What are HASL and ENIG Plating Methods?
HASL (Hot Air Solder Leveling) and ENIG (Electroless Nickel Immersion Gold) are two common surface finish plating methods used in PCB manufacturing to protect exposed copper pads and provide a solderable surface. The choice between HASL vs ENIG depends on various factors such as cost, lead-free requirements, flatness, durability, shelf life, and appearance. Let’s dive into the key differences between these two PCB surface finishes.
HASL PCB Plating
HASL has been the standard PCB surface finish for decades. The PCB is dipped in a molten solder bath, usually a tin-lead alloy. Hot air knives then blow off the excess solder, leveling the surface. The resulting finish has a slightly uneven surface with solder bumps and a shiny metallic appearance.
ENIG PCB Plating
ENIG is a newer, more advanced surface finish that has gained popularity in recent years, especially for lead-free applications. An electroless nickel layer (1-5 µm) is first deposited on the copper pads, followed by a thin immersion gold layer (0.05-0.2 µm). The gold protects the nickel from oxidation. ENIG provides a flat, smooth surface with a matte gold color.
HASL vs ENIG: 10 Key Differences
1. Flatness and Coplanarity
One of the biggest differences between HASL and ENIG is the surface flatness. HASL surfaces have an uneven topography with noticeable bumps due to the hot air leveling process. Solder thickness can vary from 1 to 25 µm. In contrast, ENIG provides an exceptionally flat and smooth surface finish (<0.5 µm variance), making it suitable for fine-pitch components and high-density interconnects.
Surface Finish | Flatness | Suitable for Fine-Pitch |
---|---|---|
HASL | Uneven (1-25 µm) | Not ideal |
ENIG | Flat (<0.5 µm) | Yes |
2. Cost
HASL is generally less expensive than ENIG. The raw materials (tin-lead solder) and process for HASL are simpler and more established. ENIG requires additional steps, chemicals, and control, making it a more costly option. However, the price difference has narrowed in recent years.
3. Lead-Free Compatibility
With the RoHS directive and the push towards lead-free electronics, ENIG has become a popular choice. ENIG is inherently lead-free, while HASL traditionally used lead-based solder. Lead-free HASL options are available (SN100C, SAC305) but require higher temperatures and more precise control.
4. Durability and Shelf Life
ENIG offers better durability and longer shelf life compared to HASL. The nickel layer in ENIG provides excellent wear and corrosion resistance. The gold layer prevents nickel oxidation, allowing ENIG PCBs to be stored for over 12 months without degradation. HASL surfaces are prone to oxidation and have a shelf life of around 6 months.
Surface Finish | Shelf Life | Durability |
---|---|---|
HASL | ~6 months | Moderate |
ENIG | >12 months | High |
5. Solderability
Both HASL and ENIG provide good solderability. HASL has a long history of reliable soldering performance. The solder wets easily to the surface during assembly. ENIG also offers excellent solderability, with the gold layer promoting good wetting. However, the gold must be completely dissolved into the solder joint to avoid embrittlement.
6. Reworkability
HASL is generally easier to rework than ENIG. The solder on a HASL surface can be easily reflowed and components removed. Reworking ENIG requires more care, as excessive heat can cause the nickel layer to dissolve into the solder joint, weakening it. Proper profile and technique are critical.
7. Solder Joint Appearance
HASL solder joints have a shiny, dome-shaped appearance due to the solder fillets. ENIG solder joints tend to be flatter and have a matte appearance. The gold layer also imparts a slightly pinkish color to the joint. While not affecting reliability, the aesthetic differences may matter in certain applications.
8. Bonding and Adhesion
ENIG provides a better surface for wire bonding and adhesion compared to HASL. The flat surface and gold layer of ENIG promote reliable bonding of wires and adhesives. The uneven topography of HASL can pose challenges for fine-pitch bonding and certain adhesives.
9. Electrical Performance
ENIG offers slightly better electrical performance than HASL. The nickel layer in ENIG provides a barrier against copper migration, which can cause short circuits. The smooth surface also reduces high-frequency signal loss. HASL solder bumps can cause impedance discontinuities.
10. Solder Mask Compatibility
HASL can occasionally cause issues with solder mask adhesion due to the high temperatures involved (260-270°C). The thermal shock can lead to solder mask cracking or delamination. ENIG processes use lower temperatures (85-90°C) and are gentler on the solder mask, ensuring better long-term adhesion.
HASL vs ENIG: Which to Choose?
The choice between HASL and ENIG depends on the specific requirements of your PCB application. Consider the following factors:
- Fine-pitch components and high-density designs: Choose ENIG for its flat surface.
- Lead-free requirements: ENIG is inherently lead-free, while HASL requires special alloys.
- Cost constraints: HASL is generally less expensive than ENIG.
- Shelf life and durability: ENIG offers longer shelf life and better wear resistance.
- Rework requirements: HASL is easier to rework than ENIG.
- Wire bonding or adhesives: ENIG provides a better surface for bonding.
In many cases, a mix of HASL and ENIG can be used on different areas of the same PCB, leveraging the strengths of each surface finish.
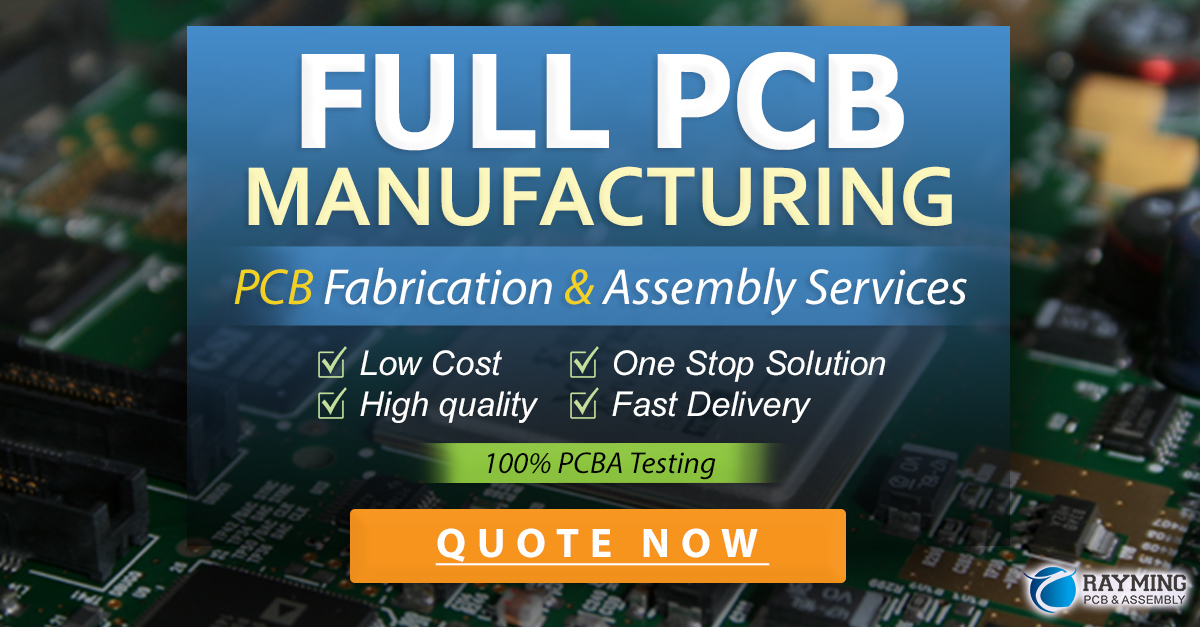
FAQ
1. Can HASL be used for lead-free PCB assembly?
Yes, lead-free HASL options like SN100C and SAC305 are available. However, they require higher process temperatures and more precise control compared to leaded HASL.
2. Is ENIG always more expensive than HASL?
While ENIG is generally more expensive than HASL due to the additional process steps and materials, the price difference has narrowed in recent years. The cost gap is not as significant as it once was.
3. How long can HASL and ENIG PCBs be stored before assembly?
HASL PCBs have a shelf life of around 6 months before oxidation starts to degrade solderability. ENIG PCBs can be stored for over 12 months without significant degradation, thanks to the protective nickel and gold layers.
4. Can HASL and ENIG be used together on the same PCB?
Yes, it’s possible to use HASL and ENIG selectively on different areas of the same PCB. This allows designers to leverage the strengths of each surface finish where needed, such as using ENIG for fine-pitch components and HASL for larger pads.
5. What is black pad syndrome, and which surface finish is affected?
Black pad syndrome is a defect that can occur with ENIG surface finish, where the nickel layer becomes overly porous and brittle, leading to weak solder joints. It appears as dark, grainy pads. Proper process control and using a thin gold layer (<0.1 µm) can help mitigate this issue. HASL is not affected by black pad syndrome.
Leave a Reply