Introduction to Backplanes
A backplane is a printed circuit board (PCB) that connects several connectors in parallel to each other, so that each pin of each connector is linked to the same relative pin of all the other connectors, forming a computer bus. It is used as a backbone to connect several printed circuit boards together to make up a complete computer system. Backplanes are commonly used in complex electronic systems such as industrial machinery, telecommunications equipment, and server/computing applications.
Key Features of a Backplane
- Provides mechanical support for plugging in other PCBs
- Routes electrical signals between boards
- Distributes power to boards
- Allows for modularity and easy swapping of components
- Enables parallel connections between boards
Types of Backplanes
There are several different types of backplanes, each designed for specific applications and requirements:
Passive Backplanes
A passive backplane is the simplest type, consisting of just the PCB with connectors. It provides the physical interconnections between boards but contains no active electronic components itself. Passive backplanes rely on the boards plugged into them to provide all processing and control functions.
Advantages of Passive Backplanes:
- Low cost
- High reliability due to simplicity
- No power consumption
- Easier to design and troubleshoot
Active Backplanes
Active backplanes contain additional circuitry beyond just connectors, such as buffers, drivers, or logic devices. The active components help manage the data flow between plug-in boards and can provide features like bus arbitration. Active backplanes offer more functionality but also add cost and complexity compared to passive versions.
Advantages of Active Backplanes:
- Improved signal integrity over long distances
- Reduced loading on plug-in boards
- Can provide advanced bus control features
- Allows more plug-in boards to be used
Standard Backplanes
Many systems use backplanes that adhere to established industry standards, such as VMEbus, VPX, CompactPCI, or ATCA. Using a standard helps ensure interoperability between boards from different vendors and provides a defined system architecture to work within.
Standard | Description |
---|---|
VMEbus | Widely used 64-bit parallel computer bus with rugged Eurocard connectors. Originated in 1981. |
VPX | High-speed successor to VMEbus that adds fast serial fabrics. Commonly used in aerospace, defense and industrial applications. |
CompactPCI | Industrial version of the PCI bus with added hot-swap capability. Uses same Eurocard form factor as VMEbus. |
ATCA | Advanced Telecom Computing Architecture – modular platform targeted at carrier-grade communications equipment. |
Custom Backplanes
In some cases, a standard backplane may not meet the unique needs of a particular system. In this case, a custom backplane can be designed with the ideal combination of size, shape, connectors, and features specifically optimized for that application. Custom backplanes offer ultimate flexibility but require additional engineering effort.
Backplane Form Factors
Backplanes come in a variety of shapes and sizes depending on the types of boards and chassis they are designed to work with. Here are some of the common form factors:
Eurocard
Eurocard is a widely used standard that defines the physical dimensions and connector placement of PCBs and backplanes. It specifies 3U (100mm x 160mm) or 6U (233mm x 160mm) board sizes with 2mm metric pin spacing DIN 41612 connectors. Many backplane standards like VME, VPX and CompactPCI use the Eurocard form factor.
Motherboard Backplanes
In a PC or server chassis, the motherboard itself acts as a kind of backplane, providing slots for expansion cards as well as interconnecting the major system components like CPU, memory and I/O. Common motherboard form factors include ATX, microATX and mini-ITX.
Proprietary Form Factors
Some systems use entirely proprietary backplane designs to fit unique size constraints or configurations not covered by standard form factors. Proprietary form factors are commonly found in embedded computing, networking equipment, storage arrays, and other specialized devices.
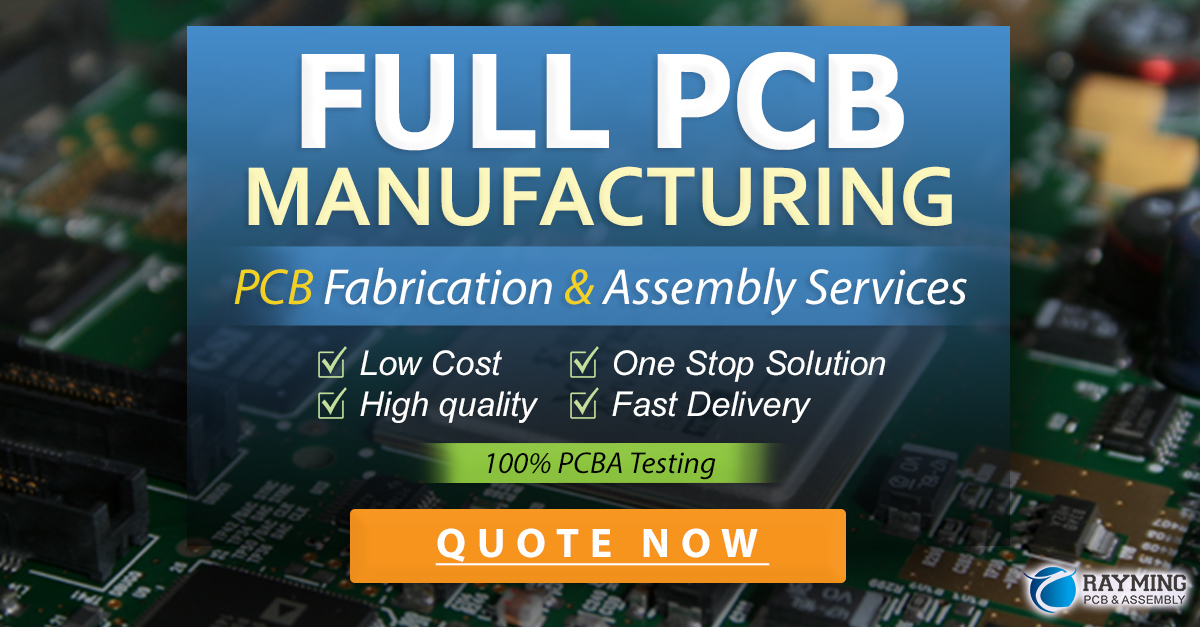
Connectors Used in Backplanes
The connectors used on a backplane are a critical aspect of its design, as they provide the interface between the backplane and its plugin modules. Choosing the right connector requires careful consideration of the electrical and mechanical requirements. Here are some key factors that influence backplane connector selection:
- Number of contacts (pins) required
- Contact spacing (pitch)
- Current carrying capacity per contact
- Maximum signal speed/frequency to be carried
- Engagement/disengagement force
- Durability requirements (mating cycles)
- Keying options to prevent incorrect insertion
- PCB termination method (press-fit, solder, etc.)
Some of the most common backplane connector families include:
DIN 41612
Originally standardized as part of the Eurocard form factor, DIN 41612 connectors feature a pin and socket design with 2mm contact pitch. They are available in 2 or 3 row variations with up to 160 pins per connector. DIN 41612 is commonly used in VMEbus, CompactPCI, and industrial control applications.
MultiGig RT
The MultiGig RT connector, originally developed by Amphenol, is a high-speed, high-density connector capable of supporting data rates up to 40 Gbps+. It uses an innovative “stacker” design that allows multiple wafers to be assembled together to increase pin count. MultiGig RT is commonly used in VPX and other advanced defense/aerospace backplanes.
VITA 66 Optical
For backplanes that need to carry extremely fast signals or cover long distances, fiber optic interfaces may be preferable to copper. The VITA 66 standard defines a family of blind mate optical modules that can be integrated into VPX or other high-speed backplanes to enable data transfer rates into the Terabit range.
Designing a Backplane
The process of designing a backplane can be complex, requiring careful attention to a variety of electrical and mechanical factors. Here are some of the key considerations:
Schematic Design
The first step is to create a schematic diagram showing all of the required interconnections between connectors. This will define the basic connectivity of the backplane. Schematics are typically created using electronic design automation (EDA) software.
Signal Integrity Analysis
For high-speed designs, it is critical to analyze and optimize the signal paths to ensure reliable data transmission. This involves modeling the electrical characteristics of the PCB traces, connectors, and terminations to avoid issues like reflections, crosstalk, and attenuation. Specialized signal integrity tools are used to simulate and verify high-speed designs.
Power Distribution
The backplane must provide power to all plug-in modules, so the power distribution network (PDN) is a key part of the design. The PDN must be designed to maintain stable voltage levels under a variety of load conditions. Careful attention must be paid to minimizing impedance and avoiding resonance effects that could lead to power integrity issues.
PCB Layout
Once the schematic and simulation are complete, the physical PCB layout can be created. This will define the actual copper traces, plane layers, holes, and mechanical features of the finished board. PCB layout requires careful attention to design rules governing trace width/spacing, hole size, component placement and manufacturability.
Mechanical Design
In addition to the PCB itself, the backplane must be designed to fit properly within its intended chassis or enclosure. 3D mechanical CAD tools are used to model the backplane assembly and ensure correct fit with mating components, mounting holes, guiderails, and cooling features. Careful mechanical design is essential to ensure proper airflow and prevent excessive mechanical stress on components.
Manufacturing and Assembly
Once the backplane design is finalized, the board must be actually fabricated and assembled. PCB manufacturing involves a multi-step process of printing, etching, drilling, and plating to create the finished board. For complex designs with high layer counts and fine features, careful choice of manufacturer is critical to ensure quality.
After fabrication, the bare board must be populated with connectors and any other required components like termination resistors, bypass capacitors or ESD protection devices. Connector attachment is a particularly crucial step, as proper soldering and alignment is essential for reliable operation. Press-fit connectors can simplify this process by allowing the connectors to be mechanically inserted prior to soldering.
Assembled backplanes should undergo rigorous inspection and electrical testing to verify that they meet all specifications. Automated optical inspection (AOI) and X-ray systems are commonly used to check for defects, while electrical tests like continuity and isolation testing help ensure proper connectivity and signal integrity. Environmental testing for vibration, shock and temperature cycling may also be required depending on the intended application.
Backplane Applications
Backplanes are used in a wide variety of electronic systems across many industries. Here are a few examples of common backplane applications:
Industrial Automation
Industrial control systems often use modular backplanes to allow flexible configuration of I/O modules, motion controllers, and communication interfaces. The rugged construction and reliable connectors used in industrial backplanes enable them to withstand harsh environments and repeated insertion cycles.
Data Centers
Large cloud data centers make extensive use of blade server chassis containing hot-swappable compute, storage and networking modules. High-speed backplanes are used to interconnect these modules and provide a path to redundant power supplies and cooling fans. Advanced Telecom Computing Architecture (ATCA) is a popular standard for these applications.
Military/Aerospace
Embedded computing systems used in defense and aerospace applications demand the utmost in reliability and performance. OpenVPX is a widely used backplane standard in this sector, offering a modular, scalable architecture for radar, electronic warfare, and autonomous vehicle platforms. Rugged VPX backplanes are designed to withstand extreme shock, vibration and temperature conditions.
Test and Measurement
Sophisticated electronic test equipment often uses modular instrumentation platforms based on backplane architectures. PXI (PCI eXtensions for Instrumentation) is a popular standard that allows users to mix and match instruments from various vendors in a single chassis. High-speed PXI backplanes provide the necessary bandwidth for advanced testing applications like 5G wireless and automotive radar.
Frequently Asked Questions (FAQ)
What is the difference between a backplane and a motherboard?
A backplane is a passive board that provides interconnections between other plug-in modules, while a motherboard is an active board that contains the core components of a system like CPU and memory. A motherboard may act as a simple backplane by providing slots for expansion cards.
How fast of a data rate can a backplane support?
The maximum data rate of a backplane depends on its design and the specific connectors used. Modern standards like VPX and ATCA can support aggregate data rates into the Terabit/s range using a combination of high-speed copper and optical interconnects.
What is the difference between a passive and active backplane?
A passive backplane contains no active components and simply routes signals between connectors. An active backplane includes additional circuitry like buffers or bus switches to improve signal integrity and provide more advanced functionality. Active backplanes are generally more expensive and complex than passive versions.
How do I know what type of backplane I need for my application?
Choosing the right backplane requires careful analysis of your system requirements, including the number and type of modules to be connected, the required data throughput, and any mechanical constraints of the enclosure. Consulting with an experienced backplane designer can help guide the selection process.
Can I mix and match modules from different vendors in the same backplane?
The ability to mix modules depends on the specific backplane standard being used. Backplanes designed around open industry standards like VPX or CompactPCI can accept modules from any vendor that complies with the standard. Proprietary backplanes may restrict you to modules from a single vendor.
Conclusion
Backplanes play a crucial role in many complex electronic systems, providing the interconnections and infrastructure necessary for modular, high-performance computing. By understanding the different types of backplanes, their key characteristics, and design considerations, engineers can make informed decisions when architecting new systems. As demands for bandwidth and processing power continue to grow, backplane technology will continue to evolve to keep pace, enabling new generations of advanced applications in defense, industry, and beyond.
Leave a Reply