Understanding PCB Opens
A PCB open occurs when there is an unintended break in the conductive pathway, preventing electrical current from flowing as intended. This can happen in various parts of the PCB, such as:
- Traces: The thin copper lines that connect components on the PCB
- Vias: The small holes that allow electrical connections between different layers of the PCB
- Pads: The exposed metal surfaces where components are soldered
- Solder joints: The points where components are attached to the PCB using solder
Opens can be complete or partial. A complete open results in a total lack of electrical continuity, while a partial open may allow some current to flow but with increased resistance, leading to intermittent issues or reduced performance.
Causes of PCB Opens
There are several reasons why opens might occur on a PCB:
- Manufacturing defects
- Incomplete etching of copper traces
- Damaged or missing vias
- Improper solder mask application
- Mechanical damage
- PCB flexing or bending
- Impact or vibration
- Improper handling during assembly or use
- Thermal stress
- Repeated heating and cooling cycles
- Coefficient of Thermal Expansion (CTE) mismatch between materials
- Chemical contamination
- Exposure to corrosive substances
- Improper cleaning or storage
- Electrical overstress (EOS)
- Voltage spikes or surges
- Electrostatic discharge (ESD)
- Age and wear
- Oxidation of copper traces
- Solder joint fatigue
Detecting PCB Opens
Identifying opens on a PCB can be challenging, especially if the board is densely populated or has multiple layers. Several methods can be used to detect opens:
Visual Inspection
A thorough visual inspection of the PCB can reveal some opens, particularly those caused by mechanical damage or manufacturing defects. Using magnification tools like microscopes or high-resolution cameras can help identify breaks in traces, damaged vias, or incomplete solder joints.
Continuity Testing
Continuity testing involves using a multimeter or ohmmeter to check for electrical continuity between two points on the PCB. By placing probes at the endpoints of a suspected open, you can determine if there is a break in the circuit. However, this method can be time-consuming for larger PCBs and may not detect partial opens.
Automated Optical Inspection (AOI)
AOI systems use high-resolution cameras and advanced image processing algorithms to inspect PCBs for defects, including opens. These systems can quickly scan the entire board and compare it to a reference design, highlighting any discrepancies. AOI is particularly useful for detecting manufacturing defects and can be integrated into the production process for real-time quality control.
X-Ray Inspection
For PCBs with multiple layers or hidden connections, X-ray inspection can be used to detect opens. X-ray systems create images of the internal structure of the PCB, allowing technicians to see breaks or voids in vias, traces, or solder joints that would otherwise be obscured by the board’s outer layers.
In-Circuit Testing (ICT)
ICT involves using a specialized test fixture to make electrical contact with specific points on the PCB, allowing for detailed testing of individual components and connections. ICT can detect opens by measuring the resistance between test points and comparing it to expected values. This method is highly accurate but requires the development of a custom test fixture for each PCB design.
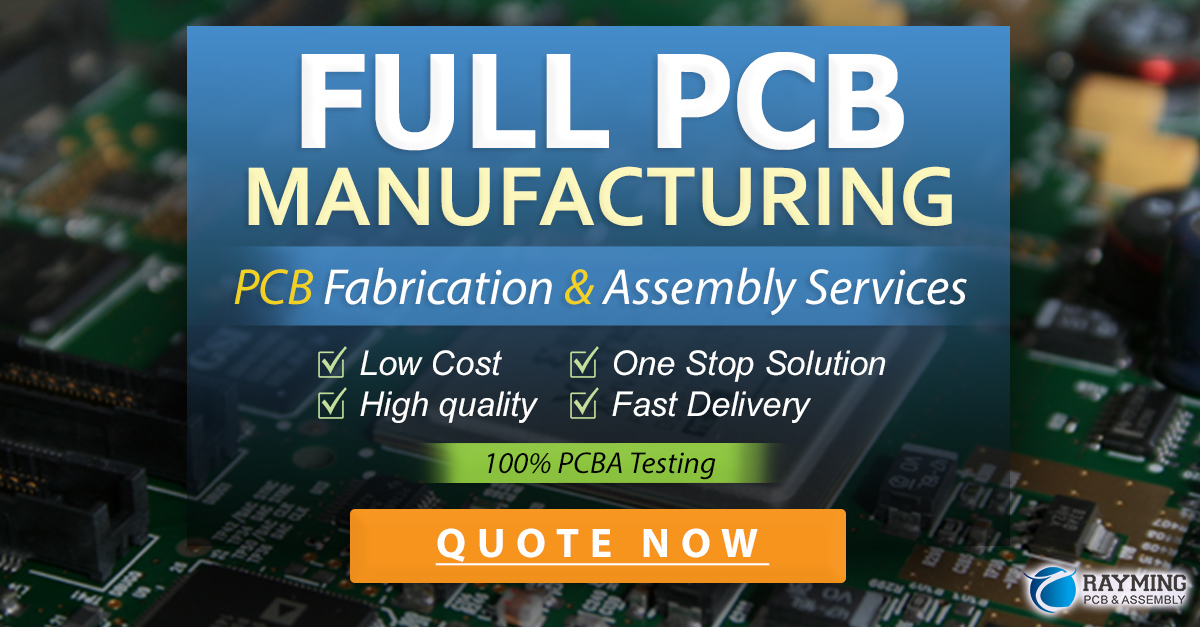
Preventing PCB Opens
Preventing opens on PCBs requires a combination of good design practices, careful manufacturing, and proper handling. Some key strategies include:
- Design for manufacturability (DFM)
- Use appropriate trace widths and spacing
- Avoid sharp angles or narrow necks in traces
- Provide adequate clearance around vias and pads
- Material selection
- Choose PCB materials with good mechanical and thermal properties
- Consider the CTE of different materials to minimize stress
- Controlled impedance design
- Use controlled impedance traces for high-speed signals
- Ensure proper termination and matching to reduce reflections
- Solder mask design
- Apply solder mask to protect traces and prevent short circuits
- Ensure proper solder mask clearance around pads and vias
- Manufacturing process control
- Implement strict quality control measures
- Monitor etching, drilling, and plating processes
- Use automated inspection systems to catch defects early
- Handling and storage
- Train personnel on proper PCB handling techniques
- Use ESD-safe packaging and storage materials
- Avoid exposing PCBs to extreme temperatures or humidity
Troubleshooting PCB Opens
When an open is detected on a PCB, the first step is to determine its location and cause. This can be done using the detection methods described earlier, such as visual inspection, continuity testing, or X-ray imaging.
Once the location of the open is known, the next step is to assess the severity of the issue. In some cases, a partial open may not significantly impact the performance of the device and may be left as-is. However, if the open is causing malfunctions or reducing reliability, it will need to be repaired.
PCB repair techniques for opens include:
- Jumper wires: Soldering a small wire across the open to restore continuity
- Conductive epoxy: Applying a conductive adhesive to bridge the gap
- Trace repair: Carefully scraping away the solder mask and applying new copper to rebuild the trace
- Via replacement: Drilling out the damaged via and installing a new one
The choice of repair method will depend on the location and extent of the damage, as well as the skills and tools available to the technician.
In some cases, opens may be too severe or numerous to repair cost-effectively. In these situations, it may be necessary to scrap the PCB and manufacture a new one, taking care to address any underlying design or process issues that led to the opens in the first place.
PCB Open Case Studies
To better understand the impact of opens on real-world PCBs, let’s look at a few case studies:
Case Study 1: Automotive Instrument Cluster
An automotive manufacturer was experiencing intermittent failures in their instrument cluster PCBs. The issue was traced to partial opens in the traces connecting the microcontroller to the display drivers. The opens were caused by a combination of vibration and thermal stress, which caused the traces to crack over time.
To address the issue, the manufacturer made several changes:
– The PCB layout was revised to use wider traces and more vias in high-stress areas
– A conformal coating was applied to the PCB to reduce vibration and provide additional mechanical support
– The mounting system was redesigned to better isolate the PCB from engine vibrations
After implementing these changes, the failure rate of the instrument cluster PCBs dropped significantly, improving overall vehicle reliability.
Case Study 2: Medical Device PCB
A medical device company was experiencing early failures in a critical PCB used in their patient monitoring system. Investigation revealed that the failures were due to opens in the solder joints of a Ball Grid Array (BGA) component.
Further analysis showed that the opens were caused by a combination of factors:
– The BGA component had a different CTE than the PCB material, leading to stress on the solder joints
– The solder paste used in the manufacturing process had poor wetting properties, resulting in weak joints
– The reflow profile was not optimized for the specific component and PCB combination
To solve the problem, the company made several changes:
– The PCB material was changed to one with a CTE closer to that of the BGA component
– A different solder paste with better wetting properties was selected
– The reflow profile was optimized through a Design of Experiments (DoE) approach
After making these changes, the solder joint reliability improved dramatically, and the medical device PCBs met their expected lifetime in the field.
FAQ
What is the difference between an open and a short circuit on a PCB?
An open refers to a lack of electrical continuity where there should be a connection, while a short circuit occurs when there is an unintended connection between two or more points that should not be connected. Opens result in a complete or partial lack of current flow, while short circuits can cause excessive current flow and potentially damage components.
Can PCB opens be detected by automated optical inspection (AOI)?
Yes, AOI systems can detect many types of PCB opens, particularly those caused by manufacturing defects such as incomplete etching or missing vias. However, AOI may not be able to detect all types of opens, especially those that are hidden under components or in internal layers of the PCB.
How can thermal stress cause PCB opens?
Thermal stress can cause PCB opens due to the different coefficients of thermal expansion (CTE) of the materials used in the board. As the PCB heats up and cools down, the materials expand and contract at different rates, which can cause mechanical stress on traces, vias, and solder joints. Over time, this stress can lead to cracks or breaks, resulting in opens.
What is the best way to repair a PCB open?
The best way to repair a PCB open depends on the location and extent of the damage. Small opens in traces can often be repaired using jumper wires or conductive epoxy, while more extensive damage may require trace repair or via replacement. In some cases, the best solution may be to scrap the damaged PCB and manufacture a new one, addressing any underlying design or process issues to prevent future opens.
Can PCB opens be prevented through design changes alone?
While good PCB design practices can help reduce the likelihood of opens, they cannot completely eliminate the risk. Manufacturing process control, proper handling, and environmental factors also play a role in preventing opens. A comprehensive approach that addresses design, manufacturing, and handling is the most effective way to minimize the occurrence of PCB opens.
Conclusion
PCB opens are a common issue that can cause significant problems in electronic devices, from minor malfunctions to complete failure. By understanding the causes, detection methods, and prevention strategies for opens, PCB designers and manufacturers can work together to create more reliable and robust circuit boards.
Regular inspection, testing, and process control are essential for catching opens early and minimizing their impact on production and end-use. When opens do occur, careful troubleshooting and repair techniques can often restore functionality, but in some cases, scrapping the affected PCB may be the most cost-effective solution.
As electronic devices continue to become more complex and mission-critical, the importance of preventing and managing PCB opens will only continue to grow. By staying up-to-date with the latest best practices and technologies, the electronics industry can ensure that PCBs remain a reliable foundation for innovation and progress.
Leave a Reply