Introduction to Single-Sided PCB
A Single-Sided PCB, also known as a Single Layer PCB, is a printed circuit board that has conductive copper traces on only one side of the board. These PCBs are the simplest and most cost-effective type of printed circuit board available in the market. Single-Sided PCBs are widely used in simple electronic devices, such as calculators, radios, and low-cost consumer electronics.
Advantages of Single-Sided PCB
- Cost-effective: Single-Sided PCBs are the most affordable type of PCB due to their simple design and manufacturing process.
- Easy to design: Designing a Single-Sided PCB is relatively simple compared to multi-layer PCBs, as there are fewer design constraints and considerations.
- Quick turnaround time: The manufacturing process for Single-Sided PCBs is faster than that of multi-layer PCBs, resulting in shorter lead times.
- Suitable for low-complexity circuits: Single-Sided PCBs are ideal for simple electronic circuits that do not require a high component density or complex routing.
Disadvantages of Single-Sided PCB
- Limited routing options: With only one conductive layer, Single-Sided PCBs have limited routing options, which can lead to larger board sizes and increased wire jumpers.
- Lower component density: Single-Sided PCBs cannot accommodate as many components as multi-layer PCBs due to the limited space available on one side of the board.
- Reduced electrical performance: Single-Sided PCBs may have reduced electrical performance compared to multi-layer PCBs, as they are more susceptible to electromagnetic interference and crosstalk.
- Not suitable for complex circuits: Single-Sided PCBs are not recommended for complex electronic circuits that require a high component density or intricate routing.
Single-Sided PCB Manufacturing Process
The manufacturing process for Single-Sided PCBs involves several steps, which are outlined below:
- Design: The PCB design is created using Electronic Design Automation (EDA) software, which generates the necessary Gerber files for manufacturing.
- Copper clad laminate preparation: A copper clad laminate, which is a board made of insulating material (typically FR-4) with a thin layer of copper on one side, is used as the base material for the Single-Sided PCB.
- Drilling: Holes are drilled into the copper clad laminate according to the PCB design to accommodate through-hole components and vias.
- Copper etching: The unwanted copper is removed from the laminate using a chemical etching process, leaving behind the desired conductive traces based on the PCB design.
- Solder mask application: A solder mask, which is a protective coating, is applied to the PCB surface to prevent short circuits and protect the copper traces from oxidation and corrosion.
- Silkscreen printing: The silkscreen layer, which includes text and component identifiers, is printed onto the solder mask to assist in PCB assembly and troubleshooting.
- Surface finish application: A surface finish, such as Hot Air Solder Leveling (HASL), Immersion Gold, or Immersion Silver, is applied to the exposed copper pads to improve solderability and protect the copper from oxidation.
- Electrical testing: The manufactured Single-Sided PCB undergoes electrical testing to ensure that it functions as intended and meets the specified quality standards.
Design Considerations for Single-Sided PCB
When designing a Single-Sided PCB, several factors must be taken into account to ensure optimal performance and manufacturability:
- Component placement: Components should be placed strategically on the PCB to minimize the number of wire jumpers required and to ensure proper clearances between components.
- Trace width and spacing: The width and spacing of the copper traces should be carefully considered to ensure proper current carrying capacity and to minimize the risk of short circuits.
- Drill hole sizes: The drill hole sizes for through-hole components and vias should be chosen based on the component lead diameter and the PCB thickness to ensure proper fitment and reliability.
- Copper pour: Incorporating copper pour in the PCB design can help improve the board’s electrical performance and reduce electromagnetic interference.
- Solder mask and silkscreen: The solder mask and silkscreen layers should be designed to ensure proper insulation and clear labeling of components and connectors.
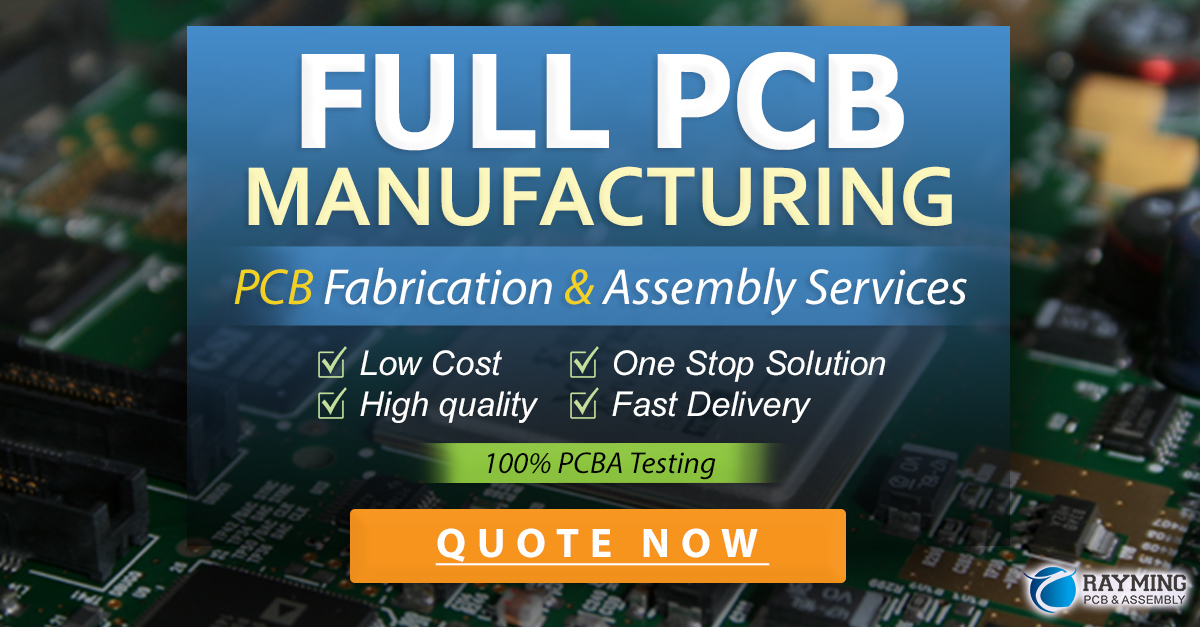
Applications of Single-Sided PCB
Single-Sided PCBs find applications in various industries and products, some of which are listed below:
- Consumer electronics: Single-Sided PCBs are commonly used in low-cost consumer electronic devices, such as calculators, remote controls, and toys.
- Automotive industry: Simple electronic circuits in automobiles, such as lighting controls and basic sensor systems, often utilize Single-Sided PCBs.
- Industrial control systems: Single-Sided PCBs are used in basic industrial control systems, such as temperature sensors and relay controls.
- Educational and hobby projects: Single-Sided PCBs are popular among students and hobbyists for simple electronic projects and prototypes due to their low cost and ease of design.
Comparison of Single-Sided PCB with Other PCB Types
Single-Sided PCBs are just one of the many types of printed circuit boards available. Here, we compare Single-Sided PCBs with other common PCB types:
PCB Type | Layers | Cost | Complexity | Applications |
---|---|---|---|---|
Single-Sided PCB | 1 | Low | Low | Simple electronics, consumer products |
Double-Sided PCB | 2 | Medium | Medium | Moderns, power supplies, amplifiers |
Multi-Layer PCB | 3+ | High | High | Smartphones, computers, servers |
Flexible PCB | 1-2 | High | Medium | Wearables, medical devices, sensors |
Rigid-Flex PCB | 3+ | High | High | Aerospace, military, high-end devices |
As evident from the table, Single-Sided PCBs are the most cost-effective and least complex type of PCB, making them suitable for simple electronic applications and consumer products.
Frequently Asked Questions (FAQ)
- What is the maximum number of components that can be placed on a Single-Sided PCB?
-
The maximum number of components that can be placed on a Single-Sided PCB depends on the board size, component sizes, and routing complexity. Generally, Single-Sided PCBs are suitable for low-complexity circuits with a limited number of components.
-
Can Single-Sided PCBs be used for high-frequency applications?
-
Single-Sided PCBs are not recommended for high-frequency applications due to their limited electrical performance and susceptibility to electromagnetic interference. For high-frequency applications, multi-layer PCBs with proper shielding and grounding techniques are preferred.
-
Are Single-Sided PCBs suitable for prototyping?
-
Yes, Single-Sided PCBs are often used for prototyping simple electronic circuits due to their low cost and quick turnaround time. However, for more complex prototypes, multi-layer PCBs may be necessary to ensure proper functionality and reliability.
-
Can Single-Sided PCBs be assembled using surface mount technology (SMT)?
-
While Single-Sided PCBs are more commonly assembled using through-hole technology (THT), they can also be assembled using surface mount technology (SMT). However, the limited space on a Single-Sided PCB may restrict the number and types of SMT components that can be used.
-
What is the typical turnaround time for manufacturing Single-Sided PCBs?
- The turnaround time for manufacturing Single-Sided PCBs is generally faster than that of multi-layer PCBs due to their simpler design and fewer manufacturing steps. Typical turnaround times for Single-Sided PCBs range from 1-5 days, depending on the manufacturer and order quantity.
Conclusion
Single-Sided PCBs are a cost-effective and simple solution for low-complexity electronic circuits and consumer products. Despite their limitations in terms of routing options, component density, and electrical performance, Single-Sided PCBs remain a popular choice for simple applications and prototyping. When designing a Single-Sided PCB, it is essential to consider factors such as component placement, trace width and spacing, drill hole sizes, and the incorporation of copper pour to ensure optimal performance and manufacturability. As technology advances and electronic devices become more complex, Single-Sided PCBs may be gradually replaced by more advanced PCB types in certain applications. However, their simplicity, affordability, and quick turnaround time ensure that they will continue to play a significant role in the electronics industry for the foreseeable future.
Leave a Reply