Introduction to Pre-heaters
A pre-heater is an essential component in various industrial processes, particularly in the production of materials such as cement, steel, and chemicals. Its primary function is to heat raw materials or feed streams before they enter the main processing unit, such as a kiln, furnace, or reactor. By preheating the materials, the pre-heater enhances energy efficiency, reduces fuel consumption, and improves the overall performance of the industrial process.
How Does a Pre-heater Work?
Pre-heaters work by utilizing waste heat from the main processing unit or external heat sources to raise the temperature of the incoming materials. The most common types of pre-heaters include:
- Cyclone pre-heaters
- Grate pre-heaters
- Suspension pre-heaters
- Shaft pre-heaters
Cyclone Pre-heaters
Cyclone pre-heaters are widely used in the cement industry. They consist of a series of cyclones arranged in a tower-like structure. The hot exhaust gases from the kiln pass through the cyclones in a counter-current flow to the raw meal (a mixture of raw materials used to produce cement). The raw meal is fed into the top cyclone and moves downward through the series of cyclones, while the hot gases move upward. As the raw meal and hot gases come into contact, heat is transferred from the gases to the raw meal, gradually increasing its temperature.
Grate Pre-heaters
Grate pre-heaters are commonly used in the steel industry to preheat the iron ore and other raw materials before they are fed into the blast furnace. The raw materials are placed on a moving grate, and hot exhaust gases from the blast furnace are passed through the grate, heating the materials. The preheated raw materials are then fed into the blast furnace, reducing the amount of energy required to melt them.
Suspension Pre-heaters
Suspension pre-heaters are used in various industries, including chemical and petrochemical processing. In this type of pre-heater, the feed stream is dispersed into a hot gas stream, creating a suspension of fine droplets or particles. The high surface area of the dispersed feed allows for efficient heat transfer from the hot gases to the feed stream. The preheated feed is then separated from the gas stream and fed into the main processing unit.
Shaft Pre-heaters
Shaft pre-heaters are vertical cylindrical vessels used to preheat solid materials, such as limestone or iron ore. The raw materials are fed into the top of the pre-heater and move downward by gravity. Hot exhaust gases from the main processing unit are introduced at the bottom of the pre-heater and flow upward, counter-current to the descending solids. As the gases and solids come into contact, heat is transferred, preheating the raw materials before they enter the main processing unit.
Benefits of Using a Pre-heater
The use of pre-heaters in industrial processes offers several significant benefits:
- Improved energy efficiency
- Reduced fuel consumption
- Increased production capacity
- Enhanced product quality
- Lower emissions
Improved Energy Efficiency
By preheating the raw materials or feed streams, pre-heaters reduce the amount of energy required in the main processing unit to bring the materials up to the desired temperature. This improved energy efficiency leads to lower overall energy consumption and reduced operating costs.
Reduced Fuel Consumption
As pre-heaters utilize waste heat from the main processing unit or external heat sources, the fuel consumption in the main processing unit is reduced. This not only saves on fuel costs but also helps to conserve natural resources and reduce the environmental impact of the industrial process.
Increased Production Capacity
Pre-heaters allow for higher throughput rates in the main processing unit. By preheating the raw materials, the time required for the materials to reach the desired temperature in the main processing unit is reduced, enabling faster processing and increased production capacity.
Enhanced Product Quality
Preheating raw materials can lead to improved product quality in various industrial processes. For example, in cement production, preheating the raw meal helps to ensure a more homogeneous mixture and reduces the formation of lumps or agglomerates. This results in a more consistent and higher-quality cement product.
Lower Emissions
Pre-heaters help to reduce emissions from industrial processes in two ways. First, by improving energy efficiency and reducing fuel consumption, pre-heaters contribute to lower greenhouse gas emissions. Second, in some cases, pre-heaters can be designed to remove certain pollutants, such as sulfur dioxide or nitrogen oxides, from the exhaust gases before they are released into the atmosphere.
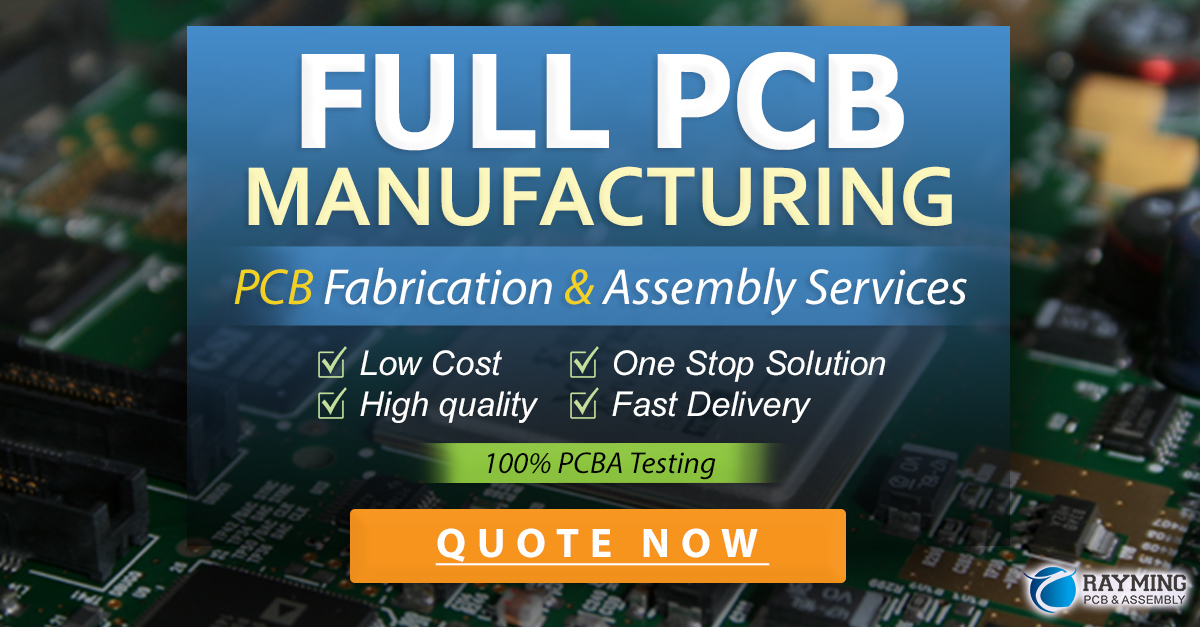
Applications of Pre-heaters
Pre-heaters are used in a wide range of industries, including:
- Cement production
- Steel manufacturing
- Chemical processing
- Petrochemical industry
- Glass manufacturing
- Pulp and paper industry
Cement Production
In the cement industry, pre-heaters are an integral part of the production process. Cyclone pre-heaters are the most common type used in cement plants. The raw meal, consisting of limestone, clay, and other raw materials, is preheated in the cyclone pre-heater before entering the rotary kiln. This preheating process improves energy efficiency, reduces fuel consumption, and increases the production capacity of the cement plant.
Steel Manufacturing
In steel manufacturing, grate pre-heaters are used to preheat the iron ore, coke, and other raw materials before they are fed into the blast furnace. The preheated raw materials require less energy to melt in the blast furnace, leading to improved energy efficiency and reduced coke consumption. Additionally, preheating the raw materials helps to improve the quality of the pig iron produced in the blast furnace.
Chemical Processing
Pre-heaters are used in various chemical processing applications, such as the production of ammonia, methanol, and hydrogen. In these processes, suspension pre-heaters are often used to preheat the feed streams before they enter the reactor. Preheating the feed streams improves the reaction kinetics, increases the conversion efficiency, and enhances the overall performance of the chemical process.
Petrochemical Industry
In the petrochemical industry, pre-heaters are used to preheat the feedstock before it enters the cracking furnaces. The most common feedstocks in the petrochemical industry are naphtha and ethane. Preheating these feedstocks helps to improve the yield of valuable products, such as ethylene and propylene, and reduces the formation of undesired byproducts.
Glass Manufacturing
In glass manufacturing, pre-heaters are used to preheat the raw materials, such as silica sand, soda ash, and limestone, before they are fed into the glass melting furnace. Preheating the raw materials reduces the energy required to melt them in the furnace, leading to improved energy efficiency and reduced fuel consumption.
Pulp and Paper Industry
In the pulp and paper industry, pre-heaters are used to preheat the air and process streams in various stages of the production process. For example, in the kraft pulping process, pre-heaters are used to preheat the combustion air for the recovery boiler, which burns the black liquor to generate steam and recover the cooking chemicals. Preheating the combustion air improves the efficiency of the recovery boiler and reduces fuel consumption.
Factors Affecting Pre-heater Performance
Several factors can influence the performance of a pre-heater:
- Heat transfer efficiency
- Pressure drop
- Fouling and corrosion
- Material properties
Heat Transfer Efficiency
The heat transfer efficiency of a pre-heater depends on various factors, such as the type of pre-heater, the design of the heat transfer surfaces, and the properties of the fluids involved. Improving the heat transfer efficiency can lead to better preheating of the materials and increased overall performance of the industrial process.
Pressure Drop
Pressure drop across the pre-heater is another important factor to consider. High pressure drops can lead to increased energy consumption in the fans or blowers used to move the fluids through the pre-heater. Designing the pre-heater to minimize pressure drop while maintaining effective heat transfer is crucial for optimal performance.
Fouling and Corrosion
Fouling and corrosion can reduce the heat transfer efficiency and overall performance of a pre-heater over time. Fouling occurs when deposits, such as dust, ash, or scale, accumulate on the heat transfer surfaces, creating a barrier to heat transfer. Corrosion can occur due to the presence of corrosive substances in the fluids, leading to the degradation of the pre-heater materials. Regular maintenance, cleaning, and the use of corrosion-resistant materials can help to mitigate these issues.
Material Properties
The properties of the materials being preheated, such as their thermal conductivity, specific heat capacity, and particle size, can affect the performance of the pre-heater. Materials with higher thermal conductivity and smaller particle sizes generally allow for more efficient heat transfer. Understanding the properties of the materials being processed is essential for designing and operating an effective pre-heater.
Innovations in Pre-heater Technology
Advances in pre-heater technology have led to the development of more efficient and environmentally friendly pre-heaters. Some of these innovations include:
- Selective non-catalytic reduction (SNCR)
- Waste heat recovery systems
- Advanced materials for enhanced heat transfer
Selective Non-catalytic Reduction (SNCR)
Selective non-catalytic reduction (SNCR) is a technology used to reduce nitrogen oxide (NOx) emissions in industrial processes. SNCR systems can be integrated with pre-heaters to inject ammonia or urea into the exhaust gases at a specific temperature range. The ammonia or urea reacts with the NOx, converting it into nitrogen and water, thereby reducing NOx emissions.
Waste Heat Recovery Systems
Waste heat recovery systems can be used in conjunction with pre-heaters to further improve energy efficiency. These systems capture waste heat from various sources, such as exhaust gases or cooling water, and use it to preheat the raw materials or feed streams. By utilizing waste heat that would otherwise be lost, these systems help to reduce overall energy consumption and improve the sustainability of the industrial process.
Advanced Materials for Enhanced Heat Transfer
The development of advanced materials with enhanced heat transfer properties has the potential to improve pre-heater performance. For example, the use of ceramic materials or metal-ceramic composites can increase the heat transfer efficiency and durability of pre-heater components. These materials can withstand higher temperatures, resist fouling and corrosion, and provide better thermal conductivity compared to traditional materials.
Conclusion
Pre-heaters play a crucial role in various industrial processes by improving energy efficiency, reducing fuel consumption, increasing production capacity, enhancing product quality, and lowering emissions. The most common types of pre-heaters include cyclone pre-heaters, grate pre-heaters, suspension pre-heaters, and shaft pre-heaters, each with its specific applications and advantages. Factors such as heat transfer efficiency, pressure drop, fouling and corrosion, and material properties influence the performance of pre-heaters. Innovations in pre-heater technology, such as selective non-catalytic reduction, waste heat recovery systems, and advanced materials, continue to drive improvements in pre-heater performance and environmental sustainability.
FAQs
-
What is the primary function of a pre-heater in industrial processes?
The primary function of a pre-heater is to heat raw materials or feed streams before they enter the main processing unit, such as a kiln, furnace, or reactor. -
How do pre-heaters improve energy efficiency in industrial processes?
Pre-heaters improve energy efficiency by utilizing waste heat from the main processing unit or external heat sources to preheat the raw materials or feed streams, reducing the amount of energy required in the main processing unit to bring the materials up to the desired temperature. -
What are the most common types of pre-heaters used in industrial processes?
The most common types of pre-heaters used in industrial processes are cyclone pre-heaters, grate pre-heaters, suspension pre-heaters, and shaft pre-heaters. -
How do pre-heaters help to reduce emissions in industrial processes?
Pre-heaters help to reduce emissions in industrial processes by improving energy efficiency and reducing fuel consumption, which leads to lower greenhouse gas emissions. Some pre-heaters can also be designed to remove certain pollutants, such as sulfur dioxide or nitrogen oxides, from the exhaust gases before they are released into the atmosphere. -
What innovations in pre-heater technology are helping to improve their performance and environmental sustainability?
Innovations in pre-heater technology include selective non-catalytic reduction (SNCR) systems for reducing nitrogen oxide emissions, waste heat recovery systems for further improving energy efficiency, and the use of advanced materials with enhanced heat transfer properties for increasing pre-heater durability and performance.
Leave a Reply