to fail. Thermal damage can happen when the soldering iron is held on the joint for too long or when the soldering iron temperature is too high.
To prevent thermal damage, it is important to use a soldering iron with a temperature that is appropriate for the PCB material and components. The soldering iron should be held on the joint for the minimum amount of time necessary to create a good solder joint.
Issue | Cause | Prevention |
---|---|---|
Solder Bridging | Too much solder or poor soldering iron control | Use the right amount of solder and control the soldering iron carefully |
Cold Solder Joints | Soldering iron not hot enough or poor solder application | Use a hot enough soldering iron and apply solder to the joint, not the tip |
Insufficient Solder | Not enough solder applied or soldering iron not hot enough | Use enough solder to create a strong joint and apply until it flows around the joint |
Excessive Solder | Too much solder applied or soldering iron held on joint for too long | Use the right amount of solder and control the soldering iron carefully |
Lifted Pads | Soldering iron held on pad for too long or too much force applied | Use appropriate soldering iron temperature and apply the right amount of pressure |
Tombstoning | Imbalance in solder volume or poor component alignment | Ensure even solder paste application and proper component alignment |
Solder Balls | Too much solder or improperly heated solder | Use the right amount of solder and ensure proper heating |
Flux Residue | Improper cleaning or incompatible flux | Use appropriate flux and clean the PCB thoroughly after soldering |
Component Misalignment | Poor component placement or uneven solder paste application | Use automated assembly equipment and ensure even solder paste application |
Thermal Damage | Excessive heat exposure | Use appropriate soldering iron temperature and minimize heat exposure time |
Frequently Asked Questions
1. What is the best type of solder to use for PCB soldering?
The best type of solder to use for PCB soldering depends on the specific application and the type of components being soldered. Lead-free solder is commonly used in modern electronics manufacturing due to environmental and health concerns. However, leaded solder may still be used in certain applications where high reliability is required, such as in aerospace or military equipment.
2. How do I choose the right soldering iron for PCB soldering?
When choosing a soldering iron for PCB soldering, consider the following factors:
- Wattage: A higher wattage soldering iron will heat up faster and maintain a more consistent temperature, but may be more difficult to control for delicate work.
- Tip size and shape: Choose a tip size and shape that is appropriate for the size of the components being soldered and the type of soldering being done (e.g. through-hole or surface mount).
- Temperature control: Look for a soldering iron with adjustable temperature control to ensure that the iron is at the appropriate temperature for the type of solder being used.
3. How do I properly clean a PCB after soldering?
To properly clean a PCB after soldering, follow these steps:
- Allow the PCB to cool completely after soldering.
- Use a solvent or cleaning agent that is compatible with the flux used during soldering. Isopropyl alcohol is a common choice.
- Apply the cleaning agent to the PCB using a brush or spray bottle.
- Use a soft brush or lint-free cloth to gently scrub the PCB, paying particular attention to areas with visible flux residue.
- Rinse the PCB with clean water or a compatible solvent to remove any remaining residue.
- Allow the PCB to dry completely before handling or installing in an electronic device.
4. What is the difference between through-hole and surface mount soldering?
Through-hole soldering involves soldering components with wire leads that are inserted through holes in the PCB and soldered on the opposite side of the board. Surface mount soldering involves soldering components directly onto pads on the surface of the PCB without holes.
Surface mount soldering allows for smaller component sizes and higher component density on the PCB, but requires more precise placement and soldering techniques. Through-hole soldering is generally easier and more forgiving, but results in larger components and lower component density.
5. How can I improve my PCB soldering skills?
To improve your PCB soldering skills, consider the following tips:
- Practice regularly on scrap PCBs or practice kits to build muscle memory and improve technique.
- Use the appropriate tools and materials for the job, including a high-quality soldering iron, solder, and flux.
- Pay attention to the fundamentals of good soldering technique, including proper tip temperature, solder application, and joint formation.
- Learn to recognize common soldering defects and how to troubleshoot and repair them.
- Consider taking a soldering course or workshop to learn from experienced professionals and receive hands-on guidance.
Conclusion
PCB soldering is a critical process in the manufacturing of electronic devices, and proper technique is essential for ensuring the reliability and functionality of the final product. By paying attention to the 10 issues discussed in this article, including solder bridging, cold solder joints, insufficient solder, excessive solder, lifted pads, tombstoning, solder balls, flux residue, component misalignment, and thermal damage, manufacturers can minimize defects and failures in their products.
Proper soldering technique involves using the right tools and materials, applying the appropriate amount of solder and heat, and carefully controlling the soldering process to ensure strong, reliable solder joints. By following best practices and continuously improving their skills, PCB manufacturers can produce high-quality electronic devices that meet the demands of today’s market.
Leave a Reply