What are the Advantages of Flexible PCB?
Flexible PCBs offer several advantages over traditional rigid PCBs, including:
Space Savings
One of the main advantages of flexible PCBs is that they can save space in electronic devices. Because they can be bent and folded, flexible PCBs can be mounted in tight spaces where rigid PCBs would not fit. This is particularly useful in applications such as smartphones, wearable devices, and medical equipment where space is at a premium.
Increased Reliability
Flexible PCBs are also more reliable than rigid PCBs in certain applications. Because they can conform to the shape of the device, they are less likely to be damaged by vibration or shock. This makes them ideal for use in automotive and aerospace applications where reliability is critical.
Reduced Weight
Another advantage of flexible PCBs is that they are typically lighter than rigid PCBs. This is because they use thinner materials and require fewer connectors and other components. This can be particularly important in applications such as drones and satellites where every gram counts.
Improved Signal Integrity
Flexible PCBs can also offer improved signal integrity compared to rigid PCBs. Because they can be designed with shorter trace lengths and fewer connectors, they can reduce signal loss and distortion. This is particularly important in high-frequency applications such as 5G wireless communication.
What are the Applications of Flexible PCB?
Flexible PCBs are used in a wide range of applications across various industries, including:
Consumer Electronics
Flexible PCBs are widely used in consumer electronics such as smartphones, tablets, and wearable devices. They allow for thinner and more compact designs while also improving reliability and signal integrity.
Medical Devices
Flexible PCBs are also used in medical devices such as hearing aids, pacemakers, and implantable sensors. They allow for smaller and more comfortable devices while also providing the necessary reliability and functionality.
Automotive Electronics
In the automotive industry, flexible PCBs are used in applications such as dashboard displays, sensors, and control modules. They offer increased reliability and space savings compared to rigid PCBs.
Aerospace and Defense
Flexible PCBs are also used in aerospace and defense applications such as satellites, drones, and military equipment. They offer reduced weight and increased reliability in these demanding environments.
What are the Different Types of Flexible PCB?
There are several different types of flexible PCBs, each with its own unique characteristics and applications. Some of the most common types include:
Single-Sided Flexible PCB
Single-sided flexible PCBs have conductive traces on only one side of the substrate. They are the simplest and most cost-effective type of flexible PCB, but they are also the least dense and have the lowest number of layers.
Double-Sided Flexible PCB
Double-sided flexible PCBs have conductive traces on both sides of the substrate, allowing for higher density and more complex designs. They are more expensive than single-sided PCBs but offer greater flexibility and functionality.
Multi-Layer Flexible PCB
Multi-layer flexible PCBs have three or more conductive layers separated by insulating layers. They offer the highest density and most complex designs but are also the most expensive type of flexible PCB.
Rigid-Flex PCB
Rigid-flex PCBs combine both rigid and flexible sections in a single board. The rigid sections provide structural support and allow for the mounting of components, while the flexible sections allow for bending and folding. This type of PCB is often used in applications where both flexibility and rigidity are required, such as in aerospace and medical devices.
Type of Flexible PCB | Advantages | Disadvantages |
---|---|---|
Single-Sided | – Low cost – Simple design |
– Low density – Limited functionality |
Double-Sided | – Higher density – More complex designs |
– Higher cost than single-sided |
Multi-Layer | – Highest density – Most complex designs |
– Highest cost |
Rigid-Flex | – Combines flexibility and rigidity – Ideal for certain applications |
– Complex design – Higher cost than standard flexible PCBs |
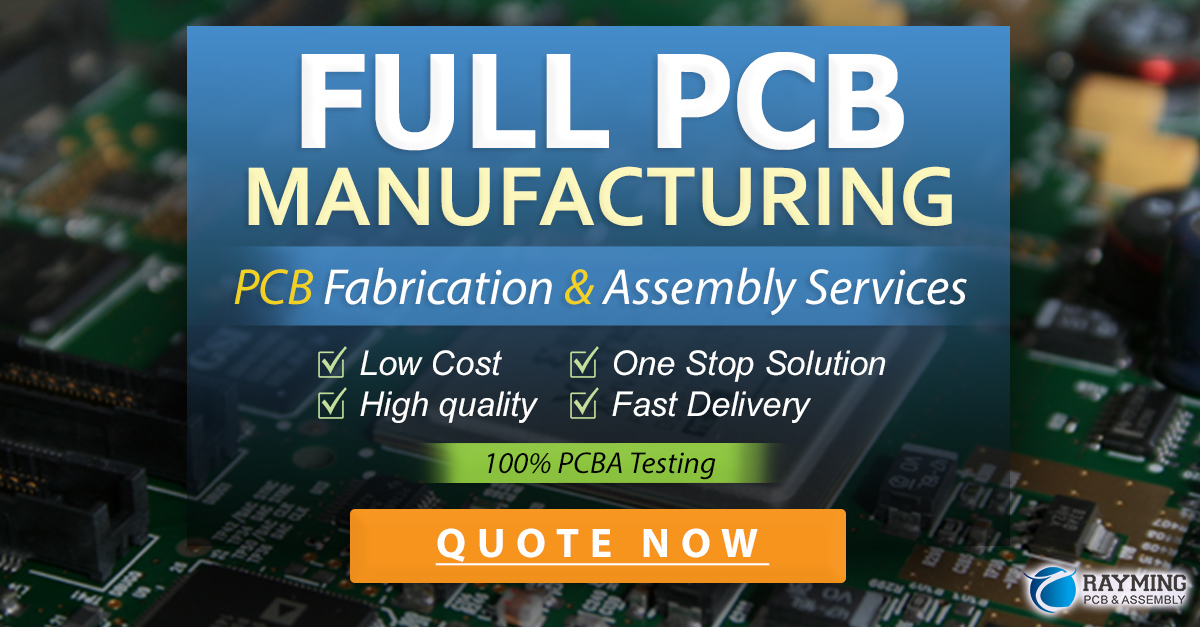
How are Flexible PCBs Manufactured?
The manufacturing process for flexible PCBs is similar to that of rigid PCBs, but with a few key differences. The basic steps include:
-
Creating the Circuit Design: The first step is to create the circuit design using computer-aided design (CAD) software. This includes laying out the conductive traces, pads, and other features of the PCB.
-
Printing the Circuit: Once the design is complete, it is printed onto a flexible substrate material, typically using a screen printing or photolithography process. The substrate is usually made of a polymer material such as polyimide or polyester.
-
Etching the Circuit: After the circuit is printed, the unwanted copper is etched away using a chemical process, leaving only the desired conductive traces.
-
Laminating the Layers: If the PCB has multiple layers, they are laminated together using heat and pressure. The layers are separated by insulating materials to prevent short circuits.
-
Adding Components: Finally, the components are added to the PCB using surface mount or through-hole technology. The components are typically smaller and more compact than those used on rigid PCBs to maximize flexibility.
What are the Challenges of Designing and Manufacturing Flexible PCBs?
While flexible PCBs offer many advantages, they also present some unique challenges in design and manufacturing. Some of the key challenges include:
Material Selection
Choosing the right materials for a flexible PCB is critical to ensure the desired performance and reliability. The substrate material must be flexible enough to allow for bending and folding, but also strong enough to withstand the stresses of use. The conductive traces must also be able to withstand repeated bending without cracking or breaking.
Mechanical Stress
Flexible PCBs are subject to mechanical stresses during use, such as bending, twisting, and stretching. These stresses can cause the conductive traces to crack or break, leading to electrical failures. Designers must carefully consider the mechanical stresses that the PCB will be subjected to and design the circuit accordingly.
Thermal Management
Flexible PCBs can be more challenging to cool than rigid PCBs due to their thinner and more compact design. Designers must carefully consider the thermal management of the PCB to ensure that it does not overheat during use.
Manufacturing Processes
Manufacturing flexible PCBs requires specialized equipment and processes that are different from those used for rigid PCBs. This can make the manufacturing process more complex and costly, particularly for high-volume production.
FAQ
-
Q: What is the difference between a flexible PCB and a rigid PCB?
A: A flexible PCB is designed to be bendable and can conform to various shapes, while a rigid PCB is a traditional circuit board that is stiff and cannot be bent. -
Q: What are the benefits of using a flexible PCB?
A: Flexible PCBs offer several benefits, including space savings, increased reliability, reduced weight, and improved signal integrity. They are also ideal for applications where flexibility and conformity to shape are important. -
Q: What industries commonly use flexible PCBs?
A: Flexible PCBs are used in a variety of industries, including consumer electronics, medical devices, automotive electronics, aerospace, and defense. -
Q: Are flexible PCBs more expensive than rigid PCBs?
A: In general, flexible PCBs are more expensive than rigid PCBs due to the specialized materials and manufacturing processes required. However, the cost can be justified in applications where the benefits of flexibility and space savings are critical. -
Q: What are some of the challenges in designing and manufacturing flexible PCBs?
A: Some of the key challenges in designing and manufacturing flexible PCBs include material selection, mechanical stress, thermal management, and specialized manufacturing processes. Designers must carefully consider these factors to ensure the desired performance and reliability of the PCB.
In conclusion, flexible PCBs offer a range of benefits over traditional rigid PCBs, including space savings, increased reliability, reduced weight, and improved signal integrity. They are used in a variety of industries where flexibility and conformity to shape are important, such as consumer electronics, medical devices, and automotive electronics.
However, designing and manufacturing flexible PCBs also presents some unique challenges, such as material selection, mechanical stress, and thermal management. As the demand for smaller and more compact electronic devices continues to grow, the use of flexible PCBs is likely to increase in the coming years.
Leave a Reply