Types of Plating Solutions
There are various types of plating solutions, each designed for specific metals and applications. Some common plating solutions include:
Copper Plating Solutions
Copper plating solutions are used for depositing a layer of copper onto a substrate, often as an undercoat for subsequent plating processes or as a standalone finish. Copper plating solutions typically contain copper sulfate (CuSO4) as the main source of copper ions, along with other additives to improve the quality and properties of the deposited layer.
Component | Concentration |
---|---|
Copper Sulfate (CuSO4·5H2O) | 200-250 g/L |
Sulfuric Acid (H2SO4) | 50-70 g/L |
Chloride Ion (Cl-) | 50-70 mg/L |
Brighteners and Levelers | As required |
Nickel Plating Solutions
Nickel plating solutions are used for depositing a layer of nickel onto a substrate, providing excellent corrosion resistance, wear resistance, and a bright, attractive finish. Nickel plating solutions typically contain nickel sulfate (NiSO4) or nickel chloride (NiCl2) as the main source of nickel ions, along with other additives to improve the quality and properties of the deposited layer.
Component | Concentration |
---|---|
Nickel Sulfate (NiSO4·6H2O) | 240-300 g/L |
Nickel Chloride (NiCl2·6H2O) | 40-60 g/L |
Boric Acid (H3BO3) | 30-40 g/L |
Brighteners and Levelers | As required |
Zinc Plating Solutions
Zinc plating solutions are used for depositing a layer of zinc onto a substrate, providing excellent corrosion resistance and a sacrificial protection layer for the underlying metal. Zinc plating solutions typically contain zinc sulfate (ZnSO4) or zinc chloride (ZnCl2) as the main source of zinc ions, along with other additives to improve the quality and properties of the deposited layer.
Component | Concentration |
---|---|
Zinc Sulfate (ZnSO4·7H2O) | 200-300 g/L |
Zinc Chloride (ZnCl2) | 30-50 g/L |
Boric Acid (H3BO3) | 20-30 g/L |
Brighteners and Levelers | As required |
Plating Bath Composition and Operating Conditions
The composition and operating conditions of a plating bath significantly impact the quality and properties of the deposited metal layer. Plating index solutions provide a standardized reference point for these parameters, ensuring consistent results across different plating facilities and applications.
Key Components of Plating Solutions
Plating solutions typically contain the following key components:
- Metal Salt: The main source of metal ions for the plating process, such as copper sulfate, nickel sulfate, or zinc sulfate.
- Complexing Agents: Chemicals that help to stabilize the metal ions in solution and improve the quality of the deposited layer, such as citric acid or EDTA.
- pH Buffers: Compounds that help to maintain a stable pH in the plating bath, such as boric acid or potassium hydrogen phthalate.
- Brighteners and Levelers: Organic additives that improve the brightness, smoothness, and uniformity of the deposited metal layer.
- Wetting Agents: Surfactants that reduce the surface tension of the plating solution, improving the wetting of the substrate and the distribution of the metal ions.
Operating Conditions
In addition to the composition of the plating solution, the operating conditions of the plating bath also play a crucial role in determining the quality and properties of the deposited metal layer. Key operating parameters include:
- Temperature: Plating baths are typically operated at elevated temperatures, usually between 20-60°C, to increase the rate of metal deposition and improve the quality of the deposited layer.
- Current Density: The current density, measured in amperes per square meter (A/m2), determines the rate of metal deposition and the thickness of the deposited layer. Higher current densities generally result in faster plating rates but may also lead to increased porosity and reduced adhesion.
- Agitation: Plating baths are often agitated using air sparging, mechanical stirring, or cathode movement to ensure a uniform distribution of metal ions and additives, preventing local depletion and improving the quality of the deposited layer.
- Filtration: Continuous filtration of the plating solution helps to remove particulate contaminants and maintain the cleanliness of the bath, improving the quality and consistency of the plated finish.
Benefits of Using Plating Index Solutions
Using plating index solutions offers several benefits for electroplating processes, including:
- Consistency: Plating index solutions provide a standardized reference point for plating bath composition and operating conditions, ensuring consistent results across different plating facilities and applications.
- Quality: By adhering to the recommended formulations and operating parameters, plating index solutions help to optimize the quality and properties of the deposited metal layer, such as brightness, smoothness, and adhesion.
- Troubleshooting: Plating index solutions serve as a starting point for troubleshooting plating issues, allowing operators to identify deviations from the standard formulation and make necessary adjustments to restore optimal performance.
- Cost Savings: By ensuring consistent, high-quality results, plating index solutions help to reduce the incidence of rejects and rework, leading to cost savings in terms of materials, labor, and energy consumption.
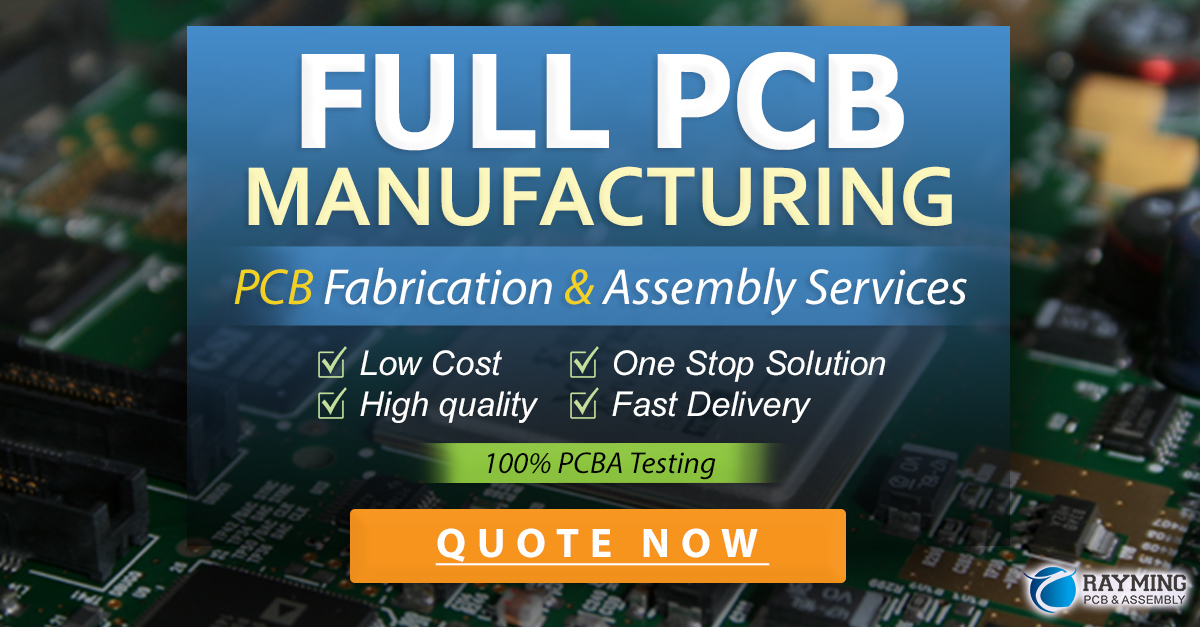
Monitoring and Maintaining Plating Solutions
To ensure the consistent performance of plating solutions, regular monitoring and maintenance are essential. Key aspects of plating solution management include:
Chemical Analysis
Periodic chemical analysis of the plating solution is necessary to monitor the concentrations of key components, such as metal ions, complexing agents, and additives. This can be done using techniques such as atomic absorption spectroscopy (AAS), inductively coupled plasma (ICP) analysis, or titration. Based on the results of the analysis, additions can be made to maintain the desired composition of the plating solution.
Hull Cell Testing
Hull cell testing is a simple and effective method for evaluating the performance of a plating solution under varying current densities. A Hull cell is a trapezoidal-shaped plating tank that allows for the deposition of a metal layer under a range of current densities in a single test. By visually inspecting the plated panel, operators can assess the brightness, smoothness, and coverage of the deposit at different current densities, helping to identify any issues with the plating solution or operating conditions.
Filtration and Carbon Treatment
Regular filtration and carbon treatment of the plating solution help to remove particulate contaminants and organic impurities that can accumulate over time. Filtration is typically done using cartridge filters or filter press systems, while carbon treatment involves passing the solution through activated carbon beds to adsorb organic compounds. These maintenance practices help to extend the life of the plating solution and ensure consistent, high-quality results.
Frequently Asked Questions (FAQ)
-
What is the difference between a plating solution and a plating index solution?
A plating solution is a general term for any electrolyte used in the electroplating process, while a plating index solution is a standardized formulation that serves as a reference point for plating bath composition and operating conditions. -
How often should I analyze my plating solution?
The frequency of chemical analysis depends on factors such as the plating solution type, the production volume, and the sensitivity of the application. As a general rule, high-volume production baths should be analyzed daily, while lower-volume baths may be analyzed weekly or monthly. -
Can I use a plating index solution for any substrate material?
Plating index solutions are designed for specific metal-substrate combinations, taking into account factors such as adhesion, compatibility, and desired properties. It is essential to select a plating index solution that is appropriate for the specific substrate material and application. -
What should I do if my plating solution is not performing as expected?
If your plating solution is not yielding the desired results, first check the composition and operating conditions against the plating index solution recommendations. Perform chemical analysis and Hull cell testing to identify any deviations or issues. Based on the findings, make necessary adjustments to the solution composition or operating parameters to restore optimal performance. -
How can I extend the life of my plating solution?
To extend the life of your plating solution, implement regular monitoring and maintenance practices, such as chemical analysis, filtration, and carbon treatment. Maintain the solution within the recommended operating parameters, and make timely additions to replenish consumed components. Proper care and maintenance can significantly extend the usable life of a plating solution, reducing waste and costs.
In conclusion, plating index solutions are essential tools for ensuring consistent, high-quality results in electroplating processes. By providing standardized formulations and operating parameters, plating index solutions help to optimize the performance of plating baths, reduce the incidence of defects, and minimize costs. Through regular monitoring and maintenance, plating solutions can be effectively managed to deliver superior plated finishes across a wide range of applications.
Leave a Reply