Introduction to Heatsink paste
Heatsink paste, also known as thermal paste, thermal grease, or thermal compound, is a crucial component in ensuring efficient heat transfer between a heat-generating device (such as a CPU or GPU) and a heatsink. The primary purpose of heatsink paste is to fill the microscopic air gaps and irregularities between the surfaces of the device and the heatsink, thereby improving thermal conductivity and heat dissipation.
The Importance of Using Heatsink Paste
Using heatsink paste is essential for several reasons:
-
Improved thermal conductivity: By filling the air gaps between the heat source and the heatsink, thermal paste allows for better heat transfer, as air is a poor conductor of heat.
-
Prevention of overheating: Efficient heat dissipation helps prevent the device from overheating, which can lead to reduced performance, system instability, and even permanent damage.
-
Longer device lifespan: By maintaining optimal operating temperatures, heatsink paste contributes to the longevity of the heat-generating device.
Types of Heatsink Paste
There are several types of heatsink paste available on the market, each with its own unique properties and performance characteristics. The most common types include:
Silicone-Based Thermal Paste
Silicone-based thermal pastes are the most widely used type of heatsink paste. They are known for their ease of application, non-conductivity, and decent thermal performance. These pastes typically consist of a silicone base mixed with thermally conductive particles, such as zinc oxide or aluminum oxide.
Advantages:
– Non-conductive and non-capacitive
– Easy to apply and remove
– Suitable for most everyday applications
Disadvantages:
– Lower thermal conductivity compared to other types
– Can dry out over time, requiring reapplication
Examples of silicone-based thermal pastes:
– Arctic MX-4
– Noctua NT-H1
– Thermal Grizzly Kryonaut
Metal-Based Thermal Paste
Metal-based thermal pastes contain thermally conductive metals, such as silver, copper, or aluminum. These pastes offer superior thermal conductivity compared to silicone-based pastes, making them ideal for high-performance applications or extreme overclocking.
Advantages:
– Excellent thermal conductivity
– Ideal for high-performance applications
– Long-lasting and durable
Disadvantages:
– Can be electrically conductive, risking short-circuits if misapplied
– More expensive than silicone-based pastes
– Can be more difficult to apply and remove
Examples of metal-based thermal pastes:
– Coollaboratory Liquid Ultra
– Thermal Grizzly Conductonaut
– Innovation Cooling Diamond
Ceramic-Based Thermal Paste
Ceramic-based thermal pastes use ceramic particles as their primary thermally conductive component. These pastes offer a balance between the thermal performance of metal-based pastes and the safety and ease of use of silicone-based pastes.
Advantages:
– Good thermal conductivity
– Non-conductive and non-capacitive
– Suitable for a wide range of applications
Disadvantages:
– Slightly more expensive than silicone-based pastes
– Can be more difficult to apply evenly compared to silicone-based pastes
Examples of ceramic-based thermal pastes:
– Arctic Silver 5
– Noctua NT-H2
– Prolimatech PK-3
Carbon-Based Thermal Paste
Carbon-based thermal pastes incorporate carbon particles, such as diamond or graphite, to enhance thermal conductivity. These pastes are relatively new to the market and offer a unique set of properties.
Advantages:
– High thermal conductivity
– Non-conductive and non-capacitive
– Long-lasting and stable performance
Disadvantages:
– More expensive than other types of thermal paste
– Limited availability compared to other types
Examples of carbon-based thermal pastes:
– Innovation Cooling Diamond
– Thermal Grizzly Carbonaut
Factors to Consider When Choosing a Heatsink Paste
When selecting a heatsink paste for your application, there are several factors to consider:
Thermal Conductivity
Thermal conductivity is a measure of how well a material can transfer heat. Higher thermal conductivity means better heat transfer and, consequently, more efficient cooling. The thermal conductivity of heatsink pastes is typically measured in watts per meter-kelvin (W/mK).
Type of Thermal Paste | Typical Thermal Conductivity Range (W/mK) |
---|---|
Silicone-based | 2-10 |
Metal-based | 20-80 |
Ceramic-based | 5-15 |
Carbon-based | 10-40 |
Electrical Conductivity
Some thermal pastes, particularly metal-based ones, can be electrically conductive. If misapplied, these pastes can cause short-circuits and damage the device or motherboard. For most applications, it is recommended to use non-conductive thermal pastes to minimize the risk of damage.
Ease of Application and Removal
The ease of application and removal is another important factor to consider. Silicone-based and ceramic-based pastes are generally easier to apply and remove compared to metal-based and carbon-based pastes. If you are new to applying thermal paste or plan to replace it frequently, choose a paste that is easy to work with.
Durability and Longevity
The durability and longevity of a thermal paste refer to how well it maintains its performance over time. Some pastes, particularly silicone-based ones, can dry out or degrade over time, requiring reapplication. Metal-based, ceramic-based, and carbon-based pastes generally offer better long-term stability.
Price and Availability
Finally, consider the price and availability of the thermal paste. Silicone-based pastes are usually the most affordable and widely available, while metal-based, ceramic-based, and carbon-based pastes can be more expensive and harder to find. Choose a paste that fits your budget and is readily available in your region.
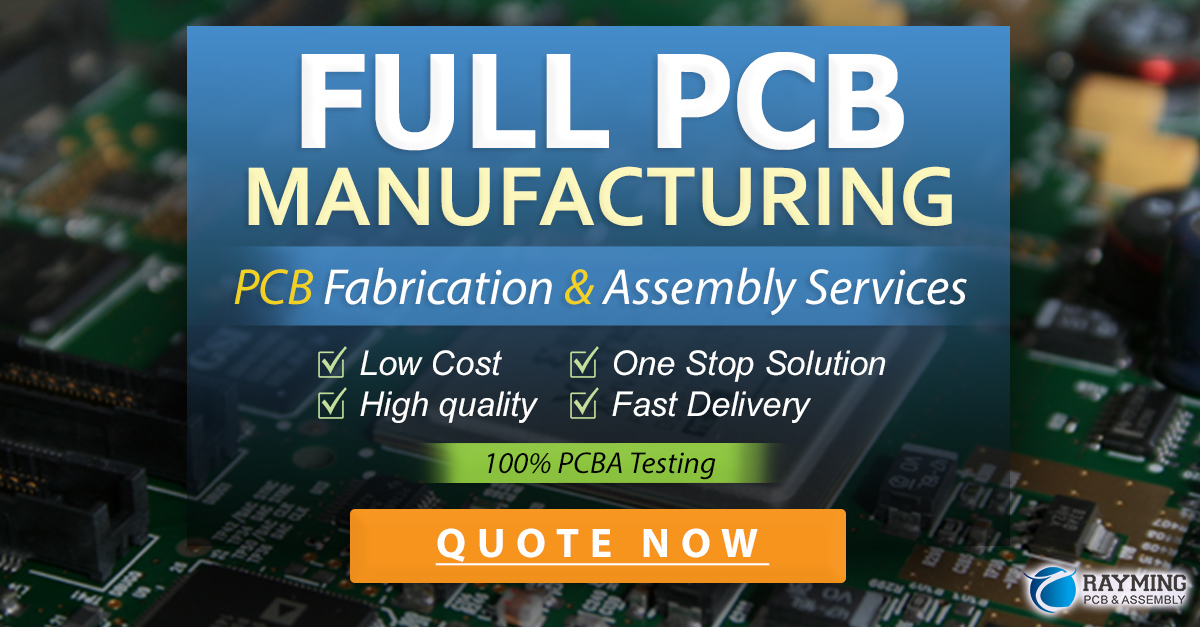
How to Apply Heatsink Paste
Applying heatsink paste correctly is crucial for achieving optimal thermal performance. Follow these steps to apply thermal paste:
-
Clean the surfaces of the heat-generating device and the heatsink using isopropyl alcohol and a lint-free cloth. Ensure that the surfaces are free of dust, grease, and old thermal paste residue.
-
Place a small amount of thermal paste on the center of the heat-generating device. The amount should be approximately the size of a rice grain for most applications.
-
Using a plastic card or spreader, gently spread the paste evenly across the surface of the device. Aim for a thin, even layer that covers the entire surface.
-
Alternatively, you can use the “dot method” by placing a small dot of paste in the center of the device and allowing the pressure from the heatsink to spread it evenly.
-
Carefully place the heatsink on top of the device, ensuring that it is properly aligned and secured.
-
Power on the device and monitor the temperatures to ensure that the thermal paste is working effectively.
Frequently Asked Questions (FAQ)
-
Q: How often should I replace my thermal paste?
A: It is generally recommended to replace your thermal paste every 2-3 years, or whenever you notice a significant increase in device temperatures. -
Q: Can I use too much thermal paste?
A: Yes, using too much thermal paste can be detrimental to thermal performance. Excess paste can act as an insulator and prevent efficient heat transfer. Always use the recommended amount specified by the manufacturer. -
Q: Is it okay to use cheap or generic thermal paste?
A: While cheap or generic thermal pastes may work, they often have lower thermal conductivity and may not provide the same level of performance as premium pastes. It is recommended to invest in a high-quality thermal paste for the best results. -
Q: Can I mix different types of thermal paste?
A: No, mixing different types of thermal paste is not recommended. Each type of paste has unique properties and mixing them can lead to reduced performance or even damage to the device. -
Q: What happens if I don’t use any thermal paste?
A: Not using thermal paste can lead to poor heat transfer between the device and the heatsink, resulting in overheating, reduced performance, and potential damage to the device. Always use thermal paste to ensure optimal thermal performance.
Conclusion
Choosing the right heatsink paste and applying it correctly is essential for ensuring optimal thermal performance and longevity of your heat-generating devices. Consider factors such as thermal conductivity, electrical conductivity, ease of application, durability, and price when selecting a thermal paste. By following proper application techniques and periodically replacing your thermal paste, you can keep your devices running cool and stable for years to come.
Leave a Reply