The Need for Lead-free Electronics
Lead has been widely used in electronic components and solders due to its favorable properties, such as low melting point, good electrical conductivity, and ability to form strong bonds. However, lead is a toxic substance that can cause serious health issues, especially in children. Exposure to lead can occur through various means, including:
- Inhalation of lead dust or fumes
- Ingestion of lead-contaminated food or water
- Skin contact with lead-containing materials
The negative health effects of lead exposure include:
- Neurological damage
- Developmental delays in children
- Kidney damage
- Reproductive issues
- Increased risk of cardiovascular disease
To minimize these risks and protect both human health and the environment, regulations have been implemented to restrict the use of lead in electronic products.
Regulations Driving the Adoption of HAL lead-free
RoHS Directive
The Restriction of Hazardous Substances (RoHS) directive is a set of regulations adopted by the European Union (EU) in 2003. The directive aims to restrict the use of six hazardous materials, including lead, in the manufacture of various types of electronic and electrical equipment. The RoHS directive has undergone several revisions, with the most recent being RoHS 3, which came into effect in July 2019.
Under the RoHS directive, the maximum concentration value for lead is 0.1% by weight in homogeneous materials. This means that electronic components and solders used in products covered by the directive must contain less than 0.1% lead by weight.
Other Regulations
In addition to the EU’s RoHS directive, other countries and regions have implemented similar regulations to restrict the use of lead in electronics:
- China RoHS
- Korea RoHS
- California RoHS
- Japan RoHS
These regulations have varying scopes and implementation timelines but share the common goal of reducing the environmental and health impacts of lead in electronic products.
Challenges in Transitioning to HAL Lead-free
The transition to HAL lead-free electronics has presented several challenges for manufacturers and the electronics industry as a whole.
Higher Melting Point of Lead-free Solders
Lead-free solders typically have higher melting points compared to traditional lead-based solders. For example, the commonly used lead-free solder alloy Sn96.5Ag3.0Cu0.5 (SAC305) has a melting point of approximately 217°C, while the lead-based solder alloy Sn63Pb37 has a melting point of around 183°C. This difference in melting points has several implications:
- Higher processing temperatures are required, which can increase energy consumption and costs.
- Higher temperatures can cause thermal stress on components, leading to potential reliability issues.
- Existing manufacturing equipment may need to be upgraded or replaced to accommodate the higher temperatures.
Compatibility Issues
The transition to lead-free solders has also raised concerns about compatibility between lead-free and lead-based components. In some cases, mixing lead-free and lead-based solders can result in the formation of intermetallic compounds that can weaken solder joints and affect the reliability of the electronic assembly.
To address this issue, manufacturers must ensure that all components and solders used in a lead-free assembly are compatible with each other. This may require additional testing and validation processes to guarantee the reliability and performance of the final product.
Reliability Concerns
The long-term reliability of lead-free solder joints has been a topic of discussion and research within the electronics industry. Some studies have suggested that lead-free solder joints may be more susceptible to certain failure modes, such as:
- Tin whisker formation: Tin whiskers are thin, conductive filaments that can grow from pure tin surfaces, potentially causing short circuits and other reliability issues.
- Solder joint fatigue: Lead-free solder joints may be more prone to fatigue failures under certain conditions, such as high-temperature cycling or mechanical stress.
To mitigate these concerns, manufacturers have developed various strategies, including:
- Using alternative lead-free solder alloys with improved properties
- Implementing additional process controls and quality assurance measures
- Conducting extensive reliability testing to validate the performance of lead-free assemblies
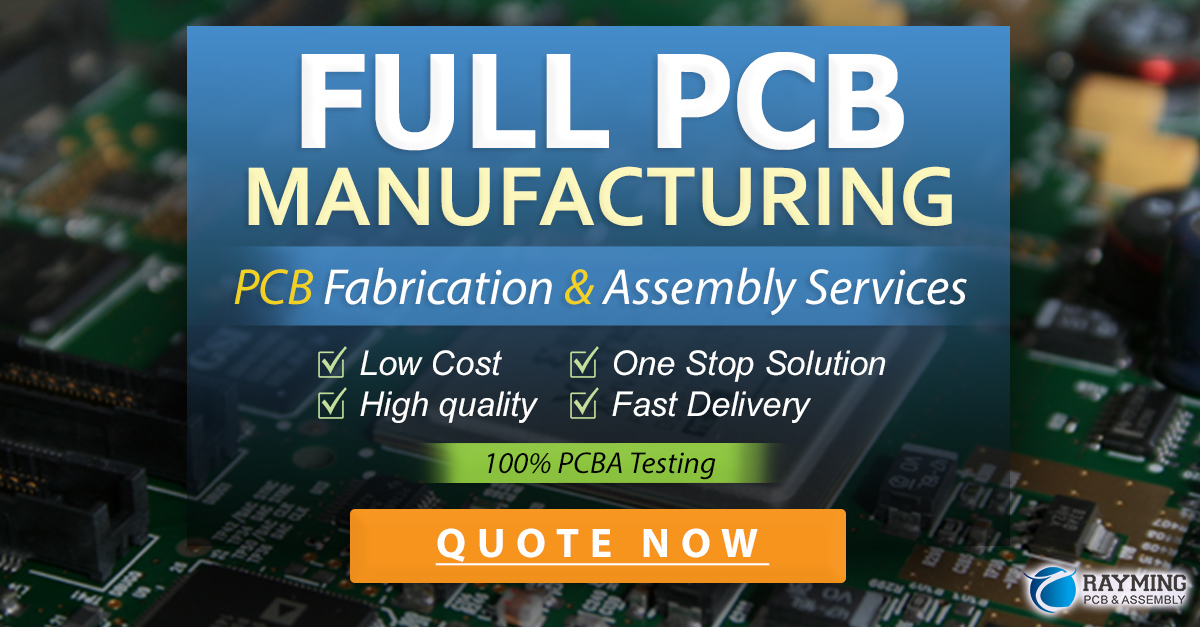
Alternatives to Lead in Electronic Components and Solders
To comply with HAL lead-free regulations and address the challenges associated with lead-free electronics, manufacturers have developed various alternative materials and alloys.
Lead-free Solder Alloys
Several lead-free solder alloys have been developed to replace traditional lead-based solders. These alloys typically contain a combination of tin (Sn), silver (Ag), and copper (Cu). Some common lead-free solder alloys include:
Alloy | Composition | Melting Point (°C) |
---|---|---|
SAC305 | Sn96.5Ag3.0Cu0.5 | 217-220 |
SAC387 | Sn95.5Ag3.8Cu0.7 | 217-219 |
SAC405 | Sn95.5Ag4.0Cu0.5 | 217-219 |
Sn99.3Cu0.7 | Sn99.3Cu0.7 | 227 |
SnAg3.5 | Sn96.5Ag3.5 | 221 |
These lead-free solder alloys have been designed to provide similar or improved performance compared to lead-based solders while meeting the requirements of HAL lead-free regulations.
Alternative Component Finishes
In addition to lead-free solders, manufacturers have also developed alternative finishes for electronic components to eliminate lead content. Some common lead-free component finishes include:
- Nickel/Palladium/Gold (NiPdAu)
- Nickel/Gold (NiAu)
- Immersion Tin (ImSn)
- Immersion Silver (ImAg)
These finishes provide a lead-free surface for component terminations and help ensure compatibility with lead-free soldering processes.
Implementing HAL Lead-free in Electronic Manufacturing
Transitioning to HAL lead-free electronics requires a comprehensive approach that involves various aspects of the manufacturing process.
Process Adjustments
To accommodate the higher melting points of lead-free solders, manufacturers may need to make adjustments to their soldering processes. This can include:
- Increasing the peak reflow temperature
- Adjusting the reflow profile to ensure proper solder joint formation
- Modifying wave soldering parameters
- Updating hand soldering techniques and tools
These process adjustments help ensure that lead-free solders are properly melted and form reliable solder joints.
Supply Chain Management
Implementing HAL lead-free electronics also requires close collaboration with suppliers to ensure that all components and materials used in the manufacturing process are compliant with lead-free regulations. This involves:
- Communicating lead-free requirements to suppliers
- Obtaining certifications and documentation to verify lead-free compliance
- Conducting incoming inspections to ensure that received components meet lead-free specifications
- Managing inventory to separate lead-free and non-lead-free materials
Effective supply chain management is crucial for maintaining the integrity of the lead-free manufacturing process and ensuring compliance with HAL lead-free regulations.
Training and Education
Transitioning to HAL lead-free electronics requires a skilled and knowledgeable workforce. Manufacturers should provide training and education to their employees to ensure that they are familiar with:
- The rationale behind lead-free electronics
- The specific requirements of HAL lead-free regulations
- The challenges and best practices associated with lead-free manufacturing processes
- The importance of maintaining lead-free compliance throughout the manufacturing process
By investing in employee training and education, manufacturers can build a strong foundation for successful HAL lead-free implementation.
FAQ
-
What does HAL lead-free stand for?
HAL lead-free stands for “Hazardous Air pollutants Lead-free,” referring to electronic components and solders that do not contain lead (Pb). -
Why is it important to use lead-free electronics?
Lead is a toxic substance that can cause serious health issues, such as neurological damage, developmental delays, and kidney damage. Using lead-free electronics helps minimize the risks associated with lead exposure and protects both human health and the environment. -
What are some common lead-free solder alloys?
Common lead-free solder alloys include SAC305 (Sn96.5Ag3.0Cu0.5), SAC387 (Sn95.5Ag3.8Cu0.7), SAC405 (Sn95.5Ag4.0Cu0.5), Sn99.3Cu0.7, and SnAg3.5 (Sn96.5Ag3.5). These alloys provide similar or improved performance compared to lead-based solders while meeting HAL lead-free regulations. -
What challenges are associated with transitioning to lead-free electronics?
Challenges in transitioning to lead-free electronics include higher melting points of lead-free solders, compatibility issues between lead-free and lead-based components, and concerns about the long-term reliability of lead-free solder joints. Manufacturers must address these challenges through process adjustments, supply chain management, and employee training. -
How can manufacturers ensure compliance with HAL lead-free regulations?
To ensure compliance with HAL lead-free regulations, manufacturers should closely collaborate with suppliers, obtain certifications and documentation verifying lead-free compliance, conduct incoming inspections, and manage inventory to separate lead-free and non-lead-free materials. Employee training and education are also crucial for maintaining lead-free compliance throughout the manufacturing process.
Conclusion
The transition to HAL lead-free electronics is a critical step in minimizing the environmental and health risks associated with lead exposure. Driven by regulations such as the RoHS directive, manufacturers have developed alternative materials and processes to produce lead-free electronic components and assemblies.
While the transition to lead-free electronics presents challenges, such as higher melting points and compatibility issues, manufacturers can overcome these hurdles through process adjustments, supply chain management, and employee training. By implementing HAL lead-free practices, the electronics industry can contribute to a safer and more sustainable future.
As regulations continue to evolve and consumer awareness of environmental and health issues grows, the demand for lead-free electronics is expected to increase. Manufacturers that embrace HAL lead-free practices and stay ahead of regulatory requirements will be well-positioned to meet this demand and demonstrate their commitment to responsible and sustainable electronics production.
Leave a Reply