What is Arc Flash?
Arc flash is an explosive electrical event that occurs when a high-voltage current jumps across an air gap between conductors or from a conductor to the ground. It is characterized by a sudden release of intense heat, light, and pressure, which can cause severe burns, hearing damage, and other injuries to nearby workers. The temperature of an arc flash can reach up to 35,000 degrees Fahrenheit (19,426 degrees Celsius), which is four times hotter than the surface of the sun.
The Physics Behind Arc Flash
To understand arc flash, it is essential to grasp the basic principles of electricity. Electricity flows through conductors, such as wires or metal parts, and follows the path of least resistance. When there is a sudden drop in resistance or an increase in voltage, an arc flash can occur. The arc flash ionizes the air, creating a plasma that conducts electricity, allowing the current to flow through the air gap.
The Consequences of Arc Flash
The consequences of arc flash can be devastating. Workers exposed to an arc flash can suffer from severe burns, hearing damage, eye injuries, and even death. The intense heat generated by an arc flash can ignite clothing and cause fires, leading to further damage and injuries. Additionally, the pressure wave created by an arc flash can throw workers across the room, causing blunt force trauma and impact injuries.
Causes of Arc Flash
Several factors can contribute to the occurrence of an arc flash. Understanding these causes is essential for implementing effective preventive measures and minimizing the risk of arc flash incidents.
Inadequate Maintenance and Testing
One of the primary causes of arc flash is inadequate maintenance and testing of electrical equipment. Over time, electrical components can deteriorate, leading to increased resistance and potential failure points. Regular maintenance, such as cleaning, tightening connections, and replacing worn parts, can help prevent arc flash incidents.
Improper Work Practices
Improper work practices, such as working on energized equipment without proper safety precautions or using incorrect tools, can increase the risk of arc flash. Workers must follow established safety procedures, use appropriate personal protective equipment (PPE), and employ proper lockout/tagout (LOTO) practices to minimize the risk of arc flash.
Equipment Failure
Equipment failure due to manufacturing defects, age, or environmental factors can also lead to arc flash incidents. Faulty insulation, loose connections, or damaged components can create the conditions necessary for an arc flash to occur.
Transient Voltage Surges
Transient voltage surges, such as those caused by lightning strikes or switching operations, can create high-voltage spikes that exceed the rated capacity of electrical equipment. These surges can cause insulation breakdown and lead to arc flash incidents.
Preventive Measures for Arc Flash
Implementing effective preventive measures is crucial for minimizing the risk of arc flash incidents and protecting workers from potential injuries. The following table summarizes some key preventive measures:
Preventive Measure | Description |
---|---|
Electrical Safety Training | Providing comprehensive electrical safety training to workers, including arc flash awareness and proper work practices. |
Personal Protective Equipment (PPE) | Using appropriate PPE, such as arc-rated clothing, face shields, and insulated gloves, to protect workers from the heat and pressure of an arc flash. |
Lockout/Tagout (LOTO) Procedures | Implementing and enforcing strict LOTO procedures to ensure that equipment is de-energized before maintenance or repair work is performed. |
Arc Flash Hazard Analysis | Conducting arc flash hazard analysis to identify potential hazards, determine the incident energy levels, and establish appropriate safety measures. |
Electrical Equipment Maintenance | Performing regular maintenance and testing of electrical equipment to ensure proper functioning and minimize the risk of failures that could lead to arc flash incidents. |
Electrical System Design | Designing electrical systems with arc flash safety in mind, incorporating features such as current-limiting devices, shorter cable runs, and isolated power systems. |
Electrical Safety Training
Providing comprehensive electrical safety training to workers is essential for preventing arc flash incidents. Training should cover topics such as:
- Fundamentals of electricity and electrical hazards
- Arc flash awareness and understanding the risks
- Proper use of personal protective equipment (PPE)
- Lockout/tagout (LOTO) procedures
- Electrical safety standards and regulations
Regular refresher training should be conducted to ensure that workers remain up-to-date with the latest safety practices and procedures.
Personal Protective Equipment (PPE)
Using appropriate personal protective equipment (PPE) is crucial for protecting workers from the heat and pressure of an arc flash. PPE for arc flash protection includes:
- Arc-rated clothing, such as flame-resistant (FR) shirts, pants, and coveralls
- Arc-rated face shields and helmets
- Insulated gloves and leather protectors
- Safety glasses or goggles
- Hearing protection, such as earplugs or earmuffs
PPE must be selected based on the incident energy levels determined through arc flash hazard analysis and should be inspected regularly to ensure its effectiveness.
Lockout/Tagout (LOTO) Procedures
Implementing and enforcing strict lockout/tagout (LOTO) procedures is essential for preventing arc flash incidents during maintenance or repair work. LOTO procedures ensure that electrical equipment is de-energized and cannot be inadvertently re-energized while work is being performed. Key elements of LOTO procedures include:
- Identifying and isolating energy sources
- Applying lockout devices and tags to energy isolation points
- Verifying that equipment is de-energized through testing
- Releasing stored energy and grounding equipment
- Communicating LOTO status to all affected workers
Arc Flash Hazard Analysis
Conducting arc flash hazard analysis is a critical step in identifying potential hazards and establishing appropriate safety measures. Arc flash hazard analysis involves:
- Collecting data on the electrical system, including equipment ratings, impedances, and protective device settings
- Calculating the available fault current and clearing times at various locations in the system
- Determining the incident energy levels and flash protection boundary distances
- Labeling equipment with arc flash warning labels and PPE requirements
Arc flash hazard analysis should be performed by qualified electrical professionals and updated periodically to account for changes in the electrical system.
Electrical Equipment Maintenance
Regular maintenance and testing of electrical equipment are essential for preventing arc flash incidents. Maintenance activities should include:
- Cleaning and inspecting equipment for signs of wear, damage, or corrosion
- Tightening loose connections and replacing worn or damaged components
- Testing protective devices, such as circuit breakers and relays, to ensure proper operation
- Conducting insulation resistance testing and thermographic inspections to identify potential failure points
Maintenance should be performed by qualified electrical personnel following established safety procedures and using appropriate PPE.
Electrical System Design
Designing electrical systems with arc flash safety in mind can help minimize the risk of arc flash incidents. Design considerations for arc flash safety include:
- Selecting equipment with higher withstand ratings and faster clearing times
- Using current-limiting devices, such as current-limiting fuses or reactors, to reduce the available fault current
- Minimizing cable lengths and using cables with higher insulation ratings
- Providing adequate working space and clearances around electrical equipment
- Incorporating remote operation and monitoring capabilities to minimize the need for workers to be in close proximity to energized equipment
Electrical system design should be performed by qualified electrical engineers who are knowledgeable about arc flash safety standards and best practices.
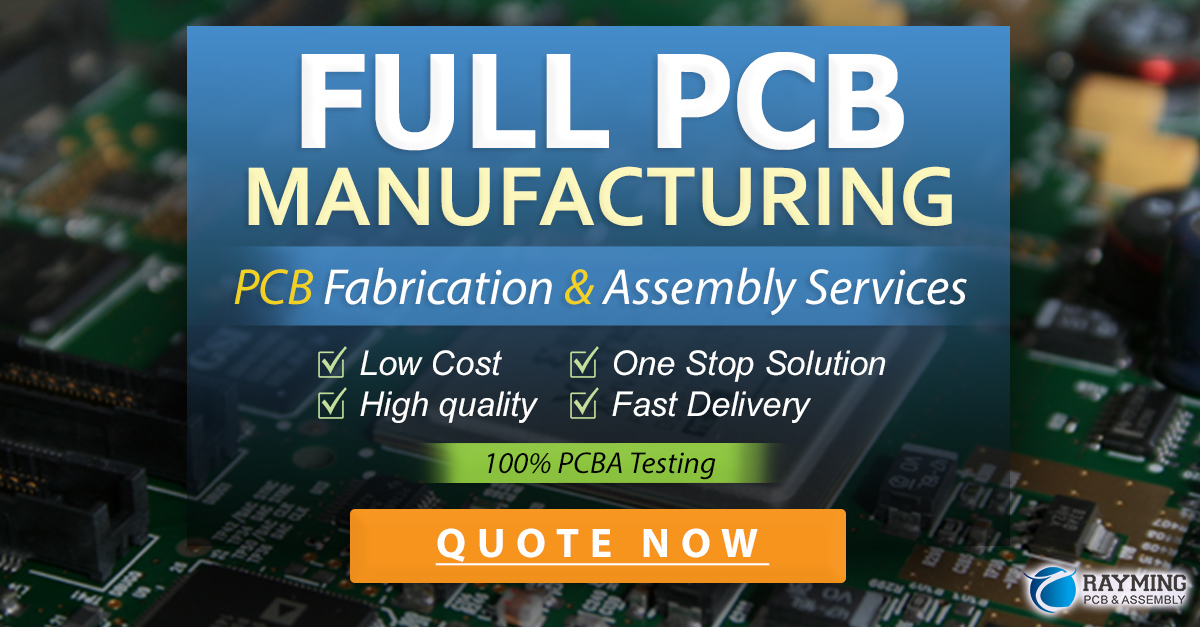
Frequently Asked Questions (FAQ)
- What is the difference between arc flash and electric shock?
-
Arc flash is an explosive electrical event that occurs when a high-voltage current jumps across an air gap, resulting in intense heat, light, and pressure. Electric shock, on the other hand, occurs when a person comes into contact with an energized electrical conductor, allowing current to flow through their body.
-
Can arc flash occur in low-voltage systems?
-
Yes, arc flash can occur in low-voltage systems, although the incident energy levels and potential for injury may be lower compared to high-voltage systems. It is essential to follow proper safety procedures and use appropriate PPE even when working on low-voltage equipment.
-
How often should arc flash hazard analysis be performed?
-
Arc flash hazard analysis should be performed initially and updated periodically, typically every 5 years or whenever significant changes are made to the electrical system. Additionally, analysis should be reviewed and updated if there are changes in the electrical equipment, protective device settings, or system configuration.
-
What is the role of protective devices in preventing arc flash incidents?
-
Protective devices, such as circuit breakers, fuses, and relays, play a critical role in preventing arc flash incidents by quickly detecting and interrupting fault currents. Proper selection, coordination, and maintenance of protective devices can help minimize the duration and energy of an arc flash event.
-
Can arc flash incidents be completely eliminated?
- While it is not possible to completely eliminate the risk of arc flash incidents, implementing comprehensive safety measures, including electrical safety training, proper PPE, LOTO procedures, arc flash hazard analysis, regular maintenance, and appropriate electrical system design, can significantly reduce the likelihood and severity of arc flash events.
Conclusion
Arc flash is a serious electrical hazard that poses significant risks to workers and equipment in industrial settings. Understanding the definition, causes, and preventive measures associated with arc flash is crucial for maintaining a safe working environment and protecting personnel from potential injuries. By implementing comprehensive safety measures, such as electrical safety training, proper PPE, LOTO procedures, arc flash hazard analysis, regular maintenance, and appropriate electrical system design, organizations can significantly reduce the risk of arc flash incidents and ensure the well-being of their workers.
Leave a Reply