Introduction to Windmill Power
Windmill power, also known as wind power, is a renewable energy source that harnesses the kinetic energy of wind to generate electricity. Wind turbines, the modern equivalent of traditional windmills, convert the wind’s kinetic energy into electrical energy through the rotation of blades connected to a generator. As the world increasingly shifts towards sustainable energy solutions, windmill power has gained significant attention as a clean and abundant alternative to fossil fuels.
In this article, we will delve into the process of building an electricity-producing wind turbine, exploring the key components, design considerations, and steps involved in harnessing the power of the wind.
Understanding the Basics of Wind Energy
Before we dive into the construction of a wind turbine, it’s essential to understand the fundamental principles behind wind energy. Wind is caused by the uneven heating of the Earth’s surface by the sun, which creates differences in atmospheric pressure. As air moves from areas of high pressure to areas of low pressure, wind is generated.
The energy contained in the wind is proportional to the cube of its speed. This means that even a small increase in wind speed can lead to a significant increase in the available energy. The power that can be extracted from the wind is given by the following equation:
P = 0.5 × ρ × A × v³
Where:
– P is the power in watts (W)
– ρ (rho) is the air density in kilograms per cubic meter (kg/m³)
– A is the swept area of the turbine blades in square meters (m²)
– v is the wind speed in meters per second (m/s)
Wind Speed and Power Density
The following table illustrates the relationship between wind speed and power density:
Wind Speed (m/s) | Power Density (W/m²) |
---|---|
5 | 65 |
6 | 132 |
7 | 225 |
8 | 355 |
9 | 531 |
10 | 763 |
As evident from the table, higher wind speeds result in significantly higher power densities, emphasizing the importance of selecting a location with favorable wind conditions for optimal energy generation.
Key Components of a Wind Turbine
A wind turbine consists of several essential components that work together to convert wind energy into electrical energy. Let’s take a closer look at each of these components:
1. Rotor Blades
The rotor blades are the most visible and iconic parts of a wind turbine. They are designed to capture the wind’s kinetic energy and convert it into rotational motion. Modern wind turbine blades are typically made from composite materials, such as fiberglass or carbon fiber, to ensure strength, durability, and lightweight properties.
The length and shape of the blades play a crucial role in determining the turbine’s efficiency and power output. Longer blades can capture more wind energy, but they also increase the overall size and cost of the turbine. The aerodynamic design of the blades helps optimize the lift and minimize drag forces, ensuring efficient energy capture.
2. Nacelle
The nacelle is the housing that sits atop the tower and contains the main mechanical and electrical components of the wind turbine. It serves as a protective enclosure for the gearbox, generator, and other critical components.
The nacelle is designed to rotate on top of the tower, allowing the rotor blades to face the wind direction for optimal energy capture. This rotation is facilitated by a yaw system, which uses motors and sensors to adjust the nacelle’s orientation based on the prevailing wind conditions.
3. Gearbox
The gearbox is a mechanical component located inside the nacelle that plays a vital role in converting the low-speed rotational motion of the rotor blades into high-speed rotation suitable for the generator. Wind turbine rotor blades typically rotate at speeds between 10 to 25 revolutions per minute (RPM), while generators require much higher speeds, usually around 1,500 RPM or more, to efficiently generate electricity.
The gearbox consists of a series of gears that increase the rotational speed while reducing the torque. This speed increase allows the generator to operate at its optimal efficiency. However, gearboxes are complex components that require regular maintenance and are susceptible to wear and tear over time.
4. Generator
The generator is the heart of the wind turbine, responsible for converting the mechanical energy from the rotor blades into electrical energy. There are two main types of generators used in wind turbines: synchronous generators and asynchronous (induction) generators.
Synchronous generators are directly connected to the electrical grid and operate at a constant speed determined by the grid frequency. They require a gearbox to match the rotor speed to the grid frequency. On the other hand, asynchronous generators, also known as induction generators, can operate at variable speeds and do not require a direct connection to the grid. They are simpler, more robust, and less expensive compared to synchronous generators.
The choice of generator depends on various factors, including the turbine size, grid requirements, and overall system design.
5. Tower
The tower is the structure that supports the nacelle and rotor blades at a suitable height above the ground. Wind turbine towers are typically made from steel or concrete and can range in height from 50 meters to over 100 meters, depending on the turbine size and wind conditions at the site.
Taller towers allow the turbine to access stronger and more consistent winds at higher altitudes, resulting in increased energy production. However, taller towers also increase the overall cost and complexity of the wind turbine installation.
The tower must be designed to withstand the significant structural loads imposed by the weight of the nacelle and rotor blades, as well as the wind forces acting on the turbine. Proper foundation design is crucial to ensure the stability and longevity of the wind turbine.
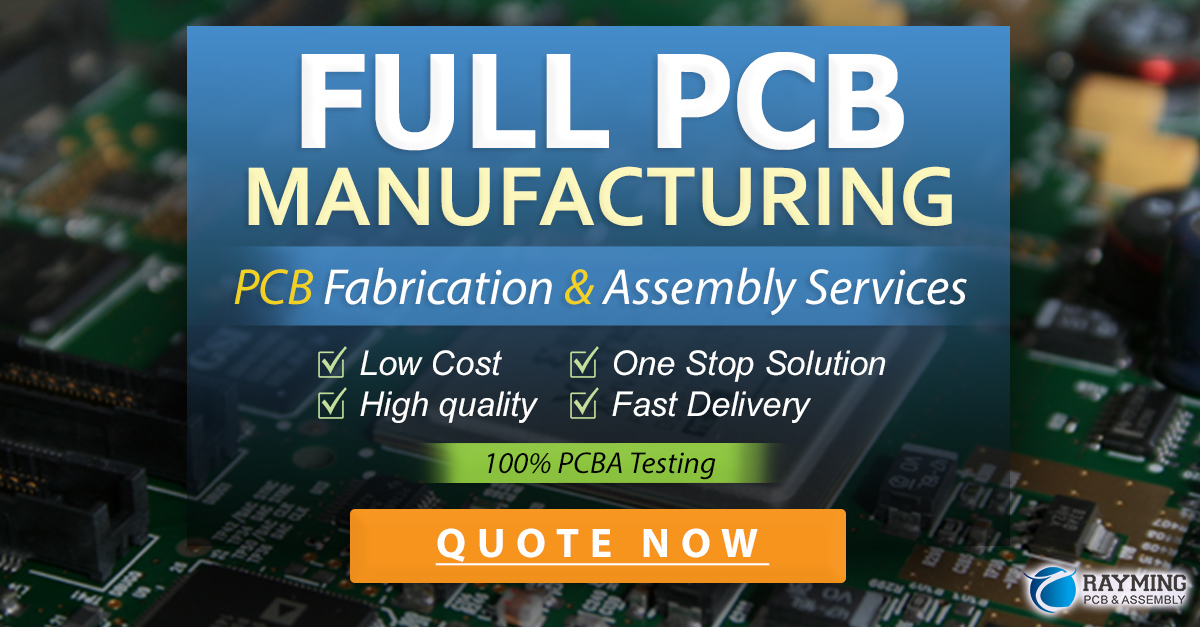
Designing and Building a Wind Turbine
Building an electricity-producing wind turbine involves several key steps, from site selection and design to manufacturing and installation. Let’s explore each of these steps in detail:
1. Site Selection
Choosing an appropriate site for a wind turbine is crucial for maximizing energy production and minimizing environmental impact. Several factors should be considered when selecting a site:
a. Wind Resource Assessment: Conduct a thorough analysis of the wind speed, direction, and consistency at the potential site. Wind data should be collected over an extended period, typically one year or more, to account for seasonal variations.
b. Terrain and Obstacles: Assess the surrounding terrain and identify any obstacles that could obstruct or disturb the wind flow, such as trees, buildings, or hills. Wind turbines should be placed in open areas with minimal turbulence for optimal performance.
c. Accessibility: Consider the accessibility of the site for construction, maintenance, and grid connection. The site should have suitable roads and infrastructure to facilitate the transportation of turbine components and equipment.
d. Environmental Impact: Evaluate the potential environmental impact of the wind turbine on the local ecosystem, including wildlife, noise levels, and visual aesthetics. Consult with local authorities and communities to ensure compliance with regulations and minimize any adverse effects.
2. Turbine Design
Once the site has been selected, the next step is to design the wind turbine based on the specific site conditions and energy requirements. The design process involves several key considerations:
a. Turbine Size: Determine the appropriate size of the wind turbine based on the available wind resource, energy demand, and site constraints. Larger turbines generally have higher power output but also require more space and investment.
b. Blade Design: Select the optimal blade design, including the length, shape, and material, to maximize energy capture and efficiency. Advanced computational fluid dynamics (CFD) simulations and wind tunnel tests can help optimize the blade design.
c. Tower Height: Determine the appropriate tower height based on the wind profile at the site and the turbine size. Taller towers generally provide access to stronger and more consistent winds but also increase the overall cost and complexity of the installation.
d. Electrical System: Design the electrical system, including the generator, power electronics, and grid connection, to efficiently convert the mechanical energy into electrical energy and feed it into the grid or local power network.
3. Component Manufacturing
Once the turbine design is finalized, the next step is to manufacture the various components of the wind turbine. This process involves several specialized industries and requires precise engineering and quality control:
a. Blade Manufacturing: The rotor blades are typically manufactured using composite materials, such as fiberglass or carbon fiber, through processes like resin infusion or prepreg layup. The blades undergo rigorous testing to ensure structural integrity and aerodynamic performance.
b. Nacelle and Gearbox Manufacturing: The nacelle and gearbox components are manufactured using high-quality steel and other materials. Precise machining and assembly processes ensure the proper fit and function of these critical components.
c. Tower Manufacturing: The tower sections are fabricated from steel or concrete, depending on the design. Steel towers are typically manufactured in segments and assembled on-site, while concrete towers may be cast in place or precast and transported to the site.
4. Installation and Commissioning
The final step in building a wind turbine is the on-site installation and commissioning process. This involves several key activities:
a. Foundation Construction: Prepare the foundation for the wind turbine tower based on the soil conditions and structural requirements. The foundation must be designed to withstand the significant loads imposed by the turbine and ensure long-term stability.
b. Tower Erection: Assemble and erect the tower sections using cranes and specialized lifting equipment. Ensure proper alignment and secure bolting of the tower segments.
c. Nacelle and Rotor Installation: Lift and install the nacelle and rotor assembly onto the top of the tower. Connect the electrical and control systems between the nacelle and the tower.
d. Commissioning and Testing: Perform comprehensive testing and commissioning of the wind turbine to ensure proper operation, safety, and performance. This includes mechanical, electrical, and control system checks, as well as power output and grid integration tests.
Frequently Asked Questions (FAQ)
-
What is the typical lifespan of a wind turbine?
Modern wind turbines are designed to operate for 20 to 25 years with proper maintenance and servicing. After this period, the turbines may be refurbished, repowered, or decommissioned, depending on their condition and the economics of continued operation. -
How much land is required for a wind turbine installation?
The land requirement for a wind turbine varies depending on the turbine size and the layout of the wind farm. While the actual footprint of a single turbine is relatively small, larger setbacks are required to minimize turbulence and wake effects between turbines. A general rule of thumb is to space turbines at least 3-5 rotor diameters apart in the prevailing wind direction and 5-10 rotor diameters apart in the crosswind direction. -
Can wind turbines operate in extreme weather conditions?
Modern wind turbines are designed to withstand extreme weather conditions, such as high winds, lightning strikes, and icing. They are equipped with sophisticated control systems that can adjust the blade pitch and orientation to protect the turbine components from damage. In case of severe weather events, the turbines can be shut down temporarily to ensure safety and prevent damage. -
How much noise do wind turbines generate?
Wind turbines generate some noise during operation, primarily from the mechanical components and the aerodynamic sound of the blades. However, modern wind turbines have significantly reduced noise levels compared to earlier designs. At a distance of 300 meters, the sound level from a wind turbine is typically around 40-50 decibels, which is comparable to the noise level of a quiet room or a gentle breeze. -
What is the efficiency of wind turbines in converting wind energy to electricity?
The efficiency of wind turbines in converting wind energy to electricity is measured by the power coefficient (Cp). The theoretical maximum efficiency, known as the Betz limit, is approximately 59.3%. However, in practice, wind turbines typically achieve efficiencies in the range of 35-45% due to various losses and design constraints. Ongoing research and development efforts aim to further improve the efficiency of wind turbines.
Conclusion
Building an electricity-producing wind turbine is a complex process that involves various disciplines, including engineering, materials science, and environmental studies. From site selection and turbine design to component manufacturing and installation, each step requires careful planning, expertise, and adherence to best practices.
As the world continues to transition towards sustainable energy solutions, wind power will play an increasingly important role in meeting our energy needs. Ongoing advancements in wind turbine technology, such as larger and more efficient designs, improved materials, and advanced control systems, will further enhance the economic and environmental viability of wind energy.
By understanding the principles behind windmill power and the process of building wind turbines, we can appreciate the immense potential of this renewable energy source in powering our homes, industries, and communities while reducing our reliance on fossil fuels and combating climate change.
Leave a Reply