Introduction
A printed circuit board (PCB) is a thin board made of fiberglass or other insulating materials that houses the components and interconnects of an electronic circuit. PCBs provide the mechanical structure to mount and electronically connect electronic components using conductive pathways or traces etched from copper sheets laminated onto a non-conductive substrate. PCBs are the core of all modern electronic devices ranging from simple electronics like calculators and remote controls to complex computer systems and supercomputers. This article provides a comprehensive overview of PCBs, their design, materials, manufacturing process, and applications across various industries.
What is a PCB made of?
A PCB consists of different materials laminated together to form a flat board. The core materials in a PCB include:
Substrate
The substrate forms the base of the PCB providing mechanical support. The most common materials used are:
- Fiberglass – Provides excellent mechanical strength and is a good electrical insulator. The fiberglass cloth is impregnated with epoxy resin to form a rigid and durable substrate.
- FR-4 – A flame retardant grade of fiberglass widely used in consumer electronics. The ‘FR’ indicates flame resistance.
- CEM-1 – A cotton paper based substrate with good mechanical strength.
- Polyimide – Used in flexible PCBs owing to its flexible nature.
- Ceramic – Used in specialized high frequency and high temperature applications.
Conductive layers
The conductive layers are made up of thin copper foils (35μm – 70μm thickness) laminated onto the substrate. The copper layers are etched to form traces or interconnects between components. Common variants include:
- Single sided – Copper on one side of substrate
- Double sided – Copper on both sides
- Multilayer – Multiple copper layers stacked with insulating dielectric films separating them
Solder mask
The solder mask is a coat of polymer or epoxy that is applied over the copper traces for insulation and preventing solder bridges. It provides mechanical protection to the traces and exposes only the soldering pads.
Silkscreen
The silkscreen is the white lettering printed on the board identifying components, connections and board outline. It helps in assembling and testing PCBs.
Plated finishes
Special coatings applied over exposed copper pads and traces to facilitate soldering and prevent oxidation. Common platings used are:
- Hasl – Hot air solder leveling using lead-tin alloy provides good solderability
- Immersion Tin – Provides excellent solderability and shelf life
- Immersion Silver – Used for high frequency and optimal conductivity
- ENIG – Electroless Nickel Immersion Gold provides excellent conductivity and shelf life
Vias
Vias are plated through holes that provide connections between different layers in multilayer PCBs. They are made by drilling holes and plating their walls with copper.
PCB Design and Layout
PCB design involves schematic capture, component footprint creation, routing traces and outputting Gerber files for manufacturing. Key aspects in PCB layout are:
- Component placement – Parts with the most connections are placed first with high priority signals getting shortest routes. Similar signals are grouped into buses.
- Routing – Traces are routed between pads based on the connections in the schematic using autorouters or manual routing. Constraints like length matching, impedance control and crosstalk are considered.
- Planes – Power, ground and signal planes are incorporated as needed for shielding and controlled impedance.
- Stackup – Layer stack with dielectric materials is designed with impedance, thickness and copper weights suited for signals.
- Footprints – Accurate footprints are created for all components to be assembled to the PCB.
- Finishes – Appropriate platings and coatings are specified.
- Fabrication data – Gerber and drill files are generated with annotations for PCB production.
PCB Manufacturing Process
PCB fabrication involves multiple stages to build up the board layer by layer.
1. Substrate preparation
The base substrate is cleaned and preconditioned. Substrates like FR4 are laminated with layers of glass reinforced epoxy.
2. Conductive layer deposition
Copper foils are laminated to the substrate using high pressure and temperature. The thickness of the copper foil is specified based on current density requirements.
3. Imaging
The PCB artwork from Gerber files is printed on the panels using a photoresistive material. Ultraviolet light is used to transfer the image through masks.
4. Etching
The unexposed photoresist is developed away chemically exposing the undesired copper which is etched away by chemicals leaving only the intended copper traces.
5. Stripping and etching
The remaining photoresist is stripped off and the panels are descummed to remove any residual copper particles.
6. Hole drilling
Holes are drilled at specified locations to create vias for through hole components. The holes are deburred to clean edges.
7. Plating and coating
Exposed copper surfaces are plated with solder or other metal finishes. Solder mask and silkscreen coatings are applied as per specification.
8. Panelization
Multiple PCBs are arranged in a panel for mass production. Test coupons are added for quality checks.
9. Rout and depanel
Completed panels are routed to separate individual PCBs which are tested and depaneled.
10. Assembly
Components are assembled on the finished boards manually or using SMT assembly lines. The populated boards are then tested.
Types of PCBs
PCBs can be classified based on the conductive layers, substrate material or assembly style as follows:
Based on conductive layers
- Single sided – Conductors on one side
- Double sided – Conductors on both sides
- Multilayer – Multiple conductive layers stacked with insulation
Based on substrate material
- Rigid PCBs – Use rigid insulating substrates like FR4
- Flexible PCBs – Use flexible substrate like polyimide
- Rigid-flex PCBs – Have both rigid and flexible sections
Based on assembly
- Through-hole technology – Uses leaded components with leads passed through holes
- Surface-mount technology – Uses smaller flat surfaced mount components
- Mixed technology – Has both through-hole and SMT components
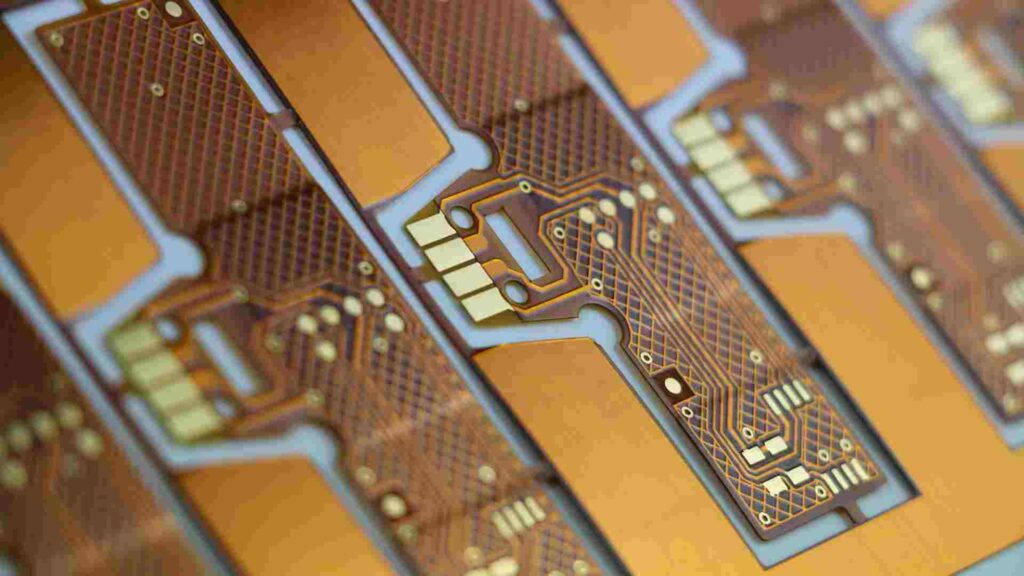
PCB Design Software
PCB design involves electronic schematic creation, footprint generation, board layout, routing and design rule checks. Popular EDA tools for PCB design are:
- Altium Designer – High performance tool with complete ecosystem
- Eagle – Freemium tool from Autodesk with good library
- KiCAD – Advanced opensource tool with 3D viewer
- OrCAD – Full featured tool from Cadence with advanced features
- Proteus – Easy to use tool good for beginners
- DipTrace – Affordable tool with good routing features
- EasyEDA – Online tool with real time collaboration
Key features
- Schematic editor – Capture circuits with library of symbols
- PCB editor – Design board outline and placements
- Autorouter – Auto route connections as per rules
- DRC – Design rule check validates manufacturability
- 3D viewer – Visualize PCB with real-time rendering
- Import/Export – Interface with other tools using industry standard formats
Applications of PCBs
PCBs form the core of electrical and electronic circuits and are ubiquitous across all industries. Some major applications include:
Consumer Electronics
All electronic appliances and gadgets including computers, mobile devices, home appliances, gaming consoles, wearables and more depend on intricately designed PCBs. Miniaturization of devices demands highly dense component mounting and routing.
Automotive
Modern cars have multiple onboard computers and elaborate electronics for various subsystems including engine control unit (ECU), infotainment, advanced driver assist systems (ADAS), battery management systems etc. This requires rugged boards that perform reliably in harsh environments.
Telecommunications
Cellphones, routers, switches, base stations and other communication systems use RF PCBs designed for high frequency signals and impedance control. Multi-layer boards with precise trace dimensions and spacing are employed.
Medical Equipment
Medical electronic devices like patient monitors, imaging systems and analyzers require highly reliable PCBs. Stringent regulatory requirements demand rigorous testing and compliance.
Industrial Electronics
Industrial automation systems, process control equipment, robotics and other mechatronic systems are complex electronic systems. The PCBs need to withstand vibration, humidity and temperature variations in industrial environments.
Military and Aerospace
Defense and aviation applications require extremely robust boards given the mission critical nature and harsh operating conditions. Rigid quality controls and testing procedures are enforced on militarized PCBs.
Internet of Things
Compact IoT nodes and sensors deployed in diverse locations need small form factor PCBs. Use of flexible circuits provide flexibility in Size, Shape and Configuration (SSC).
Advantages of Using PCBs
Some benefits of using PCBs over other forms of electronic circuit construction are:
- Compact size – More components can be housed in a small area by surface mounting devices.
- Reproducibility – Printed traces enable producing identical boards quickly.
- Reliability – Epoxy glass PCBs are rugged and withstand vibration, moisture and temperature changes.
- Ease of assembly – Automated SMT assembly allows rapid mounting of even tiny components.
- Heat dissipation – PCB substrate acts as a medium to conduct heat from components. Ground planes aid cooling.
- Reduced wiring – Short traces replace individual point to point component wiring.
- Scalability – Complex multi-layer PCBs enable highly complex circuit designs.
- Testability – Test points and controlled impedance traces aid circuit testing and debugging.
- Cost – Modern PCBs are relatively inexpensive to manufacture in high volumes.
- Environmental friendly – PCBs designed to be RoHS (restriction of hazardous substances) compliant are eco-friendly.
Thus, PCBs offer an optimal solution for assembling and interconnect electronic circuits with unmatched reliability, scalability and cost efficiency.
Future Trends in PCB Technology
Advancements in materials, fabrication techniques and design tools are driving new innovations in PCB technology:
- Miniaturization – Shrinking component sizes and finer trace geometries allow greater component density and integration. Microvia layers enable further miniaturization.
- High Density Interconnects – High density interconnect (HDI) techniques like blind and buried vias are enabling greater routing densities. Sequential lamination allows packing more routing layers.
- Embedded passives – Passive components are directly integrated into the PCB layers saving space and reducing parasitics.
- Flex and rigid-flex – Flexible circuits find increased applications in wearable and folding devices with flexible displays. Multilayer rigid-flex boards provide reliability with flex.
- Additive manufacturing – Additive fabrication using inkjet printing of conductive inks enables on-demand and low volume PCB prototyping and production.
- Advanced materials – New substrate materials like LCP (liquid crystal polymer) allow high frequency and flexible PCBs. Reliability is improved by halogen free and high Tg resin systems.
- Thermal management – Direct embedding of heat pipes, vias and films enables improved thermal performance critical for high power devices.
- Multi-die packaging – 2.5D and 3D integration involves mounting multiple ICs on a silicon interposer providing a high density interface to the PCB through high density bump arrays.
- Higher frequencies – Materials with low dielectric loss allow enhanced signal integrity for high speed digital and RF applications beyond 100 GHz.
- Design automation – AI-driven analysis and optimization of stackups, power/signal integrity, EMI/EMC at early design stages. Automated routing and tuning using evolutionary algorithms.
- Testing – Testing enhancements through built-in self test, boundary scan, automated optical and x-ray inspection enabled by machine learning.
With the relentless innovation in the field, PCB technology will continue to enable cutting edge electronic products and push the boundaries of digital transformation.
Summary
In summary, a PCB forms the core foundation of all electronic systems providing the mechanical structure to mount components and electrical interconnects between them. A multi-layer PCB is made of conductive copper laminated over an insulating substrate with additional coatings and platings. PCBs are designed with specialized CAD tools and manufactured using photolithographic processes. They find ubiquitous use across all industries given their advantages in reliability, ease of assembly and cost efficiency. Continued advancements in materials, fabrication methods and design automation will enable PCB technology to address the challenges in building next generation electronic devices.
Frequently Asked Questions
Question 1: What are the typical substrate thicknesses used in PCBs?
Answer 1: Common substrate thicknesses used are –
- 0.4mm – Widely used in consumer electronics
- 0.8mm – Standard thickness for double sided boards
- 1.6mm – Used in multilayer boards requiring more layers
- 2.4mm – Used in boards requiring high stiffness
The thickness is chosen based on number of layers, stiffness and weight requirements.
Question 2: What are some common PCB finishes and their purposes?
Answer 2: Common PCB finishes include:
- HASL (Hot air solder leveling) – Provides good solderability and shelf life
- Immersion silver – Gives excellent solderability, conductibility and shelf life
- ENIG (Electroless Nickel Immersion Gold) – Improves wear resistance and shelf life
- Immersion tin – Used as lead-free finish with good solderability
- OSP (Organic solderability preservatives) – Low cost finish to protect copper from oxidation
Question 3: What are some key challenges in high speed PCB design?
Answer 3: Key high speed design challenges include:
- Signal integrity – Controlled impedance routing, terminating lines, noise control
- Power integrity – Managing power distribution losses and transients
- EMI control – Minimizing electromagnetic interference through grounding, shielding and filtering
- Thermal issues – Effectively dissipating heat from high power components
- Skew control – Matching trace lengths for synchronous signals
- Complexity – High density routing, smaller spacings and material constraints
Question 4: What are common test procedures conducted on bare PCBs?
Answer 4: Typical tests conducted on bare PCBs are –
- Net connectivity – Validating shorts/opens using in-circuit test
- impedance – Measuring matched line impedance
- High voltage – Dielectric withstand voltage tests
- Insulation resistance – Measuring IR between conductors
- Continuity – Checking continuity of circuits
- RoHS compliance – Testing for restricted hazardous substances
Question 5: What are some key benefits of using SMT components instead of through-hole?
Answer 5: Benefits of SMT components include:
- Smaller size – Higher component density with reduced size
- Faster assembly – Automated SMT assembly is faster
- Reduced labor – Less manual intervention
- Improved performance – Better electrical characteristics
- Double-sided mounting – Components can be placed on both sides
- No hole drilling – Saves two steps of drilling and plating
- Mixed technology – Can combine with through hole components
Leave a Reply