Introduction to Flex and Flex-Rigid PCBs
Flexible printed circuit boards (PCBs) and flex-rigid PCBs are versatile interconnect solutions that offer many advantages over traditional rigid PCBs. Flex PCBs consist of a thin insulating polymer film laminated with conductive copper traces. This allows the PCB to bend, fold, and flex, enabling 3D packaging and dynamic flexing applications not possible with rigid boards.
Flex-rigid PCBs combine flexible and rigid PCB technologies by having rigid PCBs connected by integrated flex circuit sections. The rigid areas can mount components while the flex sections act as interconnects between the rigid sections. This allows complex 3D designs in a single circuit assembly.
The unique properties of flex and flex-rigid PCBs open up possibilities for creative and space-saving designs in many industries and applications. Some of the best ways to leverage the advantages of these technologies include:
- Replacing wires and connectors
- Enabling moving or folding designs
- Fitting electronics in tight spaces
- Reducing weight and material
- Increasing reliability
- Streamlining assembly
- Integrating multiple PCBs
In this article, we’ll explore these key applications of flex and flex-rigid PCBs in more detail. We’ll look at specific use cases and design considerations to help you determine if flex or flex-rigid circuits could improve your PCB designs and electronics packaging.
Replacing Wires and Connectors
One of the most impactful ways to use flex PCBs is to replace wire harnesses, ribbon cables, and connectors between PCBs. Flex circuits can integrate these interconnects into a single thin, lightweight assembly. This provides several benefits:
-
Saves space: Flex circuits are much thinner than bundles of wires. Eliminating bulky cables and connectors frees up valuable space.
-
Reduces weight: Flex PCBs use less material than wires, allowing significant weight reductions. This is especially important in aircraft and vehicles.
-
Simplifies assembly: Using flex PCBs eliminates the time-consuming process of manually connecting many wires. Flex circuits act as plug-and-play interconnects.
-
Improves reliability: Solder joints and connectors are common failure points. Flex PCBs minimize these with a integrated structure that resists vibration and shock.
The table below compares the properties of 26 AWG wire and 1 oz. finished copper flex circuits:
Property | 26 AWG Wire | 1 oz. Cu Flex |
---|---|---|
Thickness | 0.404 mm | 0.152 mm |
Weight | 0.0137 g/cm | 0.0041 g/cm |
Current Capacity | 2.2 A | 2.5 A |
Resistance | 0.134 Ω/m | 0.005 Ω/m |
As the data shows, flex circuits have comparable current handling to 26 AWG wire in a much thinner and lighter package with lower resistance. When multiplied over dozens or hundreds of interconnects, the space and weight savings of replacing wires with flex PCBs quickly add up.
Use Case: Automotive Wiring
Wiring harnesses are one of the heaviest and most complex components in modern vehicles. The average car contains over a mile of copper wiring! Replacing these bulky harnesses with flex PCBs can significantly reduce weight, increase reliability, and simplify manufacturing and maintenance.
For example, Tesla uses flex circuits to connect the many systems and sensors in its electric cars. This saves pounds of weight compared to traditional wiring, helping maximize driving range. Flex PCBs also improve reliability in the harsh automotive environment by eliminating failure-prone connectors.
Enabling Moving and Folding Designs
Another significant advantage of flex and flex-rigid PCBs is the ability to create folding and moving electronic designs. The dynamic flexibility of these circuits allows products to change shape and incorporate moving parts. Some examples include:
- Folding displays
- Hinges and slides on mobile devices
- Rotating joints on robotic arms
- Wearable electronics that move with the body
Flex circuits act like a bendable backbone that routes signals between sections while allowing repeatable flexing and motion. Rigid-flex designs can further integrate rigid PCBs for mounting components in a configuration that moves and articulates.
Use Case: Folding Smartphones
One of the most prominent current applications of flex and flex-rigid PCB technology is folding smartphones. Devices like the Samsung Galaxy Z Flip and Motorola Razr rely on these circuits to connect the two halves of the phone and enable the folding display.
The key challenge is allowing the phone to fold flat while maintaining reliability over hundreds of thousands of flexing cycles. The flex circuit must withstand the stresses of repeated folding without breaking solder joints or fatiguing the copper.
Advanced materials and careful mechanical design make this possible. The flex PCBs leverage thin polyimide films and highly ductile copper foils to create a robust interconnect. Finite element analysis simulates the stresses on the circuit to optimize bend radius and circuit routing for maximum reliability.
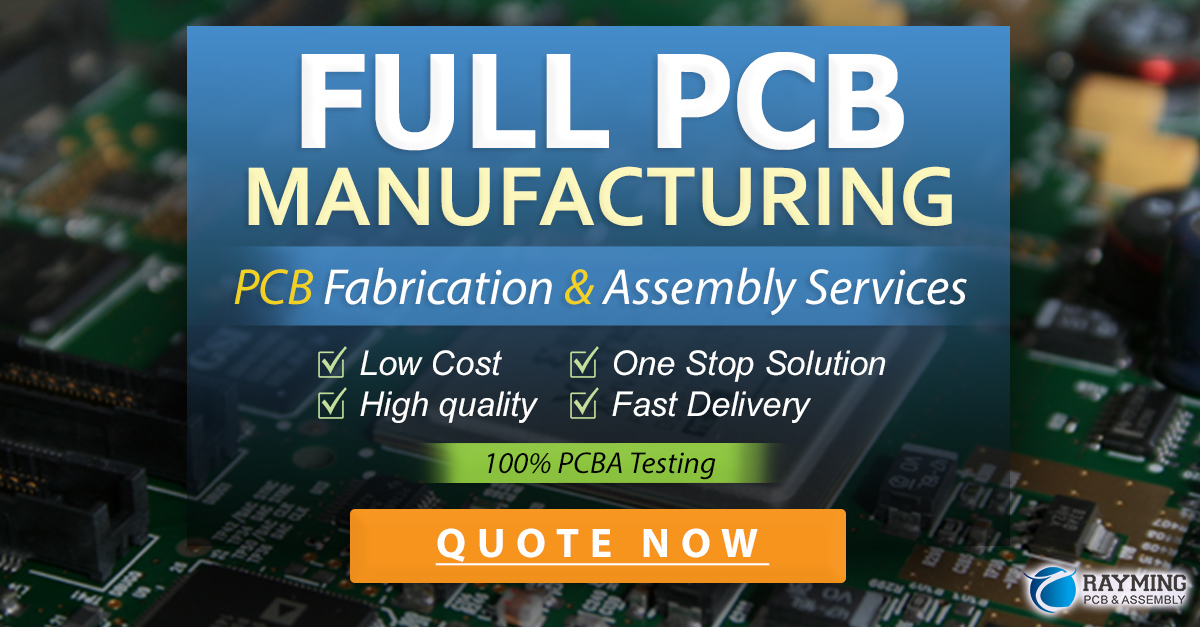
Fitting Electronics in Tight Spaces
Flex and flex-rigid PCBs can conform to fit in tight, irregular spaces where rigid PCBs cannot. The ability to bend the circuit allows utilizing all available volume in compact products. Thin flex circuits can also route through slim channels and slots.
Some applications that benefit from this capability include:
- Wearable and implantable medical devices
- Aerospace and defense electronics
- Robotics and industrial equipment
- Internet of Things (IoT) sensors
The thin profile of flex circuits is especially advantageous. Whereas rigid PCBs are commonly 1.6 mm thick, flex circuits can be as thin as 0.050-0.150 mm. This allows fitting high-density interconnects in the tight spaces between components, chips, and boards.
Use Case: Implantable Medical Devices
Implantable devices like pacemakers and neurostimulators require packing complex electronics into the smallest possible package to minimize invasiveness. Flex circuits help fit all the necessary functions into a tiny biocompatible housing.
For instance, a pacemaker may contain multiple rigid PCBs connected by flex to utilize all available space and achieve a slim profile to fit between heart and skin. Flex circuits can also integrate antenna structures and route signals to the leads that interface with the heart.
Reliability is paramount for implantable devices that must last for years inside the body. Flex PCBs increase reliability compared to individual wires by providing a complete, integrated interconnect solution. Materials like biocompatible polyimide and silicones allow the flex circuits to interface safely with body.
Reducing Weight and Material
The light weight and material efficiency of flex PCBs make them an excellent choice for applications that are sensitive to mass. Some key industries that benefit from these weight savings include:
- Aerospace: Commercial aircraft and satellites
- Military: Soldier-carried gear and unmanned vehicles
- Automotive: Electric and hydrogen fuel cell vehicles
- Medical: Portable equipment and wearables
- Consumer electronics: Laptops, phones, AR/VR headsets
Flex circuits can weigh 75% less than equivalent wire harnesses. Integrating the interconnect into the PCB also reduces the size and mass of connectors. These savings add up over a complex system to significantly reduce overall weight.
Beyond just interconnects, flex PCBs can reduce weight by replacing rigid PCB substrates. While rigid FR-4 PCBs weigh around 4.7 g/cm^3, polyimide flex circuits are only 1.5 g/cm^3. Thinning or eliminating stiffeners can further decrease mass.
The table below shows potential weight savings of using various flex materials:
Material | Weight (g/cm^3) | Potential Savings |
---|---|---|
FR-4 | 4.7 | – |
Polyimide | 1.5 | 68% |
PET | 1.4 | 70% |
LCP | 1.4 | 70% |
Use Case: CubeSats
CubeSat miniature satellites are a prime example of an application that benefits from the weight and space efficiency of flex and flex-rigid PCBs. These satellites measure just 10 cm per side and weigh only a few kilograms, so every gram counts.
Using rigid-flex PCBs to integrate all electronics in the folded stack enables maximal functionality in minimal volume. Flex interconnects save precious weight compared to wires. NASA, ESA, and many commercial CubeSat builders utilize rigid-flex designs.
Furthermore, flex and rigid-flex PCBs increase CubeSat reliability compared to mating multiple rigid boards with connectors. Eliminating these points of failure is critical for satellites that must survive launch and operate in the harsh environment of space.
Increasing Reliability
Reliability is vital for electronics that must operate in challenging conditions or where failure is unacceptable. Flex and flex-rigid PCBs provide an inherently robust interconnect solution that resists common failure modes. Benefits include:
-
Shock and vibration resistance: Flex absorbs shocks and vibration that could crack rigid PCBs and connectors. Eliminating wires also prevents chafing and breaking from vibration.
-
Thermal cycling endurance: Flex PCBs withstand thermal expansion mismatch stresses that could cause solder joint failures in rigid boards. The CTE of polyimide closely matches copper.
-
Creep resistance: The properties of polyimide films resist material creep that could cause circuit failure over time under load or high heat.
-
Folding endurance: Special copper foils and bend relief features allow flex circuits to withstand millions of flexing cycles without fatigue.
Careful design is necessary to realize the full reliability potential of flex PCBs. Factors like bend radius, stiffener placement, copper type, and plating play a role. Following best practices and industry standards maximizes reliability.
Use Case: Aerospace Electronics
Aircraft and spacecraft electronics demand ultimate reliability to ensure passenger safety and prevent costly failures. Flex and rigid-flex PCBs meet these needs through the benefits described above.
The Boeing 787 Dreamliner, for example, uses flex circuits extensively for distributing power and signals. Flex is more reliable than wires in the plane’s dynamic environment, resisting vibration and thermal cycling. Flex also saves significant weight to improve fuel efficiency.
SpaceX’s Falcon 9 rocket and Dragon capsule leverage rigid-flex PCBs for their avionics systems. The integrated rigid-flex assemblies withstand the intense vibration and shock of launch, as well as the thermal and radiation extremes of space. Rigid-flex construction reduces potential failure points compared to mating rigid boards with connectors.
Streamlining Assembly
Flex and rigid-flex PCBs simplify and streamline electronics assembly compared to using separate rigid boards, wires, and connectors. All the interconnects are integrated into the flex circuit, eliminating the time-consuming process of manually connecting components.
Rigid-flex designs are especially advantageous for assembly. Rigid sections can mount components using standard SMT and through-hole processes. The flex interconnects then allow folding the rigid sections into a 3D configuration. Rigid-flex assembly can replace multiple rigid PCBs connected with wires and connectors.
Benefits of flex and rigid-flex assembly include:
- Reduced labor time and cost
- Fewer assembly steps and failure points
- Simplified wire routing and cable management
- Improved alignment and registration between boards
- Faster and easier troubleshooting and rework
Flex-rigid PCBs enable modular design approaches like Z-fold and book-fold configurations. Standardized flex interconnects allow plugging various rigid modules together in different combinations. This modular architecture streamlines customization and updating of electronics.
Use Case: Smartphones
Smartphones are one of the most ubiquitous examples of flex and rigid-flex PCB assembly. Modern phones pack immense functionality into slim, lightweight devices. Flex and rigid-flex circuits make this possible.
A smartphone’s main PCBA typically includes multiple rigid sections connected by flex circuits in a folded stack. The flex interconnects route signals between the processor, memory, RF, power, and interface boards. Using flex eliminates the need for cumbersome board-to-board connectors.
Smartphones also utilize flex PCBs for the various buttons, switches, sensors, and connectors around the edges of the device. Flex allows routing these interfaces to the main board in the tight spaces of the phone’s housing. Flex is far more efficient than using individual wires.
Integrating Multiple PCBs
Flex-rigid PCBs provide a simple method for integrating multiple interconnected rigid PCBs into a single 3D assembly. Rather than connecting separate PCBs with cables or connectors, rigid-flex designs combine them into one circuit with integrated flex interconnects.
Rigid-flex integration provides several benefits:
-
3D packaging: Rigid-flex allows folding and stacking rigid circuit boards in compact 3D configurations to efficiently utilize limited space.
-
Consolidated BOM: Integrating multiple PCBs into one flex-rigid assembly reduces the number of unique parts to procure and stock.
-
Improved signal integrity: Flex interconnects provide consistent impedance control and shielding to maintain signal integrity between circuit sections.
-
EMI/RFI shielding: Flex layers with ground planes and shielding can isolate and protect signals from interference between boards.
-
Reduced system complexity: Rigid-flex assemblies are simpler to integrate on a system level than multiple individual PCBs, cables, and connectors.
While rigid-flex PCBs have higher unit costs than rigid boards, they can reduce overall system costs by simplifying assembly, reducing part count, and increasing reliability. The integrated approach streamlines the entire product lifecycle.
Use Case: Wearables
Wearable devices like smartwatches and fitness trackers rely on rigid-flex PCBs to achieve their compact, curved designs. Flex-rigid assemblies integrate all the necessary components into a dense package that fits on the wrist.
For example, a smartwatch may use a rigid-flex PCB with separate rigid sections for the processor, memory, battery, display, and sensors. Flex interconnects route signals between the sections, allowing the assembly to fold and fit within the watch housing.
Using a rigid-flex design consolidates these functions into a single PCB assembly. This improves system integration and signal integrity compared to a design with multiple rigid PCBs connected by cables or board-to-board connectors. The flex-rigid architecture enables a thinner, more comfortable product.
Summary
In summary, flex and rigid-flex PCBs provide a versatile solution for creating dense, lightweight, and robust electronic packaging. Some of the best applications of these technologies include:
- Replacing wires, cables, and connectors
- Enabling moving and folding product designs
- Fitting circuits in tight, compact spaces
- Reducing system weight and material
- Increasing reliability in harsh environments
- Streamlining and simplifying assembly
- Integrating multiple PCBs into a consolidated package
These advantages make flex and rigid-flex PCBs an attractive option for a wide range of industries and products. While they require careful design and have higher initial costs than rigid PCBs, the system-level benefits can provide a compelling return on investment.
As electronic devices continue to advance in complexity and miniaturization, flex and rigid-flex circuits will play an ever-growing role in enabling these cutting-edge designs. Understanding and leveraging these technologies can help you create more competitive, reliable, and innovative products.
Frequently Asked Questions
What are the key differences between flex and rigid-flex PCBs?
Flex PCBs consist entirely of flexible circuit layers, while rigid-flex PCBs integrate both flexible and rigid circuit sections. Rigid-flex allows combining the benefits of flex interconnects with the component mounting and mechanical advantages of rigid boards. The rigid sections are typically connected by flex in folded 3D configurations.
What are the most common materials used for flex and rigid-flex PCBs?
The most common base material for flex PCBs is polyimide film. Polyimide provides high heat resistance, dimensional stability, and mechanical durability. Copper foil is bonded to the polyimide to form the conductive circuit layers. Adhesives like acrylic and epoxy bond the layers together. Polyimide coverlay or solder mask insulates the outer layers.
Rigid-flex PCBs use a combination of polyimide and traditional FR-4 materials. The rigid sections use FR-4 layers like a standard rigid PCB, while the flex sections use polyimide. The rigid and flex areas are laminated together into a single, integrated assembly.
What are the limitations and challenges of using flex and rigid-flex PCBs?
The main limitations of flex and rigid-flex PCBs include:
- Higher material and fabrication costs than rigid PCBs
- More complex and time-consuming design process
- Requires specialized knowledge and design tools
- Limited range of materials and suppliers compared to rigid PCBs
- Reduced thermal conductivity of polyimide compared to FR-4
- Lower current carrying capacity for a given thickness compared to rigid
- Can be difficult to rework and repair in the field
Despite these challenges, the benefits of flex and rigid-flex often outweigh the drawbacks for applications that require their unique capabilities. As usage of the technology grows, costs are decreasing and the supply chain is maturing, making flex and rigid-flex increasingly accessible
Leave a Reply