Introduction
A flexible printed circuit board (Flex PCB) is a type of printed circuit board that is thin, bendable and flexible. Unlike traditional rigid PCBs, flex PCBs can be bent, folded and shaped to fit into tight or moving spaces in electronic devices. One of the key components that allows a flex PCB to be flexible is the adhesive that bonds the conductive copper traces to the flexible base material.
The adhesive plays a critical role in ensuring the reliability and durability of the flex PCB. As the board is flexed and bent repeatedly, the adhesive prevents the copper traces from cracking or peeling away from the substrate. Choosing the right adhesive is therefore important when manufacturing quality flex PCBs.
This article provides an in-depth look at the types of adhesives used in flex PCBs, their properties, selection criteria and applications.
Types of Adhesives Used in Flex PCBs
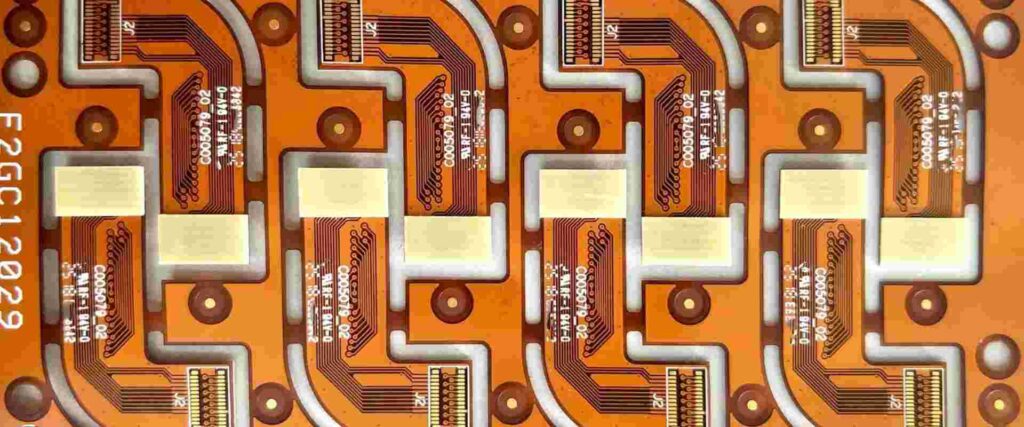
There are two main categories of adhesives used to bond the copper to the flexible substrate in flex PCBs:
1. Thermosetting Adhesives
Thermosetting adhesives cure and harden permanently when heated. The most commonly used thermosetting adhesives for flex PCBs include:
- Epoxy – Epoxy is the most popular and widely used adhesive for flex PCBs. It provides excellent adhesion, good flexibility, chemical and moisture resistance.
- Phenolic – Phenolic adhesives offer high bond strength and thermal stability. However, they have limited flexibility compared to epoxy.
- Silicone – Silicone adhesives maintain flexibility and adhesion at extreme temperatures. But they have lower bond strength than epoxy.
- Polyimide – Polyimide adhesives can withstand very high temperatures. They also have good chemical resistance. But they are relatively expensive.
2. Thermoplastic Adhesives
Thermoplastic adhesives soften when heated and harden upon cooling. Common thermoplastic adhesives used in flex PCBs include:
- Acrylic – Acrylic adhesives offer good flexibility and low cost. However, they have moderate bond strength and chemical/thermal resistance.
- Polyurethane – Polyurethane adhesives provide high flexibility and abrasion resistance. But they have poor solvent resistance.
Comparison between Thermosetting and Thermoplastic Adhesives
Properties | Thermosetting | Thermoplastic |
---|---|---|
Bond strength | High | Moderate |
Flexibility | Moderate | High |
Thermal stability | High | Low to moderate |
Solvent resistance | High | Low to moderate |
Cost | Moderate | Low |
Properties of Flex PCB Adhesives
The adhesives used in flex PCBs must have specific properties and characteristics to meet the demanding requirements of flexible circuits. Some key properties include:
- Flexibility – The adhesive must remain flexible, bendable and elastic to facilitate repeated bending and flexing motions.
- Adhesion – It must form a strong bond between the copper foil and substrate to prevent delamination or cracking under stress.
- Temperature resistance – It must be able to withstand high and low temperature extremes that flexible circuits may be exposed to.
- Chemical resistance – The adhesive should be resistant to chemicals like solvents, fuels, oils and cleaning agents.
- Creep resistance – It should have low creep or deformation over time when subjected to sustained loads or vibrations.
- Dielectric strength – The adhesive must have good insulating properties and high dielectric strength.
- Processability – The adhesive must be easy to apply and process using standard flex PCB manufacturing techniques.
Selection Criteria for Flex PCB Adhesives
Several factors need to be considered when selecting an appropriate adhesive for a flex PCB application:
- Base material – The adhesive compatibility with the substrate material (polyimide, PET, PEN etc.) is crucial.
- Conductor type – Compatibility with conductor metal (usually copper) is important.
- Bonding process – The adhesive must be suitable for the bonding method – heat lamination, pressure sensitive etc.
- Service temperatures – The adhesive must withstand the minimum and maximum temperatures.
- Flexibility requirements – More flexible circuits require more elastic adhesives.
- Chemical exposure – Applications with chemical exposure require adhesives with higher chemical resistance.
- Cost – The adhesive cost may be a deciding factor for high volume commercial applications.
Applications of Flex PCB Adhesives
Some common applications where specialized flex PCB adhesives are used:
- Consumer electronics – Wearables, display panels, flex antennas in mobile devices. Require high flexibility and bend cycles.
- Automotive – Flex circuits for engine control units, brake systems. Require reliability at high temps.
- Industrial – Flexible heaters, robotic arms. Require adhesives with good thermal conductivity.
- Medical – Implantable devices, patient monitoring systems. Require bio-compatible, moisture resistant adhesives.
- Military/Aerospace – Missile guidance systems, avionics. Require adhesives with extreme temperature and chemical resistance.
- Flexible photovoltaics – Thin flexible solar cells. Require transparency and resist prolonged UV exposure.
Common Problems with Flex PCB Adhesives
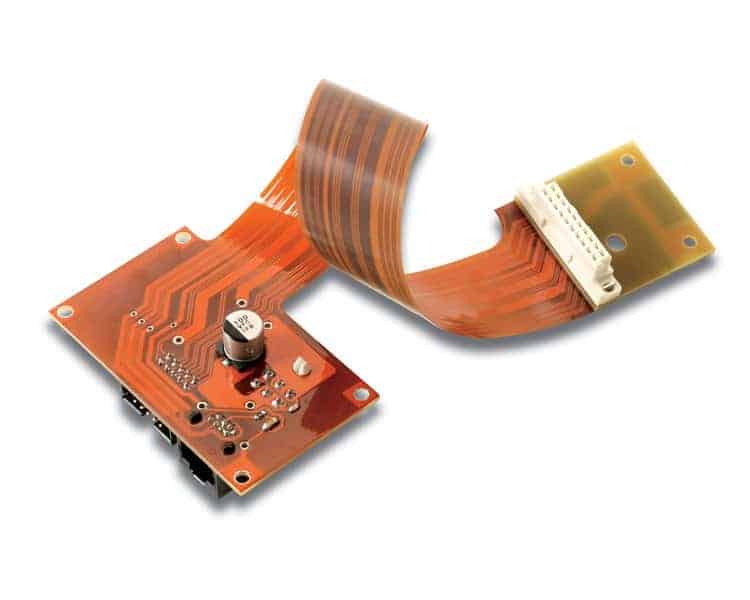
Some potential problems encountered with adhesives in flex PCBs:
- Delamination – Insufficient bond strength can cause separation of the copper traces from the substrate.
- Cracking – Lack of flexibility can lead to cracking of traces when flexed.
- Creep – Some adhesives can deform permanently under sustained loads and vibration.
- Outgassing – Release of gases trapped in the adhesive when subjected to high temperatures.
- Cold flow – Adhesive slowly moves and spreads out from under the copper foil over time.
- Poor chemical resistance – Harsh chemicals degrade and dissolve some adhesive types.
Proper adhesive selection, surface treatment and bonding process controls can help avoid these defects and reliability issues.
Frequently Asked Questions
Q1. Which is better for flex PCBs – thermosetting or thermoplastic adhesives?
Thermosetting adhesives like epoxy are generally preferred for flex PCBs due to their higher bond strength, thermal stability and chemical resistance compared to thermoplastics. However, thermoplastic adhesives provide higher flexibility.
Q2. How does flexing and bending affect flex PCB adhesives?
Repeated flexing applies cyclic stresses which can cause adhesion loss, cracking or delamination over time. Flexible, high elongation adhesives with good fatigue resistance are required.
Q3. What are some surface treatment methods used to improve flex PCB adhesive bonding?
Surface treatments like chemical etching or plasma treatment help improve adhesion by roughening the surface and removing weak boundary layers.
Q4. How are the adhesives applied during flex PCB fabrication?
Liquid adhesives are applied by roller coating, dip coating or lamination processes. Hot melt adhesive films are bonded through heat and pressure.
Q5. Can conformal coatings be used to improve flex PCB adhesive performance?
Yes, conformal coatings enhance chemical, moisture and abrasion resistance. But they can impact flexibility if not selected properly.
Conclusion
The adhesive plays a vital role in holding the layers of a flex PCB together and enabling dynamic flexing motions. Epoxies are the predominant adhesive type due to their versatile performance, but other options are also used depending on requirements. Careful design, material selection and process controls are needed to prevent adhesive-related failures in flex circuits. As flex PCBs become smaller and more robust, continuous advancements in adhesive technology will be key to their success across an ever-increasing array of applications.
Leave a Reply