Introduction to Peelable Soldermask
A peelable soldermask, also known as a temporary soldermask or removable soldermask, is a protective coating applied to printed circuit boards (PCBs) during the manufacturing process. This special type of soldermask is designed to be easily removed from specific areas of the PCB when needed, allowing for selective soldering or component placement. Peelable soldermasks offer several advantages over traditional permanent soldermasks, making them an essential tool in modern PCB fabrication.
Key Features of Peelable Soldermasks
-
Removability: The primary feature of a peelable soldermask is its ability to be easily peeled off from the PCB surface without leaving residue or damaging the underlying circuitry.
-
Precision: Peelable soldermasks can be applied to specific areas of the PCB with high precision, allowing for accurate control over the soldermask coverage.
-
Compatibility: These soldermasks are compatible with various PCB materials, including FR-4, polyimide, and flexible substrates.
-
Temperature resistance: Peelable soldermasks can withstand the high temperatures encountered during the soldering process, providing reliable protection to the covered areas.
Benefits of Using Peelable Soldermasks
Selective Soldering
One of the primary benefits of using a peelable soldermask is the ability to perform selective soldering. In some cases, certain components or areas of the PCB may require soldering while others need to be protected. By applying a peelable soldermask to the areas that need protection, manufacturers can easily solder the desired components without affecting the rest of the board.
Rework and Repair
Peelable soldermasks also facilitate the rework and repair process for PCBs. If a component needs to be replaced or a connection needs to be fixed, the peelable soldermask can be removed from the specific area, allowing technicians to access the underlying circuitry. After the repair is complete, a new layer of peelable soldermask can be applied to protect the area once again.
Prototype Development
In prototype development, peelable soldermasks offer flexibility and ease of use. Engineers can quickly apply and remove soldermasks as needed during the iterative design process, making it easier to test different configurations and make necessary changes.
Types of Peelable Soldermasks
Liquid Peelable Soldermasks
Liquid peelable soldermasks are applied to the PCB surface in a liquid form using various methods such as screen printing, spraying, or dipping. These soldermasks cure through exposure to ultraviolet (UV) light or heat, forming a solid protective layer. Liquid peelable soldermasks offer excellent coverage and can be easily removed by peeling when needed.
Film Peelable Soldermasks
Film peelable soldermasks, also known as dry film soldermasks, are supplied in the form of a solid film. The film is laminated onto the PCB surface using heat and pressure, conforming to the contours of the board. Film peelable soldermasks provide a uniform thickness and can be easily peeled off when required.
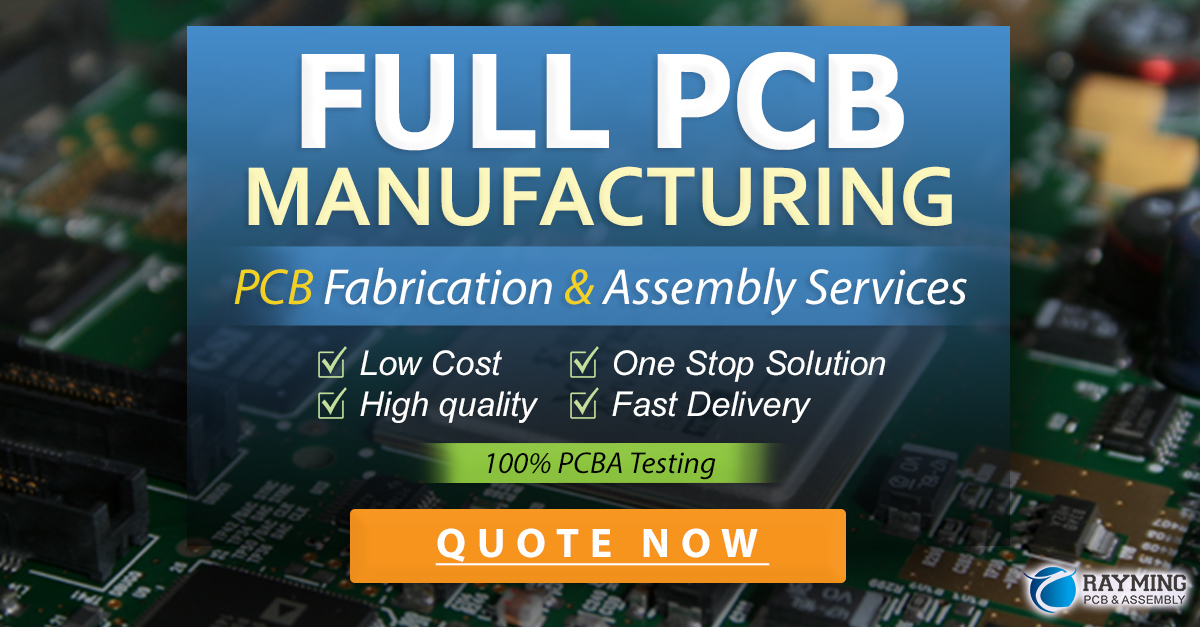
Application Process for Peelable Soldermasks
The application process for peelable soldermasks varies depending on the type of soldermask being used. However, the general steps involved are as follows:
-
Surface Preparation: The PCB surface is cleaned and prepared to ensure proper adhesion of the soldermask.
-
Soldermask Application: The peelable soldermask is applied to the PCB surface using the appropriate method (screen printing, lamination, etc.).
-
Curing: The soldermask is cured using UV light or heat, depending on the specific product requirements.
-
Inspection: The PCB is inspected to ensure proper coverage and adhesion of the peelable soldermask.
Step | Liquid Soldermask | Film Soldermask |
---|---|---|
1 | Surface Cleaning | Surface Cleaning |
2 | Screen Printing | Lamination |
3 | UV Curing | Heat Curing |
4 | Inspection | Inspection |
Factors to Consider When Choosing a Peelable Soldermask
When selecting a peelable soldermask for your PCB manufacturing process, consider the following factors:
- Compatibility with PCB materials and components
- Ease of application and removal
- Temperature resistance during soldering
- Adhesion strength to the PCB surface
- Durability and shelf life of the soldermask
Frequently Asked Questions (FAQ)
1. Can peelable soldermasks be reapplied after removal?
In most cases, yes. After removing the peelable soldermask, a new layer can be applied to the PCB surface to provide continued protection.
2. How long do peelable soldermasks last?
The lifespan of a peelable soldermask depends on various factors, such as storage conditions and the specific product used. Typically, peelable soldermasks can last for several months to a year when stored properly.
3. Are peelable soldermasks suitable for high-volume production?
Yes, peelable soldermasks can be used in high-volume PCB production. Many peelable soldermask products are designed for efficient application and removal, making them suitable for large-scale manufacturing.
4. Can peelable soldermasks be used on flexible PCBs?
Yes, there are peelable soldermask products specifically formulated for use on flexible PCBs. These soldermasks are designed to withstand the bending and flexing of the circuit board without cracking or peeling.
5. Are peelable soldermasks more expensive than permanent soldermasks?
In general, peelable soldermasks may be slightly more expensive than permanent soldermasks due to their specialized properties. However, the added benefits of selective soldering, easy rework, and prototype development often justify the additional cost.
Conclusion
Peelable soldermasks are a valuable tool in PCB manufacturing, offering flexibility, precision, and protection during the soldering process. By understanding the types of peelable soldermasks available, their application process, and the factors to consider when choosing one, PCB manufacturers can optimize their production workflow and create high-quality circuit boards. As technology continues to advance, the use of peelable soldermasks is likely to grow, enabling more efficient and adaptable PCB fabrication processes.
Leave a Reply