Introduction to Metal Core PCB
A Metal Core PCB (MCPCB) is a type of printed circuit board that uses a metal substrate as the base material instead of the traditional FR-4 material. The metal substrate, usually aluminum, provides excellent thermal conductivity, making it ideal for applications that generate a significant amount of heat, such as high-power LED lighting, power electronics, and automotive systems.
Advantages of Metal Core PCB
- Enhanced thermal management
- Improved electrical performance
- Increased reliability and longevity
- Reduced size and weight
Structure of a Metal Core PCB
A typical Metal Core PCB consists of three main layers:
- Dielectric layer
- Metal core substrate
- Copper circuit layer
Dielectric Layer
The dielectric layer is an electrically insulating material that separates the copper circuit layer from the metal core substrate. It is typically made of a thin, thermally conductive material such as aluminum oxide, boron nitride, or ceramic-filled polymer. The dielectric layer must have the following properties:
- High thermal conductivity
- Electrical insulation
- Good adhesion to both the metal core and copper layer
- Resistance to thermal stress and mechanical damage
Metal Core Substrate
The metal core substrate is the foundation of the MCPCB, providing mechanical support and thermal dissipation. Aluminum is the most commonly used material for the metal core due to its excellent thermal conductivity, lightweight, and low cost. Other materials, such as copper or stainless steel, may be used in specific applications.
The thickness of the metal core substrate can vary depending on the application and the required thermal performance. Typical thicknesses range from 0.5 mm to 3.0 mm.
Copper Circuit Layer
The copper circuit layer is where the electronic components are mounted and interconnected. It is similar to the copper layer in a standard PCB, but with some key differences:
- The copper layer is typically thinner (18-35 μm) to minimize thermal resistance
- The copper layer is usually pre-bonded to the dielectric layer to ensure good adhesion and thermal transfer
- The copper layer may have a higher thermal conductivity than standard PCB copper, such as Copper Invar Copper (CIC) or Copper Molybdenum Copper (CMC)
Manufacturing Process of Metal Core PCB
The manufacturing process of a Metal Core PCB involves several steps:
- Substrate preparation
- Dielectric layer application
- Copper foil lamination
- Circuit pattern imaging and etching
- Solder mask application
- Surface finish
- Cutting and drilling
Substrate Preparation
The aluminum substrate is cleaned and pretreated to remove any surface contaminants and improve adhesion. This may involve chemical cleaning, mechanical abrasion, or anodizing.
Dielectric Layer Application
The dielectric layer is applied to the metal substrate using various methods, such as:
- Screen printing
- Roller coating
- Electrostatic spray coating
- Vacuum lamination
The dielectric layer must be applied evenly and without any voids or defects to ensure good thermal transfer and electrical insulation.
Copper Foil Lamination
The copper foil is laminated to the dielectric layer using heat and pressure. The lamination process must ensure good adhesion between the copper foil and the dielectric layer, without any air gaps or delamination.
Circuit Pattern Imaging and Etching
The desired circuit pattern is transferred to the copper layer using photolithography and etching processes, similar to standard PCB manufacturing.
Solder Mask Application
A solder mask is applied to the copper layer to protect the circuitry from oxidation and short circuits. The solder mask also helps to define the solderable areas for component assembly.
Surface Finish
A surface finish, such as HASL, ENIG, or OSP, is applied to the exposed copper areas to prevent oxidation and improve solderability.
Cutting and Drilling
The final step is to cut the MCPCB to the desired size and shape, and drill any necessary holes for component mounting or mechanical fixation.
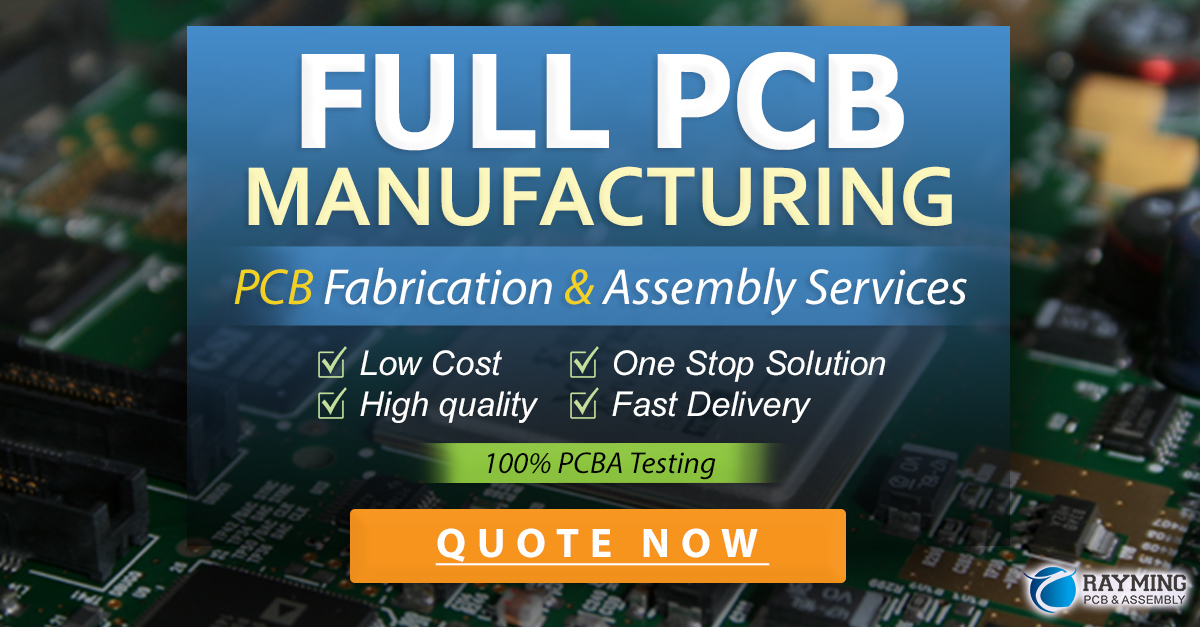
Applications of Metal Core PCB
Metal Core PCBs are used in various applications that require efficient thermal management and high reliability, such as:
- LED lighting
- Power electronics
- Automotive electronics
- Solar energy systems
- Telecommunications equipment
- Medical devices
- Aerospace and defense systems
LED Lighting
Metal Core PCBs are widely used in LED lighting applications, such as street lights, automotive headlights, and high-power LED fixtures. The excellent thermal conductivity of the metal substrate helps to dissipate the heat generated by the LEDs, improving their efficiency, reliability, and lifetime.
Application | Power Density (W/cm²) | Thermal Conductivity (W/mK) |
---|---|---|
LED lighting | 0.5 – 2.0 | 1.0 – 3.0 |
Power Electronics
Power electronic devices, such as MOSFET, IGBT, and power diodes, generate significant amounts of heat during operation. Metal Core PCBs provide an efficient thermal path to dissipate this heat, allowing for higher power densities and improved performance.
Application | Power Density (W/cm²) | Thermal Conductivity (W/mK) |
---|---|---|
Power electronics | 1.0 – 5.0 | 2.0 – 5.0 |
Automotive Electronics
Metal Core PCBs are increasingly used in automotive electronics, such as engine control units, power inverters, and battery management systems. The harsh operating environment and high reliability requirements of automotive applications make MCPCBs an ideal choice.
Application | Power Density (W/cm²) | Thermal Conductivity (W/mK) |
---|---|---|
Automotive electronics | 0.5 – 3.0 | 1.5 – 4.0 |
Design Considerations for Metal Core PCB
When designing a Metal Core PCB, there are several key factors to consider:
- Thermal management
- Dielectric material selection
- Copper thickness and trace width
- Component placement and orientation
- Mechanical constraints
Thermal Management
Thermal management is the primary design consideration for a Metal Core PCB. The following factors influence the thermal performance of an MCPCB:
- Metal substrate material and thickness
- Dielectric material and thickness
- Copper thickness and trace width
- Component power dissipation and placement
- Cooling method (natural convection, forced air, or liquid cooling)
Thermal simulations and measurements should be performed to optimize the thermal design and ensure that the components operate within their specified temperature limits.
Dielectric Material Selection
The dielectric material must be carefully selected based on the application requirements, such as:
- Thermal conductivity
- Dielectric strength
- Thermal expansion coefficient
- Mechanical strength
- Cost
Common dielectric materials for Metal Core PCBs include:
- Aluminum oxide (Al₂O₃)
- Boron nitride (BN)
- Ceramic-filled epoxy
- Polyimide
Copper Thickness and Trace Width
The copper thickness and trace width should be optimized to balance the electrical and thermal performance of the MCPCB. Thicker copper layers provide lower electrical resistance and better thermal conductivity, but may increase the overall thickness and cost of the board.
Trace widths should be designed to minimize thermal resistance while maintaining the required current carrying capacity and signal integrity.
Component Placement and Orientation
Component placement and orientation play a crucial role in the thermal management of a Metal Core PCB. High-power components should be placed close to the metal substrate to minimize the thermal path and improve heat dissipation.
Components should also be oriented to optimize the airflow and minimize any thermal shadowing effects.
Mechanical Constraints
The mechanical constraints of the application, such as size, weight, and mounting requirements, must be considered when designing a Metal Core PCB. The metal substrate may require additional mechanical support or fixation compared to a standard PCB.
The coefficient of thermal expansion (CTE) of the metal substrate should also be considered to ensure compatibility with the components and avoid any mechanical stress or deformation during temperature cycling.
FAQ
1. What is the difference between a Metal Core PCB and a standard PCB?
A Metal Core PCB uses a metal substrate (usually aluminum) as the base material, while a standard PCB uses an FR-4 material. The metal substrate provides better thermal conductivity and heat dissipation compared to FR-4.
2. What are the advantages of using a Metal Core PCB?
The main advantages of using a Metal Core PCB are:
– Improved thermal management and heat dissipation
– Higher power density and reliability
– Reduced size and weight compared to standard PCBs with heatsinks
– Better mechanical stability and durability
3. What are the common applications of Metal Core PCBs?
Metal Core PCBs are commonly used in applications that generate significant amounts of heat, such as:
– LED lighting
– Power electronics
– Automotive electronics
– Solar energy systems
– Telecommunications equipment
4. How do I select the right dielectric material for my Metal Core PCB?
The dielectric material should be selected based on the application requirements, such as thermal conductivity, dielectric strength, thermal expansion coefficient, mechanical strength, and cost. Common dielectric materials include aluminum oxide, boron nitride, ceramic-filled epoxy, and polyimide.
5. What are the key design considerations for a Metal Core PCB?
The key design considerations for a Metal Core PCB are:
– Thermal management (metal substrate, dielectric material, copper thickness, and component placement)
– Dielectric material selection based on application requirements
– Copper thickness and trace width optimization for electrical and thermal performance
– Component placement and orientation for optimal heat dissipation and airflow
– Mechanical constraints, such as size, weight, and mounting requirements
Conclusion
Metal Core PCBs offer significant advantages over standard PCBs in applications that require efficient thermal management and high reliability. By understanding the structure, manufacturing process, and design considerations of MCPCBs, engineers can create optimized solutions for a wide range of applications, from LED lighting to automotive electronics.
As the demand for high-power and miniaturized electronic devices continues to grow, Metal Core PCBs will play an increasingly important role in enabling the next generation of innovative products and technologies.
Leave a Reply