Introduction
Flex PCB (Flexible Printed Circuit Board), also known as flex circuits, is a technology that enables flexible connections between electronic components. Unlike rigid PCBs, flex PCBs can bend and flex to accommodate different product shapes and spaces. This flexibility comes at a price – flex PCBs are generally much more expensive than their rigid counterparts. In this article, we will examine the reasons behind the high costs of flex PCBs and provide some guidance on managing those costs.
What is a Flex PCB?
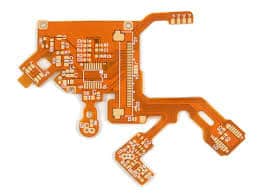
A flex PCB uses flexible substrates like polyimide rather than traditional rigid substrates like FR-4. By removing the fiberglass reinforcement, the PCB can bend and flex while still retaining its electrical connectivity. Components are mounted on the surface of the flex PCB and can move dynamically along with the bending substrate.
Some key properties and advantages of flex PCBs:
- Can conform to different shapes and spaces
- Dynamic flexing and bending
- Thin and lightweight
- Durable under bending strains
- Allows for compact, efficient products
- Can integrate rigid and flex PCBs together
Flex PCBs are commonly used in products like mobile phones, medical devices, automotive electronics, wearables and other applications where flexibility and space efficiency are needed.
Why are Flex PCBs More Expensive than Rigid PCBs?
There are several factors that contribute to the higher fabrication costs of flex PCBs compared to standard rigid PCBs:
1. Base Material Costs
The flexible substrate materials used in flex PCBs like polyimide and PI are more expensive than the rigid FR-4 substrates used in traditional PCBs. Polyimide costs between 5-10 times more per square foot than FR-4.
2. Complex Manufacturing Process
Producing flex PCBs requires more complex fabrication steps than rigid PCBs. The flexible materials need special handling and processing to create the circuits. Steps like lamination, coverlay application and flexible etching/cutting all add to production costs.
3. Lower Economies of Scale
Rigid PCB production has been highly optimized over decades for mass production. Flex PCBs have more specialized uses and lower volume production, preventing manufacturers from achieving the same economies of scale as rigid PCBs. This gets reflected in the pricing.
4. Testing and Compatibility Requirements
The dynamic flexing of flex PCBs requires more extensive testing to ensure proper functionality. Parameters like bend radius, cyclic bending endurance, electrical connectivity during flexing need rigorous testing.
5. Design Overhead
Designing flex PCB layouts requires accounting for flexibility and thermal expansion of the substrate. This demands more complex design principles and PCB design software capabilities.
6. Lower Yields
The specialized materials and fabrication processes involved result in lower yields and higher reject rates in flex PCB manufacturing. Manufacturers factor these losses into flex PCB pricing.
Typical Cost Comparison Between Flex PCBs and Rigid PCBs
Here is a typical per unit cost comparison between rigid and flex PCBs of similar size and layer count:
PCB Type | Layers | Unit Cost |
---|---|---|
Rigid PCB | 4 | $100 |
Flex PCB | 4 | $500 |
As evident from the table, the flex PCB is almost 5 times more expensive for the same specifications. This cost factor holds true over most variations of PCB sizes, layer counts and quantities.
Strategies for Reducing Flex PCB Costs
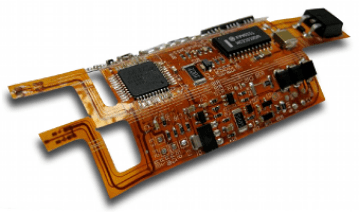
While flex PCB costs are inherently higher, here are some ways to manage those costs:
- Optimize design to minimize flex area – Concentrate flex areas and connections to regions that strictly require it. This reduces overall flexible substrate requirements.
- Build rigid sections on flex – Rigid sections like component mounting areas and connectors can be built onto the flex PCB itself instead of using an additional rigid PCB. This improves reliability and reduces interconnect costs.
- Standardize designs – Standardize certain flex PCB elements across your products, like outlines, bends and component areas. This improves manufacturing efficiency.
- Work with flex PCB specialists – Use a flex PCB company specializing in high mix/flex volumes. Avoid companies geared to high volume/low mix rigid boards.
- Consider panelization – Panelizing multiple flex PCB designs together can improve fabrication efficiency and lower costs. But this requires caution to avoid compromising quality.
- Optimize layer stackup – Minimize layer count by careful layout planning. Reduce layers if possible. Build flex-rigid hybrids selectively.
- Evaluate advanced flex materials – Newer flex substrate materials like polyester-based flex can offer cost savings in certain applications.
- Look for alternative flex technologies – Emerging flex technologies like molded interconnect devices (MID) allow integration of flex and electronics into plastic moldings.
- Leverage design software features – Use flex-aware design tools that simplify flex modeling, visualization, DFM and library management.
FQA
What is a flex PCB?
A flex PCB uses flexible substrate materials like polyimide rather than rigid materials like FR-4. This allows the PCB to dynamically bend and flex while retaining electrical functionality. Components mount on the surface.
Why are flex PCBs more complex to manufacture?
They require specialized materials, handling and fabrication steps like flexible etching and lamination. The flex materials also have lower yields and higher reject rates.
Does flex PCB size affect cost?
Yes, larger flex PCBs require more raw flexible substrate material, driving up base costs. But cost per unit area is still higher than rigid PCBs.
Can flex PCBs substitute interconnect cables?
Yes, flex PCB interconnects often replace ribbon cables, wire harnesses and connectors between PCBs. This improves reliability and compactness.
Are there design principles unique to flex PCBs?
Yes, flex PCB layouts require managing factors like dynamic flex, thermal expansion, bend radius, component placement and rigid-flex optimization.
Conclusion
Flex PCBs enable innovative and compact product designs, but come at a significant cost premium versus standard rigid PCBs. The specialized materials, manufacturing processes and lower production volumes contribute to the higher fabrication costs. With careful design optimization, cost-reduction technologies and selecting the right flex PCB partner, some of this cost impact can be alleviated. But the intrinsic benefits of miniaturization and dynamic flexibility afforded by flex circuits still provide an overall value advantage in the right applications.
Leave a Reply