What is a White PCB?
A white PCB, also known as a solder mask white PCB or a white solder mask PCB, is a printed circuit board that features a white solder mask layer instead of the more common green color. The white solder mask gives the PCB a unique appearance and provides several advantages over traditional green PCBs.
Advantages of White PCBs
- Improved Aesthetics: White PCBs have a clean and modern look that can enhance the visual appeal of electronic devices, especially in consumer products.
- Enhanced Contrast: The white background provides better contrast for component labels and silk screen markings, making them easier to read and inspect.
- Increased Reflectivity: White solder mask reflects more light than green, which can be beneficial for applications that require better visibility or optical performance.
- Better Heat Dissipation: White PCBs can dissipate heat more efficiently than green PCBs due to their higher reflectivity, which can help improve the overall thermal performance of the device.
Manufacturing Process of White PCBs
The manufacturing process of white PCBs is similar to that of standard green PCBs, with a few key differences in the solder mask application stage.
PCB Fabrication Steps
- Design: The PCB layout is designed using CAD software, taking into account the specific requirements of the white solder mask.
- Material Selection: The appropriate substrate material, typically FR-4, is chosen based on the application and desired properties of the PCB.
- Copper Etching: The designed circuit pattern is etched onto the copper-clad substrate using a photolithography process.
- Drilling: Holes are drilled into the PCB for component mounting and via connections.
- Plating: The drilled holes are plated with copper to establish electrical connections between layers.
- Solder Mask Application: A white solder mask ink is applied to the PCB surface, covering the areas that do not require soldering. The white ink is then cured using UV light or heat.
- Surface Finish: A surface finish, such as HASL, ENIG, or immersion silver, is applied to the exposed copper areas to protect them from oxidation and enhance solderability.
- Silkscreen: The component labels and other markings are printed onto the white solder mask using a silkscreen process.
- Electrical Testing: The completed PCB undergoes electrical testing to ensure proper functionality and adherence to specifications.
Challenges in White PCB Manufacturing
While white PCBs offer several benefits, there are some challenges associated with their manufacturing process:
- Solder Mask Formulation: Developing a suitable white solder mask ink that provides good coverage, adhesion, and durability can be more challenging than formulating standard green solder masks.
- Curing Process: White solder masks may require different curing parameters compared to green solder masks, such as longer exposure times or higher temperatures, to achieve optimal properties.
- Contamination Control: White PCBs are more susceptible to visible contamination due to their light color, requiring stricter cleanliness standards during manufacturing and handling.
Applications of White PCBs
White PCBs find applications in various industries and products where aesthetics, contrast, or reflectivity are important factors.
Consumer Electronics
White PCBs are commonly used in consumer electronic devices, such as:
- Smartphones and tablets
- Laptops and computers
- Wearable devices
- Smart home appliances
- Gaming consoles and controllers
The white color of the PCB complements the design of these devices and provides a premium look and feel.
Lighting and Optoelectronics
White PCBs are also used in lighting and optoelectronic applications, where their reflective properties can enhance the performance of the device. Examples include:
- LED lighting fixtures
- Optical sensors and detectors
- Display backlighting
- Fiber optic communication systems
The white solder mask helps to reflect and distribute light more efficiently, improving the overall output and sensitivity of these devices.
Medical Devices
White PCBs are sometimes used in medical devices, particularly in diagnostic and imaging equipment, due to their high contrast and visibility. The white background makes it easier to identify components and trace connections during assembly and maintenance.
Automotive Electronics
In the automotive industry, white PCBs can be found in various electronic systems, such as:
- Infotainment systems
- Instrument clusters
- Heads-up displays (HUDs)
- Advanced driver assistance systems (ADAS)
The white color of the PCB enhances the readability of displays and indicators, which is crucial for driver safety and user experience.
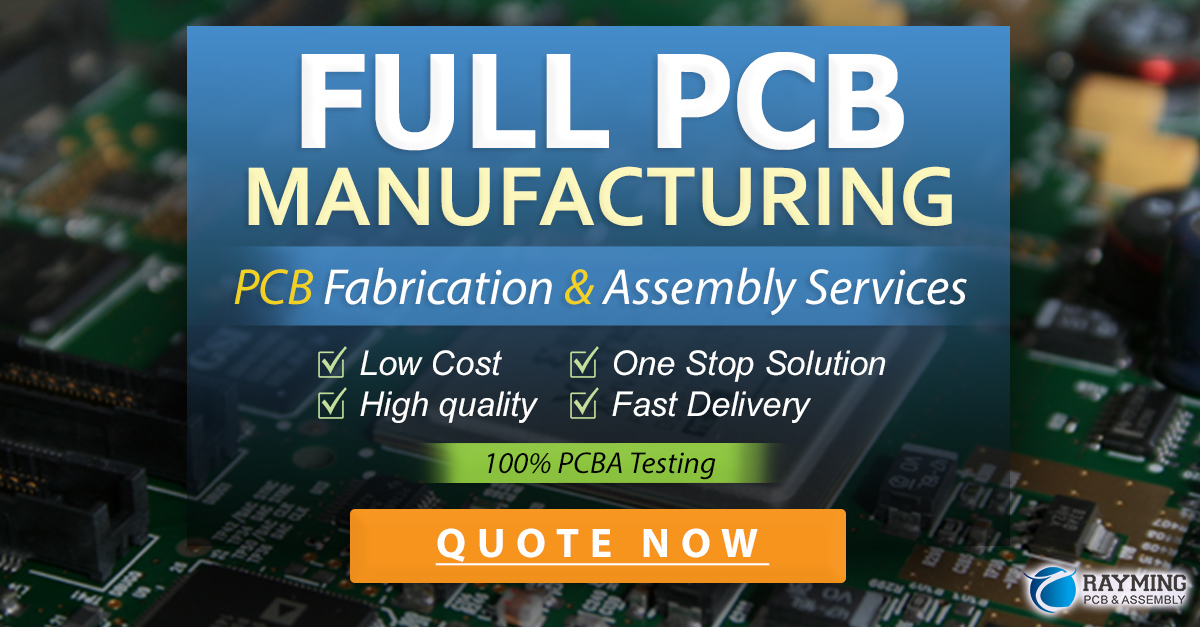
Designing for White PCBs
When designing a white PCB, there are several factors to consider to ensure optimal performance and manufacturability.
Design Guidelines
- Solder Mask Clearance: Ensure sufficient clearance between the solder mask and the copper features to prevent solder mask bleeding or bridging.
- Silkscreen Legibility: Choose appropriate font sizes and colors for the silkscreen to maintain good legibility against the white background.
- Thermal Management: Consider the thermal properties of the white solder mask and adjust the design accordingly, such as increasing the copper area for better heat dissipation.
- Contrast Ratio: Verify that the contrast ratio between the white solder mask and the copper features is sufficient for automated optical inspection (AOI) systems.
CAD Tools and Settings
When creating the PCB layout in CAD software, some specific settings may need to be adjusted for white PCBs:
- Solder Mask Color: Set the solder mask color to white in the CAD tool’s layer properties.
- Silkscreen Color: Choose a suitable silkscreen color, typically black or dark colors, that provides good contrast against the white background.
- Solder Mask Expansion: Adjust the solder mask expansion settings to ensure proper coverage and clearance around the copper features.
Collaborating with PCB Manufacturers
To ensure the successful fabrication of white PCBs, it is essential to collaborate closely with the PCB manufacturer throughout the design and production process.
- Communicate Requirements: Clearly specify the requirements for the white solder mask, including color, finish, and any special considerations.
- Design Review: Request a design review from the manufacturer to identify any potential issues or improvements related to the white PCB design.
- Material Selection: Discuss the available white solder mask options with the manufacturer and select the most suitable one for the application.
- Prototyping: Order Prototype Boards to verify the design, functionality, and appearance of the white PCB before proceeding with mass production.
Testing and Quality Control
Proper testing and quality control measures are crucial to ensure the reliability and performance of white PCBs.
Visual Inspection
White PCBs undergo visual inspection to check for any defects or anomalies, such as:
- Solder mask coverage and uniformity
- Silkscreen legibility and alignment
- Surface contamination or discoloration
- Copper feature integrity and spacing
Automated optical inspection (AOI) systems can be used to perform high-speed, high-resolution inspections of white PCBs.
Electrical Testing
Electrical testing is performed to verify the functionality and performance of the white PCB, including:
- Continuity and isolation testing
- Impedance and capacitance measurements
- Signal integrity and crosstalk analysis
- Functional testing of the assembled PCB
These tests ensure that the white PCB meets the specified electrical requirements and performs as intended in the final application.
Environmental Testing
Depending on the application and the operating environment, white PCBs may need to undergo additional environmental tests, such as:
- Thermal cycling and shock testing
- Humidity and moisture resistance testing
- Vibration and mechanical shock testing
- Salt spray and corrosion testing
These tests help to validate the durability and reliability of the white PCB under various environmental conditions.
Troubleshooting Common Issues
Despite careful design and manufacturing, issues may arise during the production or use of white PCBs. Some common problems and their potential solutions are:
- Solder Mask Discoloration: If the white solder mask appears yellowed or discolored, it may be due to improper curing, contamination, or exposure to UV light. Adjusting the curing process or using a different solder mask formulation can help resolve this issue.
- Silkscreen Legibility: If the silkscreen markings are difficult to read against the white background, consider using a darker silkscreen color or increasing the font size. Alternatively, using a different silkscreen printing method, such as direct legend printing, can improve legibility.
- Solder Mask Adhesion: Poor adhesion of the white solder mask to the PCB surface can lead to delamination or peeling. Ensure proper surface preparation and cleaning before applying the solder mask, and verify the compatibility of the solder mask with the substrate material.
- Electrical Performance: If the white PCB exhibits unexpected electrical behavior, such as signal integrity issues or high impedance, review the design and layout for potential problems. Consult with the PCB manufacturer or a signal integrity specialist to identify and resolve the issue.
Industry Standards and Certifications
When manufacturing and using white PCBs, it is important to adhere to relevant industry standards and certifications to ensure quality, reliability, and compliance.
IPC Standards
The Association Connecting Electronics Industries (IPC) publishes several standards that apply to PCBs, including white PCBs:
- IPC-A-600: Acceptability of Printed Boards
- IPC-6012: Qualification and Performance Specification for Rigid Printed Boards
- IPC-SM-840: Qualification and Performance of Permanent Solder Mask
These standards provide guidelines for the design, fabrication, and inspection of PCBs, ensuring consistent quality and reliability across the industry.
UL Certification
Underwriters Laboratories (UL) is a global safety certification company that tests and certifies products, including PCBs, for safety and performance. White PCBs used in certain applications, such as lighting or medical devices, may require UL certification to ensure compliance with safety standards.
RoHS Compliance
The Restriction of Hazardous Substances (RoHS) directive regulates the use of certain hazardous substances in electrical and electronic equipment. White PCBs must comply with RoHS requirements, ensuring that they do not contain restricted substances above the specified limits.
Future Trends and Developments
As technology advances and new applications emerge, the development and use of white PCBs are expected to evolve. Some potential future trends and developments include:
- Improved Solder Mask Formulations: Ongoing research and development efforts aim to create white solder mask formulations with enhanced properties, such as better adhesion, higher reflectivity, and improved durability.
- Advanced Manufacturing Techniques: New manufacturing techniques, such as inkjet printing or 3D printing, may enable the production of white PCBs with more complex geometries and finer features.
- Expanded Application Areas: White PCBs may find new applications in emerging technologies, such as 5G communication, flexible electronics, or quantum computing, where their unique properties can offer specific advantages.
- Eco-Friendly Materials: The development of more environmentally friendly white solder mask materials, such as those based on bio-derived or recyclable resins, may help reduce the environmental impact of PCB manufacturing.
Conclusion
White PCBs offer a unique combination of aesthetics, functionality, and performance that make them a valuable choice for a wide range of electronic applications. By understanding the manufacturing process, design considerations, and testing requirements, engineers and manufacturers can successfully incorporate white PCBs into their products.
As technology continues to advance, the use of white PCBs is expected to grow and evolve, driven by the demand for visually appealing, high-contrast, and reflective circuit boards. By staying informed about the latest developments and best practices in white PCB manufacturing, the electronics industry can leverage the benefits of this innovative technology to create more compelling and reliable products.
Frequently Asked Questions (FAQ)
1. What is the difference between a white PCB and a standard green PCB?
A white PCB uses a white solder mask instead of the traditional green color, which gives it a distinctive appearance and provides benefits such as improved contrast, reflectivity, and heat dissipation. The manufacturing process and design considerations for white PCBs also differ slightly from those of green PCBs.
2. Are white PCBs more expensive than green PCBs?
Yes, white PCBs are generally more expensive than green PCBs due to the specialized materials and processes required for their manufacture. The cost difference can vary depending on factors such as the PCB complexity, volume, and manufacturer.
3. Can white PCBs be used for all types of electronic devices?
White PCBs can be used in a wide range of electronic devices, but they are particularly well-suited for applications where aesthetics, contrast, or reflectivity are important. Examples include consumer electronics, lighting and optoelectronics, medical devices, and automotive electronics.
4. How do I design a white PCB?
Designing a white PCB involves considering factors such as solder mask clearance, silkscreen legibility, thermal management, and contrast ratio. CAD tools may require specific settings for white PCBs, and it is important to collaborate closely with the PCB manufacturer throughout the design and production process.
5. What testing and quality control measures are used for white PCBs?
White PCBs undergo various testing and quality control measures, including visual inspection, electrical testing, and environmental testing. These tests ensure that the PCBs meet the specified requirements for appearance, functionality, and reliability under different operating conditions.
Leave a Reply