The Importance of Wiring Harness Labels
Identification and Traceability
Labeling wires in a wiring harness is essential for identification and traceability purposes. In complex systems with numerous wires, labels help technicians quickly identify specific wires and their corresponding functions. This is particularly important during troubleshooting, maintenance, and repair processes, as it allows technicians to pinpoint issues and make necessary repairs efficiently.
Wiring harness labels typically include information such as:
- Wire gauge
- Wire color
- Circuit number
- Connector type
- Terminal type
By providing this information, labels enable technicians to easily trace wires from one point to another, saving time and reducing the risk of errors.
Standardization and Consistency
Implementing a standardized labeling system for wiring harnesses ensures consistency across different projects and teams. When all wires are labeled using the same format and terminology, it becomes easier for technicians to understand and work with the harnesses, regardless of their experience level or familiarity with the specific project.
Standardized labeling also facilitates better communication between different departments, such as design, manufacturing, and quality control. By using a common language, teams can collaborate more effectively, reducing the likelihood of misunderstandings and errors.
Quality Control and Compliance
Wiring harness labels play a crucial role in quality control and compliance. Many industries have strict regulations and standards that govern the design, manufacturing, and installation of wiring harnesses. These standards often include requirements for labeling, such as the format, content, and durability of the labels.
By adhering to these standards and regulations, manufacturers can ensure that their wiring harnesses meet the necessary quality and safety requirements. This not only helps to prevent potential hazards but also demonstrates the manufacturer’s commitment to producing high-quality products that comply with industry standards.
Efficiency in Manufacturing and Assembly
Labeling wires during the manufacturing process can significantly improve efficiency and accuracy. Clear and consistent labels help assembly line workers quickly identify the correct wires and components, reducing the time spent on searching and sorting. This streamlined process minimizes the risk of assembly errors, which can lead to costly rework and delays.
In addition, labeled wiring harnesses are easier to package and ship, as the labels provide clear instructions for handling and installation. This can help to reduce damage during transportation and ensure that the harnesses are installed correctly at their final destination.
Types of Wiring Harness Labels
There are various types of wiring harness labels available, each with its own advantages and applications. The choice of label type depends on factors such as the operating environment, the size of the wires, and the durability requirements. Some common types of wiring harness labels include:
Heat-Shrink Labels
Heat-shrink labels are made from a material that shrinks when exposed to heat, forming a tight and secure fit around the wire. These labels are highly durable and resistant to abrasion, chemicals, and extreme temperatures. Heat-shrink labels are ideal for applications where the wires are exposed to harsh environments or where a permanent and tamper-evident labeling solution is required.
Adhesive Labels
Adhesive labels are self-adhesive labels that can be easily applied to the surface of the wire. These labels are available in various sizes, colors, and materials, making them suitable for a wide range of applications. Adhesive labels are quick and easy to apply, making them a popular choice for many manufacturers. However, they may not be as durable as heat-shrink labels and can be prone to peeling or fading over time.
Flag Labels
Flag labels are designed to be wrapped around the wire, with a flag-like portion extending outward for easy identification. These labels are ideal for applications where the wires need to be easily identifiable from a distance or where the labels need to be read from multiple angles. Flag labels can be made from various materials, including paper, vinyl, and polyester, depending on the durability requirements.
Sleeve Labels
Sleeve labels are tubular labels that are slipped over the wire and secured in place. These labels provide a 360-degree view of the label information, making them easily readable from any angle. Sleeve labels are available in various materials, including heat-shrink and non-heat-shrink options, and can be printed with text, barcodes, or graphics.
Labeling Techniques and Best Practices
To ensure the effectiveness and longevity of wiring harness labels, it is essential to follow best practices during the labeling process. Some key considerations include:
Label Placement
Labels should be placed in a consistent and easily accessible location on the wire. The placement should be such that the label is visible and readable without the need to manipulate the wire or the surrounding components. In some cases, it may be necessary to use multiple labels along the length of the wire to ensure visibility and traceability.
Label Durability
The durability of the label is critical, especially in harsh operating environments. Factors such as temperature, humidity, chemicals, and abrasion can all affect the longevity of the label. It is important to choose a label material and printing method that can withstand the specific environmental conditions of the application.
Legibility and Readability
The information on the label must be clear, legible, and easily readable. This requires the use of appropriate font sizes, colors, and contrasts. In some cases, it may be necessary to use machine-readable formats, such as barcodes or QR codes, to facilitate automatic data capture and tracking.
Consistency and Standardization
Consistency and standardization are key to effective wiring harness labeling. This involves using a consistent format, terminology, and color-coding scheme across all labels. Standardization helps to reduce confusion and errors, while also facilitating better communication and collaboration between teams.
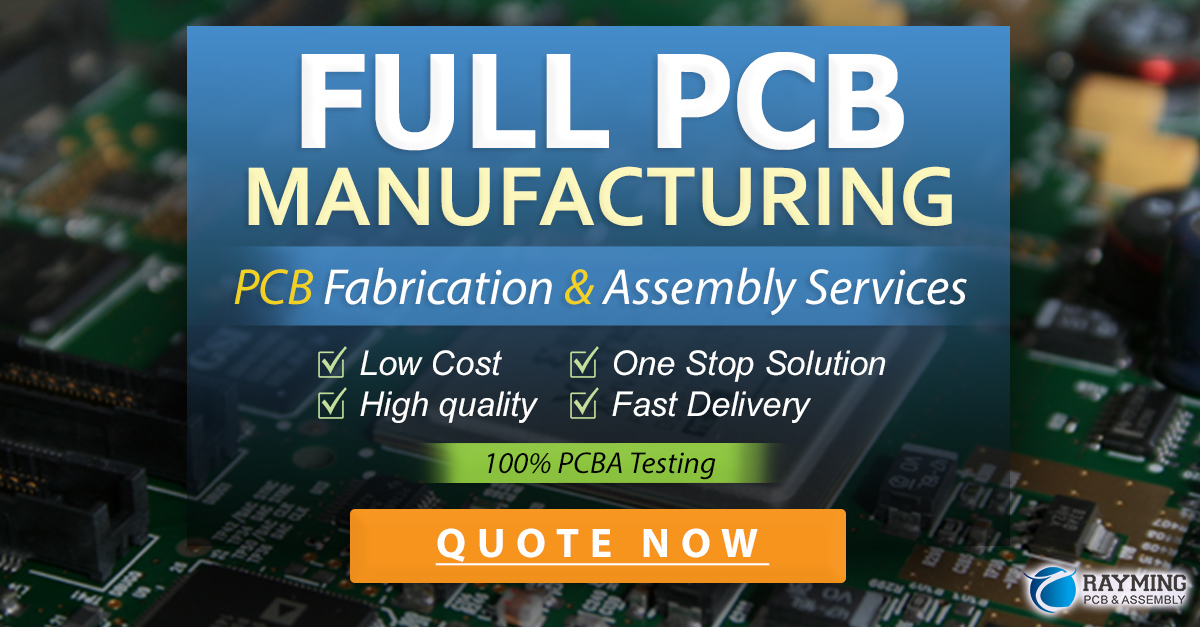
Frequently Asked Questions (FAQ)
-
What information should be included on a wiring harness label?
A wiring harness label should typically include information such as the wire gauge, wire color, circuit number, connector type, and terminal type. Additional information may be included depending on the specific application and industry standards. -
How do I choose the right type of label for my wiring harness?
The choice of label type depends on factors such as the operating environment, the size of the wires, and the durability requirements. Heat-shrink labels are ideal for harsh environments and applications requiring permanent and tamper-evident labeling. Adhesive labels are quick and easy to apply but may not be as durable. Flag labels are suitable for easy identification from a distance, while sleeve labels provide a 360-degree view of the label information. -
Can I print my own wiring harness labels?
Yes, it is possible to print your own wiring harness labels using a suitable label printer and software. However, it is important to ensure that the labels meet the necessary durability and legibility requirements for your specific application. In some cases, it may be more cost-effective and reliable to purchase pre-printed labels from a specialized supplier. -
How can I ensure the durability of my wiring harness labels?
To ensure the durability of your wiring harness labels, choose a label material and printing method that can withstand the specific environmental conditions of your application. This may involve using heat-shrink labels, UV-resistant materials, or laminated labels. It is also important to follow best practices for label placement and handling to minimize the risk of damage or deterioration. -
What are the benefits of using standardized wiring harness labeling?
Standardized wiring harness labeling offers several benefits, including improved identification and traceability, enhanced communication and collaboration between teams, and increased efficiency in manufacturing and assembly processes. Standardization also helps to ensure compliance with industry regulations and quality control requirements, reducing the risk of errors and potential hazards.
Conclusion
Wiring harness labels are essential components in the design, manufacturing, and maintenance of electrical systems. By providing clear and consistent identification of wires and their functions, labels facilitate efficient troubleshooting, repairs, and assembly processes. Labeling also plays a crucial role in quality control and compliance, ensuring that wiring harnesses meet the necessary industry standards and regulations.
When implementing a wiring harness labeling system, it is important to consider factors such as label type, placement, durability, and legibility. By following best practices and standardizing labeling processes, manufacturers can improve efficiency, reduce errors, and enhance the overall quality of their products.
As the complexity of electrical systems continues to grow, the importance of effective wiring harness labeling will only increase. By investing in robust labeling solutions and processes, manufacturers can position themselves to meet the evolving demands of their industries and deliver high-quality, reliable products to their customers.
Leave a Reply