Properties of Copper Foil
Copper foil possesses several unique properties that make it an essential material in many applications:
Electrical Conductivity
One of the most notable properties of copper foil is its exceptional electrical conductivity. Copper is one of the best conductors of electricity, second only to silver. This property makes copper foil an ideal material for use in electrical and electronic applications, such as printed circuit boards (PCBs), transformers, and electromagnetic shielding.
Thermal Conductivity
In addition to its excellent electrical conductivity, copper foil also exhibits high thermal conductivity. This means that it can efficiently transfer heat from one point to another, making it useful in applications that require heat dissipation, such as heat sinks and thermal interfaces.
Malleability and Ductility
Copper foil is highly malleable and ductile, which means it can be easily shaped and formed without breaking. This property allows manufacturers to create intricate designs and patterns using copper foil, making it a popular material in art and crafts.
Corrosion Resistance
Copper foil has a natural resistance to corrosion, particularly in dry environments. When exposed to air, copper forms a thin layer of copper oxide on its surface, which acts as a protective barrier against further corrosion. However, in humid or acidic environments, copper foil may be prone to more rapid corrosion.
Manufacturing Process of Copper Foil
Copper foil is typically manufactured using one of two methods: electrodeposition or rolling.
Electrodeposition
Electrodeposition is the most common method for producing thin copper foil, particularly for use in electronic applications. The process involves the following steps:
- A rotating stainless steel drum is partially immersed in an electrolytic solution containing copper ions.
- An electric current is applied, causing the copper ions to deposit onto the surface of the drum, forming a thin layer of copper foil.
- As the drum rotates, the copper foil is continuously deposited and grows in thickness.
- Once the desired thickness is achieved, the copper foil is peeled off the drum and wound onto a roll.
Electrodeposited copper foil can be produced in thicknesses ranging from 5 to 105 microns (μm) and widths up to 1.5 meters.
Rolling
Rolling is another method for producing copper foil, typically used for thicker foils or applications that require higher mechanical strength. The process involves the following steps:
- A thick copper sheet is passed through a series of rolling mills, which gradually reduce its thickness.
- The copper sheet is annealed (heat-treated) between rolling passes to maintain its malleability and prevent cracking.
- Once the desired thickness is achieved, the copper foil is trimmed to the required width and wound onto a roll.
Rolled copper foil can be produced in thicknesses ranging from 10 to 200 microns (μm) and widths up to 1 meter.
Applications of Copper Foil
Copper foil finds use in a wide range of industries and applications, thanks to its unique combination of properties. Some of the most common applications include:
Electronics
Copper foil is extensively used in the electronics industry, particularly in the production of printed circuit boards (PCBs). PCBs are the backbone of modern electronic devices, providing a platform for mounting and interconnecting electronic components. Copper foil is used to create the conductive traces on the PCB, which carry electrical signals between components.
In addition to PCBs, copper foil is also used in the manufacturing of other electronic components, such as:
- Transformers: Copper foil is wound around a core to create the primary and secondary windings of a transformer, which is used to step up or step down voltage in electrical systems.
- Electromagnetic shielding: Copper foil can be used to create barriers that block electromagnetic interference (EMI) from affecting sensitive electronic devices.
- Batteries: Copper foil is used as a current collector in some types of batteries, such as lithium-ion batteries, due to its high electrical conductivity and low resistance.
Art and Crafts
Copper foil is a popular material in the art and crafts industry, particularly in stained glass work and jewelry making.
In stained glass, copper foil is used to wrap the edges of glass pieces before soldering them together. This technique, known as the Tiffany method, allows for the creation of intricate and detailed stained glass designs.
In jewelry making, copper foil is used to create unique and eye-catching pieces. It can be embossed, etched, or painted to create various textures and patterns, and then shaped into pendants, earrings, or other decorative elements.
Construction
Copper foil is also used in the construction industry, primarily for its weatherproofing and moisture-resistant properties.
In roofing applications, copper foil is used as an underlayment beneath shingles or tiles to provide an additional layer of protection against water infiltration. It is also used to flash around chimneys, vents, and other roof penetrations to prevent leaks.
In wall construction, copper foil can be used as a vapor barrier to prevent moisture from penetrating the walls and causing damage to the structure. It is particularly useful in bathrooms, kitchens, and other areas prone to high humidity.
Automotive
Copper foil finds several applications in the automotive industry, primarily due to its electrical conductivity and heat dissipation properties.
In electric vehicles (EVs), copper foil is used in the construction of the battery pack, where it serves as a current collector and helps to distribute heat evenly throughout the pack. This helps to maintain optimal battery performance and extends the life of the battery.
Copper foil is also used in the manufacturing of various automotive electrical components, such as wiring harnesses, connectors, and sensors. Its high electrical conductivity ensures reliable and efficient power transmission throughout the vehicle.
Medical
Copper foil has several applications in the medical industry, thanks to its antimicrobial properties and electrical conductivity.
In medical equipment, copper foil is used to create conductive traces on flexible printed circuits (FPCs), which are used in devices such as blood pressure monitors, heart rate monitors, and other wearable medical devices. The flexibility of copper foil allows these devices to be comfortable and unobtrusive for patients to wear.
Copper foil is also used in the manufacturing of antimicrobial touch surfaces, such as door handles and push plates in hospitals and other healthcare facilities. The natural antimicrobial properties of copper help to reduce the spread of infections and maintain a hygienic environment.
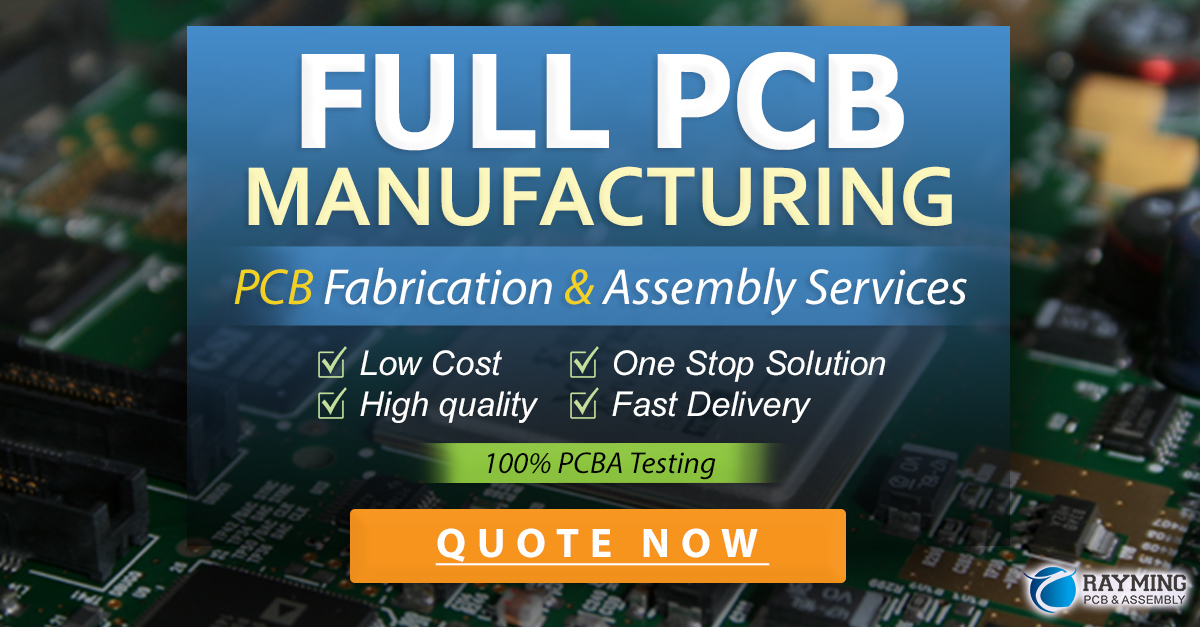
Copper Foil Thickness and Weight
Copper foil is available in a range of thicknesses and weights to suit various applications. The thickness of copper foil is typically measured in microns (μm) or mils (thousandths of an inch), while the weight is expressed in ounces per square foot (oz/ft²).
The following table provides a comparison of common copper foil thicknesses and their corresponding weights:
Thickness (μm) | Thickness (mils) | Weight (oz/ft²) |
---|---|---|
18 | 0.7 | 0.5 |
35 | 1.4 | 1.0 |
70 | 2.8 | 2.0 |
105 | 4.1 | 3.0 |
152 | 6.0 | 4.0 |
It’s important to choose the appropriate thickness and weight of copper foil for a given application, as this can impact the performance, durability, and cost of the final product.
Copper Foil vs. Other Materials
Copper foil is often compared to other materials that serve similar purposes, such as aluminum foil and conductive inks.
Copper Foil vs. Aluminum Foil
While both copper and aluminum foils are used in various applications, they have some key differences:
- Electrical conductivity: Copper foil has a higher electrical conductivity than aluminum foil, making it more suitable for applications that require efficient power transmission.
- Thermal conductivity: Copper foil also has a higher thermal conductivity than aluminum foil, which makes it better suited for applications that require heat dissipation.
- Cost: Aluminum foil is generally less expensive than copper foil, which can make it a more cost-effective choice for certain applications.
- Weight: Aluminum foil is lighter than copper foil, which can be advantageous in applications where weight is a critical factor, such as in aerospace and automotive industries.
Copper Foil vs. Conductive Inks
Conductive inks are another material used in the creation of conductive traces and patterns, particularly in printed electronics. Compared to copper foil, conductive inks have some advantages and disadvantages:
- Flexibility: Conductive inks can be printed on a wide range of flexible substrates, such as paper, plastic, and fabric, making them suitable for applications that require conformable or stretchable electronics.
- Processing: Conductive inks can be applied using various printing methods, such as screen printing, inkjet printing, and gravure printing, which can be faster and more cost-effective than working with copper foil for certain applications.
- Electrical conductivity: While conductive inks have improved in recent years, they still have a lower electrical conductivity compared to copper foil, which can limit their use in applications that require high current carrying capacity.
- Durability: Copper foil is generally more durable and resistant to wear and tear than conductive inks, which can be more susceptible to cracking or flaking over time.
FAQ
-
What is the difference between electrodeposited and rolled copper foil?
Electrodeposited copper foil is produced by depositing copper ions onto a rotating stainless steel drum in an electrolytic solution, while rolled copper foil is produced by passing a thick copper sheet through a series of rolling mills to reduce its thickness. Electrodeposited copper foil is generally thinner and more suitable for electronic applications, while rolled copper foil is thicker and offers higher mechanical strength. -
Can copper foil be soldered?
Yes, copper foil can be easily soldered using standard soldering techniques. Its excellent electrical conductivity and malleability make it well-suited for soldering in electronic applications, such as in the assembly of printed circuit boards (PCBs) and stained glass artwork. -
Is copper foil toxic?
Copper foil itself is not toxic; however, exposure to copper dust or fumes can be harmful if inhaled or ingested in large quantities. When working with copper foil, it is essential to follow proper safety guidelines, such as wearing protective gloves and working in a well-ventilated area to minimize exposure to copper dust. -
How long does copper foil last?
The lifespan of copper foil depends on various factors, such as the environment it is exposed to and the application in which it is used. In dry, indoor environments, copper foil can last for decades without significant deterioration. However, in humid or acidic environments, copper foil may be prone to more rapid corrosion, which can shorten its lifespan. -
Can copper foil be recycled?
Yes, copper foil is recyclable. Copper is a valuable material that can be recycled indefinitely without losing its properties. Recycling copper foil helps to conserve natural resources, reduce energy consumption, and minimize waste in landfills. Many scrap metal recycling facilities accept copper foil, and the recycled copper can be used to produce new copper products.
In conclusion, copper foil is a versatile and essential material with a wide range of applications across various industries. Its unique combination of properties, including excellent electrical and thermal conductivity, malleability, and durability, make it an indispensable component in electronics, art, construction, automotive, and medical fields. As technology continues to advance, the demand for copper foil is expected to grow, driving innovation and development in the manufacturing and application of this remarkable material.
Leave a Reply