Introduction
When designing a printed circuit board (PCB), one of the most important considerations is choosing the right substrate material. The substrate material, also known as the base material, is what the copper traces are printed on to form the circuit board. The cost of the substrate material can have a significant impact on the overall cost of producing the PCB. For hobbyists, makers, and other situations where cost is a primary concern, figuring out the cheapest PCB material that still meets functional requirements is crucial.
In this article, we will compare the costs and characteristics of some of the most common PCB substrate materials to determine which options are the most budget-friendly. We will look at factors like material cost, processing costs, frequency support, thermal performance, and mechanical properties. Read on to learn what the cheapest PCB materials are and which one might be the best fit for your next project.
Common PCB Substrate Materials
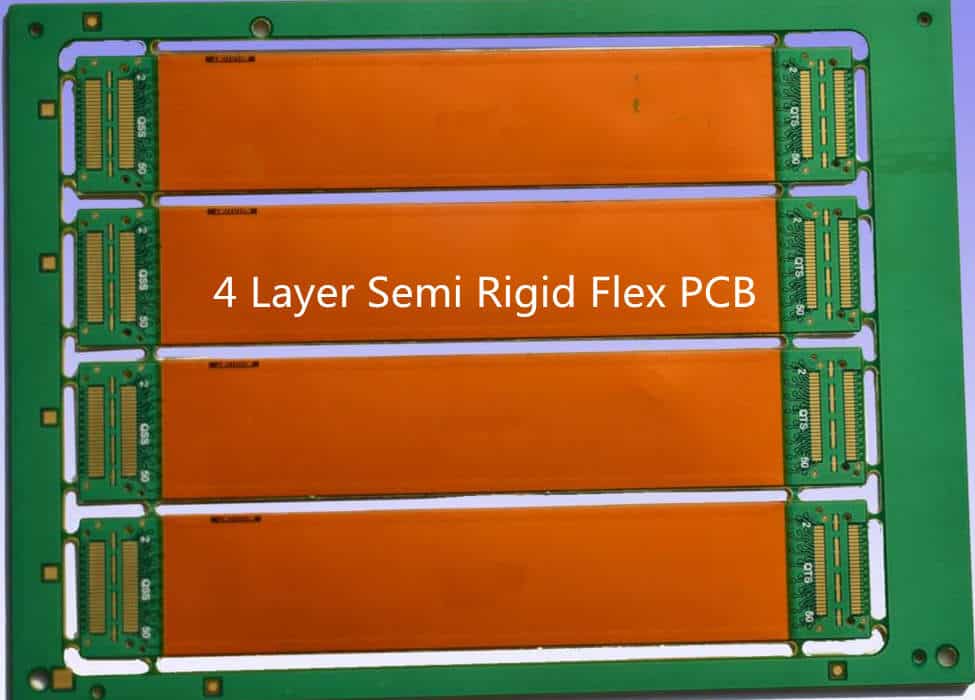
Here is an overview of some of the most frequently used PCB substrate materials and their typical properties:
Material | Typical Cost | Frequency Support | Thermal Performance | Mechanical Properties |
---|---|---|---|---|
FR-4 | Low | Up to GHz frequencies | Moderate, Tg 130-170°C | Moderate strength |
CEM-1 | Low | Up to GHz frequencies | Moderate, Tg 120-180°C | Moderate strength |
Polyimide | Moderate | Extremely high frequencies, 10+ GHz | Excellent, Tg > 300°C | Excellent strength |
PTFE (Teflon) | High | Extremely high frequencies, 10+ GHz | Excellent, Tg > 250°C | Moderate strength |
Alumina (ceramic) | Very high | Extremely high frequencies, 10+ GHz | Excellent, Tg > 300°C | Brittle |
FR-4
FR-4 is the cheapest and most widely used material for rigid PCBs. It is made of woven fiberglass cloth with an epoxy resin binder. It has moderate thermal performance, with a glass transition temperature around 130-170°C. It supports frequencies up to several GHz and has moderate mechanical strength. The low cost and good balance of properties makes FR-4 a popular choice for many consumer electronics and light industrial applications.
CEM-1
CEM-1 is another common type of PCB substrate made of fiberglass reinforced epoxy. It has very similar properties to FR-4 but uses brominated flame retardants to achieve higher flame resistance. This makes it popular for consumer electronics requiring UL flammability ratings. It has equivalent performance to FR-4 in terms of cost, frequency support, and mechanical and thermal characteristics.
Polyimide
Polyimide films like Kapton provide an excellent high performance PCB material. The material has high heat and chemical resistance with a glass transition temperature over 300°C. This makes it useful for very high temperature applications. Polyimide is more expensive than FR-4 but supports frequencies up to 20GHz or higher. It also has excellent mechanical properties. Polyimide is a popular choice for aerospace, military, and advanced electronics applications.
PTFE (Teflon)
PTFE, also referred to by the brand name Teflon, provides the highest frequency support and thermal performance of readily available PCB materials. It has extremely low dielectric losses, allowing it to support frequencies up to 100GHz. It also offers high heat and chemical resistance. However, PTFE is significantly more expensive than other common substrates. This limits its use to specialized high frequency or high reliability applications.
Alumina (ceramic)
Alumina ceramic provides unmatched frequency support and temperature resistance, with low loss through microwave frequencies and thermal stability above 300°C. However, ceramic PCBs are extremely expensive to fabricate. Most ceramic boards are limited to hybrid circuits rather than full printed boards. The high cost and brittleness of ceramics restricts their use to niche applications like military systems.
Cheapest PCB Materials
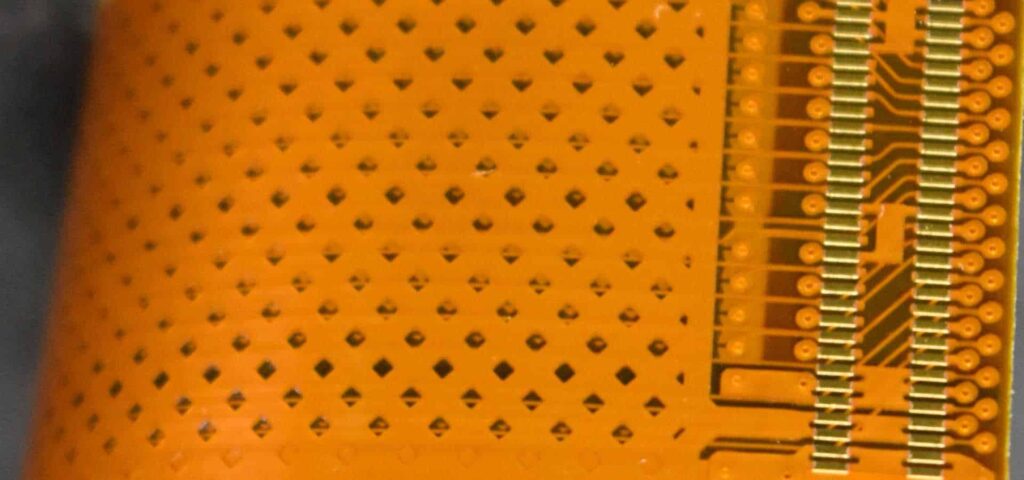
For the vast majority of PCB applications, FR-4 is the cheapest substrate option. The low cost is driven by several factors:
- Inexpensive raw materials – Fiberglass and epoxy resins are commodity materials produced at very large volumes.
- Highly optimized fabrication – FR-4 processing has been refined over decades of high volume manufacturing.
- No specialty requirements – FR-4 does not require special processing conditions like high heat or chemical resistance.
Other materials like CEM-1 can match FR-4’s cost in some cases, but FR-4 remains the benchmark for low cost, high volume PCB production. Some key advantages of FR-4 are:
- Low material cost – Around $2-5/ft2
- Standard processing – No specialty requirements for fabrication
- Wide availability – Offered by virtually all PCB manufacturers
For prototyping or small batch orders, the total board cost is dominated by processing rather than just material cost. In these cases, FR-4 or CEM-1 will still typically be the cheapest options. The specialized processing required for higher performance materials makes them much more expensive for small quantity orders.
The one exception where another material may be cheaper is flex PCBs. Polyimide and polyester flex circuits can sometimes cost less than FR-4 rigid boards for simple flex designs. But rigid FR-4 will still be cheaper than more complex multilayer flex boards.
When to Consider Other Materials
While FR-4 is the cheapest PCB material overall, there are some instances where it makes sense to use a more expensive substrate:
High frequency circuits – FR-4 losses start to increase above a few GHz. For microwave frequencies and very high speed digital, specialty materials like PTFE or ceramic provide much lower loss. The increased cost can be justified for performance.
High temperature operation – If the circuit will operate for long periods above 170°C, the relatively low Tg of FR-4 becomes problematic. High Tg materials like polyimide and PTFE maintain stable electrical and mechanical properties at elevated temperatures.
Specialized applications – Some applications, like aerospace systems, justify the use of much more expensive materials due to high reliability requirements. Very lightweight circuits may also use flexible PCB substrates instead of rigid FR-4.
Quick prototyping – For one-off prototype PCBs without cost constraints, high performance materials like PTFE or polyimide can be easier to hand solder and less prone to heat damage. This can offset their higher cost for prototyping scenarios.
Space constraints – When a design requires packing high density traces and components into a very small space, higher performance materials allow for finer trace widths and spacing. The increased cost can be justified when FR-4 does not provide enough design flexibility.
So in specialized cases where performance, size, weight, or reliability considerations outweigh cost, more exotic PCB materials may be justified. But for the vast majority of cost-driven applications, FR-4 remains the cheapest PCB material option.
Factors Affecting PCB Cost
While material cost is critical, there are ways to optimize other aspects of a design to reduce overall fabrication cost:
Number of layers – Boards with fewer layers are significantly cheaper, with 2-4 layer designs offering the best tradeoff of cost and routing flexibility. High layer counts quickly drive up fabrication cost.
Board size – Larger boards will obviously cost more in terms of base material. But larger sizes also reduce the number of boards that can be panelized for a production run, increasing cost per board.
Trace/space – Wider traces and greater clearance between traces enables lower cost etching processes. Finer lines require more expensive processing.
Via process – Boards with only through hole vias can be much cheaper than designs requiring buried/blind vias. Skip vias where possible.
Solder mask – Skipping solder mask for low volume prototypes saves one fabrication step and cost.
Lead times – Standard lead times allow better batching and cost savings compared to “expedited” turns.
Assembly optimization – Simpler component packages, consolidated component types, and other assembly friendly practices reduce manufacturing costs.
So material cost is not the only consideration. Optimizing the physical and electrical design for easier, lower cost fabrication and assembly is key to producing the most cost effective PCBs.
Summary
To recap, the main points about low cost PCB materials:
- For most applications, FR-4 provides the cheapest PCB substrate option. It offers the lowest material cost and well optimized processing.
- Other common rigid materials like CEM-1 have comparable cost to FR-4 but may offer specific advantages for certain applications.
- More advanced materials provide higher performance but at much higher cost. They are only cost justifiable for specialized applications.
- To get the lowest overall PCB cost, optimizing the layout for ease of fabrication and assembly is just as important as substrate material selection.
So focus design efforts on simplicity and manufacturability, and choose the cheapest material that meets the application requirements. In most cases, that optimum choice will be good old FR-4. With smart design practices, it provides the best balance of cost and capabilities for a wide range of electronics projects.
FAQ
Here are answers to some frequently asked questions about cheap PCB materials:
What is the cheapest material for a 2 layer PCB?
For a simple 2 layer board, FR-4 glass epoxy is the cheapest common material option. With only 2 routing layers, the lowest cost process will be desired.
Is polyimide cheaper than FR4?
No, polyimide substrates are generally more expensive than FR-4. Polyimide provides higher performance but costs more due to raw material costs and additional processing requirements.
When should I use Teflon PCBs instead of FR4?
Teflon (PTFE) should be used when the application requires operation above 170°C or at microwave frequencies above 10GHz. The higher cost can be justified by the increased thermal and frequency performance compared to FR-4.
What is the cheapest flex PCB material?
The cheapest flex PCB materials are PET (polyester) and PI (polyimide) films. Of the two, polyester films are typically the most economical option while still providing good flex performance.
Is ceramic PCB cheaper than FR4?
No, ceramic boards are much more expensive to fabricate than FR-4. They provide excellent thermal and frequency performance but are only cost justifiable for niche applications like military systems.
Leave a Reply