Composition of PCB Prepreg
PCB Prepreg is composed of two main components:
- Reinforcement fabric
- Thermosetting resin
Reinforcement Fabric
The reinforcement fabric used in PCB Prepreg is most commonly glass fiber, although other materials such as aramid or carbon fiber can be used for specific applications. The fabric is woven into a pattern, with the most common being plain weave and twill weave.
Weave Type | Description |
---|---|
Plain Weave | Simple over-under pattern, provides good stability and strength |
Twill Weave | Diagonal pattern, offers better drape and flexibility |
The choice of reinforcement fabric depends on the desired properties of the final PCB, such as thermal stability, electrical insulation, and mechanical strength.
Thermosetting Resin
The thermosetting resin used in PCB Prepreg is typically an epoxy-based material. The resin is partially cured, or “B-staged,” meaning that it has been heated to a point where it has begun to polymerize but has not fully cross-linked. This allows the Prepreg to remain flexible and easy to handle during the PCB manufacturing process.
The resin serves several purposes:
- Insulation between conductive layers
- Adhesion of layers during lamination
- Protection of the reinforcement fabric from mechanical damage
Manufacturing Process
The manufacturing process of PCB Prepreg involves several steps:
- Impregnation
- Drying
- Cutting
- Packaging
Impregnation
The reinforcement fabric is first fed through a bath containing the liquid thermosetting resin. The fabric is thoroughly saturated with the resin, ensuring even distribution throughout the material.
Drying
After impregnation, the fabric is passed through a series of heated rollers to remove excess resin and partially cure the material. The temperature and duration of this process are carefully controlled to achieve the desired degree of cure, or “B-stage.”
Cutting
Once the PCB Prepreg has been dried and partially cured, it is cut to the required dimensions. This is typically done using a computerized cutting machine to ensure precise and consistent sizing.
Packaging
The cut Prepreg sheets are then packaged in a moisture-resistant material, such as plastic film, to protect them from humidity and contamination during storage and transportation.
Properties of PCB Prepreg
PCB Prepreg exhibits several key properties that make it an essential material in the manufacturing of high-quality PCBs:
- Insulation
- Adhesion
- Mechanical strength
- Thermal stability
Insulation
The thermosetting resin in PCB Prepreg provides excellent electrical insulation between the conductive layers of the PCB. This insulation is crucial for preventing short circuits and ensuring the proper functioning of the electronic components.
Adhesion
During the lamination process, the partially cured resin in the Prepreg melts and flows, bonding the layers of the PCB together. This adhesion is essential for maintaining the structural integrity of the final PCB Assembly.
Mechanical Strength
The combination of the reinforcement fabric and the thermosetting resin gives PCB Prepreg excellent mechanical strength. This strength is necessary to withstand the stresses encountered during the manufacturing process and the end-use of the PCB.
Thermal Stability
PCB Prepreg is designed to maintain its properties over a wide range of temperatures. This thermal stability is essential for ensuring the reliability of the PCB in various operating conditions.
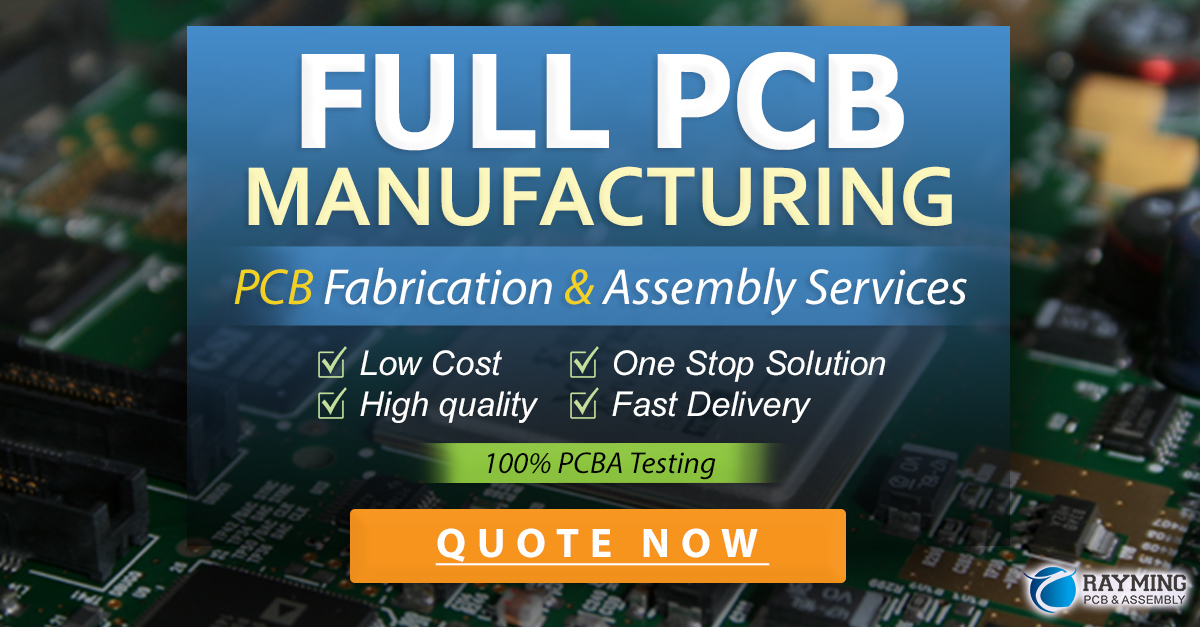
Types of PCB Prepreg
There are several types of PCB Prepreg available, each with its own unique properties and applications:
- FR-4 Prepreg
- High Tg Prepreg
- Halogen-free Prepreg
- Low-loss Prepreg
FR-4 Prepreg
FR-4 Prepreg is the most common type used in the manufacturing of PCBs. It is made with a glass fiber reinforcement fabric and an epoxy resin. FR-4 Prepreg offers good mechanical strength, electrical insulation, and thermal stability, making it suitable for a wide range of applications.
High Tg Prepreg
High Tg Prepreg is designed for use in high-temperature applications. It is made with a specialized resin that has a higher glass transition temperature (Tg) than standard FR-4 Prepreg. This allows the PCB to maintain its properties at elevated temperatures, making it ideal for automotive, aerospace, and military applications.
Halogen-free Prepreg
Halogen-free Prepreg is made with a resin that does not contain any halogenated compounds, such as bromine or chlorine. This type of Prepreg is becoming increasingly popular due to environmental and health concerns associated with halogenated materials. Halogen-free Prepreg offers similar performance to standard FR-4 Prepreg, making it a viable alternative for many applications.
Low-loss Prepreg
Low-loss Prepreg is designed for use in high-frequency applications, such as 5G communication networks. It is made with a specialized resin that has a lower dielectric constant and dissipation factor than standard FR-4 Prepreg. This reduces signal loss and improves the overall performance of the PCB in high-frequency applications.
Prepreg Type | Key Features |
---|---|
FR-4 Prepreg | Standard material, suitable for most applications |
High Tg Prepreg | Maintains properties at high temperatures |
Halogen-free Prepreg | Environmentally friendly, no halogenated compounds |
Low-loss Prepreg | Suitable for high-frequency applications |
Applications of PCB Prepreg
PCB Prepreg is used in a wide range of applications, including:
- Consumer electronics
- Automotive electronics
- Aerospace and defense
- Medical devices
- Industrial equipment
The specific type of Prepreg used in each application depends on the unique requirements and operating conditions of the final product.
Frequently Asked Questions (FAQ)
-
Q: What is the difference between PCB Prepreg and core material?
A: PCB Prepreg is a pre-impregnated material that is partially cured, while core material is fully cured. Prepreg is used to bond the layers of a PCB together during the lamination process, while core material is used as the base substrate for the PCB. -
Q: Can PCB Prepreg be stored for long periods?
A: PCB Prepreg has a limited shelf life due to the partial cure of the resin. It is typically recommended to store Prepreg in a cool, dry place and use it within 6 months of manufacture to ensure optimal performance. -
Q: How does the choice of reinforcement fabric affect the properties of PCB Prepreg?
A: The choice of reinforcement fabric can impact the mechanical strength, thermal stability, and electrical properties of the PCB Prepreg. For example, glass fiber provides good overall performance, while aramid fiber offers higher strength and thermal stability. -
Q: What is the role of the resin in PCB Prepreg?
A: The resin in PCB Prepreg serves several purposes, including providing electrical insulation between conductive layers, bonding the layers together during lamination, and protecting the reinforcement fabric from mechanical damage. -
Q: How do I choose the right type of PCB Prepreg for my application?
A: The choice of PCB Prepreg depends on the specific requirements of your application, such as operating temperature, frequency, and environmental conditions. Consult with your PCB manufacturer or material supplier to select the most suitable type of Prepreg for your needs.
In conclusion, PCB Prepreg is a critical material in the manufacturing of high-quality printed circuit boards. Its unique composition and properties enable the production of PCBs with excellent electrical insulation, mechanical strength, and thermal stability. By understanding the different types of Prepreg available and their specific characteristics, engineers and manufacturers can select the most appropriate material for their applications, ensuring the optimal performance and reliability of their electronic devices.
Leave a Reply